Project Charter
Background
This project aims at producing a new device used in certain medical products and its effective marketing. The project is expected to help the organization to diversify its product range, enter new markets, and increase profits. Medical products have been in high demand in the USA, and technological (including computer-based) advances are valued in this sphere. However, this is quite a new area for the organization, so the project will require effective management, additional resources, and employees’ commitment.
Goals
- The necessary volume of high-quality devices is produced within the established term
- The organization has the necessary resources to start mass production of the device
- All the necessary licenses are obtained within the defined period
Scope
The production of a new device is the end result of this project. The process will be divided into several phases including planning, prototype design and production, obtaining the necessary legal documents, preparation for the production, and the production of the device. The product marketing process is excluded from this project as this area will be the responsibility of another team. At that, marketing specialists will be involved in the process of the new product planning and development as their insights are instrumental in the successful implementation of the project.
Key People
The project team will include the employees from the departments mentioned above, and these people will collaborate during the planning and implementation stages. The representatives of the departments will focus on the scope of the work of their structural units. For instance, marketing manager will ensure that the product will be effectively promoted and sold, and it has the necessary features to become successful in the market.
Project Milestones
The project will be implemented within 12 months starting from December 1, 2018. The mass production and the associated testing will be implemented during three autumn months in 2019 (see table 1).
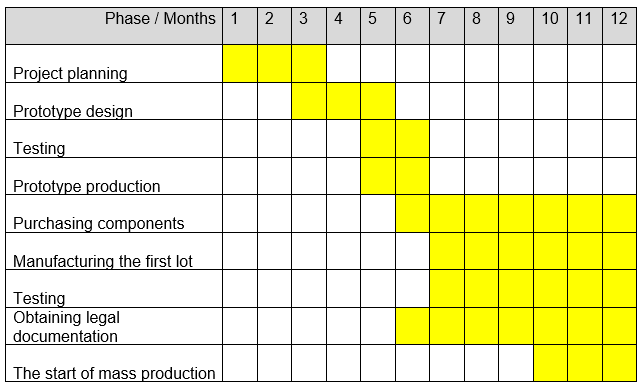
Project Budget
The preliminary estimation of the costs indicates that the overall budget for the project will be $100,000 (including the development of the prototype) (see table 2). The number of the boards produced within the scope of this project will be 20,000 items. The implementation of this project will require the acquisition of new equipment and software, as well as staff training. The involved people will participate in the project and simultaneously continue working on their current tasks. Although no additional staff will be hired and no considerable funds will be allocated to pay additional salaries, certain bonuses and perks should be provided so some investment in human resources should be considered.
Table 2. Preliminary Budget.
Constraints and Assumptions
Various factors are likely to have an impact on the project implementation process. First, the lack of well-established communication channels and communication competency can have adverse effects on the project. This area needs specific attention, and extensive training, as well as the development of the corresponding culture, is necessary. Secondly, the employees (key stakeholders) do not have experience in working on such projects as all new products development projects were managed by hired consultants.
In addition, no devices for medical equipment have been produced, so people lack knowledge and skills in this area. Employees’ motivation to perform properly can be low as they will have to focus on their current tasks instead of investing all their time in the project. The company will also have to allocate certain funds to ensure the successful management of this project, which can be difficult due to the existing economic challenges.
This project relies on a set of assumptions that include the presence of strong leadership, vision, and overall readiness for changes. The company’s top management has a clear vision that is properly communicated. It is also acknowledged that the organization needs certain transformations related to communication competency development. The company has the necessary resources including funds, equipment, and manpower to successfully manage the project. The employees do not reveal their negative attitudes and can be interested in participating in the project. The new product is likely to be marketed effectively, which will ensure meeting the established goals.
Project Risks Spreadsheet
The implementation of any project is associated with a variety of risks that should be considered. It is essential to identify the most serious issues that may happen in order to come up with an effective risk management plan. Although the organization does not have a sound risk management planning culture, a risk management plan will be created for the project in question. This plan will ensure the successful implementation of the project as the project team will be ready to address the challenges that may hinder the success of the new product development.
Approval Signatures
CEO_______________________.
Project Manager_______________________.