Introduction
Operations management refers to the process of planning and managing the efficient production of goods and services. The application of best business practices can help a company ensure its resources’ rational use, which influences customer service and product quality. This paper focuses on the case study of a company that manufactures tables and cabinets used to hold household appliances. Space Age Furniture Company follows similar production and assembly procedures for its products; however, it requires a solution for the optimization of its production of part 3079. The detail is crafted on a specific machine and used in two further subassemblies: no. 435 for Gemini TV stand and no. 257 for Saturn microwave stand.
However, the machinist Ed Szewczak must be present to run all the company machines, which results in increased workload and job dissatisfaction for him. The operations manager Coral Snodgrass needs to keep the valuable employee and met the production requirements. This paper aims to analyze the case study of Space Age Furniture Company, develop an MRP, suggest ways for improvement of the production, and recommend changes that might benefit the company and its customers.
Material Requirements Planning (MRP)
The Significance of MRP for Operations Management
For operations management, applying efficient techniques and tools is essential to plan and control inventory; in particular, the Material Requirements Planning (MRP) system is widely used. If done correctly, MRP ensures the fluent flow of raw materials and parts available in the right quantity at the right time. Even though it is challenging to manage materials, it is the primary way to meet customers’ requirements and increase the company’s competitiveness in the market. The MRP system calculates what materials and components are needed and when the order goes into production, based on the current and upcoming orders, demand, the Master Production Schedule, the Bill of Materials, and inventory (Abdullah, 2017).
The system influences the decision-making within the company and significantly benefits the manufacturing process. In particular, it allows for better inventory control, reduces cost, and improves scheduling. Consequently, proper operations management results in improved customer service and on-time delivery of the products. Therefore, MRP can simplify the time-consuming process of materials and orders management and help the manufacturer eliminate errors and effectively plan the production.
MRP for Space Age Furniture Company
Space Age Furniture Company can benefit from the MRP system since it will help optimize the production of Gemini TV stands and Saturn microwave stands, which require part 3079. In this regard, the data from the Bill of Materials (BOM) and Master Production Schedule (MPS) is needed to design an MRP for the company. According to the case study, there is a demand for 1,000 subassemblies 435 and 1,000 subassemblies 257 in week 1. For each subassembly, one part no. 3079 is used, and no inventory is in stock at the beginning of week 1. There are currently no other orders, which means that the machinist can devote his time to the lathe used specifically for part 3079. Given the data, the recommended MRP for Space Age Furniture Company is suggested in Table 1 for the Gemini TV stand and Table 2 for the Saturn microwave stand, respectively.
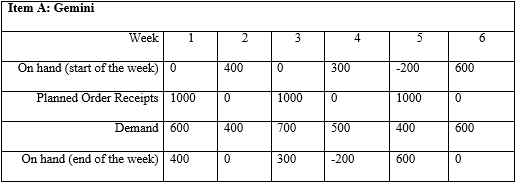
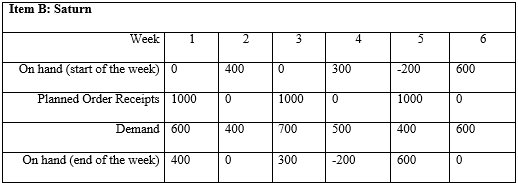
Therefore, the MRP suggests that no stock will be remaining available for each item by the end of week 6. At the same time, holding costs need to be calculated regarding the products that are not shipped immediately. Even though no set-up time is required for the lathe, the processing time is 0.03 hours per unit. Besides, it costs the company $0.25 to store parts an extra week and $0.75 to keep a subassembly unit an additional week. Thus, Space Age Furniture Company will incur a total of $975 for six weeks in relation to holding costs for subassembly 435:
Week 1: 400 * $0.75 = $300
Week 3: 300 * $0.75 = $225
Week 5: 600 * $0.75 = $450
Total holding cost for six weeks: $300 + $225 + $450 = $975
Similarly, the calculations for subassembly 257 imply that Space Age Furniture Company will incur a total of $975 of holding costs for six weeks:
Week 1: 400 * $0.75 = $300
Week 3: 300 * $0.75 = $225
Week 5: 600 * $0.75 = $450
Total holding cost for six weeks: $300 + $225 + $450 = $975
Overall, the holding cost for six weeks for subassemblies 435 and 257 will constitute $1950. In this regard, holding too many stock items is associated with an extra expense for the company, while having too little inventory can result in losing customer confidence in the company’s supply. Therefore, MRP can present a better overview of the problem, and measures can be taken to decrease holding costs. In particular, lot sizing is a crucial aspect of inventory and operations management. The following chapter suggests ways for improvement of subassembly performance and lot sizes.
Suggested Ways for Improvements over Subassemblies in Lot Sizes of 1,000
The subassembly unit performance is crucial for the quality and time of manufacturing of a product. As Abubakar and Wang (2019) report, mixed-model assembly is efficient for performance improvement in manufacturing companies. The case study data suggests that two subassemblies are produced with part 3079, which requires the use of one machine. In this regard, change over time is an essential factor, and the company wishes to minimize it for its production. Change over time refers to the time needed to prepare a device from producing the last good part of the previous procedure to the first good piece of the following process. Minimizing this factor can significantly improve assembly performance.
For Space Age Furniture Company, the goal of reducing change over time can be achieved if the limit of 1,000 parts per batch is set. At the same time, as stated in the case study, no issue with the capacity of the device is present. Hence, the company might improve its subassemblies performance by eliminating the production time waste. In this regard, it is crucial to take into account configurations (Abubakar & Wang, 2019).
The production of subassemblies does not require complicated configurations, and simplifying them can help reduce the production time of subassemblies no. 435 and no. 257 used for final products. Besides, the performance can be improved when the lot volume moves quicker, and when the number of parts loaded is reduced. With the implementation of the steps mentioned above, Space Age Furniture Company should be able to optimize its subassembly performance and reduce the change over time.
The Trade-off between Overtime Costs and Inventory Costs
Different trade-offs need to be considered when calculating the overtime cost and inventory cost. According to Lemmens (2018), both calculations are essential to reduce the supply chain costs since they account for finding the point where the gain overcomes the expense. Overtime production is a result of the manufacturer’s attempt to meet the clients’ excess demand, which requires additional labor and inventory.
The company incurs overtime costs when it needs to pay employees who work extra hours to finish pending work. At the same time, inventory costs for the organization result from maintaining inventory and can include storage costs, insurance, and taxes. A cost-benefit analysis is required for the company to choose the action plan in which expenses are minimized, and benefits are maximized. In this regard, MRP can be applied to manage the expenses and reduce overtime costs.
Achieving a balance between the overtime costs and inventory costs requires a management approach to schedule productions in accordance with the demand. In the given scenario, the machinist’s hourly wage is $22, while overtime results in a 50% premium for the employee. Earnings for Ed for one hour of overtime are $33. The cost of holding each unit can help determine the best practice for Space Age Furniture Company. In this regard, the processing time per unit is 0.03 hours; hence, the number of units produced in one hour is 2000.
Considering it costs $0.75 to keep a subassembly unit for a week, the cost of holding 2000 units for a week is $1500. Thus, the trade-off is as follows: the company will spend $1500 for keeping subassemblies in the inventory for a week, while the overtime cost for the employee’s additional hour of labor will be $33. It is clear that the company should choose to pay overtime instead of preferring the costs of holding extensive inventories.
Overall, the right scheduling algorithm can lower the production cost and help the company choose the right strategy. According to the MRP for Space Age Furniture Company, its main inventory costs result from large amounts of components needed for the two items. Therefore, with one employee who has to work overtime, the inventory costs will increase eventually. In this regard, the base MRP needs a reevaluation in order to manage the costs better.
A New MRP That Improves the Base MRP
Improving the initial MRPs is crucial to enhance the performance and manage inventory and costs better. There are different ways to enhance the calculations: for instance, by incorporating additional elements. In this regard, the base MRP for Space Age Furniture Company can be improved if the total number of items produced per week is obtained. The improved MRPs for the company can be based on the calculations made using data from the Master Production Schedule (see Table 3).

The calculations below present the number of items in demand for subassemblies no. 435 and no. 257:
Week 1: 600 + 300 = 900.
Week 2: 400 + 400 = 800.
Week 3: 700 + 400 = 1100.
Week 4: 500 + 600 = 1100.
Week 5: 400 + 300 = 700.
Week 6: 600 + 300 = 900.
Considering that subassemblies are items that are required in one unit for each final product, the gross requirements will remain the same. Therefore, dropping the number of produced units will equally reduce the number of subassemblies produced. Consequently, it will lower the number of parts no. 3079 produced to be used in subassemblies. As mentioned above, storing the inventory implies significant expenses for the company, and reducing the number of units will help minimize the total cost. Space Age Furniture Company can increase its production performance by leveling and reducing waste. In particular, the situation when demand is constant is more advantageous for managers. Assuming that the demand is continuous, the calculations based on master schedule data can help balance the production process.
The Types of Production Processing and the Primary Mode of Operation
Manufacturing companies are involved in the process of transforming raw materials into finished products. The production processing needs to be considered, and three essential types need to be differentiated between for a better understanding of the operations management within the company. In this regard, a job shop, batch, and repetitive or continuous production are considered three major types of production processing. Establishing the primary operation mode for the company is a determinant of its performance and efficiency.
A job shop refers to the process when a facility produces a number of products with a small volume. In other words, the term job shop can be used to define a small manufacturing network, which enables the company to proceed to a new assignment once the previous task is completed (Sharma & Jain, 2016). This mode usually involves performing tasks for different customers and requires machines combined based on their functions and technological expertise. Machine shops or tools manufacturers can be considered an example of a job shop. Since not all tasks are constrained to one device, the production process is rather flexible.
In turn, a batch process is used to describe a manufacturer who carries out automated tasks and does not involve manual interfering. Put differently, the production line has a set of instructions that enables the machine to complete tasks without human intervention in the operations (Zhu et al., 2018). Batch processing is efficient since it helps produce high volumes, compared to the alternative of job shops.
Another type of production processing, repetitive production, refers to the method that allows the companies to produce sets of identical items. Mass production occurs, and the whole manufacturing process revolves around it. In this regard, such an approach is associated with reduced inventory cost, while, in turn, lower production cost results from minimized inventory expenses. Hence, companies that have implemented the repetitive production as their primary method benefit from reduced expenses in the long term.
Even though all three production types are common among manufacturing companies, the job shop is often viewed as the primary mode of operation. This statement can be explained by the nature of the processing in a job shop, which repeatedly performs the production of different items. It is no doubt that batch and repetitive production play an essential role in the production process; however, the approach applied in job shops can help the manufacturer produce any products altogether. At the same time, when choosing the primary mode of production, one should always consider the content delivered and its characteristics rather than the time required.
Ways for Management to Keep Track of Job Status and Location During Production
Monitoring and enhancing the production process constitutes one of the crucial tasks of operation management. In this regard, job status and location need to be considered to assess the production line’s efficiency. The job status in a company involves the production time of a given product. For Space Age Furniture Company, customer orders define the demand marked in the master production schedule, and the products are shipped as soon as possible. The job status can help the company establish the phase of production of subassemblies and improve on-time deliveries.
In this regard, developing a production plan and using MRPs and tracking software can help managers monitor job status during production. In turn, the location of the goods is another essential factor that defines the delivery time for a product. The use of MRPs and computer software by managers can help them manage the location during production. Overall, cost-effective and time-saving solutions can be implemented using automated monitoring techniques.
Recommended Changes for the Company
Considering the analysis of the case study presented above, Space Age Furniture Company can implement changes to enhance its performance and optimize the production process. The main issue is the fact that a skilled machinist has to do frequent overtime to operate a special lathe producing the details for subassemblies. Job dissatisfaction can lead to the loss of a valuable employee, and the manager needs to keep the machinist without compromising the on-time delivery of the items. In this regard, using MRP and enhancing it is the first step to improve the performance and monitor the production.
Besides, simplifying the machine configurations can help reduce the production time of the subassemblies. Acquiring another machine or employing another machinist can be beneficial in terms of saving time and increasing production rates. However, purchasing another device can involve a significant investment, while opting for an outsourcing program can be considered a reasonable decision. As to the overtime issue, the company can implement various shifts to help the employee avoid professional burnout and retain the job. Overall, a combination of the methods mentioned above can benefit the Space Age Furniture Company.
To sum up, Space Age Furniture Company can benefit from utilizing the developed and improved MRP and managing the production process on various levels. MRP is an essential contribution to the manufacturer’s performance, and it is highly recommended that the manager employs the system and additional software to improve the production line. At the same time, resolving the issue of the employee’s dissatisfaction with his overtime requires a comprehensive approach and managerial decisions made within a company, such as acquiring another lathe or employing an additional machinist.
References
Abdullah, A. M. A. (2017). Evolution of enterprise resource planning. Excel Journal of Engineering Technology and Management Science, 1(11), 1-6. Web.
Abubakar, M. I., & Wang, Q. (2019). Key human factors and their effects on human centered assembly performance. International Journal of Industrial Ergonomics, 69, 48-57. Web.
Lemmens, S. (2018). The trade-off between inventories, lead time and capacity: Application to vaccine supply chain design (Publication No. 621) [Doctoral dissertation, Ku Leuven]. Lirias.
Sharma, P., & Jain, A. (2016). A review on job shop scheduling with set-up times. Proceedings of the Institution of Mechanical Engineers, Part B: Journal of Engineering Manufacture, 230(3), 517-533. Web.
Zhu, J., Wang, Y., Zhou, D., & Gao, F. (2018). Batch process modeling and monitoring with local outlier factor. IEEE Transactions on Control Systems Technology, 27(4), 1552-1565. Web.