Introduction
The success of any organization depends on the quality of the services and products it offers to its customers. It is difficult to achieve this goal if the management of an organization does not have proper management systems in place to ensure that the quality of products and services is maintained. Total quality management is one of the most fundamental systems needed in an organization to sustain the continuous improvement strategies.
Any customer focused organization uses this management system that involves all the stakeholders. The continuous quality improvement strategies can only be effectively implemented if the total quality management system is in place. The total quality management system integrates quality principles in the organizational culture using the building blocks of the continuous quality improvement system (Pekar 45). This paper will discuss the various strategies for implementing the total quality management system in Europe Car Company. Europe Car Company is a leading market player in providing car rental services in Europe and the entire world.
Vision and Objectives
The mission of a total quality management system in Europe Car Company is to continually improve its products and services for customer satisfaction. This is meant to improve the company profits and promote the company brand throughout the whole world. The management should create a favorable environment for continuous quality improvement strategies to be implemented (Pekar 67). The management should motivate the employees and make sure they are satisfied because they are very important stakeholders in the continuous improvement process. Change obstacles should be constantly dealt with in all the phases of a continuous quality improvement process. The guiding principles of a total quality management system should be incorporated in the company culture and norms for easy implementation of total quality management strategies (Pekar 67).
People should express the meaning of quality in their daily lives for them to qualify as credible candidates for leading quality improvement initiatives in an organization (James 23). In total quality management, it is very important to inspect a production process the same way the product is inspected before being delivered to the customer. This principle is important because when the production processes are of the required standard, then the final product will definitely be of high quality.
The probability of variation in the quality of a product should be known in a total quality management system. The management should use scientific methods in determining accurate information in the level of quality variation in products and services (James 24). The company managers should continually work towards improving the company systems while the employees use the developed system to improve the quality of goods and services.
Total quality management strategies should be consistent with the general organizational guidelines to ensure that all the stakeholders in the organization are well informed of the changes being made (Samuel 12). The total quality management process should begin from the current state of the company until the mission is finally accomplished. The total quality management system is continuous and all the expected results can not be achieved in a single day (Samuel 12).
The company safety and hygiene are very important in the total quality management system. Employees need to work in a clean and safe environment for them to perform to their best. It is the responsibility of the management to provide safety facilities for their employees. All the members of an organization should be aware of the fact that the quality of the company products and services is their responsibility (Samuel 14). All stakeholders should embrace the principle of doing the right thing all times. Quality is a long continuous journey and complacency of any sense should be avoided regardless of some accomplished goals.
Customer satisfaction is the best tool of measuring the quality of products and services. Quality is only achieved when the customers are satisfied. When employees are involved in the total quality management process, it inspires them to come up with new ideas and innovations that can be vital to the organization (Pekar 40). Analytical tools should be used to determine the areas and departments that need improvement.
It is very difficult to sustain the total quality management system if the company managers do not of offer enabling and consistent leadership. The product or service managers should always be thinking of how to improve products and services all the time to sustain the continuous quality improvement system (Pekar 40). The objectives of total quality management can only be achieved if the guiding principles are observed to the latter.
All the continuous improvement strategies put in place by the Europe Car Company are aimed at making the company remain a market leader in quality and efficient car rental services. Any total quality management system should have a common purpose that is constant at all levels of the organization (Winchell 21). The total quality management system is supposed to ensure that all the company stakeholders adopt a common philosophy of continuous quality improvement. The other fundamental objective of a total quality management system is to stop the dependence on inspection alone as a way of determining and achieving quality (Winchell 21). Total Quality management aims at coming up with new methods of quality improvement.
Total quality management system is meant to end the common practice of relying on price alone while awarding business. One of the major objectives of a total quality management system is to provide other alternative criteria to base on while awarding business. Constant process improvement should be one of the main preoccupations of a total quality improvement team (Samuel 44).
A successful total quality management system should ensure that all the employees and stakeholders receive modern training on how to continually improve the quality of products and services. Total quality management can not be effective if old methods of supervision are still being used. The organization should at the of the day institute new supervision methods that are relevant to the current systems (Samuel 44). This can only be achieved by putting in place a very aggressive total quality management system.
Total quality management system should give the employees the freedom to express themselves. This encourages the employees to point out areas that need improvement and motivates then to actively participate in the continuous quality improvement process (Pekar 70). The other objective of a total quality management system is to eliminate all the barriers in departments. This helps a great deal in promoting teamwork and everyone feels more responsible for quality improvement. Total quality management should at the end of the day make the employees and other stakeholders to take pride in their work.
Employees who are proud of their work will no doubt offer quality services to the organization. Numeral goals being a major prescription of company work standards are not good for an organization practicing continuous quality improvement (Pekar 71). One of the goals of a total quality management system is to do away with such work standards. Total quality management should cut down the cost of operations by dealing with one supplier. The system should remove any fear that might exist among employees and encourage them to work towards transforming the organization (Pekar 71). Since total quality management is a customer focused process, customer satisfaction is the major objective of total quality management.
Europe Car Company expects to attain superiority in its performance by emphasizing quality and timely delivery of car rental services to its customers. Dependability and flexibility are some of the basic qualities that an organization should possess through the total quality management system (James 48). The other objective of total quality management is to enable the organization incorporate the culture of continuous improvement in all operations. TQM should encourage transparency in the organizational leadership. This will in turn help the Europe Car Company to excel in its area of specialization (James 48).
Apart from the broad objectives, Europe Car Company has specific total quality management objectives for all the departments. When all the departments work towards attaining quality, then the whole organization will generally produce quality services and products (Winchell 52). The procurement department plays a vital role in determining the final quality of products and services. The quality of fleet cars and other parts determines the quality of the final service to the customer. If quality principles are not applied at this stage, then the whole system is bound to fail (Winchell 53).
Total quality management should ensure that the company procures quality and standard fleet cars and other parts. The procurement department At Europe Car Company aims at achieving timely delivery of fleet cars from suppliers which facilitates quick service delivery to customers (Samuel 79). Quality involves timely delivery of vehicles to clients and this should be facilitated by the procurement department. The other objective of total quality management is to reduce the cost of operations and the procurement department should help in meeting that objective by negotiating for fair prices when purchasing fleet cars (Samuel 89).
The quality assurance department is the core department of the company and most quality strategies are facilitated by this department. The objective of this department is to produce quality automobiles that are safe and comfortable to use by customers. Due to recent concern about environmental conservation, Europe Car Company is forced to incorporate environmental strategies in its operations. The quality assurance department works in coordination with the procurement to ensure the fleet cars purchased emit less carbon dioxide to the atmosphere.
One of the strategies put in place to meet this objective is the purchase of electric vehicles. The major total quality management objective in the quality assurance department is to order for fleet cars that are safe to use and environmentally conscious (Pekar 112). The other objective of the quality assurance department at Europe Car Company is creating a new line of eco-citizen vehicles under the environmental conservation initiative. The sales and marketing department has the objective of transforming the Europe Car Company into a customer focused company that makes customer satisfaction its primary priority (Pekar 112).
On of the major objectives of a total quality management system is to satisfy customers and at the same time make profits. The sales and marketing department has the responsibility of meeting the objective (Samuel 54). The other objectives of the sales and marketing department at Europe Car Company are to facilitate market penetration, improve product development, diversification of services and market development. The Information Technology department aims at ensuring that the information flow in the in the company is quick and efficient.
Information is very fundamental in achieving quality and the IT department should ensure that all the systems are continually improved in line with modern requirements. The IT department at Europe Car Company is supposed to facilitate all online operations like bookings, marketing and inquiries. The other key department in implementing quality principles is the human resource department. The department has the objective of hiring a qualified and experienced workforce who will render quality services to the organization (Samuel 56). The department has to meet the objective of continuous training of employees in order to sustain the continuous quality improvement system.
The other department hat has a huge responsibility of initiating total quality management initiatives at Europe Car Company is the customer service department. The department is supposed to continuously improve response time and road-side assistance for customers (Pekar 115). The department should come up with other methods of determining quality other than inspection. The finance department should demonstrate accountability and transparency because they are key attributes in total quality management. The main objective of the finance department at Europe Car Company is to company debts by ensuring that there is sufficient cash holding in the company. All the departments play a vital role in the continuous quality improvement system making it necessary for all barriers between departments to be completely eliminated (Pekar 115).
TQM Tools
Total quality management tools are very important in assessing the performance of an organization both qualitatively and quantitatively. Total Quality Management tools are almost similar to all organizations regardless of the area of specialization. The universal TQM Tools are used at Europe Car Company in the implementation of continuous improvement initiatives. The TQM tools identify and analyze quality concerns of an organization as a basis for quality improvement strategies (James 66). The tools are used to enhance efficiency and quality in company procedures and processes. All the quality concerns addressed by the total quality management tools should be relevant to the organization.
Some information is difficult to assimilate and the TQM tools help in illustrate the quality level of all the company processes. Total quality management tools help in analyzing the market and establishing the exact customer needs (James 66). Competition, logistics and financial analysis is normally made easier when the total quality management tools are used. The total quality management tools are also very important in determining internal and external forces that affect the organization. Statistical analysis is widely applied in total quality management tools which are essential for accurate fault finding in all company operations.
One of the commonly used total quality management tools is the Pareto chart. The chart prioritizes all the issues affecting the organization in a very organized way making it easy for the management to fix the problems in the organization. According to this principle, all qualitative data is grouped and rated depending on the number of complains received (Samuel 97). This makes it easy for the management to determine the areas that require some urgent action. The chart is very easy to analyze and can be created before or after the total quality management strategies have been implemented.
The Pareto chart is a combination of two graphs that represent common causes of defects in a descending manner. The bar graph represents individual values whereas the line graph represents the cumulative total (Samuel 97). The chart has two vertical axes with the left one represent the frequency of defects occurrence. The percentage of cumulative totals is always represented on the right vertical axis. The processes or systems with the highest frequency of defects or complains are normally given the first priority when implementing quality measures (Pekar 120). The Pareto principle states that 80% of the effects are as a result 20% causes. An organization should strive to do away with 20% causes in order to solve 80% of its quality problems.
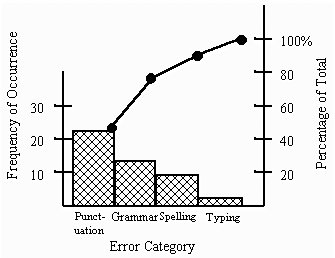
The chart illustrates different categories of errors in an academic paper. The categories are arranged in a descending order from the one with the highest frequency of occurrence to the least. From the chart, it can be seen that punctuation errors are the majority and need immediate attention followed by grammar, spelling, and typing errors in that order (Pekar 120). The line graph shows the total cumulative values of each individual error category. The left vertical axis shows the frequency of error occurrence in all the error categories. The right vertical axis represents the cumulative percentage of individual error categories (Pekar 121).
The overall quality of the academic paper depends on the error categories shown. This student should work towards improving the quality of his papers by improving on his punctuation, grammar, spelling and typing. From the chart it is easy to determine which problems need to be given the first priority according to their frequency of occurrence (Pekar 121). Priority should be given to improving punctuation and then followed by grammar and the rest. Fig 1 is a perfect example of how total quality management tools can be used to analyze quality issues in an organization.
Benchmarking
Benchmarking is a total quality management process that involves the evaluation of existing processes and systems in an organization in relation to other major players in the same industry. Europe Car Company faces competition from other company companies providing car rental services and benchmarking is essential for it to remain relevant in the market (Samuel 56). The organization can focus on the best practices available in the industry and can decide to adopt them as a continuous quality improvement strategy. Total quality management can effectively be implemented using benchmarking as an implementation tool. Since the main objective of total quality management is to continuously improve company processes, benchmarking is important in setting standards for improvement (Samuel 57).
An organization should first of all understand all the principles of a total quality management system before benchmarking its processes with other successful companies. Effective benchmarking requires the availability of some accurate data about the about for easy comparison with other companies. Process and financial results of the company should be available to facilitate the benchmarking process. Benchmarking can be done against the leaders in the industry or a company can decide to do it against its own practices and processes (James 75). Benchmarking goals should be very realistic in order to maintain the morale in the company.
For benchmarking to be useful in solving problems, it must be done against major processes. The benchmarking process should continually compare organizational processes and strategies with other industry leaders (James 75). After comparison, the organization should strive to match the performance of even perform better. Benchmarking can be done in there levels depending on the strategies of an organization. To begin with, benchmarking can be done internally where the company benchmarks against its own processes and strategies. Similar functions in different departments within an organization are compared to enhance quality in all departments. The second level is benchmarking against other companies within the same industry.
These companies may be top competitors or industry leaders (James 78). The third and final level of benchmarking is external benchmarking where an organization does benchmarking against companies that produce different products and services. The Europe Car Company can benchmark its customer care practices against those of a hotel. For effective and comprehensive benchmarking, it is advisable for an organization to practice all the three levels of benchmarking (Pekar 80).
The benchmarking process comes with many benefits to the organization. To begin with, benchmarking is always a wake up call for an organization that is always conservative (Pekar 80). It enables the members of an organization to appreciate the fact that there are other better performing companies and a change from the traditional ways of doing things is mandatory for the company to improve its performance. Through benchmarking, an organization is always in a better position to set realistic goals that can easily be achieved. Benchmarking improves the performance of an organization by identifying gaps in performance and strategizes on how to improve on them.
Quality improvement strategies improve both group and individual performances in an organization (James 69). The human resource can not be in a better position to establish the basis of training employees if the company does not benchmark. Benchmarking enables the human resource department to effectively prepare relevant training programs for its personnel. This helps in closing performance gaps and the employees are put in a better position to solve problems and implement the continuous quality improvement strategies. An organization can only enjoy these benefits if the benchmarking process is done according to the required principles (James 69).
The benchmarking efforts can turn out to be futile if the findings are not put into practice by the organization in question. An organization should practically use the knowledge gained from the benchmarking process to effectively improve its processes and systems and narrow any gap that might exist between it and other players in the industry. There are almost six steps that should be strictly followed for successful benchmarking. These implementation techniques are universally recognized in benchmarking (Pekar 128). To begin with, an organization should categorically decide on the processes and systems to benchmark. By identifying the processes, it is easy to collect the required data for benchmarking.
The company should also have a proper record of its current performance for easy comparison with other companies. Information about the current performance of an organization should be from accurately collected data in all the affected area. This data enables the company to actually understand its current position and decide whether improvements are needed or not (Pekar 128). Planning is very essential in any process and benchmarking is no exemption. A company should have a clear plan on how and when to carry out the benchmarking process. By failing to plan, the company will be planning to fail in its benchmarking endeavors.
The system to be benchmarked should be thoroughly studied in relation to that of the target company. Accurate data should then be collected from the system or process as a basis for benchmarking. The organization should then use the collected data to learn valuable lessons that can help in improving the performance of the organization. The final step is for the company to fully implement the findings and incorporate them in its continuous quality improvement system (James, 121). Performance improvement can only be achieved if the benchmarking findings are properly integrated in the total quality management system and all the stakeholders are willing to embrace the changes brought about by the new total quality management initiatives (James 121).
TQM Implementation
The implementation of total quality management initiatives at Europe Car Company follows the conventional implementation procedure. There are some misconceptions about total quality management that can hinder the implementation process and the management should avoid them as much as possible (Winchell 54). An organization should start the continuous quality improvement process as soon as possible in order to catch up with competitors. Before starting the process of total quality management implementation, the managers and those leading the continuous quality improvement process should first of all obtain a total commitment from the company Chief Executive Officer and the top leadership if the company.
The second step is to educate the top company leadership about their role in the total quality management process (Samuel 126). The company CEO and the top management should show their commitment in the continuous quality improvement process by allocating the required resources of time of money to the continuous quality improvement initiatives. The top leadership should actively participate in the development of the total quality management vision, principles and objectives. The top management should be at the fore front in showing the expected conduct in the TQM implementation phase (Samuel 126).
The top management should demonstrate leadership by facilitating all company training on quality improvement issues. The other role of the top management is to instill confidence in employees by eliminating all uncalled for fear from the organization. The CEO and senior management recognize and award those who make significant efforts in meeting the total quality management objectives. The top management is expected to make important decisions for the organization especially those regarding quality.
The company leadership should create an environment that is suitable for the total quality management system (Pekar 146). This is made possible by creating an organizational culture that facilitates the smooth implementation of total quality management in the organization. The organizational culture should have some basic underlying elements for it to be termed as being favorable for continuous quality improvement. To begin with, all the information about quality should specifically be used to improve the quality of products and services and not to intimidate and judge other people (Pekar 146).
Other elements of the total quality management culture include taking responsibility for quality, rewards and recognition, cooperation, job security, fairness equality and a sense of ownership. Total quality management implementation needs leadership and this necessitates the creation of a steering committee to oversee the whole process. The steering committee should comprehensively do a survey on customers in coordination with the research and development department to have the actual facts on the ground. The other role of the steering committee is to identify all the processes and departments that need improvement based on data and customer recommendations.
It is the responsibility of the steering committee to appoint the quality improvement teams and recommend them for training (Samuel 189). The committee should constantly monitor all the processes recommended for improvement and ensure the improvement strategies are being executed according to plan. The steering committee has the responsibility of informing the rest of the organization about the progress being made and noting the major achievements in the implementation process. The committee recommends employees for recognition according to their efforts in the continuous improvement process Samuel 189).
The next step in the implementation process is the establishment of total quality management principles. The guiding principles together with the total quality management vision and mission statements should effectively be communicated to all stakeholders for effective implementation of conterminous quality improvement initiatives. The basic guiding principles include customer satisfaction, safety, empowerment of employees, continuous improvement and the principle of doing the right thing at all times (Pekar 168). The next step is to prepare a flow diagram representing all the company processes as a guide to implementing quality processes in the organization. Customer focus is the next fundamental step in implementing total quality management.
This is done through doing a vigorous customer survey to establish customer attitudes, recommendations, beliefs, concerns, complain and preferences. This information is very important in determining the areas that need improvement for maximum satisfaction of the customer. The company should collect as much information as possible about how the customers feels about their products and services, methods of communication, administration, planning, technical competences, responsiveness and speed of delivery (Pekar 168). This information is very important for the continuous quality improvement system. Customers define quality and their recommendations are very important to the general success of the organization.
The next stem in the total quality management implementation process is to consider all the stakeholders as internal customers and owners of the organization. This makes it easy for the management to effectively implement the quality strategies because it receives first hand information from insiders on the areas that need improvement. The next step is initiating training programs to equip he employees with the required skills for implementing the new quality initiatives.
The training should begin from the top management down to subcontractors (James 180). All stakeholders should be continually trained on how to implement the total quality management initiatives. The top management should be trained on the basic quality concepts like quality definitions, customer satisfaction, TQM benefits, quality costs, employee empowerment and total quality management implementation steps.
The company supervisors play a very crucial role in implementing processes and systems in the company and them too require a comprehensive training. The supervisors need to receive training on the general quality improvement processes and total quality management guiding principles (James 186). The non supervisory employees also need some training in the aspects of total quality management systems and team work. The training process is continuous and elaborate. To begin with, a consultant in total quality management is selected to take charge of the training process.
The consultant trains the management first before a trainer from the company is sent for training. After being trained, the facilitator trains supervisors and later other employees (Samuel 190). The company can hire new employees at this stage and forms a training committee to oversee the entire training process. The facilitator then trains all the employees in team building. What follows is the evaluation and improvement of the training programs.
The next step in the implementation process is the establishment of quality improvement teams. The number and size of the teams depends on the size of the organization. The quality team has the responsibility of identifying and investigating areas that need improvement. Members of a quality improvement team should be committed to change and training and should also have good communication and organizational skills (Samuel 190).
The members are usually drawn from different departments. Quality improvement teams have the responsibility of designing a process flowchart and identifying inputs and outputs of each process. The team reviews current procedures by data collection and recommends solutions to areas that have problems. The quality improvement team reports to the steering committee on all the changes made to the company processes.
The quality improvement team helps in incorporating the total quality management culture in the organizational culture. The quality improvement team should also report to the top management of the organization and update them on the progress of the quality improvement initiatives. A quality improvement team should meet at least once per week on a regular basis. Each member in the quality improvement team has a special role to play as assigned by the team.
The members spend most of their time in training and facilitating the total quality management tasks. The main objective of this team is to ensure the satisfaction of both employees and customers. Employees are satisfied through empowerment and recognition while customers derive their satisfaction from quality products and service produced by quality systems and processes (Winchell 134). The quality improvement team plans all the training programs with the help of facilitators.
The next step after training is the actual implementation of the process improvements. There are several factors that need to be considered while implementing process improvements. The management should demonstrate their full support for the initiatives by being interested in the implementation process. The improvement strategies should mainly focus on improving and satisfying customers. After identifying all the processes that need improvement, all the employees should be actively involved in the implementation process. Corporation is highly needed and everyone should be viewed as a customer (Winchell 134).
The implementation teams should consist of members from different levels and departments for the process to look inclusive. The criteria and systems used to identify processes should be improved. All the employees and stakeholders should be comprehensively trained in all issues about quality in the organization. The communication outside is greatly enhanced to constantly keep in touch with the customers.
Process improvement is normally carried out using the structure approach. To begin with, the steering committee is informed of the existing problem. The steering committee goes ahead to form another team to analyze the process in question and come up with recommendations on how to improve the process. After reviewing its mission, the team begins training (Winchell 123). The team is supposed to meet regularly to come up with the necessary solution to the problem. The solution is first implemented on a testing basis before the results of the preliminary solution are critically analyzed by the steering committee. After the solution is approved by the steering committee, it is then fully implemented in the entire company.
The second last step in implementing the total quality management system is the use of the TQM tools to fully analyze and understand the situation of all company processes in terms of quality. Some of the total quality management tools used include Pareto charts, cause and effect diagrams, control charts, histograms, check sheets and run charts. The final step in total quality management implementation is reviewing the benefits of total quality management to the organization. It is very important for a company to implement the total quality management system because failure to do so will make it lose a lot of money (James 160).
The cost of quality is very high and will continue to escalate if the necessary improvements are not made to the company processes. Company systems and processes that lack continuous improvement will lead to errors, accidents, omissions, poor quality products and lateness in delivery. This costs the organization in terms of money and time because of the many consequences that come with the failure to improve the quality of processes. Poor quality products will lead to loss of customers and can also lead to penalties and liquidated damages (James 150).
Just like any other processes, the total quality management initiative also faces some resistance. Total quality management brings some large scale changes to the organization and the change agents need to address the situation as fast as possible. Total quality management advocates for employee empowerment and this is bound to cause some resistance from the top management because they see employee empowerment as an initiative of reducing their power to make decisions for the organization.
Empowering employees does not make the managers lose their fundamental authority in the organization. Resistance is also bound to occur if the total quality management initiatives are only implemented on a pilot basis (Samuel 145). Total quality management advocates for the use of data in analyzing processes and the quality of service. This can be a problem to the traditional worker who is not used to this method of evaluation.
Conclusion
Total quality management is one of the fundamental management systems for improving company processes and operations. The main objective of total quality management is to promote customer satisfaction and minimize quality cost as much as possible. Total quality management guiding principles are very vital in implementing and sustaining a continuous quality improvement system. All stakeholders of the organization should be trained on quality issues and in the process be empowered to actively participate in implementing quality strategies. Proper training and awareness about the general aspects and benefits of total quality management to the organization helps a great deal in eliminating all misconception and resistance to the total quality management initiatives.
Works Cited
James, Paul T. Total Quality Management: An Introductory Text. New York: Prentice, 1996. Print.
Pekar, Jack P. Total Quality Management: Guiding Principles for Application. New York: ASTM International, 1995. Print.
Samuel, Anand A. Total Quality Management. New York: PHI Learning Pvt. Ltd., 2004. Print.
Winchell, William. Continuous Quality Improvement: A Manufacturing Professional’s Guide. New York: Society of Manufacturing Engineers, 1991. Print.