Introduction
The manufacturing industry is one of the most competitive economic sectors due to intense rivalry from different players competing to produce quality products to meet customer demand. At the same time, managers have to balance quality concerns with cost considerations – a fete that some firms find difficult to achieve (Davim, 2018). In this regard, some firms have to tweak their production processes to find a balance between the above-mentioned considerations. This process may involve recalibrating key activities relating to the movement of raw materials or physical goods through a series of steps to achieve an optimum balance between quality and cost considerations (Nabi & Aized, 2019; Jasti & Sharma, 2014). Relative to this assertion, companies are under increased pressure to improve the efficiency of their manufacturing processes (Levinson, 2017; Trubetskaya & Mullers, 2021). Some of them have adapted to these pressures by adopting leaner and more efficient techniques of production, such as lean manufacturing and Six Sigma tools.
As its name suggests, lean manufacturing is focused on promoting efficiency in production. In other words, it is an efficient model for identifying areas of wastage in a company’s production process and correcting the same by adopting the technique (Elbert, 2018; Silvério, Trabasso, & Pereira Pessôa, 2020). Stewart (2018) assumes that the popularity of the concept stems from the constant pressure that firms are under to produce quality goods and services with limited resources. Lean manufacturing is closely related to the principle of Just-in-Time (JIT) production, which seeks to promote efficiency by eliminating static processes in production (Edem & Hans, 2018; AME, 2017; Guo, Jiang, Xu, & Peng, 2019). The lean production model also traces its roots to Toyota, a Japanese car automaker, which was among the first companies to embrace the concept in its manufacturing model (Pinto, Matias, Pimentel, Azevedo, & Govindan, 2018). Toyota adopted the model with two key objectives in mind.
The first one was to minimize waste, and the second one was to streamline its production processes. In Japanese philosophy, these objectives are defined as “Muda” and “Mura,” respectively (Edem & Hans, 2018; Stewart, 2018). Collectively, they have four main priority areas, which are to improve quality, eliminate waste, minimize production time, and reduce the cost of manufacturing (Wang, Zheng, & Li, 2018; Márquez, Segovia, Bányai, and Tamás, 2020). Given the centrality of these goals to production efficiency, the business philosophy is founded on the need to identify and minimize waste as part of a continuous improvement process to make companies more efficient and productive (Stewart & Kelley, 2020). Therefore, a key feature of lean manufacturing is a waste reduction with a keen focus on customer value maximization.
In this document, modalities for the application of lean management techniques will be explored using a manufacturing company known as Evernot as a case study. However, before delving into the details of the analysis, examples of the application of industry lean production methods will be explored in the literature review section. The aim is to understand the lessons and opportunities that firms, which have adopted the model pose to its adoption. The information obtained in this section of the analysis will be instrumental in providing a background to the application of the model in manufacturing processes. Emphasis will be made on understanding strategies chosen by companies when implementing this model and the challenges they face as a result. The lessons to be learned in the analysis will also be documented in the present study with a view to improving future applications of the concept. In subsequent sections of this paper, these lessons will be used to explain how lean manufacturing tools, including Six Sigma could be adopted or implemented at Evernot. However, before delving into these details, it is important to understand the background of the company.
Company Background
Evernot is based in South Yorkshire, England, and is seeking to enhance its efficiency through the adoption of lean manufacturing processes. The companies mainly produces steel/alloy flanges and processed bars using advanced manufacturing, deep water shipment techniques, and plasma cutting tools. In other words, the business engages in plasma cutting and provides high-quality bespoke products to its customers. Although the company has a market presence in various locations, the focus of this study will be on its headquarters, where flanges are cut and developed into semi-finished forgings. These items are often purchased at Hilton Metal Forging Ltd, which is an Indian subsidiary of the main company. By collaborating with Sheffield Hallam University, the company seeks to improve the odds of adopting its change management strategy through knowledge transfer.
Typically, Evernot produces flanges that are manufactured and delivered to customers within a 24-hour business cycle. In the last few years, the company’s manufacturing capacity has expanded as the demand for its products increased. The firm has been experiencing challenges meeting the increased demand because of physical limitations inhibiting expansion at its corporate headquarters. This has left little room for increasing its overall layout to accommodate an expanded manufacturing plant. Lean Six Sigma emerges as a useful tool for navigating some of these challenges because it seeks to optimize production within the confines of the current plant layout. However, making such changes to the firm’s production process requires a keen understanding of the opportunities and challenges that exist in the implementation process. From this background, it is important to understand the experiences that other companies have had with the implementation of this model.
Literature Review
The merits associated with the adoption of Lean Six Sigma technique are undisputed because of the existence of several case studies showing the model’s success in maintaining or supporting organizational success in various industries. Table 1 below presents a summary of the application of these techniques in different industries and the strategies that have been implemented to realize their benefits.
Table 1. Application of the Lean Six Sigma techniques in industries
Overall, lean manufacturing processes are inclined to generate cost savings as well as improve a company’s image because of their contemporary nature. For example, Six Sigma techniques have been highlighted as tools for improving a firm’s product acceptability (Pande, Neuman, & Cavanagh, 2000; Maware & Adetunji, 2019). Cox, Gaudard, and Stephens (2016) opine that the lean manufacturing method is also useful in simplifying decisions relating to the production process because value-mapping techniques help to identify issues that are of critical importance to the overall manufacturing process but receive less attention. In this regard, they argue that lean production is only useful when its advantages are embraced and its disadvantages avoided (Guo et al., 2019). By ranking production problems, the tool helps managers to allocate their resources towards those that are most impactful to the production process.
As highlighted above, the benefits of adopting lean manufacturing have been highlighted in several journals and scholarly literature. However, some researchers suggest the need to be cautious when adopting the tools in their production processes because some companies have failed to realize the above-mentioned benefits (Atari & Prause, 2019). The problem has been traced to several issues, most of which are firm-specific, but the failure to organize organizational topics, especially in supply chain management, is the most common cause of implementation failure.
Part of the problem has also been attributed to the lack of innovation when implementing lean manufacturing processes in organizations, as it is deemed an important part of the implementation. In this regard, networked systems have been cited as innovative techniques used by modern organizations to circumnavigate this challenge (Moon, Lee, Park, Kiritsis, and von Cieminski, 2018). Vidal (2017) also alludes to this problem by highlighting human weaknesses in lean manufacturing implementation. She mentions the rational choice theory as an example of assumptions that people make when implementing lean manufacturing under the assumption that managers have the same capability to utilize information in the same way as computers do (Vidal, 2017). Given these limitations, it is proposed that a bottom-up model of lean manufacturing implementation should be adopted.
The American manufacturing sector has embraced such an approach and now boasts of having employee welfare and lean production models ingrained in their institutional culture. In this assessment, part of the problem associated with the implementation of lean manufacturing processes is having moderate aspirations, such that defective aspects of its performance are embraced for the sake of integration (Vidal, 2017). In this regard, there is a need to be cognizant of firm-specific limitations affecting the adoption of lean manufacturing.
Value Stream Maps
Current and future value stream maps for the Everton case study will be highlighted in this section. Faulkner and Badurdeen (2014) say that the implementation of lean manufacturing methods depends on the development of robust value stream maps. However, critics suggest that this approach is limiting because it has various shortcomings, some of which demand that a simulation be effectively adopted. According to the value stream map highlighted in figure 1 below, three levels of operation emerge. The first one is the business level, where superficial aspects of firm performance are discussed. The cell level is the second one, which provides more detail about the business-level strategies highlighted above. The third level is the process mapping stage, where complete details are provided at a cell level. Overall, this value stream map looks at several factors affecting production, including material flows, information flows, and lead-time development.
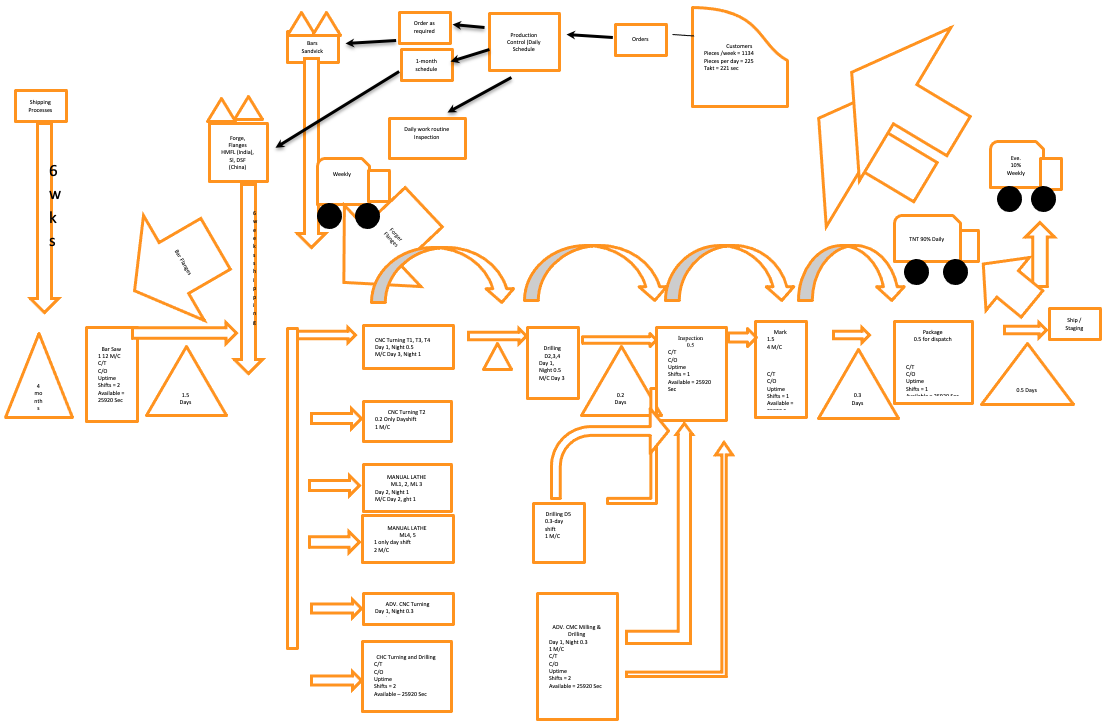
Assumption about Batch Size
Three different product categories will be used to make assumptions about batch sizes when developing future value stream maps. For the first product route, 137 parts will be manufactured, and 20 items will be available for inspection to make sure that the rest of the batches meet the preferred standard of measurement. Alternatively, 45 units will be used for inspection. In the second product route, 40 parts will be available for inspection for Mazak Int 200, while Mazak Int 300 will have 17 parts for inspection. Alternatively, Mazak VAZ 500 will provide 77 pieces for inspection in the second product route, with 5 parts available for inspection and 10 for packaging. Assumptions about the third product route will be relevant to CNC-T2, M-L3, L4, and 16 parts and will be available for inspection with five parts relevant to the analysis. However, for CNC-D5, six parts will be available for review in two product categories. Four items will be used for inspection and a similar number of products for packaging. Based on these assumptions, the future value stream for Evernot emerges in figure 2 below.
Future Value Stream Map
The future value stream for Evernot is based on changes to be made from figure 1 above. The result is depicted below.
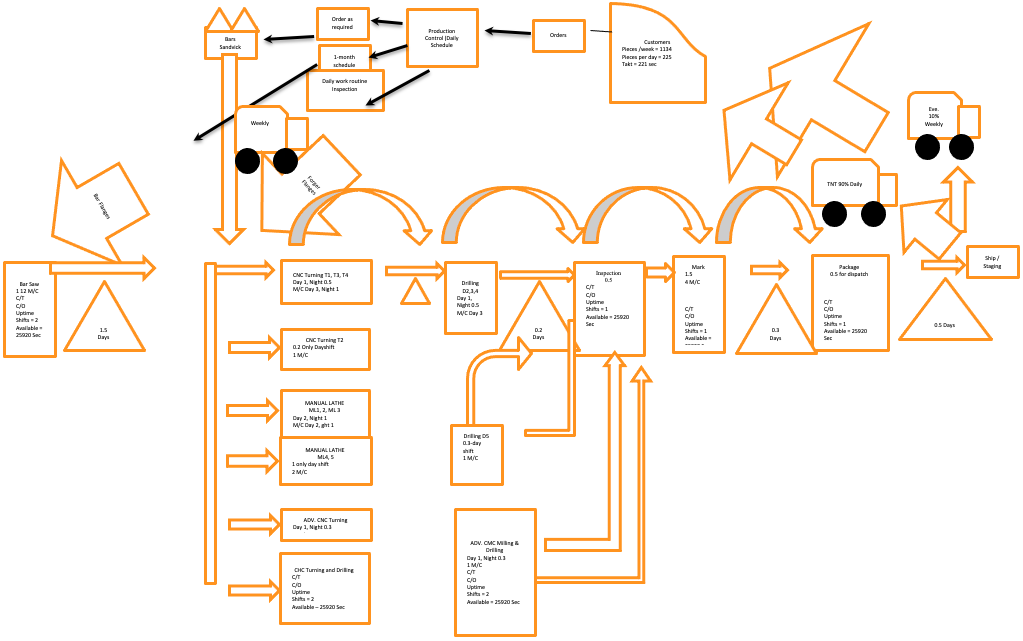
As highlighted in figure 2 above diagram, the future value stream map has been simplified by eliminating lengthy shipping processes. This means that six weeks required to process overseas products are eliminated and substituted with road and air transportation, which could take a lesser time to complete. There is also no urgency in implementing the mapping process because it is not critical to the performance of every product category. For example, according to the future value stream map identified above, this process is not critical to the first product category. It means that implementation may not happen within a month, as it may take several of them to identify the right markets of production. The diminished relevance of marking in the entire value chain process is informed by the fact that it primarily involved labeling the products. This activity could imply significant changes for the organization if implemented during the initial phases of growth because a wrong label could spoil an entire batch of products. This is why in the first product category, labeling is not emphasized as a critical process.
Implementation Plan
Based on a review of the findings highlighted above, implementing industry Lean and Six Sigma techniques may require a careful review of approaches to be followed in the plan. In this section of the paper, recommendations for implementing the models in Evernot are highlighted. Implementing the proposed value stream map will require a keen understanding of organizational processes and the limitations of the production.
The implementation plan will be adopted in three phases, each representing different product categories for the organization. The importance of implementing the plan in three phases is to avoid product distortions for the different value categories highlighted in the plan. Furthermore, by implementing the model in batches, it would be possible to identify challenges that may emerge in each phase of the project. Consequently, it would be possible to address them before moving into a new phase of development. Researchers such as Pinto et al. (2018) emphasize its adoption in critical manufacturing processes because the failure to understand the challenges relating to one product category could compound the implementation plan for other product categories. Therefore, the implementation plan will be undertaken in phases, which are expected to last a couple of weeks for each product category. As each product category is being implemented, other aspects of production are expected to be ongoing. However, the modalities for their operations will be dependent on legacy systems because it is not the intention of the managers to fundamentally change the production process.
The benefit to be gained from adopting this implementation plan is the centrality of organizational operations because, in as much as new systems and processes are expected to be adopted, there is a need to standardize production processes to make sure that significant changes are not registered on the product characteristics. In other words, the intention is to change how the system works for better efficiency and not to change fundamental aspects of the product categories. The latter could have far-reaching marketing implications because current orders are based on a review of existing customer orders, which have not changed much despite the adoption of the Six Sigma method.
Despite the adoption of relevant areas of product implementation, it is not anticipated that the entire change process will be implemented in one phase. It will be done gradually to accommodate changes that may emerge from the implementation process. For example, in the second and third product categories, drilling has been identified as a secondary manufacturing process, thereby leaving room for its implementation at the end of the product review stage. However, the packaging is mentioned as a critical part of the manufacturing process, thereby necessitating its adoption in the early stages of implementation.
The implementation plan is also developed with the understanding that some of the key processes involved in the activity would disappear in a couple of years due to automation. Particularly, processes that involve drilling and marking are likely to be eliminated through automation. This is why they are not given priority in the future value stream of the company. However, those that involve inspection and packaging are prioritized because they require a degree of human input to function effectively. For example, in all the three product categories identified in this paper, inspection is regarded as a critical activity because machines may fail to identify some of the main challenges of product development.
At the same time, problems associated with packaging are also given priority in the implementation phase because of their centrality to the organization’s value system programs. Therefore, in the overall implementation plan, processes that cannot be substituted through automation are given critical importance because of their relevance to the company’s overall production process. Those that can function without human input can be substituted through automation, hence the minimal emphasis on certain product development aspects. Overall, the findings highlighted in this implementation plan suggest that future value stream processes account for the effects of automation and product control throughout all three product categories.
Sustaining Changes
As demonstrated in the literature reviews section of this study, lean manufacturing has been proposed for use at Evernot because of its ability to reduce labor and material costs. Some of the changes proposed to the current value stream model of the organization are intended to promote sustainability as a core principle of the company’s production processes. The United Nations DPI (2018) defines sustainability as a business principle founded on the quest to meet the demands of the business today as in the future. However, as demonstrated by Williams and McDuie-Ra (2017), sustaining these changes in the long-term could be a difficult task because of challenges in implementing sustainable practices in an organization that has traditionally relied on performance-based metrics of assessment. Stated differently, sustaining changes made through the Lean Six Sigma technique could be a difficult task for managers of Evernot. However, to make sure that the changes proposed in the overall care plan are sustainable, it is important to adopt “green” practices.
As part of the green manufacturing process, a key component of the proposed sustainable strategy is to infuse important concepts of performance to Evernot’s overall corporate strategy by integrating the importance of environmental awareness in the manufacturing process. As opposed to overseeing a parallel manufacturing process, the concept of sustainability should be integrated into the existing improved model to provide an enhanced understanding of Evernot’s processes (Schulzki, 2019). Given the challenges experienced in implementing industry lean and Six Sigma techniques highlighted in this study, the process of sustaining proposed improvements at Evernote could still be challenging.
In this section of the study, proposals are provided on how to sustain some of the proposed changes mentioned in this study. Chen, Fortuny-Santos, Lujan, and Ruiz-de-Arbulo-Lopez (2019) give reasons for the need to adopt sustainable management practices when adopting the Lean Six Sigma method because antecedents of lean manufacturing are increasingly being based on a company’s production capacity. In this regard, they believe that current discussions on sustaining changes brought by the adoption of lean manufacturing need to be factored within the broader context of “greening” production processes (Zokaei, Lovins, Wood, & Hines, 2017; Chen et al., 2019). Although proponents of this school of thought argue that lean production models will have different impacts on varied stages of production (Ijagbemi & Campbell, 2017), the overall model should be implemented within the prism of environmental sustainability. In this regard, the lean sigma method should be part of the sustainable management of production functions.
It is important to make sure that various facets of performance are accounted for in the lean manufacturing model, including the environmental and social performance of lean manufacturing systems. Relative to this statement assertion, Brown, Amundson, and Badurdeen (2014) and Dao, Howlett, Setchi, and Vlacic (2018) add that a sustainable lean manufacturing process should take into account several factors, including product design, manufacturing processes, and manufacturing systems. The goal is to make sure that lean manufacturing processes effectively address the intricacies of an entire supply chain system (Ijagbemi & Campbell, 2017; Socconini & Reato, 2019). Traditional value stream mapping has been identified as lacking the above-mentioned components of sustainable development (Brown et al., 2014). Conversely, it means that the main difference between traditional and contemporary value stream modeling is the addition of environmental and social goals in the broader assessment of organizational processes.
Businesses have to follow specific steps to realize their sustainable goals. Faulkner and Badurdeen (2014) say that one of the first steps of guaranteeing sustainable production is to examine current practices and modalities for changing them to accommodate better management practices. Therefore, extending value stream mapping procedures should be done with the recognition that they should account for the environmental and social impact of the value stream model (Rother and Shook, 2003; Trubetskaya & Mullers, 2021). Figure 3 below shows the distinction between different types of manufacturing processes, including traditional, lean, green, and sustainable manufacturing.
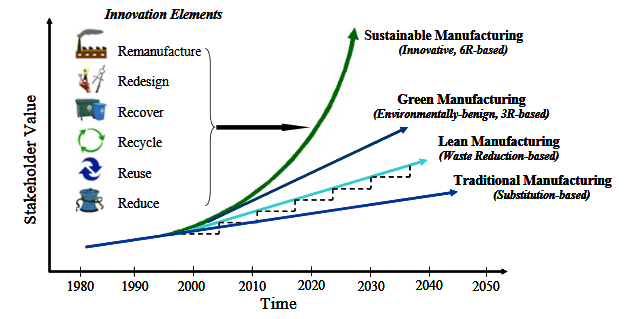
As highlighted in figure 1 above, stakeholder value in manufacturing has changed with the evolution of manufacturing strategies. For most parts of the 1980s up to the early 2000s, traditional manufacturing represented a bigger share of the value that stakeholders got from participating in manufacturing processes (Thakur, 2019). This model evolved into lean manufacturing, where the emphasis has been on waste reduction, and the ultimate goal is to promote efficiency.
The model has since paved the way for the adoption of green manufacturing systems, which strive to promote the adoption of environmentally friendly manufacturing and production processes (Management Association, Information Resources, 2019). Today, sustainable manufacturing has taken center stage in scholarly discussions (Camp, 2013). It is associated with the adoption of innovative techniques in production, which may include remanufacturing, redesigning, recovering, recycling, reusing, and reducing the use of materials. In this regard, sustainable manufacturing contains different elements of other manufacturing processes that came before it but with the emphasis being on innovation to promote a firm’s competitiveness.
Overall, the lean manufacturing techniques proposed in this study have been proposed to have a sustainable focus because of their ability to minimize the negative environmental impact of their business processes and conserve the organization’s limited resources. The green manufacturing processes outlined above are part of a continuous improvement strategy proposed to boost Evernot’s productivity and competitiveness in the industry. A systems approach may also be used to integrate sustainable aspects of Evernot’s lean manufacturing processes with their traditional characteristics. The system approach is focused on critically evaluating the company’s upstream and downstream processes by examining the role of customers and suppliers in the overall process (Perumal, 2020). In this assessment, the focus should be on the design and innovation of the company’s production processes. The greening process is likely to make the company’s production model leaner and efficient. Additionally, to make its production process more environmentally focused, it is important to first adopt the principles of lean manufacturing, which include equipment reliability and operator care programs.
Compatibility of Lean Sigma with Environmental Goals
Environmental goals should be at the center of all production processes because of their importance in developing sustainable business practices. In the context of this review, sustainability is identified as an important organizational process because it captures the aspirations of different stakeholders involved in the overall care review process. Part of the discussion stems from the relationship between human processes and nature. For example, it is believed that a significant part of our DNA comes from ancient bacteria (Hendler, 2009). In this regard, the past is a window through which future processes should be reviewed and evaluated.
The global climate change crisis that is ongoing today is partly a creation of our unwillingness to confront challenges that exist in our production processes. There is little commitment by those who benefit the most from the current state of affairs because they show little or no resolve to change things as they are. The blame particularly goes to rich countries, which are responsible for a significant part of the greenhouse gas emissions emitted in the world today (Hendler, 2009). Regardless of the difficulties in changing the current state of affairs, managers can adopt firm-level changes that contribute towards the development of a sustainable future. This statement explains why it is important to evaluate the production processes of Evernot to identify areas of improvement or control that could be used to promote the realization of this goal. One way of doing this is to review materials used in production processes to adopt those that have a minimal environmental impact.
Relative to the above statement, Evernot uses alloy as its main production raw material. This substance is appropriate for use in the company because it has a minimal environmental impact. In other words, it does not negatively affect the environment, regardless of whether it is sour or acidic. There are ongoing efforts by researchers to look for newer techniques for minimizing the environmental impact of production processes because there is a promise that they could eliminate the negative impact of the raw materials used in production (Ijagbemi & Campbell, 2017). This attempt at reducing the environmental impact of production is consistent with the goals of the Six Sigma and lean production methods because they also strive to promote efficiency as a function of production processes (Hendler, 2009). Therefore, it is critically important for Evernot to pursue this line of development.
Regardless of the efforts made by Evernot to reduce its environmental impact, it is still important to understand the contribution made by the company in creating the current state of affairs. For example, some of the company’s activities are aimed at bolstering the activities of the oil and gas industry, which is responsible for a significant portion of greenhouse gases emitted in the world today (Hendler, 2009). In other words, the company’s main clients are located in the oil and energy industry because they are the biggest users of this raw material. At the risk of halting the company’s operations, it is important to review the contribution made by the company with the goal of understanding important areas of production that could be changed to yield better results. The use of more efficient materials is only one among a series of other strategies that can be adopted to achieve this goal.
Broadly, it is crucial to appreciate the need to balance environmental interests and environmental concerns when implementing Evernot’s future value stream model. Automation is proposed as an alternative measure that can be adopted to improve the company’s overall standing in the environmental protection space. It represents the need to protect legacy systems and reduce the impact of existing processes on the environment. At an international level, the United Nations Climate Change Conference plays a critical role in developing consensus among nations on how best to protect the environment as they pursue their economic goals. It seeks to secure the commitment of various actors and players that they would seek to reduce their emissions by following agreed standards and modes of operations that bind partner states (Bodansky, Brunnée, & Rajamani, 2017; Sartal, Bellas, Mejías, & García-Collado, 2020). Given the implications of climate change on our environment, following the above-mentioned proposals will have a significant impact on the application of the Lean Six Sigma method (Roos, Womack & Jones, 2014). Particularly, discussions on whether some of its associated tools should be avoided or embraced remain a critical part of contemporary discussions on how companies should balance environmental and economic interests (Zheng & Ming, 2017). Relative to these discussions, this study shows that the application of the Six Sigma model at Evenort is still compatible with strategies adopted by nations in reducing emissions, as per the Conference of the Parties (COP) 26 agreements.
Consistency is observed because Lean Six Sigma tools seek to promote efficiency in production processes, which signifies minimized resource use and efficient production processes, which are consistent with the goals of COP 26. In other words, the Six Sigma tools are still relevant with the goal of being “green.” Relative to the above discussions, the organization’s leadership should be changed to be consistent with the new focus (Zheng & Ming, 2017). Leadership is highlighted as a critical change factor because of its centrality in harnessing organization’s resources to achieve common objectives. One of the techniques through which lean manufacturing can help to achieve the goals of COP 26 is through waste minimization. Lean manufacturing is specialized in this area of assessment because it has been used to make production processes more efficient and responsive to the needs of an organization, based on its ability to minimize waste (Hendler, 2009). Waste minimization is one of the objectives of COP 26, alongside other environmental management goals, such as recycling and reusing materials. The lean manufacturing method fits within this narrative because it focuses on continuous improvement as a basis for improving a company’s products or services. Therefore, it promotes the sustainability of business operations via the flow of products or services in a manufacturing unit.
Conclusion
This paper has highlighted the role of Lean and Six Sigma management models in streamlining organizational processes for purposes of improved service delivery. These models seek to improve efficiency in production without making significant alterations to legacy stems involved in production. In this regard, the proposals mentioned in this paper avoid sudden shifts in production that may be detrimental to the future sustainability of its operations. Furthermore, drastic changes to production systems may affect current and future customer orders. Consequently, the proposals mentioned in this document seek to provide a seamless crossover of current and future value streams. At the same time, automation and the use of environmentally friendly materials are proposed as some of the ways through which sustainability in production can be improved. Its goals align with those of the Six Sigma lean production models because the latter seeks to minimize waste and promote production efficiency, while the former looks for ways of safeguarding this progress in the long term. Therefore, the process of implementing this plan should be undertaken with practical and environmental goals in mind.
References
Adeyemi, B., Ogbeyemi, A., & Zhang, W. (2021). Combining simple motion measurement, lean analysis technique and historical data review for countering negative labor cost variance: A case study. International Journal of Engineering Business Management, 13(3), 1-5.
Alkunsol, W. H., Sharabati, A. A., Alsalhi, N., & El-Tamimi, H. S. (2018). Lean Six Sigma effect on Jordanian pharmaceutical industry’s performance. International Journal of Lean Six Sigma 10(4), 1-11.
AME. (2017). Sustaining lean: Case studies in transforming culture (3rd ed.). CRC Press.
Atari, S., & Prause, G. (2019). Lean intrapreneurship for networked manufacturing enterprises. Journal of Entrepreneurship and Innovation in Emerging Economies, 5(1), 10–21.
Bodansky, D., Brunnée, J., & Rajamani, L. (2017). International climate change law. Oxford University Press.
Brown, A., Amundson, J., & Badurdeen, F. (2014). Sustainable value stream mapping (Sus-VSM) in different manufacturing system configurations: Application case studies. Journal of Cleaner Production, 85(2), 164-179.
Camp, R. B. (2013). Sustainable lean: The story of a cultural transformation. CRC Press.
Chen, P., Fortuny-Santos, J., Lujan, I., & Ruiz-de-Arbulo-Lo´pez, P. (2019). Sustainable manufacturing: Exploring antecedents and influence of total productive maintenance and lean manufacturing. Advances in Mechanical Engineering, 11(11), 1–16.
Cox, I., Gaudard, M. A., & Stephens, M. L. (2016). Visual Six Sigma: Making data analysis lean. John Wiley & Sons.
Dao, D., Howlett, R. J., Setchi, R., & Vlacic, L. (Eds.). (2018). Sustainable design and manufacturing 2018: Proceedings of the 5th international conference on sustainable design and manufacturing. Springer.
Davim, J. P. (2018). Progress in lean manufacturing. Springer.
Edem, G. T., & Hans, C. (Eds.). (2018). Lean Six Sigma for optimal system performance in manufacturing and service organizations: Emerging research and opportunities: emerging research and opportunities. IGI Global.
Elbert, M. (2018). Lean production for the small company. CRC Press.
Faulkner, W., & Badurdeen, F. (2014). Sustainable Value Stream Mapping (Sus-VSM): methodology to visualize and assess manufacturing sustainability performance. Journal of Cleaner Production, 85(2), 8-18.
Guo, W., Jiang, P., Xu, L., & Peng, G. (2019). Integration of value stream mapping with DMAIC for concurrent Lean-Kaizen: A case study on an air-conditioner assembly line. Advances in Mechanical Engineering, 11(2), 1–17.
Gurumurthy, A., & Kodali, R. (2011). Design of lean manufacturing systems using value stream mapping with simulation. Journal of Manufacturing Technology Management, 22(4), 444-473.
Hendler, B. (2009). True Earth; The short history of our planet. Sydney: Australian Broadcasting Corporation.
Hill, J., Thomas, A. J., Mason-Jones, R. K., & El-Kateb, S. (2018). The implementation of a Lean Six Sigma framework to enhance
operational performance in an MRO facility. Production & Manufacturing Research, 6(1), 26-4.
Ijagbemi, C., & Campbell, H. (2017). Skills development for sustainable manufacturing. Books on Demand.
Jasti, N. V. & Sharma, A. (2014). Lean manufacturing implementation using value stream mapping as a tool: A case study from auto components industry. International Journal of Lean Six Sigma, 5(1), pp. 89-116.
Levinson, W. A. (2017). Lean management system: A framework for continual lean improvement. CRC Press.
Management Association, Information Resources. (Ed.). (2019). Sustainable business: Concepts, methodologies, tools, and applications: concepts, methodologies, tools, and applications. IGI Global.
Márquez, P. G., Segovia, I., Bányai, T., & Tamás, P. (Eds.). (2020). Lean manufacturing and Six Sigma: behind the mask. Books on Demand.
Maware, C., & Adetunji, O. (2019). Lean manufacturing implementation in Zimbabwean industries: Impact on operational performance. International Journal of Engineering Business Management, 11(6), 1-12.
Moon, I., Lee, G. M., Park, J., Kiritsis, D., & von Cieminski, G. (2018). Advances in production management systems. Production management for data-driven, intelligent, collaborative, and sustainable manufacturing: IFIP WG 5.7 International Conference, APMS 2018, Seoul, Korea, August 26-30, 2018, Proceedings, Part I. Springer.
Nabi, H. Z., & Aized, T. (2019). Modeling and analysis of carousel-based mixed-model flexible manufacturing system using colored Petri net. Advances in Mechanical Engineering, 4(1), pp. 1-11.
Pande, P., Neuman, R. and Cavanagh, R., (2000). The Six Sigma way. McGraw-Hill.
Perumal, P. A. (2020) Lean dominancy. UTeM Press.
Pinto, Q., Matias, J. C., Pimentel, C., Azevedo, G., & Govindan, K. (2018). Just in time factory: Implementation through lean manufacturing tools. Springer.
Roos, D., Womack, J. and Jones, D., (2014). The machine that changed the world: Free Press.
Rother, M. and Shook, J., (2003). Learning to see. Dansk Industri.
Sartal, A., Bellas, R., Mejías, A. M., & García-Collado, A. (2020). The sustainable manufacturing concept, evolution and opportunities within Industry 4.0: A literature review. Advances in Mechanical Engineering, 6(1), pp. 1-11.
Schulzki, E. (2019). The global institutionalisation of environmental protection measures by the United Nations. United Nations.
Silvério, L., Trabasso, L. G., & Pereira Pessôa, M. V. (2020). A roadmap for a leanness company to emerge as a true lean organization. Concurrent Engineering, 28(1), 3–19.
Singh, J., Singh, H., Singh, A., & Singh, J. (2020). Managing industrial operations by lean thinking using value stream mapping and Six Sigma in manufacturing unit. Management Decision, 58(6), 1118-1148.
Socconini, L., & Reato, C. (2019). Lean Six Sigma management system for leaders. Marge Books.
Stewart, F., & Kelley, K. (2020). Connecting hands and heads: Retooling engineering technology for the “smart” manufacturing workplace. Economic Development Quarterly, 34(1), 31–45.
Stewart, J. (2018). The Toyota Kaizen continuum: A practical guide to implementing lean. CRC Press.
Takao, M. R., Woldt, J., & da Silva, I. B. (2017). Six Sigma methodology advantages for small- and medium-sized enterprises: A case study in the plumbing industry in the United States. Advances in Mechanical Engineering, 9(10), 1–10.
Thakur, A. (2019) The lean Six Sigma dictionary: Explaining the basics of continuous improvement. ARTH-Excel.
Trubetskaya, A., & Mullers, H. (2021). Transforming a global human resource service delivery operating model using Lean Six Sigma. International Journal of Engineering Business Management, 13(2), 1–16.
United Nations DPI. (2018). Yearbook of the United Nations 2013. United Nations.
Vidal, M. (2017). Lean enough: Institutional logics of best practice and managerial satisficing in American manufacturing. Sociological Research for a Dynamic World, 3(2), 1–17.
Wang, J., Zheng, L., & Li, J. (2018). A critical review on the sources and instruments of marine microplastics and prospects on the relevant management in China. Waste Management and Research, 36(10), 898–911.
Williams, M., & McDuie-Ra, D. (2017). Combatting climate change in the pacific: The role of regional organizations. Springer.
Yusof, N. S. B., Sapuan, S. M., Sultan, M. T., & and Jawaid, M. (2020). Materials selection of “green” natural fibers in polymer composite automotive crash box using DMAIC approach in Six Sigma method. Journal of Engineered Fibers and Fabrics, 15(1), 1–13.
Zheng, M., & Ming, X. (2017). Construction of cyber-physical system–integrated smart manufacturing workshops: A case study in automobile industry. Advances in Mechanical Engineering, 9(3), 1-10.
Zokaei, K., Lovins, H., Wood, A., & Hines, P. (2017). Creating a lean and green business system: Techniques for improving profits and sustainability. CRC Press.