The role of inventory as it pertains to logistics
Generally, an inventory in a logistics process entails materials, waste materials, unfinished goods, finished goods, parts, and assembled goods, which belong to the company. The major role of the inventory is to control the flow of materials within the supply chain to allow the company to meet its future needs at the right time, with the right quantities, and at favorable costs. It protects the company against constraints from external environments. The inventory allows the company to supply goods as needed by the downstream parts (distributors) in the supply chain while it enhances manufacturing or logistics activities.
Managerial decisions to make on inventory in logistics
The main decisions involved are cost control. Hence, the manager must replenish, maintain, and ensure effective utilization of materials for economically sensible outcomes in the supply chain. Strategies of balancing costs associated with storage are imperative in decision-making. Such costs include carrying costs, ordering costs, and stockout costs. In addition, decisions also involve demand forecasting, determining safety stock, replenishment and supply scheduling, storage, and staging of finished goods.
Firms that supply Wal-Mart must have extra inventories to protect them against unforeseen demands. Wal-Mart orders goods frequently, and its supplier’s must-have safety stocks to avoid stockouts. Consequently, Wal-Mart suppliers must be efficient and fast to meet its demands within a short period. Therefore, suppliers of Wal-Mart, particularly fruits and vegetable suppliers, must improve their customer service levels and lead time to meet the company’s frequent demands.
Logistics “optimization”
Logistics optimization entails improvements in significant business processes in order to satisfy customers’ needs and reduce costs. Failure to improve or optimize business processes can result in critical customer dissatisfaction. Therefore, firms must strive to optimize logistics systems with the aim of increasing customer satisfaction. In addition, Logistics Optimization helps companies to reduce their operating costs.
Companies must note that any improvements in their supply chain have cost implications but enhance customer service. Increased logistic costs originate from inventory management, transportation, and other services.
Components of logistics that can be optimized
All logistics components can be optimized, but they must rely on the business forecast as defined in the company’s strategic objectives. Hence, the company creates a competitive advantage. Specifically, all logistics elements associated with the distribution operations for optimization may include:
- order management;
- it focuses on all aspects that relate to order processes, from order entry to order invoicing and performance management;
- warehousing operations which enhance warehousing activities, such as receiving, storage, picking, packing, and labor scheduling, among others;
- outbound transportation improves all processes that involve carrier selection to freight payment;
- inventory management.
This involves forecast analysis, demand planning, replenishment planning, and system parameter measures.
UPS uses these functions in business processes and available tools to control actions and ensure that they improve customer service during parcel delivery. It focuses on accuracy, consistency, and speed as customers track their parcels on a real-time basis.
Risks faced by logistics managers and their mitigation
There are internal risks, which the Logistics manager may influence and control. They include poor quality of the finished products, disruptions in asset productivity, missing key data features in products, and difficulties in tracking all stages in the supply chain due to lack of visibility, particularly during shipment. The best supply chain management must focus on managing internal risks by adopting and leveraging best practices. Organizations use technologies to reduce such risks.
Logistics managers also face risks from external sources, which they cannot control easily. Hence, the approach is rather reactive and not proactive. Some of these external risks include macroeconomic factors that relate to general trends in economic activities of a country; increasing and highly regulated environments; natural disasters like weather and other threats such as acts of terrorism and piracy; and market uncertainties, which affect customer demands.
Disruptions experienced by companies
Initially, UPS faced challenges related to wrong parcel delivery, delays, poor packaging, and inability to track shipment status, among others. Consequently, the company turned on risk mitigation efforts. It relied on key performance indicators to detect any form of disruption and solve such problems.
The company also adopted smart technologies with real-time reporting capabilities to track cargo throughout the system, detect potential late deliveries or wrong deliveries, and make immediate adjustments. It continued to evaluate business performance with the aim of optimizing operations. In addition, UPS encouraged its employees to manage risks at individual levels.
Reverse logistics, spare parts logistics, and returns management
Reverse logistics involves developing, controlling, and enhancing the successful movement of materials from the source to the end-users to determine value in logistics. It is a critical element in logistics, which firms may use to control costs.
Spare parts logistics focuses on the management of exchangeable parts in an inventory and for purposes of substituting or repairing defective parts. Spare parts may be under a service contract, or the customer may buy them for replacement. Spare parts logistics must account for costs related to inventory management and steady availability of units.
Returns management involves re-entering returned products into inventory ledgers. This is a risky situation for the firm because of inventory carrying costs and storage space. Hence, it contributes to the total costs of returns in logistics management.
Multi-echelon inventory optimization
Multi-echelon inventory optimization focuses on inventory drivers entirely within all areas of the supply chain as it accounts for the effects of inventories in any specific echelon in the logistics activities.
This figure shows a true multi-echelon approach in managing inventory. The major goal of this approach is to minimize all inventories at every echelon (RDC – regional distribution center and DC -distribution center) while accounting for supplies to end customers and costs as components of optimization. It optimizes forecast updates, lead times, bullwhip effect, visibility, and service differentiation, among others.
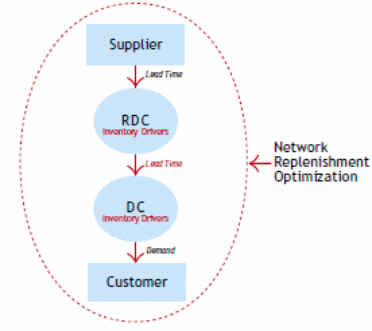
Future of logistics: a multidimensional view
Global Inventory Control
This will involve a global focus on inventory management by reducing inventory through multi-echelon optimization and eliminating delays, and reducing inventory through visibility with the aim of saving costs. Major players will include Black & Decker with its Optiant solution and Liz Claiborne with TradeBeam.
International Logistics Outsourcing
This shall enhance cutting costs and collapsing order cycle times via outsourcing. Key players in this category will be Royal Philips Electronics with its UPS and Redback Networks with its D.W. Morgan. There would be significant savings in order cycles and logistics.
Transportation Spend Management
Williams-Sonoma and Multinational Manufacturer will offer low costs with their GT Nexus and CombineNet solutions, respectively. Future logistics should demonstrate a high degree of competitiveness, flexibility, cycle times, cost reduction, overall impacts across different business units, promote change management, and collaboration with customers and service providers.
The Concept of Same-Day Delivery
Same-day delivery is already here as Amazon.com, Inc., Google, Inc., eBay Inc., and Uber has launched these services to traditional upset couriers and other modes of deliveries. However, while these are attempts to facilitate product delivery to end-users, not all may succeed.
The same-day delivery concept is quite new, and players might take a considerable period to understand its perfect model. In fact, all these aggressive companies are still testing their models. They will need significant investments in technologies and equipment to realize the same-delivery approach.