Audit Report
The process of managing a supply chain is often glanced over by side observers when considering the performance of an organization. However, the analysis of a company’s SCM and, particularly, the issues associated with the management of information and the development of an infrastructure for an SCM are central to running a company successfully. The DHL company is a useful example of how a supply chain should be run and how the process of data management can be improved with the help of the latest technological additions. This audit report seeks to examine DHL’s SCM and the related strategies that the company uses in the process, thus commenting on the efficacy of DHL’s performance and recommending options for further improvements.
Strategy
Being one of the major organizations offering supply chain management (SCM) services, DHL has been gaining an increasing amount of attention recently. The company has been expanding at a massive rate, embracing new opportunities for transportation and delivery of crucial products and assisting organizations and individuals in the process (Lall et al., 2019). Although the outcomes of the current economic and health-related crisis have affected DHL to an extent, the firm has still been delivering consistently positive results. By considering the SCM framework used at DHL, one will be able to promote a similar range of improvements within the environment of other organizations, thus launching a chain of upgrades across all companies within the global economy and creating premises for a rapid improvement of their performance.
The current strategic direction of DHL has clearly been geared toward global expansion. The company has been understandably seeking opportunities for diversifying its customer base, as well as seeking options for receiving support from other organizations by means of partnerships (Liu, 2020). As a result, DHL’s current strategic direction can be described as one of an innovation-driven approach with a close focus on risk management and mitigation (Hilorme et al., 2019). Specifically, the company appears to place a high value on the management of costs and the integration of innovative tools for managing data, which adds to its competitive advantage.
Applying the Value Chain Analysis framework, one will notice that the approach adopted at DHL allows the organization to benefit due to the focus on the digitalization of pro processes within it. As a result, the threat of failing to complete specific steps within the SCM process is reduced significantly. Specifically, applying the value chain analysis to the situation at DHL, one will have to acknowledge the fact that the current infrastructure of the organization, its HRM, the use of technology, and especially the procurement framework allows DHL to retain its competitive advantage and reinforce its competitive strength (see Fig. 1).
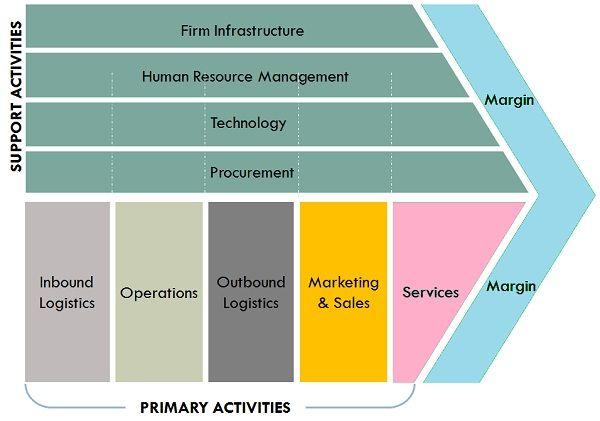
As Fig. 1 above shows, the selection of procurement strategies affects the company’s competitiveness particularly strongly since it allows for sustaining the company’s supply chain. At DHL, the observed correlation is particularly visible since the company deploys a value-added approach along with the traditional framework for SCM. Namely, the company’s managed transport solution that it uses as the foundational principle for its performance allows for increasing the efficacy of inbound and outbound logistics by reducing the time taken for the transportation, as well as increasing its quality and the overall damage control (Gold and Schleper, 2017).
Furthermore, the integration of digital tools for data management increases the efficacy of operations, making the key processes fast and smooth (Oláh et al., 2018). Likewise, the development of applications for users to download in order to control how the product that they have purchased is being transported allows for improving the sales and marketing of the company, making it more trustworthy and client-oriented. As a result, the organization’s strategy remains effective. Finally, the use of digital techniques in sales and marketing, specifically, the creation of feedback tools will help receive data that will inform future improvements.
Moreover, the transfer to the digital context has simplified the management of information substantially. According to the account provided at DHL, the organization has been building its competitive advantage in the global market due to the emphasis on the “standardization and the use of new technologies” (Deutsche Post DHL Group, 2020). In the wake of the technological breakthrough witnessed in the global community, an innovation-driven strategy should be regarded as a powerful tool for attaining global success.
Namely, the integration of IT and ICT tools into the supply chain of the organization creates additional opportunities for managing data in a manner as expeditious as possible, while managing to retain every bit of information without losing it. As a result, problems associated with delays and the failure to meet set deadlines are avoided at DHL successfully.
Overall, the business strategy of DHL can be described as a combination of innovativeness and a stakeholder-oriented approach. The specified solution seems to produce the best resulting in the context of the target industry given the necessity to produce the necessary services promptly while maintaining communication with stakeholders (Goldsby et al., 2018). Therefore, the framework that DHL has been adopting has proven to be impressively efficient even in spite of the recent events that have affected the global economy tremendously.
If anything, the DHL company has only proven to be especially successful at the time of the epidemics since it has managed to continue evolving and adapting its business toward the changing global setting and the restrictions set in the global economic context. To confirm the specified observation, one might want to consider changes in the company’s share price. Indeed, the company has been showing steady development since March 2020 (see Fig. 2).
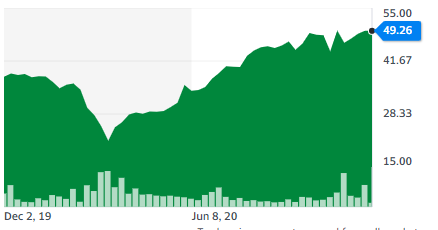
Moreover, the strategy selected by the organization also allows for maintaining customer connection and processing feedback from buyers constantly, which is central to updating DHL’s services and improving its performance. Finally, what deserves particular praise is DHL’s persistent and unwavering focus on green solutions in it transportation strategy. According to Lall et al. (2019), DHL has been deploying the green SCM principles and especially the premises of the agile approach in its blockchain framework for a while. The described approach places DHL especially highly on the list of the top organizations offering sustainable logistics solutions for the transportation and delivery of products worldwide (Denktaş-Şakar and Sürücü, 2020).
The suggested technique allows for enhancing the value chain of the organization, creating a unique competitive advantage for DHL to use as the selling point in the global market. Arguably, the company could improve its performance even further by introducing the Lean, agile, resilience, and green (LARG) framework into its SCM to cement its image as one a green organization (Suifan et al., 2019). However, even with the current approach, the overall framework for strategic management that DHL has been using in improving its business and keeping its competitive advantage relevant in the global market is quite impressive.
Organization
Key operations management roles and responsibilities
Notably, DHL has also been organized in a way that allows the company to maximize its profits and efficacy while keeping a cost-efficient approach toward resource management. The described framework has become available to the organization due to the smart framework for assigning roles and responsibilities to staff members within the constructed SCM design. Among the key OM roles and responsibilities at DHL, one should pay particular attention to the tasks such as human resource management (HRM), the asset management framework, and the cost management technique (Le et al., 2019). Although DHL has been enjoying the position of the world’s top transportation and logistics company, it has been prioritizing the reduction of expenses, which its approach toward pricing and resource usage reflects.
The HRM strategy that DHL uses is not entirely groundbreaking since multiple companies have already tried implementing it and succeeded, yet the specified approach remains one of the principal devices for keeping employees engaged and invested in the company’s performance. Namely, the HRM technique adopted at DHL is primarily oriented toward integration into international markets, which is why it prioritizes cross-cultural collaboration and emphasis cultural awareness and cultural competence (Cai, 2016).
The described approach has been assisting the company in mitigating the instances of misunderstandings and conflicts occurring due to cultural differences (Sabuhari et al., 2020). In addition to improving cooperation within the company’s organizational setting, the proposed framework also inhibits the development of problems that DHL may face in emerging markets (Danso, 2018).
Given the current policy toward expansion into new market settings that DHL has been pursuing in an attempt at capturing a global presence, the specified initiative in HRM can be described as rather suitable. Indeed, the existing accounts of DHL’s HRM framework efficacy have been quite positive. For instance, the study by Dolgui et al. (2018) outlines that the organization’s ability to utilize the available infrastructure characteristics to establish a working framework for transferring goods from one point to another has been beyond impressive.
Key supply chain management roles and responsibilities
In addition, DHL has been quite efficient in the assignment of roles and responsibilities to its staff members and ensuring that these roles meet the staff’s skills and level of expertise. Namely, the company has been utilizing its information management resources very effectively to keep track of the latest change and trends within the environment of the target market (Dolgui et al., 2018). DHL has a system that allows it to spot alterations in the logistics and transportation industry, particularly, the ones related to technological breakthroughs and disruptive innovations (Herold et al., 2017).
The specified role is attributed to a specific unit, whereas regular supply chain managers observe the situation across the company’s supply chain, in general, and negotiate with partners, particularly, suppliers, vendors, and retailers to ensure that products and materials are delivered on time (Nguyen, 2017). The specified approach allows DHL to keep its supply chain processes running correctly while also ensuring that every participant contributes to the development of the organization.
In addition, planning and analysis take a substantial part of the range of responsibilities and jobs that staff members across DHL’s supply chain must assume in order to deliver the expected results. Specifically, the company has been utilizing an elaborate framework for planning based on the Theory of Constraints (Puche et al., 2016). However, given DHL’s issues with managing customer relationships, the incorporation of the Customer Relationships Management Theory would be an important improvement.
The nature of the supply chain structure or network
The focus on sustainability and talent management in the context of logistics-related tasks is what makes DHL’s approach toward structuring its supply chain so impressive. Although DHL also recognizes the importance of supervising and controlling processes within its supply, chain, the company places most of the emphasis on people and the approach that it uses to motivate and engage them (Veleva et al., 2016).
Thus, DHL manages to achieve a high success rate even in an environment that can be described as highly hostile, particularly, due to the economic crisis caused by the outbreak of COVID-19 and the resulting lockdown (Veselovská, 2020). The concessions that DHL has been making to ensure that its staff members remain loyal and devoted have helped the organization frame its relationships with its employees based on trust, cooperation, and support.
Specifically, the application of the lifecycle approach toward assisting its staff members to integrate into the context of the organization and become members constitutes the nature of the company’s structure and its internal network. According to the official statement issued by the company representatives, “It is important that our talent strategy ensures DHL hires and manages its employees effectively in order to develop their skills and progress them within the business. In order to do so, DHL uses a lifecycle approach that clearly maps out an employee’s journey” (Bridges, 2020, para. 3). Thus, the HRM framework that the company has been using to forward its business progress and goals can be regarded as the cornerstone idea for its supply chain structure and the related SCM activities.
The nature of relationships with supply chain partners
In its approach toward structuring relationships with its partners across the supply chain, DHL has been seeking to create and implement an entirely new strategy that allows broadening the horizons of the traditional understanding of SCM collaboration. Specifically, the organization emphasizes that, apart from traditional transactions, it strives to implement new frameworks for business partnership whenever possible (Herold et al., 2017). According to the company’s recent announcement, DHL has shifted toward the implementation of the framework known as the “Business Collective 1.0,” or BC 1.0 (Beyond transactions: Taking partnering to the next level, 2020).
Therefore, the nature of the company’s relationships with its partners has morphed from being based on purely transactional principles toward the goals of mutual support and collaboration. The described change, namely, the focus on building trust-based interactions between DHL and its SCM partners, serves as the building block in its new structure for strategic management of its SCM processes. Specifically, with the promotion of mutual trust and responsibility, the extent of control over key transactions will increase, leading to better management of risks, costs, and other relevant concerns in the SCM context.
Processes
In order to evaluate the extent to which DHL has been meeting the operational performance standards, as well as the SCM performance requirements, one will need to deploy the assessment of DHL’s inventory turnover. According to the recent statistics concerning the levels of inventory turnover at DHL, the company has curbed the rates of equipment replacement, which indicates that DHL has found a way of maintaining its tools more effectively and using them in a more cost-efficient manner (Pant and Mahapatra, 2018).
Specifically, as shown in Appendix A, DHL’s inventory turnover rates have increased only slightly from 74.9 to 100.47, which, given the rise in the performance rates, indicates a sensible approach to managing the company’s inventory (Deutsche Post AG NA O.N. (DPWGn), 2020). The current extent of the company’s performance is, therefore, quite impressive, especially given the complicated environment in which the organization is forced to function.
Business Process Models
A thorough understanding of how DHL functions will require the application of a business process model to its performance, particularly, to the implementation of the SCM processes within the company’s design. Remarkably, there is a plethora of ways and techniques for describing the internal processes of an organization and identifying the chain of key activities launched in order to start the production process. Specifically, business process models such as flow charts, Gantt charts, data flow diagrams, colored Petri-nets, workflow techniques, and object-oriented methods, to name just a few, are utilized to describe the processes occurring within an organization (Qi et al., 2018).
The specified frameworks are quite different in their layout yet their purpose and the ultimate effects of their application are similar. Namely, all of these tools are expected to pinpoint the key processes within an organization and show how they are related to each other, thus creating a chain of activities performed within an organization to achieve its production goals (Effendi et al., 2018). As a rule, to encompass the complexity of SMART goals and the challenges that the global economic environment contains, the DHL Company develops a framework rooted in the Flow Chart Technique (Dani et al., 2019).
The described tool allows for keeping the description simple while also portraying complex relationships within the processes that do not necessarily have to be linear in nature. Thus, for DHL’s purposes, the specified model serves perfectly, representing a tool for coordination and control of the main tasks and their implementation at every stage of the logistics services offered by the organization, primarily, the fright services and the transportation of the products and materials from one point to another.
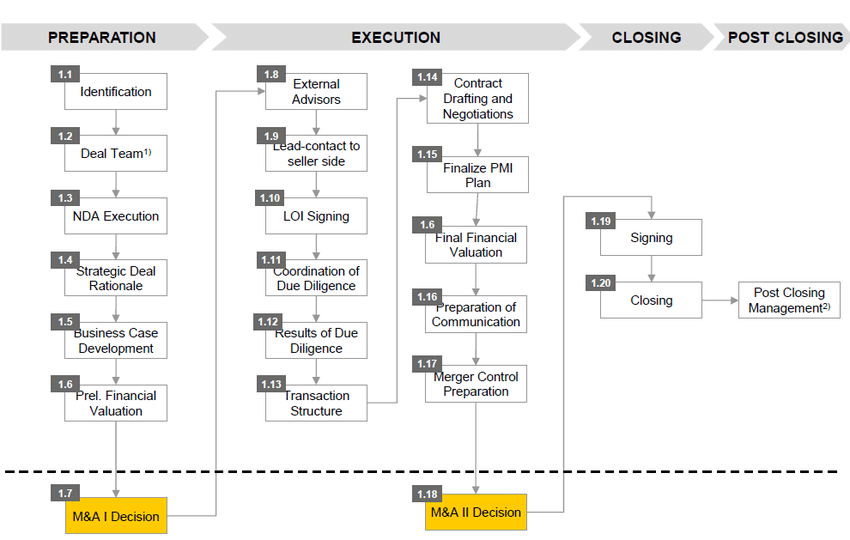
Therefore, to represent the performance of the target organization in the most accurate manner possible, one should opt for the use of the Flow Chart Technique as the approach that allows illustrating the processes within DHL most accurately. As Figure 3 above shows, the company currently implements five key tasks when conducting its primary activities, namely, the preparation for the process the execution of it, and the closing phase, followed by the post-closing analysis.
The proposed business model allows the company to integrate interdisciplinary collaboration and decision-making prior to implementing the key solutions, specifically, by creating a deal team after the identification of key goals. The further development of the strategic deal rationale and the resulting business case, thus, is based on the SMART objectives detailed during the development of the group and specific information gathered at the identification and NDA execution phases.
In turn, the twofold implementation process allows coordinating an array of tasks, from financial concerns to the development of communication frameworks and control tools. Thus, all systems are prepared for the management of key goals in unison, which is central to preventing risks from occurring while keeping all participants in the process informed. As a result, the threat of data loss and the failure to develop a sustainable business strategy is driven to a minimum (Amjadd et al., 2018). Furthermore, the final step of the third stage, specifically, the preparation of control, suggests that the complex issue of logistics-related services, particularly, the process of transporting products from one point to another, is fully coordinated and controlled.
Finally, the closing and post-closing stages might seem redundant, yet they serve a crucial purpose of ensuring that the key tasks are accomplished and that the outcomes of the business process are analyzed thoroughly. As a result, the opportunity for analyzing the outcomes and detailing the issues that could be addressed in a more productive way is isolated and resolved. Specifically, the problems such as an improved trajectory of the route for delivering particular products, the need for revisiting a specific communication channel to reinforce the connection with one of the partners, and similar concerns can be handled at the specified stage.
Managing Operations and Supply Chain Processes
DHL has shown the ability to handle key SCM processes and related tasks quite effectively. As the supply chain analysis above has shown, DHL has incorporated an effective SCM approach due to the effective use of the available infrastructure and resources. However, the company’s information management technique could use change in order to increase DHL’s popularity.
Means of Process Improvement
Although the current business process model utilized by the DHL company is quite effective as a method of aligning primarily tasks within an organization in a cohesive set of processes, it could still use a range of minor improvements. For instance, the issue of communication could be addressed in greater detail due to the nuanced context of the global trade process and the issues that an organization may encounter when installing a communication framework for collaborating on a global scale. Specifically, among the aspects of the present business model that DHL is applying, one should not issue with tracking down the transportation of the package ordered by a client (Sari and Maya, 2018). Specifically, customer reviews, including both older and more recent ones, all point to the same problem of products being lost or delivered in a very poor condition and much later than the set deadline (Wiśniewski et al., 2019). Therefore, the organization should consider improving both the time management approach and the framework for controlling the process of package delivery.
Indeed, despite the efficacy and intricacy of the business model currently deployed at DHL, the measures for controlling product delivery are quite scarce and not very reliable (Sari and Maya, 2018). The outlined problem surprisingly coexists with a rather effective communication framework that DHL has launched across its departments to ensure collaboration and better data management and access to customers’ information (Montgomery and Borror, 2017). Therefore, the organizational issue should be considered the main core of the problem observed.
Thus, to improve the problem of delivery deadlines and the condition in which packages are provided to the end customer, DHL will have to implement a more complex tracking tool that would help both the company and the customer to observe the package being transported. Specifically, a digital application for tracking down the trajectory of the package’s transportation and determining the date of its delivery must be developed and launched as soon as possible. Additionally to the outlined tracking service, the application should allow customers to contact the support team promptly in case there are delays or any other issues observed in the process (Froger et al., 2019). Thus, the problem of mismanaging the transportation and delivery issues will be handled swiftly.
It should also be mentioned that, apart from creating innovative solutions for its SCM and, specifically, the management of logistics and the related issues, DHL has also been constructing an intricate yet effective framework for process improvement. Therefore, the company has been aware of the internal problems within its framework and the necessity to resolve them. Specifically, DHL has been developing a single-provider model for managing its logistics processes, which is expected to help to manage customers’ needs on an individual level (Montgomery and Borror, 2017).
Moreover, the challenges of urbanization as one of the major concerns that DHL has been facing in improving its SCM deserves to be mentioned. After acknowledging the complications that urbanization has entailed for the organization, DHL has focused on the improvement of the infrastructure for its logistic processes, namely, the identification of opportunities for faster transportation of products, as well as strategies for keeping packages intact in the process.
Information
At first glance, DHL’s approach toward information management has been quite effective, given the increase in performance rates that the firm has been showing recently despite the presence of major global factors, such as the pandemic of the coronavirus. However, more careful scrutiny of DHL’s current performance will show that some of the aspects of its information management process could use improvements. Namely, the company has been using Big Data analysis as the means of forecasting future changes within the industry (Jagoda and Samaranayake, 2017). The specified framework is quite innovative in its nature, yet it appears to be lacking several important components that could assist the organization in managing the delivery process and the quality of its services more effectively.
Analyzing the current problem of the data management approach that DHL has been using, one should notice that DHL has been placing the main emphasis on the use of an all-encompassing study of major factors to which it is subjected in the global context. In turn, minor issues that occur at the implementation stage between DHL and its partners, as well as the information management framework used to navigate the communication process among its staff members, has been left mostly unattended (Tarigan et al., 2019).
As a result, the present approach toward arranging the company’s related internal data is at its inception stage, which obstructs the company’s view of the internal issues that could potentially affect the management of transportation and delivery of products (de Oliveira Dias et al., 2018).
However, to give credit to where it belongs, the strategy for addressing the analysis of the Big Data and the forecasting tools for managing information on the global level is impeccable at DHL. The focus on the use of AI as the method of modeling key scenarios, which is a recent addition to the inventory of the organization’s information management framework, has been seen as a particularly promising endeavor. The opportunity to spot trends and correlation in the changes occurring on a global scale based on the Big Data analysis represents a massive potential for DHL since it will help the company to model the scenarios in which the threat of losses, as well as any logistics-related risks, in general, will be minimized (Lukkarinen and Majava, 2020). Therefore, the emphasis on the creation of the IA tools for the analysis of Big Data should be recognized as a major advancement.
The integration of the Big Data analysis with the help of AI is particularly useful for the company given the present circumstances. Specifically, with the increased economic uncertainty within the global market caused by the pandemic, being able to predict possible developments within the goal economy and the transportation industry is priceless (Saleh et al., 2018). Consequently, the options that the current framework provides are very valuable. Overall, the present framework for data management can be defined as highly reliable and allows for an all-encompassing analysis of the major factors that DHL may encounter in the environment of the global market.
However, the absence of emphasis on the internal issues linked to data management and the promotion of stronger data management across DHL’s supply chains deserves closer scrutiny as a major problem of its current approach. Specifically, the lack of an effective tool for tracking down the main phases of the product transportation stage, as well as the loss of information and the problems with delivering products to customers on time, deserves to be studied further (Jayakrishnan et al., 2018). Specifically, DHL seems to be suffering from a lack of control over data within its own supply chain framework. The observed phenomenon is rather understandable given the scale at which the company operates, yet it does not make it any less excusable. Therefore, DHL should integrate tools for improved communication within its supply chain so that the process of transportation and delivery could be controlled at every stage and that the exact location of the parcel could be identified at any moment,
Therefore, the focus on personalizing the communication process and reducing the threat of data loss should be considered some of the key priorities for DHL presently. Without the suggested change, the organization could lose its position as a leader within the industry (Aldiabat et al., 2018). Moreover, the extent of customers’ trust in the company and their loyalty toward it, which are presently very high, will be undermined and, thus, reduced.
The proposed change can be implemented by introducing cross-divisional information management standards. By setting the principles of collaboration on the level of the company’s departments and specific parts of its supply chain, DHL will be able to minimize the probability of omitting crucial information or misinterpreting data in the process of transferring it across its supply chain (Riazi et al., 2019). Recent developments in the company’s information management approach have indicated that the company has been working on inter-divisional data management techniques.
Specifically, the recent report issued by the company has proven that DHL has been seeking opportunities to enhance its information management framework: “We are working to improve cross-divisionally on a continuous basis. In doing so, we are concentrating upon initiatives that create value for various stakeholders, for example, environmentally-friendly solutions and an optimized IT landscape” (Deutsche Post DHL Group, 2020, para. 3). The outlined change in the IT framework of the organization is central to the improvement in the quality of transportation and the efficacy of product delivery (Nikou et al., 2016). Specifically, the change outlined above will help to spot problems in the management of information at rather early stages of SCM and prevent problems from developing. Therefore, apart from aligning with DHL’s green SCM policy, the described improvement will also lead to better customer relationships.
In addition, to ensure that customers have the information about the product being delivered to them readily available, an application for tracking down every stage of delivery will be required. The application in question will help to detect the exact stage of the product transportation and receive a detailed account of its location, the delivery date, and the issues that may have occurred during the transportation process (Miraz et al., 2020). Thus, customers will receive products that will not be damaged or mishandled, and the delivery will occur at the expected date.
Performance
Based on the information above, DHL’s operations and supply chain performance can be described as highly effective and of appropriate quality. Although minor problems with the speed of package delivery and the state in which it was handed to the recipient have been observed, the general impression that the DHL company gives is that it of a trustworthy service with a high level of responsibility, functioning, and commitment.
To evaluate the company’s performance, the extent of customer satisfaction and the level of service quality was assessed (Piyachat, 2017). Specifically, customer satisfaction rates were analyzed based on the feedback submitted to the company and the general rating that DHL has received over time. In addition to the specified qualitative analysis, a quantitative perspective has also been incorporated, allowing to gauge the difference in DHL’s past and current performance rates.
The outcomes of the performance management overview, specifically, in regard to the company’s SCM, indicate that the firm has improved slightly. Namely, DHL has incorporated several important data management tools into its framework, while also updating its infrastructure and relationships with its partners. As a result, DHL has managed to maintain its competitive advantage high at the time of a global economic crisis.
However, the same evaluation has also proven that DHL has a long way to go in terms of improving its communication and, particularly, its customer relationships, as well as data management among staff members. Although DHL has been very prolific in introducing innovative technologies and devices as a response to changes within the target market, and the necessity to update its performance, DHL has also faced the need to increase the efficacy of its dialogue with its employees and customers (Limcharoen et al., 2017). The issue of communicating essential information to staff members represents a particularly difficult challenge for the company to accept since the current model will have to be replaced with a new one in order to establish connection with employees (Masudin et al., 2020). Moreover, new communication channels must be developed in order to ensure that staff members receive instructions and are capable of implementing them accordingly. Finally, the opportunities for introducing unity among staff members in order to improve the levels o organizational performance deserves a mentioning as an important stage of enhancing the company’s productivity.
Furthermore, the change in the communication patterns will also require altering DHL’s current perception of its staff members’ input in regard to the alterations in corporate policies. Specifically, DHL will have to listen more carefully to its employees in order to maintain its credibility and weight among them. Thus, the incorporation of a homogenous organizational framework based on enhanced communication between the company and its staff will be needed (Bakar and Jaafar, 2016). Once the proposed change is implement, opportunities for improvements are introduced. Specifically, n updated communication framework used by staff members to transfer urgent and vital information will imply that fewer data will be lost or misrepresented in the process. The described outcome is particularly important given the need for DHL to transfer data fast while also keeping it palatable in the context of its diverse organizational environment (Feng et al., 2018). Therefore, by introducing the specified framework into its context, DHL develop the setting where the mismanagement of data can be easily avoided and amended, whenever necessary, without major detrimental effects on the quality of the product.
Action Plan
As shown in the assessment above, problems with communication, data management within the organization, and adherence to quality standards appear to be the crucial factors that do not allow DHL to remain the most efficient company in the transportation industry. Therefore, the DHL company will have to set the platform for change in its organizational context ad, especially in the environment of its supply chain. The plan for implementing change will be based on Kotter’s eight-step change management model (Bhatt, 2017).
The selection of the framework was justified by the need to introduce a clear, accurate, and detailed instruction for managing change (Ján and Veronika, 2017). Due to the established framework for functioning in the target market, DHL will have to be very cautious about the introduction of any changes into its already well-functioning framework (Brock et al., 2019). In turn, Kotter’s eight-step model will help DHL to take full control over the alterations to be observed in its organizational context and introduce minor tweaks to the general change process whenever necessary.
The first step, which requires increasing urgency, should be based on a group meeting where DHL will introduce its members to the fact that the organization could use several improvements in regard to its information and quality management strategies. Afterward, the second step, which will require building a team of devoted staff members with a strong initiative and impetus for improvements. Thus, the core of change will be introduced into the organizational context. The next step will imply developing the vision, which, in DHL’s case, will be based on innovation and will be introduced to the rest of the staff via the team in question (Mansaray, 2019).
The fourth stage of change implementation will require communicating change for a buy-in, which will require a significant amount of persuasion from DHL’s managers to ensure that no resistance to change should occur among staff members. Specifically, the company will have to prove that the promoted alterations will have multiple benefits for all those involved in the company’s performance, including its staff.
Afterward, DHL must empower action in accordance with Kotter’s framework. The specified stage implies that DHL will need a set of criteria for popper performance that employees will use in order to improve their output. Thus, the focus on quality management ad communication with the target customers will have to be outlined as the key priorities in the new guidelines for managing the logistics processes (Dijesh and Mary, 2017). In addition, the new requirements will have to incorporate the focus on R&D as the critical aspect of improvement and the opportunity to embrace the full extent of innovation. Additionally, essential milestones will be introduced to create short-term wins as the sixth step of the model requires. Finally, the requirements of not letting up and maintaining the change will need the introduction of control tools, which may take the form of audits or reports in the selected setting.
Reference List
Aldiabat, B. F., Bataineh, A. and Abu-Hamour, H. M. J. (2018) ‘The impact of business process management on Job performance’, Journal of Business and Retail Management Research, 13(2), 1-9.
Amjad, A., Azam, F., Anwar, M. W., Butt, W. H. and Rashid, M. (2018) ‘Event-driven process chain for modeling and verification of business requirements–a systematic literature review,’ IEEE Access, 6, pp. 9027-9048.
Bakar, M. A. A. and Jaafar, H. S. (2016) ‘Malaysian logistics performance: a manufacturer’s perspective’, Procedia-Social and Behavioral Sciences, 224, pp. 571-578.
Beyond transactions: taking partnering to the next level. (2020). Web.
Bhatt, R. (2017) ‘Theoretical perspective of change management’, CLEAR International Journal of Research in Commerce & Management, 8(2), pp. 1-7.
Bridges, L. (2020) DHL: Talent management within logistics. Web.
Brock, J., Peak, K. and Bunch, P. (2019) ‘Intuitively leading change: completing a kinesiology department-to-school transformation using Kotter’s 8-stage change model’, Journal of Physical Education, 6(2), pp. 14-24.
Cai, D. Y. (2016) ‘A concept analysis of cultural competence’, International Journal of Nursing Sciences, 3(3), pp. 268-273.
Dani, V. S., Freitas, C. M. D. S. and Thom, L. H. (2019) ‘Ten years of visualization of business process models: A systematic literature review,’ Computer Standards & Interfaces, 66, 1-8.
Danso, R. (2018) ‘Cultural competence and cultural humility: A critical reflection on key cultural diversity concepts’, Journal of Social Work, 18(4), pp, 410-430.
de Oliveira Dias, M., Magalhães, M. A., Soares, C. P. and Valle, A. B. (2018) ‘Critical Success Factors on Business Process Orientation’, International Journal of Management, 5(3), pp. 43-61.
Denktaş-Şakar, G. and Sürücü, E. (2020) ‘Stakeholder engagement via social media: an analysis of third-party logistics companies’, The Service Industries Journal, 40(11-12), pp. 866-889.
Deutsche Post AG (DPSGY). (2020). Web.
Deutsche Post AG NA O.N. (DPWGn). (2020). Web.
Deutsche Post DHL Group. (2020) Group management report. Web.
Deutsche Post DHL Group. (2020) Supply chain. Web.
Dijesh, K. J. and Mary, R. R. (2017) ‘Analysis of change models and evolving business strategies for proposed change in dynamic environment’, International Research Journal of Engineering and Technology, 4(3), pp. 1351-1357.
Dolgui, A., Ivanov, D. and Sokolov, B. (2018) ‘Ripple effect in the supply chain: an analysis and recent literature’, International Journal of Production Research, 56(1-2), pp. 414-430.
Effendi, Y. A., Sarno, R. and Innov, J. (2018) ‘Modeling parallel business process using modified time-based alpha miner‘, International Journal of Innovative Computing, Information and Control, 14(5), pp. 1565-1582.
Feng, Y., Hsieh, J. C., Zou, W. J., Chiu, Y. H. and Chen, H. Y. (2018) ‘Evaluating performance of logistics in the FMCG industry’, International Journal of Organizational Innovation, 10(4), pp. 1-9.
Froger, M., Benaben, F., Truptil, S. and Boissel-Dallier, N. (2019) ‘A non-linear business process management maturity framework to apprehend future challenges’, International Journal of Information Management, 49, pp. 290-300.
Gold, S., & Schleper, M. C. (2017) ‘A pathway towards true sustainability: a recognition foundation of sustainable supply chain management’, European Management Journal, 35(4), pp. 425-429.
Goldsby, M. G., Kuratko, D. F., Bishop, J. W., Kreiser, P. M. and Hornsby, J. S. (2018) ‘Social proactiveness and innovation: The impact of stakeholder salience on corporate entrepreneurship’, Journal of Small Business Strategy, 28(2), pp. 1-15.
Herold, D. M. and Lee, K. H. (2017) ‘The influence of the sustainability logic on carbon disclosure in the global logistics industry: The case of DHL, FDX and UPS’, Sustainability, 9(4), p. 601.
Hilorme, T., Zamazii, O., Judina, O., Korolenko, R. and Melnikova, Y. (2019) ‘Formation of risk mitigating strategies for the implementation of projects of energy saving technologies’, Academy of Strategic Management Journal, 18(3), pp. 1-6.
Jagoda, K. and Samaranayake, P. (2017) ‘An integrated framework for ERP system implementation’, International Journal of Accounting & Information Management. Management, 25(1), pp. 91-109.
Ján, D. and Veronika, T. (2017) ‘Examination of factors affecting the implementation of organizational changes’, Journal of Competitiveness, 9(4), p. 5.
Jayakrishnan, M., Mohamad, A. K. and Yusof, M. M. (2018) ‘Assimilation of business intelligence (BI) and Big Data Analytics (BDA) towards establishing organizational strategic performance management diagnostics framework: a case study’, Journal of Digital Information Management, 16(1), pp. 1-14.
Lall, V., Rumb, R., & Dufault, C. (2019). Block chains-the technology and application in supply chain management. Journal of Global Business Management, 15(1), pp. 1-11.
Le, T., Nguyen, T., Phan, T., Tran, M., Phung, X., Tran, T. and Giao, K. (2019) ‘Impact of corporate social responsibility on supply chain management and financial performance in Vietnamese garment and textile firms’, Uncertain Supply Chain Management, 7(4), pp. 679-690.
Limcharoen, A., Jangkrajarng, V., Wisittipanich, W. and Ramingwong, S. (2017) ‘Thailand logistics trend: logistics performance index’, International Journal of Applied Engineering Research, 12(15), pp. 4882-4885.
Liu, Y. (2020) ‘The micro-foundations of global business incubation: Stakeholder engagement and strategic entrepreneurial partnerships’, Technological Forecasting and Social Change, 161, pp. 1-9.
Lukkarinen, J. and Majava, J. (2020) ‘Inventory Management in a Corporation Context’, Management, 20, p. 22.
Mansaray, H. E. (2019) ‘The role of leadership style in organisational change management: a literature review’, Journal of Human Resource Management, 7(1), pp. 18-31.
Masudin, I., Fernanda, F. W., Zulfikarijah, F. and Restuputri, D. P. (2020) ‘Customer loyalty on Halal Meat Product: a case study of Indonesian logistics performance perspective’, International Journal of Business and Society, 21(1), pp. 433-453.
Miraz, M. H., Hye, A. M., Wahab, M. K., Alkurthee, K. A. M., Majumder, M. I., Habib, M. M. and Alsabahi, M. A. (2020) ‘Electronics product promotion and SCM, contemporary research on Bangladesh’, International Supply Chain Technology Journal, 6(01), pp. 1-15.
Montgomery, D. C. and Borror, C. M. (2017) ‘Systems for modern quality and business improvement’, Quality Technology & Quantitative Management, 14(4), pp. 343-352.
Nguyen, T. T. H. (2017) ‘Wal-Mart’s successfully integrated supply chain and the necessity of establishing the Triple-A supply chain in the 21st century’, Journal of Economics & Management, 29, pp. 102-117.
Nikou, S. H., Selamat, H. B., Yusoff, R. C. M. and Khiabani, M. M. (2016) ‘Electronic customer relationship management, customer satisfaction, and customer loyalty: A comprehensive review study’, International Journal of Management and Economics Invention, 2(12), pp. 1133-1144.
Oláh, J., Karmazin, G., Pető, K. and Popp, J. (2018) ‘Information technology developments of logistics service providers in Hungary’, International Journal of Logistics Research and Applications, 21(3), pp. 332-344.
Pant, S., & Mahapatra, S. (2018) ‘Bank mediated financial supply chains: Implications for supply chain strategy and operations’, International Journal of Supply and Operations Management, 5(4), pp. 298-318.
Piyachat, B. (2017) ‘The relationships among resources’ commitment reverse logistics innovation reverse logistics performance and reverse logistics cost savings: Manufacturing vs service industry’, Journal of Administrative and Business Studies, 3(3), pp. 122-135.
Puche, J., Ponte, B., Costas, J., Pino, R. and De la Fuente, D. (2016) ‘Systemic approach to supply chain management through the viable system model and the theory of constraints’, Production Planning & Control, 27(5), pp. 421-430.
Qi, H., Du, Y., Qi, L. and Wang, L. (2018) ‘An approach to repair Petri net-based process models with choice structures’, Enterprise Information Systems, 12(8-9), pp. 1149-1179.
Riazi, S. R. M., Nawi, M. N. M., Salleh, N. A. and Ahmad, M. A. (2019) ‘Collaborative Supply Chain Management (SCM) tools for improved teamwork in construction projects’, International Journal of Supply Chain Management, 8(5), pp. 473-480.
Sabuhari, R., Sudiro, A., Irawanto, D. and Rahayu, M. (2020) ‘The effects of human resource flexibility, employee competency, organizational culture adaptation and job satisfaction on employee performance’, Management Science Letters, 10(8), pp. 1775-1786.
Saleh, S. H., Ismail, R., Ibrahim, Z. and Hussin, N. (2018) ‘Issues, challenges and solutions of big data in information management: an overview’, Int. J. Acad. Res. Bus. Soc. Sci, 8, p. 12.
Sari, N. and Maya, Z. (2018) ‘The effect business process to quality of accounting information systems with survey in BUMN industrial strategies in Bandung Indonesia’, International Journal of Trend in Research and Development, 5(6), pp. 1-4.
Suifan, T., Alazab, M., & Alhyari, S. (2019) ‘Trade-off among lean, agile, resilient and green paradigms: an empirical study on pharmaceutical industry in Jordan using a TOPSIS-entropy method’, International Journal of Advanced Operations Management, 11(1-2), pp. 69-101.
Tarigan, Z. J. H., Basana, S. R. and Siagian, H. (2019) ‘The Effect of Internal Information Management on Firm Performance, through Supplier Partnership and Sustainable SCM’, International Journal of Innovation, Management and Technology, 10(6), pp. 1-8.
Veleva, V., Bodkin, G., & Todorova, S. (2017) ‘The need for better measurement and employee engagement to advance a circular economy: Lessons from Biogen’s “zero waste” journey’, Journal of Cleaner Production, 154, pp. 517-529.
Veselovská, L. (2020) ‘Supply chain disruptions in the context of early stages of the global COVID-19 outbreak’, Problems and Perspectives in Management, 18(2), p. 490.
Wiśniewski, P., Kluza, K., Kucharska, E. and Ligęza, A. (2019) ‘Spreadsheets as interoperability solution for business process representation’, Applied Sciences, 9(2), pp. 345.
Appendxi A
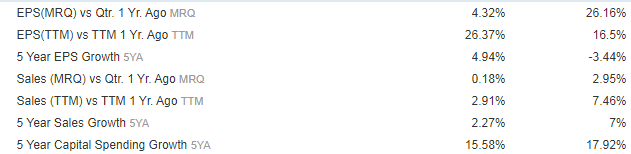