Abstract
Khalifa Industrial Zone (Kizad) is an industrial park that was developed by the government of Abu Dhabi with the primary goal of attracting investors as a way of diversifying the economy. The question was to determine how management of this industrial park can embrace effective management strategies that foreign investors can find attractive. In this paper, the aim was to analyze and discuss various quality management tools that can be used to improve service delivery and overall performance of the park. The primary method used in the paper to gather information was through review of secondary sources. The result has identified Lean Six Sigma tools to be effective in the context of this firm. It is evident that if the management embraces the suggested recommendations, the performance of the industrial park will improve significantly.
Introduction
Khalifa Industrial Zone, popularly known as Kizad, is an industrial park and port at Taweelah, just adjacent to the Khalifa Port. According to Ramos (2016), Kizad is set to become Abu Dhabi’s first industrial free zone that offers 100 percent foreign ownership. The initiative is meant to help in the diversification of the emirate’s economy beyond oil and gas. It was constructed in line with Abu Dhabi’s Vision 2030, which focuses on diversifying the economy of the country (Oxford Business Group, 2014). The aim of this study is to use various quality management tools that can help Kizad to achieve its strategic goals. The study is worthwhile because it will help the management of this organization to cut its expenses while at the same time increase its productivity.
Literature Review
It is important to review reports and theoretical concepts that have been developed by other scholars, which are relevant to this field of study. Quality management has become one of the most important factors that public institutions have to take into consideration to ensure that there is value for every investment that the government makes. Various tools have emerged that can be used to measure and improve the quality of service and productivity at an organization (Anninos, 2007). In this section of the paper, the focus will be on Lean Six Sigma, which has become relevant specifically to the manufacturing sector. The review starts by conducting an in-depth analysis of the Lean Six Sigma techniques and tools relevant to Khalifa Industrial Zone.
In-Depth Study of the Lean Six Sigma Tools and Techniques
The in-depth analysis of this tool makes it possible to understand how this organization can use it to achieve specific challenges and to meet objectives that have been set. Given the fact that Kizad is specifically targeting foreigners, the management must ensure that it has incentives that the targeted clients will find to be attractive. The following are some of the specific tools of the Lean Six Sigma that can be used to enhance service delivery at this entity.
DMAIC model
One of the most important tools that the management of this company will find relevant is the DMAIC model. It identifies five main steps that should be taken to reduce defects in products (Zink, 2007). The first step is to define what seeks to be achieved. The management of state in clear terms what each of its departments should realize within a specific financial period. The second step is to measure, which involves identifying how the set goals should be realized in statistical terms (Tseng & Wu, 2014). The team can develop performance measures to help individual employees at Kizad to understand what is expected of them.
The third step when using this model is to conduct an analysis of the progress made. Of interest is to identify possible weaknesses within the system that may have a significant impact on the outcome of a specific project. Chatterjee (2016) suggests that during this process, the outcome of the analysis should be stated clearly, explaining the source of the problem and possible ways of addressing it. The fourth step is the improvement. Based upon the report of the analysis, the management team at Kizad will be expected to identify initiatives that can help address the identified weaknesses and propose various ways of improving the outcome. The last stage is the control, where the team will measure the overall outcome and propose potential ways of improvement. This model is shown in Appendix 1 below.
The 5s system
Lean Six Sigma also identifies the 5s system that can help improve the performance of the industrial park. Under this model, the first step is to sort the system (Yuen & Thai, 2015). It involves eliminating unnecessary items within the workplace that may disorient the performance of the employees. The management should then set everything in order by ensuring that items are arranged in order to make it easy for employees to find and use them. It means placing everything at the right place based on its usage. The third step is to shine, where stakeholders are expected to keep the work area and items neat and clean (Juran Institute Inc., 2013).
The assumption is that the neatness will be a motivation to the workers. The fourth step is to standardize operations, where the team will be required to have a consistent approach to procedures and tasks (Bicheno & Catherwood, 2005). The strategy is meant to ensure that everyone understand what is expected of them at every stage of production. The last stage is to sustain, where everyone is expected to make a habit of maintaining the approved procedures and practices (Socconini & Reato, 2019). Figure 1 below identifies the 5 stages of the 5s model.
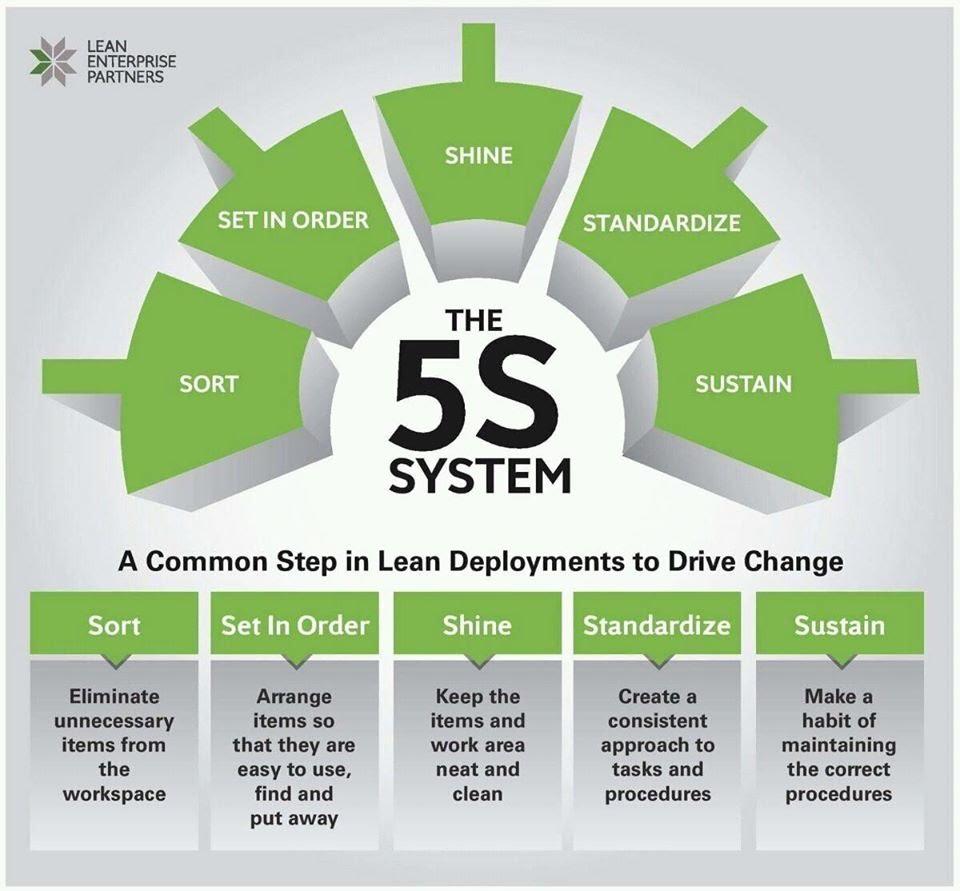
Value stream mapping
Value stream mapping is a popular model that is often used to classify organizational activities. According to Juran and De (2017), these activities should be classified as value-enabling, value-adding, or non-value adding activities. This tool helps in ensuring that organizational processes are more compact, swift, and precise to save resources and time. Once activities are classified into the three stages, the goal is to eliminate the non-value adding activities because they waste time and resources. Focus should be on value-enabling and value-adding activities. Employees should understand how their actions fall under each of the three classes. For instance, they have to understand that spending time on social media during working hours fall under non-value adding activities, which have to be avoided.
Kaizen
Kaizen is another tool under the Lean Six Sigma that focuses primarily on the need to have continuous improvement. According to Chatterjee (2016), it is not possible to realize perfection overnight. As such, the management should consider setting small short-term goals based on the competencies of the employees and the infrastructure available. The team should then remain committed to a consistent quality improvement effort to ensure that once the set goals at each stage is realized, new ones are set. This tool often helps in eliminating wastes in the production process.
Every time an improvement is made, the team will look at the new areas of weaknesses and how they can be addressed. This tool will help the management of Kizad to ensure that various issues that will emerge in the normal running of the entity are addressed effectively and within the right time. Figure 2 below shows the cyclic process of continuous improvement of value within an organization as suggested under this model
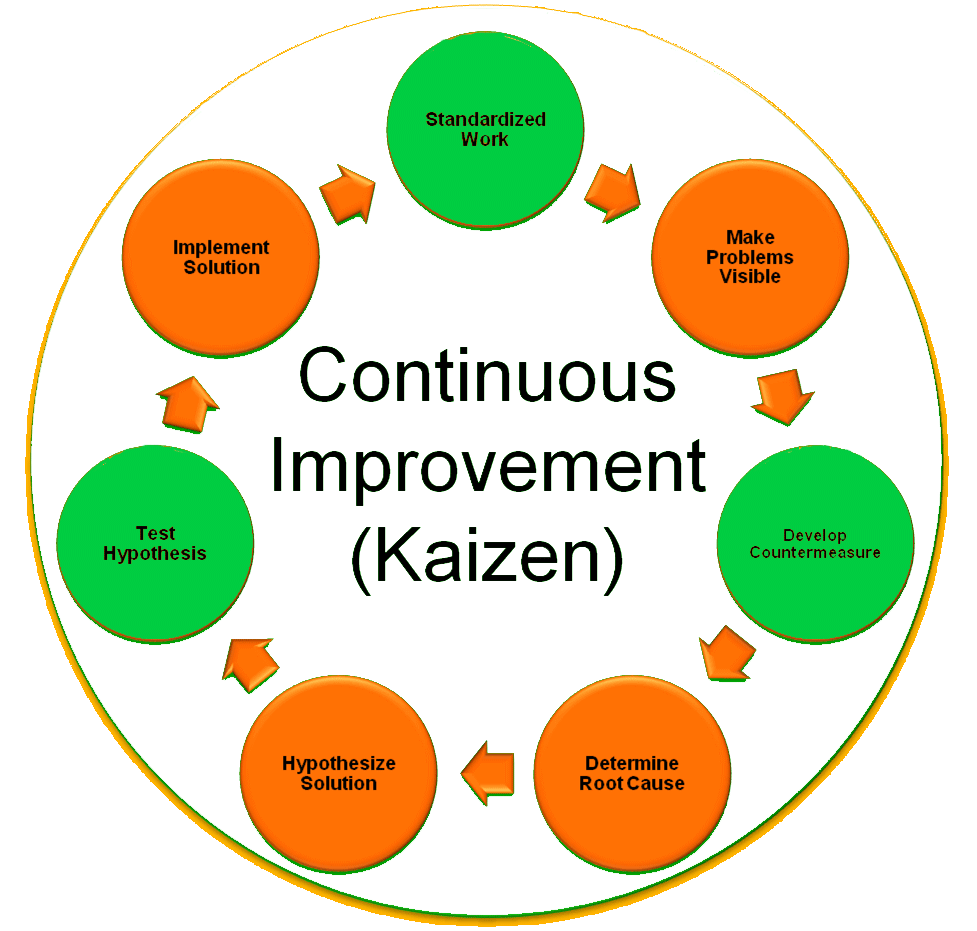
Research Methodology
When conducting research, one of the first steps that have to be taken after defining the objectives and research questions is to determine the appropriate methodology. One should clearly define the method used to collect and analyze data from various sources. In this project, it was desirable to collect data from a sample of employees of Khalifa Industrial Zone, especially those who are in the top managerial positions. However, the limited time available for the project made it impossible to conduct interviews with these individuals. As such, the study relied on secondary data. Information was obtained from books and online publications made by the government relating to this project. Quantitative data analysis was considered appropriate in processing data obtained from various sources. Using excel spreadsheet, it was possible to present findings made using graphs and figures for clarity purposes.
Data Analysis and Results
It is evident that Kizad has the potential of improving the economy of Abu Dhabi if it serves its intended purpose effectively. The government has made massive investment into this project to ensure that it yields the expected returns. The primary expectation of the government is that there will be a consistent increase in the percentage contributions that Kizad will make to the economy of Abu Dhabi. Figure 3 below shows the consistent increase in the contribution of this industrial park to the country’s economy.
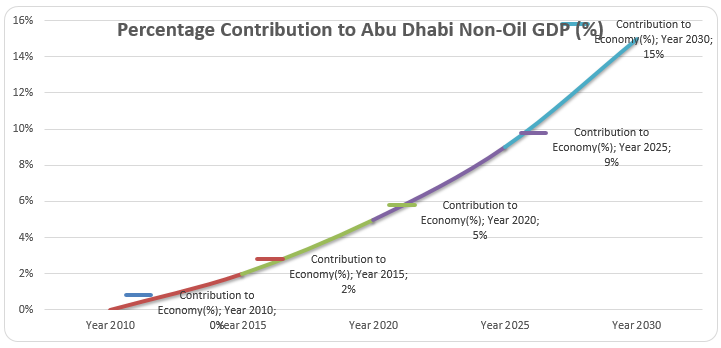
As shown in the figure above, if the right progress is made in this major progress, then there will be a consistent increase in this project, which was unveiled in 2010 and officially opened in 2012. It is expected that by 2030, the Khalifa Industrial Park will contribute 15% of Abu Dhabi’s non-oil gross domestic product. The government has put in place measures to ensure that the majority of goods manufactured in this industrial park are exported to other parts of the world. As such, it will become a major source of foreign currency earner to the country at a time when it is expected that the demand and availability of oil will be going down. Figure 4 below is a comparative analysis of goods meant for domestic consumption vis-à -vis that for export at this facility.
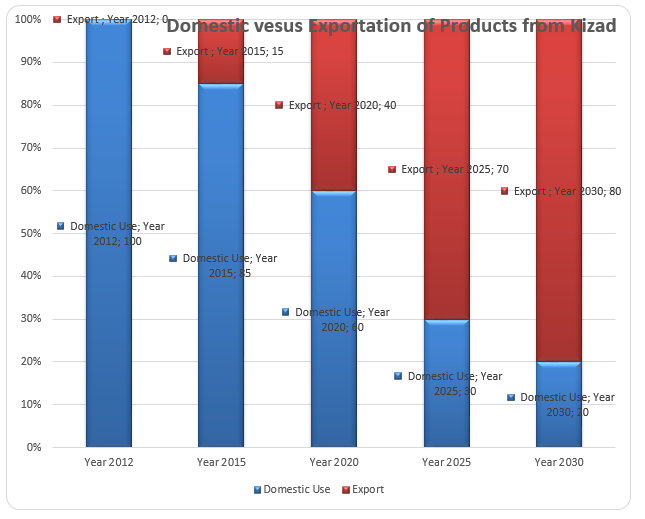
When Kizad officially started its operations in 2012, almost all the products were consumed locally. However, the government, working closely with the local and international private investors, has ensured that a significant portion of these products are sold in the international market. It is expected that by 2030, only 20% of these products will be utilized locally, with the remaining 80% sold in the global market. The hypothesis, shown in the objectives of the project, is confirmed by the statistics, as it shows that the park will become a major contributor to the country’s economy.
Discussion
The research question of this study focused on how Kizad can embrace effective quality management techniques to ensure that the park attracts foreign investors and becomes a major contributor to the country’s economy. The review of the literature has identified Lean Six Sigma as the tool that can help this firm to realize the set goal. The findings shown above indicate that the desired goals can be realized if the firm embraces these strategies and tools.
Evaluating Relevant Tools and Techniques of Quality Improvement
The Lean Six Sigma, discussed in the literature review, primarily focuses on the elimination of wastes within this park while at the same time improving productivity. According to Friis, Holmgren, and Eskildsen (2016), one of the ways of achieving success in the current competitive global market is to ensure that a firm can produce high quality products at low prices. The Lean Six Sigma focuses specifically on achieving this goal. As such, it is highly relevant to the management of Kizad as it seeks to ensure that its products are sold in the international market.
Key Quality Issues Which Can Be Improved Using Lean Six Sigma
As discussed on the literature review, the Lean Six Sigma will be focusing on specific issues, which are of great significance to Kizad. One of the key quality issues is elimination of wastes. As Brown (2013) observes, one of the main factors that often lead to compromised quality is a system that is characterized by massive wastage. Through the models discussed above, this quality issue will be addressed. The model also emphasizes the need to ensure that there is an effective management of time. Every activity should be completed at the right time to ensure that it does not affect subsequent activities.
Recommendations
The Lean Six Sigma theory discussed above shows that Khalifa Industrial Zone has the potential of becoming one of the major business hubs in Abu Dhabi if the right steps are taken to enhance quality of products, eliminate wastes, and lower costs. Based on this information, the management should consider embracing the following recommendations:
- The management of Kizad should ensure that it has a team of highly skilled and experienced workers that can implement these quality management tools.
- The government should invest in technology to make it easy to monitor progress of activities at this facility.
- The management of Kizad should embrace benchmarking as another way of improving performance.
Conclusion
Khalifa industrial zone is an initiative of the government of Abu Dhabi meant to create an industrial park and port meant for foreign investors to help diversify the economy. The government intended to ensure that most of the goods from the park are exported to help in the diversification of the economy. To achieve this ambitious goal, it is necessary for the management of the park to embrace tools and strategies of the Lean Six Sigma. These tools will help lower the cost of operation while at the same time improving productivity.
Appendices
Appendix 1: DMAIC Model
Appendix 2: Khalifa Industrial Zone
References
The chosen style for the study was American Psychological Association (APA). The following are the sources used in the paper:
Anninos, L. (2007). The archetype of excellence in universities and TQM. Journal of Management History, 13(4), 307-321.
Bicheno, J., & Catherwood, P. (2005). Six SIGMA and the quality toolbox: For service and manufacturing. London, UK: Pixie Books.
Brown, A. (2013). Quality: Where have we come from and what can we expect? The TQM Journal, 25(6), 585-596.
Chatterjee, B. (2016). Applying lean six sigma in the pharmaceutical industry (2nd ed.). New York, NY: Routledge.
Friis, O., Holmgren, J. & Eskildsen, J. (2016). A strategy model: Better performance through improved strategy work. Journal of Modeling in Management, 11(3), 742-762.
Juran Institute Inc. (2013). Quality improvement tools: Reference & participant training kit. New York, NY: Independent Publishing Platform.
Juran, J. M., & De, F. J. A. (2017). Juran’s quality handbook: The complete guide to performance excellence (7th ed.). New York, NY: McGraw Hill.
Oxford Business Group. (2014). Report: Abu dhabi 2014. Oxford, UK: Oxford University Press.
Ramos, S. J. (2016). Dubai amplified: The engineering of a port geography. London, UK: Routledge.
Socconini, L., & Reato, C. (2019). Lean six sigma management system for leaders. Barcelona, Spain: Marge Books.
Tseng, S., & Wu, P. (2014). The impact of customer knowledge and customer relationship management on service quality. International Journal of Quality and Service Sciences, 6(1), 77-96.
Yuen, K., & Thai, V. (2015). Service quality and customer satisfaction in liner shipping. International Journal of Quality and Service Sciences, 7(2), 170-183.
Zink, K. (2007). From total quality management to corporate sustainability based on a stakeholder management. Journal of Management History, 13(4), 394-401.