Analysis of Leopard Tools’ Manufacturing and Global Supply Chain Approach
Leopard Tools uses mass production of tools, such that there is no specialization. The products are of various categories, some of which serve nearly the same purpose. The company holds too much stock of multiple components failing to realize the full benefits of economies of scale. On its stock, there are disparate components, and most of them are unique to a single product. It means that the company cannot practice bulk buying of such elements, but it can purchase them in small quantities. The items come from different suppliers; hence, a broad supplier base and complexity in managing them.
Leopard Tools release small batches of products per trip due to the need to change tooling. Producing a few items is associated with the under-utilization of their production capacity, which is expensive due to fixed costs and eliminates the benefits of economies of scale (Calderone, 2017). Moreover, it adopts every item’s in-house production, such that not all processes involved in manufacturing a product, from designing to assembling, are from the factory. Innovation is minimal in Leopard tools both for products and production systems. Nearly all company items have been in the company for many years as no new products have been launched. Production tooling in the organization is old and won indicating that, maintenance and replacement of production tools are ineffective. The company lacks preservation core competencies, such as unique designs, as they rely on manufacturing staff knowledge.
Proposed Strategies
The adoption of a process perspective in the management of operations is significant because operations can be analyzed at an intermediate level. The company undertakes diverse and interlinked tasks. Therefore, a process lens will guide the required integration to ensure that all work practices are explicitly linked to the company’s overall functioning (Zemguliene & Valukonis, 2018). The company should adopt end-to-end processes to reduce customer complaints by fulfilling their needs effectively (Calabrese et al., 2019).
End-to-end processes are defined mainly by the processes they do, for instance, designing processes, invoicing, warehousing, sales, and assembly, among many others specific to a company. It increases convenience as similar groups can share common resources to reduce overall costs (Holocentric, 2018). However, it will demand a radical rethink from the management and relocation of processes and resources to meet customers’ needs effectively.
Another strategy that Leopard tools can adopt is the Value, Rarity, Imitability and Organization (VRIO) framework for managing their operations. The company should focus on its core competencies to gain a competitive advantage now and in the future. Some resources such as high quality, unique distribution systems, and suitable supplier bases can help the company. Management should identify rare, imperfectly mobile valuables, difficult to imitate and hardly substitutable and focus on them rather than engaging in all operations (Slack & Brandon-Jones, 2018). Focusing on core competencies will not only position the company better in the future. Still, it will also reduce the burden from engaging in every process, including non-core operations (Asatiani et al., 2019).
It should also consider outsourcing non-core activities to contractors to focus on core operations and hire specialists in processes that need specific knowledge lacking in the company. Figure 1 is a demonstration of the association of competitive advantage and core competencies in a VRIO framework.
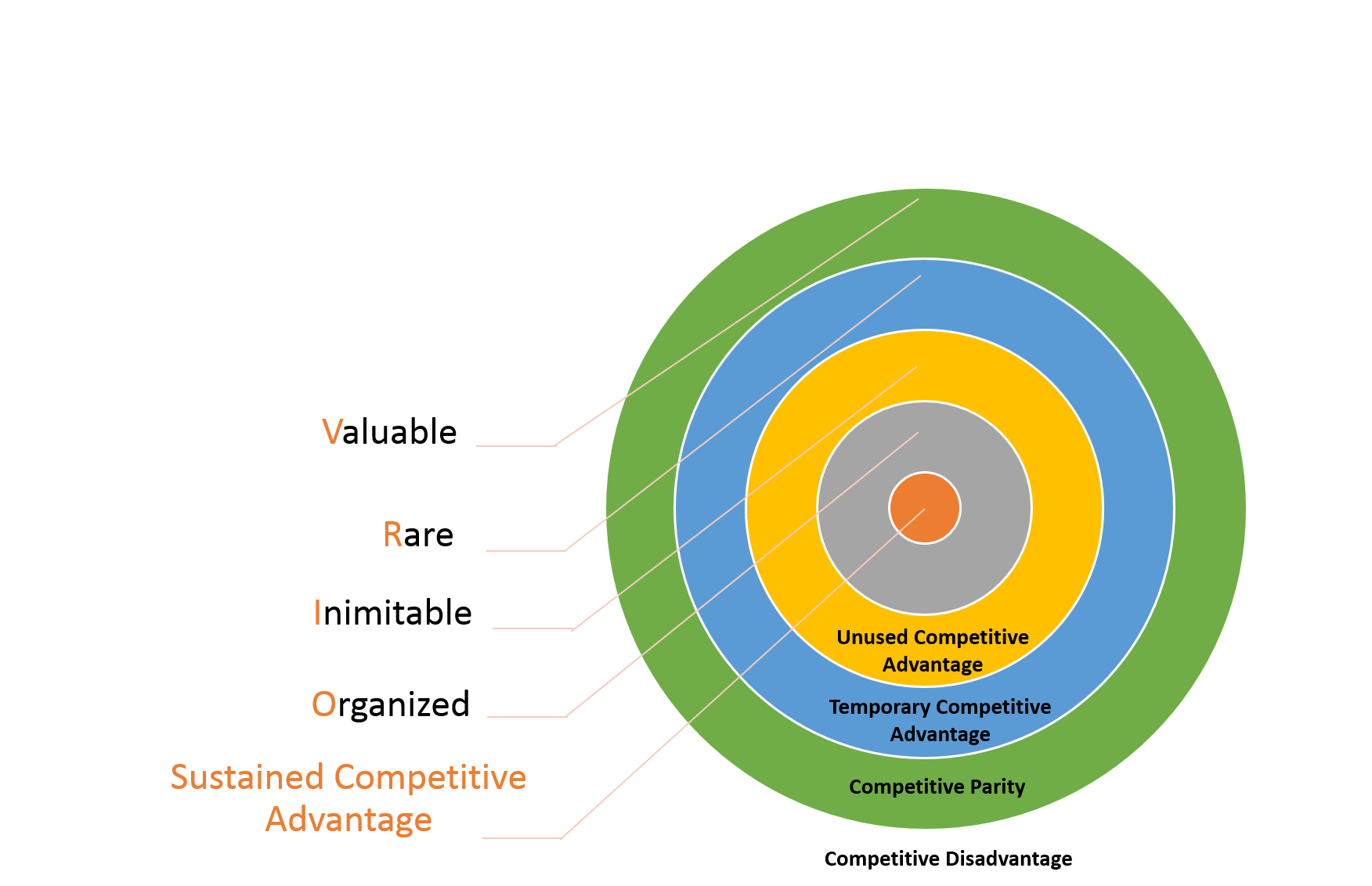
Leopard tools should also change their inventory management system to more cost-effective and convenient means such as Just-in-time, lean production, and others. It will reduce the amount of stock held in the company at a particular time (Holgado de Frutos et al., 2020). They are storing many components, and work-in-progress ties too much capital, which could have been used for development or research. The company should focus on customer preferences rather than internal operations and capabilities during production and designing tools. The market’s nature has changed significantly, and the most successful companies prioritize customers’ satisfaction (Calderone, 2017).
Tastes and preferences change with time, and therefore producing the same items the company has been producing for years could render it uncompetitive (Calderone, 2017). It should invest more in research and development to better understand the market and customers and make necessary forecasts depending on data collected.
The company should update their process technologies to increase operational efficiency. Old production tooling and strategies employed by Leopard tools affect products’ speed and quality, consequently increasing production costs. Although the systems used in the company could still be operational and have not been affected by advancements in technology, updating them would increase efficiency (Calderone, 2017).
Processes in the manufacturing industry are becoming automated, even in the labor-intensive sector, demanding a complete shift in the way companies operate. Product technology has also advanced, changing the functionality and specification of tools. Leopard tools should adjust its products to fit in the current and future market by launching modernized items that are flexible to adapt to the economy’s changes. However, the process is costly, as it requires intensive capital investments and continuous research and development.
A Comparison of the Current Strategy with the Proposed Strategies
Leopard Tools currently adopts mass production of items, which is advantageous in offsetting production costs. However, the strategy reduces the adaptability of products, apart from making it difficult for the company to restructure production. Further, using current inventory and manufacturing control techniques such as lean production and vendor management will help the company produce the right amount and high-quality items (Qi et al., 2017; Amachree et al., 2017). The methods will also increase the flexibility of products to suit the dynamic customers’ tastes and preferences, increasing consumer satisfaction (Calderone, 2017).
Additionally, they eliminate money-holding costs, facilitating resource circulation in the facility. However, the strategy requires restructuring processes and investment in current technologies and software, particularly for communication and inventory management, adding more operating costs.
The company currently produces everything in-house, which ensures maintenance of high quality and protection of the brand. However, the strategy is costly and hinders it from benefiting from new technologies and skills from external sources (Sprock et al., 2019). The proposed outsourcing technique will ensure that some products, components, and services are acquired from third parties. Further, it reduces production costs and enables the company to focus on core operations (Asatiani et al., 2019). However, contractors can overprice their services or expose the company to the risk of imitation. They can produce low-quality items to save on production costs, or increase the company’s overdependence on them, failing to develop its workforce for future sustainability.
Lastly, Leopard Tools controls every process and stage of production, apart from focusing on availing products themselves. It performs all the supply network activities from supplier’s management, production, warehousing, distribution, and marketing. The proposed strategy of focusing on core competencies and operations will reduce workload (Agburu et al., 2017). Its core competencies will push the brand further and make it hard for competitors to imitate their products and processes (Asatiani et al., 2019). This strategy’s challenges include putting too much attention on the competencies and neglecting other critical operations such as new product development and market trends or competition.
References
Agburu, J.I., Anza, N.C. & Iyortsuun, A.S. (2017). Effect of outsourcing strategies on the performance of small and medium scale enterprises (SMEs). Journal of Global Entrepreneurship Research 7, (26). Web.
Amachree, T.T., Apkan, E. O. P, Ubani, E. C, Okorocha, K. A., & Eberendu, A. C (2017). Inventory management strategies for productivity improvement in equipment manufacturing firms. International Journal of Scientific & Technology Research, 21(10), 1-18.
Asatiani, A., Penttinen, E., & Kumar, A. (2019). Uncovering the nature of the relationship between outsourcing motivations and the degree of outsourcing: An empirical study on Finnish small and medium-sized enterprises. Journal of Information Technology, 34(1), 39–58.
Calabrese, F., Gamberi, M., Lelli, G., Manzini, R., Pilati, F., & Regattieri, A. (2019). Optimal operations management of hybrid energy systems through short-term atmospheric and demand forecasts. Procedia Manufacturing, 39, 702-711.
Calderone, L. (2017). The benefits of just in time inventory. Manufacturing Tomorrow. Web.
Holgado de Frutos, E., Trapero, J. R., & Ramos, F. (2020). A literature review on operational decisions applied to collaborative supply chains. PLoS 1, 15(3), e0230152. Web.
Holocentric. (2018). The power of end-to-end process management. Web.
Qi, Y., Huo, B., Wang, Z., & Yeung, H. (2017). The impact of operations and supply chain strategies on integration and performance. Elsevier, 185(C), 162-174. Web.
Slack, N., & Brandon-Jones, A. (2018). Operations and process management principles and practice for strategic impact (5th ed.). Pearson Publishing Company.
Smith, R. (n.d.). Explaining the VRIO framework (with a real-life example). Clear Point Strategy. Web.
Sprock, T., Sharp, M., Bernstein, W. Z., Brundage, M. P., Helu, M., & Hedberg, T. (2019). Integrated operations management for distributed manufacturing. IFAC-PapersOnLine, 52(13), 1820-1824.
Zemguliene, J., & Valukonis, M. (2018). Structured literature review on business process performance analysis and evaluation. Entrepreneurship and Sustainability Issues, 6(1), 226-252. Web.