Abstract
This study presents the relationship between the implementation of quality management systems and innovation in Dubai Customs. The study embodies a rich literature review on innovation, change, and quality management systems. The research uses personal interviews and self-administered questionnaires to collect data for a sample of five interviews at Dubai Customs. Data analysis was carried out with the use of structural and reduction processes of constructs. The findings of the research support the hypothesis that a positive relationship exists between the implementation of QMS and innovation performance.
Introduction
Innovation management is increasingly gaining significance among modern organisations as the changing environment continues to present new challenges. In the wake of globalisation, escalating rivalry, and changing consumer behaviours, it has become critical for both private and public organisations to reinvent themselves as a survival strategy in today’s competitive business environment. Technological stagnation among companies is likely to reduce their competitiveness. As such, the implementation of quality management systems has been evolving to help firms in enhancing innovation initiatives.
The modern global economy has become more complex as technological changes further revolutionise contemporary service provision frameworks. The twenty-first century presents a plethora of challenges to customs, especially border and trade environments. Innovation is a key driver for successful customs administration. It ensures the realisation of the above objectives with ease in addition to improving its marketing positioning in a dynamic business environment. The paper explores the influence of implantation of Quality Management Systems (QMS) on innovation initiatives in Dubai Customs.
Research Background
The past two decades have witnessed growing numbers of studies focusing on the area of innovation in the private sector. Numerous scholars have examined the impact of quality management on organisational performance and innovation initiatives (Xiaorong, Bojian & Huili 2013). Mainly, Quality Management Systems (QMS) has gained popularity among organisational managers and quality practitioners as a change management approach (Kuei, Madu & Lin 2011).
The model plays a vital role in the development of management practices and flexibility besides being integral in enhancing the competitiveness of organisations. Service organisations in the public sector stand a huge chance of attaining excellence, creating the first-time attitude, acquiring efficient business solutions and realising competitive advantage if the total quality management system is successfully implemented (Kuei, Madu & Lin 2011). The purpose of this study is to show the impact of the implementation of quality management systems in Dubai Customs as the service industry strives to leverage its innovation initiatives.
Research Questions
The following primary research questions guide the present study.
- Does successful implementation of quality management systems have significant impacts on the organisation’s quality performance?
- Is there a correlation between quality management systems implementation with innovation performance?
- What set of performance indicators are utilised in Dubai Customs as measures of quality management system outcomes?
Theory and Hypothesis
Several outcomes can be hypothesised regarding the research questions
- H1. Quality systems can assist in developing innovative initiatives that lead to a sustainable innovation process at Dubai customs.
- H2. There is a positive correlation between QMS implementation and organisational innovation performance.
Literature Review
Management Quality Systems and TQM
The following changes stemming from globalisation of markets as well as the need for standardisation and uniformity of products, systems, and services have escalated. Given that, the standards for systems management have been continually employed amid several revisions (Kuei, Madu & Lin 2011). These standards and uniformity ensure that as the wave of innovation sweeps across many organisations around the world, adequate attention is paid the to systems to avoid plunging consumers into adverse consequences of low quality or incompatible outcomes (Zhang, Song & Song 2014).
This phenomenon has led to the creation and establishment of numerous standards including quality management system, environmental protection, healthcare, information security, customs, and many others (Alas, Kaarelson & Rees 2014). In the contemporary business environment, the implementation of QMS has become a distinguishable assurance of trust in certified business (Xiaorong, Bojian & Huili 2013).
Standard ISO 9004 has been proactive in directing companies to sustainable prosperity which is grounded on endeavours for consistent improvements, learning and innovations (Kostiantyn & Hanna 2014). The standard presupposes that organisations respecting the eight principles of quality management system are in a good position to secure continued success. Innovation is not an option for firms that wish to make progress in market terms (Ingason 2015).
According to the International Standards Organisation (ISO), the quality system is a simplified pack of standards that apply to both small and large organisations to provide firms with capabilities of producing according to requirements of customers. Specifically, the ISO 9001 quality management system intends to provide an orderly and systematic way of offering quality commodities to consumers (Alič 2014).
It is worth noting that the implementation of QMS and its subsequent certification is a choice which supports an organisation’s strategy, inspirations, policies, and goals (Xiaorong, Bojian & Huili 2013). Additionally, firms can retrieve more benefits from ISO 900 series quality management systems by taking into account that the design and implementation of QMS are highly contingent on the strategy, size, structure, and the environment changes and the challenges it poses.
As such, there are numerous ways in which organisations can implement quality management systems. In the Customs industry, which falls among service industries, implementation of the QMS brings a significant difference in the quality of the way is perceived and measured (Lal & Bharadwaj 2015). It is critical to note what happens in organisations following the implementation of QMS considering the connection between the implementation of QMS and desired outcome (Zhang, Song & Song 2014). However, many studies fail to show what happens after application.
The Rationale for Implementing Quality Management Systems
There are varied reasons that lead organisations to implement quality management systems. First, QMS can be conceived as a means for improving internal processes and product, systems, or service quality. Second, an organisation might be intending to increase market share abroad, where ISO certification is required (Zhang, Song & Song 2014). In this regard, QMS becomes critical; therefore, companies restructure the production systems to match international standards (Gardena 2013). Third, organisations can act out of pressure from external stakeholders including partners, suppliers or customers who might request to enhance their quality assurance systems to the firms’ internal quality control (Starzyńska & Hamrol 2013).
Additionally, companies that perceive certification as an opportunity for improving internal processes and systems are in a better position to obtain quality results from ISO 9000 quality management systems (Zhang, Song & Song 2014). The most profound impact of ISO 9000 quality management systems includes clear, more apparent working guidelines and responsibilities. However, the most obvious problem of the ISO 9000 quality management system is the bureaucracy which usually hampers flexibility in organisations (Xiaorong, Bojian & Huili 2013).
As an extrinsic factor, ISO 9001 certification has been useful as a marketing tool. In fact, for most countries securing contracts is impossible without the certification (Iyer, Saranga, & Seshadri 2013). Establishing as well as sustaining commercial relationships in the modern globalised economy means that ISO 9000 certification is not optional but mandatory. The knowledge-driven global economy features customers who understand their needs more than ever before (Zhang, Song & Song 2014).
Technological advancement is continually influencing consumption behaviours. That being the case, the modern-day consumer is exerting pressure on companies to produce goods and offer services that match the anticipated quality. In this situation, firms that fail to better their quality management systems are not likely to meet these customers’ needs. Moreover, the level of rivalry has escalated in the business arena.
In this sense, organisations are looking for ways of leveraging the competitiveness (Xiaorong, Bojian & Huili 2013). One way of confronting the ever-intensifying business rivalry is by ensuring quality through viable, innovative initiatives. ISO 9000 quality management systems play a central role in facilitating the attainment of these strategic goals (Munechika et al. 2014).
There exists a strong relationship between companies’ certification inspirations and the outcomes (Zhang, Song & Song 2014). While internal motivations lead to the realisation of positive results, external motivations of certification often cause limited performance results. For instance, a customs company adopting quality management systems approaches as a response to customers’ pressures usually leads the company achieving less positive results compared with a company that was internally motivated to implement QMS. External factors can make ISO 9000 quality management systems adoption a prime goal in itself rather than the company focusing on the results of implementation (Xiaorong, Bojian & Huili 2013).
A Model for Implementing QMS
Due to the increasing wave of globalisation, consumers’ pressure on firms to acquire ISO 9000 certification has escalated in the past two decades. This changing scenario has forced many organisations to seek ISO 9000 certifications, a prerequisite during the process of selecting suppliers (Wright, Sturdy, & Wylie 2012). Additionally, the entry into some countries is not possible unless organisations have acquired the quality management systems ISO 9000 (Zhang, Song & Song 2014).
The assumption and implementation of quality management systems as occurred even among companies that do not necessarily need them. The adoption of ISO 9000 certification is now a strategy to occupy a competitive position in the ever-changing environment (Zhang, Song & Song 2014). This section presents a model that has been conceptualised and considered appropriate. According to Cheng and Tummala (1998), the process of adoption and implementation QMS involves three critical phases, as shown in figure 1.0.
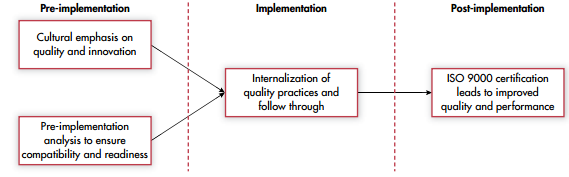
The three phases include establishment, implementation, and maintenance. Other scholars use different phrases while referring to the stages such as pre-implementation, implementation and post-implementation (Zhang, Song & Song 2014).
The pre-implementation phase is the initial stage that embodies the layout of the foundation to embed a quality-oriented organisational culture besides mobilisation and preparation staff to adopt a QMS (Xiaorong, Bojian & Huili 2013). This level entails internalisation of quality practices across the entire organisation. This stage sees firms acquire the ISO 9000 standards requirements, a step that marks the beginning of the post-implementation phase in which quality and performance or firms should seek how to enhance over time following continuous improvements of the quality management system (Reddi & Moon 2013).
The subject of quality management systems has evoked numerous studies due to the ever-growing demand by organisations around the globe seeking ISO 9000 certification. However, too little attention has been paid to the post-certification stage. Numerous studies applied conceptual models rather than empirical testing (Xiaorong, Bojian & Huili 2013).
Change Management in Customs
The operating environment for customs is highly complex; hence, it is demanding besides its constantly changing nature (Alas, Kaarelson & Rees 2014). The perpetual quest for ways to conform to the ever-changing regional and international obligations places the organisations at the epicentre of the need to change management. Customs handle people and complex movement of goods from diverse sources (Venugopal & Priya 2015). In this respect, the need for the management of property dealing with the firms’ jurisdiction is a complex issue, especially in the ever-changing trading environment.
Change management in customs requires the adoption of efficient tools. Multiple theories, methods, and principles have been advanced to guide organisations in driving public firms toward managing change (Reddi & Moon 2013). Some of the theoretical arguments concerning the change in organisations include risk management, innovation management, business re-engineering, and succession management (Zhang, Song & Song 2014). The clearest attention to organisational change arises from theory and methods of change management (Blackburn 2014).
Change management theory is grounded on the vast experience obtained from change processes in both public and the private sectors (Alas, Kaarelson & Rees 2014). It focuses on the needs of the people in an organisation and systems that are affected by the change process. The methods are simple for easy understanding by the target people to ensure that desired changes are achievable and sustainable (Buchhorn & Shannon 2014). Sometimes, change may involve the alteration of the environment. In such a case, the managers ought to be prepared to examine change themselves even where they find it easy to inform others what the change requires (Blackburn 2014).
Customs are environments of constant change. In this sense, managers must be aware of the multifaceted changes affecting customs (Din, Abd-Hamid, & Bryde 2011). These may range from technological, human resources, regulatory, protection of information systems, and organisational structure, among others. Quality management systems and innovation are interrelated, and they complement each other.
Innovation
A growing body of literature reveals that different views exist about the connection between quality management systems and innovation. Some groups conceive a positive correlation while others hold contrary views showing a negative correlation (Tigani 2012). Advocates of QMS claim that companies that successfully implement this approach alongside the integration of organisational culture create a favourable climate for innovation (David & Quang 2014).
The supporters posit that quality management systems involve principles and guidelines that are congruent with innovation (Alas, Kaarelson & Rees 2014). One of the principles requires organisations adopting QMS to invest in customer analysis and needs evaluation (Kirsch et al. 2010). It implies that companies ought to understand customer’s needs and design products aimed at satisfying them.
It is evident that it elicits the question of innovation as the firms strive to meet identified customers’ demands (Alas, Kaarelson & Rees 2014). The dynamic nature of market needs requirements of organisations to engage in continuous and adaptive innovative culture (Johansson, Witell & Elg 2013). It improves the business’s competitive advantage besides enhancing the internal capabilities of the organisation.
Another principle of QMS is continuous enhancement. It encourages change and creative thinking to define the way activities of the firms are organised and executed. The innovative notion of this QMS principle is evident (Huang, Bian & Cai 2013). Other principles of QMS include empowerment, inclusion, and teamwork, which are essential components that underpin organisational innovation. In this sense, quality management systems have a positive relationship with change (Alas, Kaarelson & Rees 2014).
The second group of scholars disagree with the above views regarding the relationship between quality management systems and organisational innovation. Their chief contrasting argument is that QMS and innovation are incompatible since the principles are likely to hamper innovative thinking and initiatives (Alas, Kaarelson & Rees 2014). For instance, a customer’s focus philosophy is likely to lead firms to focus only on the incremental enhancements in their current product portfolio rather than creating new innovative commodities (Chee, Kathawala & Sawalha 2015).
While organisations’ central focus centres on product enhancement rather than developing new ones, they are likely to lack the motivation to innovate. In this regard, the customer’s focus could compromise the views of managers concerning the market. Seeing it from the customers’ perspective can hinder exploration of latent consumer needs. The inevitable consequence is the failure to encourage generative learning through the research on potential market gaps (Alas, Kaarelson & Rees 2014).
Also, scholars hold opposing views on the principle of continuous improvement. They perceive it as comprising too many regulatory standards and activities, which require a routine to acquire full understanding and implementation. Hence, the principle is likely to plunge organisations into wastage of time.
According to Guijarro et al. (2012), opponents of QMS, control, and stability assert that the core of continuous process improvement from the innovative perspective, standardisation is considered necessary for conformity and reducing erratic production in organisations (Nicula & Popşa 2014).
The opponents of QMS see it as a possible trap of people into the notion of remaining content with what is workable rather than designing new products. This idea is likely to cause organisational rigidity, a huge hindrance to innovation. The principle of continuous improvement encourages the simplification or streamlining of processes to take place faster and better. This approach has been interpreted to mean enhancement rather than innovation (Alas, Kaarelson & Rees 2014). It is, therefore, detrimental to organisational innovation. Organisations are likely to continue working with old systems and production ways that are already flawed (Pimentel & Major, 2014).
The contest on the relationship between quality management and innovation performance in organisations elicits two significant questions. The first issue is whether firms can achieve success without innovation (Alas, Kaarelson & Rees 2014). Second, on what companies should prioritise: quality performance or innovation. Some authors assert that it can be challenging to deliver quality performance and innovation simultaneously (Delić et al. 2014).
Frequent and speedy innovation may not allow time for firms to learn process improvements. It can be argued that as long as enterprises strive to undertake change, the implementation of quality management systems will ensure that the standards of products are close (Guijarro et al. 2012). A company that implements the QMS and shows high innovative capabilities is likely to attract brand loyalty and, thus, enhancing its competitiveness regarding the market share and the trust of customers (Nicula & Popşa 2014). However, in some circumstances, a company may choose quality over innovation as long as the latter adversely impacts the former (Santos, Mendes & Barbosa 2011). The vice versa can also prevail where market conditions require high innovation capabilities for survival.
Methods
Research Design
The research adopted personal interviews and a self-administered survey to collect information from the research participants from Dubai Customs. The personal interviews comprised a set of six questions that were administered to five individuals. The interviews contained open-ended questions that were meant to expand the scope of the research findings. One of the advantages of an open-ended interview is the ability to collect projected and non-projected information from the research participants. The questions focused on the managerial responsibilities in enhancing innovation initiatives for the organisation.
The self-administered survey comprised a majority of close-ended questions and a few open-ended questions. However, the open-ended questions were meant to elaborate some of the responses from the close-ended questions. The questions are focused on the roles and professional responsibilities of participants. Additionally, they evaluated the levels of relationships between the employees, the management, and the customers. The surveys will assess some of the challenges faced by the employees working for the Dubai Customs.
Sample and Data Sources
Data collection targeted managerial positions, employees, and customers. Personal interviews and self-administered questionnaire methods were utilised to gather data. Dubai customs is a large organisation in the public sector that has different departments. The firm has a quality management department, which was at the focal point of our research. The study adopted purposeful sampling methods. One of the reasons for using this sampling technique is that section of respondents is done for convenience.
Only the relevant participants are selected. Also, the selection of participants followed the snowballing sampling technique. The chief advantage of snowballing is that the already selected participants offer referrals to other suitable prospective respondents to take part in the survey or interviews. The overall data collection activity sought to engage a total of five purposely selected participants who were better placed to provide credible responses to the questions.
The respondents comprised a quality control department manager, procurements officer representative, an administrative representative, one supplier and a loyal customer. The supplier and customer selected were selected through snowballing in which referrals helped to get in touch with the most trusted external entities of the organisation. The self-administered questionnaires were given to the respondents and face-to-face interviews conducted in a period of two months. Dubai Customs is a very busy company, and most of the times, the respondents were not available for the research exercise. However, informed consent was sent requesting for an appropriate time for the process.
Procedure
The design of survey instruments may require the application of constructs, which are integral in management research. They are latent variables whose direct measurement is not possible. Inquiries concerning behavioural aspect often lack an effective device that can produce a single merit. As such, researchers use two or more measures to weigh a concept. This study adopts an instrument that has been used and pre-tested in past empirical studies.
This way, the study ensures high validity and reliability. There are two parts of the tool adopted in the present study. The first one includes six constructs of TQM practices. The second part features the constructs of outcomes, which are the conceptual indicators of the relationship between implementation of TQM and organisational performance concerning quality, product, innovation, and process innovation.
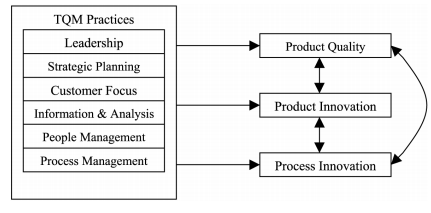
A five-point Likert scale was adopted for the present study. It represents a range of attitudes ranging from 1 (strongly agree) to 5 (strongly disagree). Based on the process of data reduction and coding, the interviews entailed tape recording and transcribing to allow for further analysis.
Measure
Total Quality Management Measures
The total quality management practices used in the current study comprised six criteria that were mostly used in past empirical studies. They include leadership, strategy and planning, customer focus, information and analysis, people management, and process management. Besides the measures which are common with past research, this study added information and analysis criteria in which there are three components. Regarding information and analysis elements, three items were added. These include the organisation’s strategy in assessing performance, the availability of data and information about performance, and the application of information in decision-making processes carried out by the top management of Dubai Customs.
Quality Performance Measures
The current study aims at measuring quality performance besides assessing the impact of QMS implementation of innovation performances of Dubai Customs. The construct of measuring quality performance helped in meeting the research objective of the current study. It showed good validity and reliability. The quality performance comprises four indicators namely: performance, resilience, dependability, and conformance.
Innovation Performance Measures
This study endeavoured to capture detailed aspects of innovation performance in Dubai customs. As such, it built the construct to measure the product and process innovation based on several criteria that were conceptualised and employed in numerous past empirical studies of innovation. They include the number, speed, and level of novelty. These elements sought to unravel the aspects of the novelty for Dubai Customs about its services, products, and processes. This study included the last two concepts to measure aspects of radical innovation in Dubai Customs. The scales utilised to measure the above mentioned elements of innovation are summed up in the table 1.0.
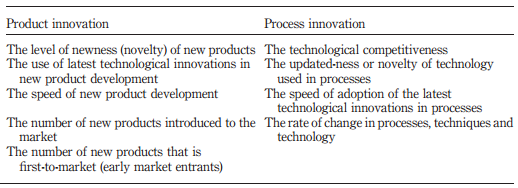
Data Analysis and Results
Two steps were carried out to analyse the data. These included data reduction process and structural analysis. The data reduction process aimed at plummeting variables and parameters of the research model to a favourable ratio in conformance with the structural equation modelling (SEM). The relationship among the three performance variables including product quality, product innovation, and process innovation with total quality management was examined with the use of structural relationship analysis. There are nine constructs each of which consists of four to six items. For the purpose of the current study, the data reduction process was applied to reduce the number of these constructs to six, which are more manageable.
The study used six constructs including leadership, strategic planning, customer focus, people management, process management, information and analysis. These constructs constituted the total quality management latent variables. The three constructs including product quality, product innovation, and process innovation comprised the three organisational performance measures. The nine constructs were tested for validity and reliability before obtaining a single score to represent each of them.
The Confirmatory Factor Analysis (CFA) was used alongside the LISREL 8.30 to investigate the validity of each scale by assessing the appropriateness of measuring the individual items. The goodness fit indices (GFI) of all the constructs surpassed the 0.9 criterion. Thus, the nine constructs passed the validity test. The reliability analysis involved calculation of the Cronbach’s alpha for each scale. All the constructs surpassed the threshold point of 0.7. The results of the validity and reliability tests of all the constructs are exhibited in Table 1.1.
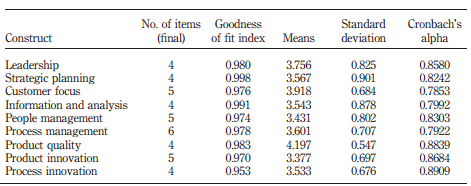
The structural relationship analysis involved SEM using LISREL 8.30 that helped to examine the connection between a set of quality management practices and the three indicators of organisational performance such as product innovation, process innovation, and product quality. Figure 1.2 shows the LISREL model of the relationship between total quality management practices and firm performance.
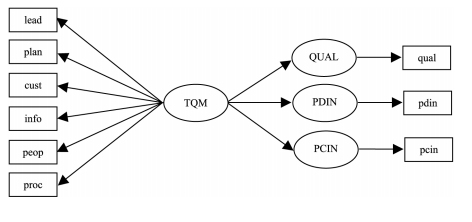
The design features TQM as a single latent construct composed of six variables, whose regressions were done against three latent constructs of organisation performance, where each variable was measured by one latent variable. Estimation of the path coefficient, the single latent variable TQM and the five individual variables (lx2, lx3,1, lx4,1, lx5,1, and lx6,1) and the corresponding error differences were conducted. However, the variance error for TQM and leadership variable (lx1, 1) remained fixed to 1.
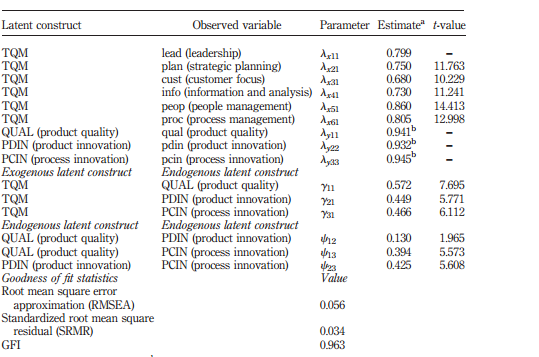
Limitations
The research combined verbal and pictorial presentations, as well as numerical codes, to prepare questionnaires, hence, necessitating the use of mixed research methods. In the case study, the research investigated the employees’ innovation culture using statistical analysis techniques, as well as human analyses from observations. The combination of these two strategies required the adoption of qualitative and quantitative research methods. The limitation was due to time and finding proper literature and the confidentiality of some data.
Discussion
The results of the SEM demonstrate that the total quality management systems and practices have a positive relationship with quality performance and innovation performance. Hence, the findings show support for the position that a positive relationship exists between TQM and innovation performance. Also, the findings provide support for most of the arguments presented in the literature review section obtained from past empirical studies.
Nevertheless, the SEM outcome demonstrates that the explanatory strength of TQM of total quality exceeds the one toward quality management as well as innovation performance. The findings show that quality management systems and practices still centre on quality control despite the argument that there is a shift towards organisational performance.
Dubai Customs pays considerable attention to quality and innovation. As such, the research has shown that the organisation can gain additional benefits by emphasising the utilisation of certain techniques such as SPC to eliminate variation, which is not applicable in innovation. Therefore, even though the results indicate a positive correlation of TQM with innovation performance, it is evident that total quality management is not enough in itself in the maximisation of organisational innovation performance. From the innovation perspective, total quality management is deemed as a form of innovation by its right.
The implementation of quality management systems is associated with the realisation of both desired and undesired innovation outcomes. TQM and innovation performance demonstrates confirmation of the research question two that shows a causal connection between quality management and innovation performance.
Total quality management, according to the results, has the strongest connection with product quality followed by process innovation and product innovation. The relationship between product quality and process innovation is stronger than product innovation. Additionally, a real coherence is manifested by the relationship between total quality management, product quality and process innovation. Radical innovation that employs the first-mover strategy to enter the market is viable in propelling Dubai Customs towards organisational performance.
Theoretical Implications
The result of the research is of high interest to managers who aim to develop their organisations and the literature for future studies. The study contributes to the theory by affirming that implementation of quality management systems positively correlates with innovation. Also, the post-implementation of QMS shows improved organisation performance.
Managerial Implications
This study provides crucial insights to managers responsible for spearheading change management and innovation in organisations. The implementation of QMS is not an option if firms intend to attain and sustain competitive edge through in the contemporary business environment.
Conclusion
This study has examined a rich body of literature on the relationship between quality management systems and innovation performance at Dubai Customs. Numerous studies mentioned in the paper have provided a lot of information on the relationship between quality management systems. Total quality management practices have been applied in the study of such relationships. Dubai Customs, which is a very complex organisation, was chosen for the present research as it offers an opportunity to measure the relationship between QMS, TQM and product, innovation, and overall organisational performance. The findings provide support for the arguments suggested in the literature view that a positive relationship exists between the implementation of QMS and innovation performance in Dubai Customs.
References
Alas, R, Kaarelson, T & Rees, C 2014, ‘The Impact of Social, Political and Economic Changes on People Management in Estonian Organisations’, Journal of Management & Change, vol. 33 no. 2, pp. 77-88.
Alič, M 2014, ‘Impact of ISO 9001 certification cancellation on business performance: a case study in Slovenian organisations’, Total Quality Management & Business Excellence, vol. 25 no. 8, pp. 790-811.
Blackburn, G 2014, ‘Elements of Successful Change: The Service Tasmania Experience to Public Sector Reform’, Australian Journal of Public Administration, vol. 73 no. 1, pp. 103-114.
Buchhorn, H & Shannon, E 2014, ‘From Service Provider to Service Manager: exploring the transition experience’, Asia Pacific Journal of Health Management, vol. 9 no. 3, pp. 24-30.
Chee, O, Kathawala, Y & Sawalha, N 2015, ‘A Model for ISO 9000 Quality Management System Maintenance’, Quality Management Journal, vol. 22 no. 2, pp. 11-32.
David, W & Quang, H 2014, ‘The Relationships among Quality Management System, Knowledge Management and Organisational Performance: An Application of the Heckman Two-step Method’, Journal of Applied Economics & Business Research, vol. 4 no. 4, pp. 235-245.
Delić, M, Radlovački, V, Kamberović, B, Vulanović, S & Hadžistević, M 2014, ‘Exploring the impact of quality management and application of information technologies on organisational performance – the case of Serbia and the wider region’, Total Quality Management & Business Excellence, vol. 25 no. 8, pp. 776-789.
Din, S, Abd-Hamid, Z & Bryde, D 2011, ‘ISO 9000 certification and construction project performance: The Malaysian experience’, International Journal of Project Management, vol. 29 no. 1, pp. 1044-1056.
Gardena, C 2013, ‘Based Tru-Form Plastics Inc. was awarded ISO 9001:2008 Certification for its Quality Management System (QMS)’, Medical Product Outsourcing, vol. 1 no. 6, pp. 149.
Guijarro, F, López-Rodríguez, F, Moral, F, Mena, Á & Álvarez, P 2012, ‘Using an objective method for managing the implementation of quality certification in the industry’, Computers & Industrial Engineering, vol. 62 no. 1, pp. 591-598.
Huang, J, Bian, Y & Cai, W 2013, Effectiveness evaluation research of quality management system. Web.
Ingason, H 2015, ‘Best Project Management Practices in the Implementation of an ISO 9001 Quality Management System’, Procedia – Social and Behavioural Sciences, vol. 194 no.1, pp. 192-200.
Iyer, A, Saranga, H & Seshadri, S 2013, ‘Effect of Quality Management Systems and Total Quality Management on Productivity Before and After: Empirical Evidence from the Indian Auto Component Industry’, Production & Operations Management, vol. 22 no. 2, pp. 283-301.
Johansson, E, Witell, L & Elg, M 2013, ‘Changing quality initiative – does the quality profile really change?’, Total Quality Management & Business Excellence, vol. 24 no. 1, pp. 79-90.
Kirsch, M, Vogg, I, Hosten, N & Fleßa, S 2010, ‘Quality management in a radiological practice. Experiences with a certification for DIN EN ISO 9001:2000’, European Journal of Radiology, vol. 75, no. 1, pp. 1-8.
Kostiantyn, M & Hanna, M 2014, ‘Conceptual aspects of formation of the system of integrated management of quality of tourist services’, Problems of Economy, vol. 1 no. 1, pp. 259-264.
Kuei, C, Madu, C & Lin, C 2011, ‘Developing global supply chain quality management systems’, International Journal of Production Research, vol. 49 no. 15, pp. 4457-4481.
Lal, P & Bharadwaj, S 2015, ‘Assessing The Performance Of Cloud-Based Customer Relationship Management Systems’, Skyline Business Journal, vol. 11 no. 1, pp. 89-100.
Munechika, M, Sano, M, Jin, H & Kajihara, C 2014, ‘Quality management system for health care and its effectiveness’, Total Quality Management & Business Excellence, vol. 25, no. 7, pp. 889-896.
Nicula, V & Popşa, R 2014, ‘Implementation of a Quality Management System in a Travel Agency’, Studies in Business & Economics, vol. 9 no. 1, pp. 109-124.
Pimentel, L & Major, M 2014, ‘Quality management and a balanced scorecard as supporting frameworks for a new management model and organisational change’, Total Quality Management & Business Excellence, vol. 25 no. 7, pp. 763-775.
Reddi, K & Moon, Y 2013, ‘Modelling engineering change management in a new product development supply chain’, International Journal of Production Research, vol. 51 no. 17, pp. 5271-5291.
Richards, K 2013, ‘The Importance of Change Management in Managing IT Projects in the Public Service of Trinidad and Tobago’, West Indian Journal of Engineering, vol. 36 no. 1, pp. 35-46.
Santos, G, Mendes, F & Barbosa, J 2011, ‘Certification and integration of management systems: the experience of Portuguese small and medium enterprises’, Journal of Cleaner Production, vol. 19 no. 1, pp. 1965-1974.
Starzyńska, B & Hamrol, A 2013, ‘Excellence toolbox: Decision support system for quality tools and techniques selection and application’, Total Quality Management & Business Excellence, vol. 24 no. 5, pp. 577-595.
Tigani, OE 2012, ‘For a Brighter ISO 9001:2008 Certification’, Journal for Quality & Participation, vol. 35 no. 3, pp. 1.
Venugopal, P & Priya, A 2015, ‘The Impact of Customer Service On Customer Relationship Management’, Global Management Review, vol. 10 no. 1, pp. 139-152.
Wright, C, Sturdy, A & Wylie, N 2012, ‘Management innovation through standardisation: Consultants as standardisers of organisational practice’, Research Policy, vol. 41 no. 1, pp. 652-662.
Xiaorong, N, Bojian, X & Huili, Z 2013, ‘The application of total quality management in rural tourism in the context of new rural construction – the case in China’, Total Quality Management & Business Excellence, vol. 24 no. 10, pp. 1188-1201.
Zhang, Z, Song, T & Song, J 2014, ‘Analysis of Relationship between Quality Management System and Design Assurance System’, Procedia Engineering, vol. 80 no. 3, pp. 565-572.