Introduction
Business environment is rapidly getting competitive, and firms are forced to find better ways of managing this competition. According to Sarkar (90), the current market competition has gotten so stiff that firms are finding it difficult to manage their operations without the threat of losing their market share. This competition means that firms must go beyond offering common products to the market. They must find a way of delivering unique value to the consumers in order to create a pool of loyal customers who will help in ensuring that they remain sustainable.
Consumers are becoming very demanding given that they have access to knowledge about the products they need. Ease of accessing this knowledge through the media has helped consumers realize that they can get more value from their purchases. Media also provides them with alternatives to choose from in terms of products or brands. For this reason, customers are currently demanding for higher value from their purchases at reduced costs. Firms have to find a way of delivering this high value at lower costs while remaining profitable.
To achieve this, some business units are using Total Quality Management theories in order to ensure that they deliver the best quality to their customers. As Harry (31) notes, delivering quality needs a clear approach taken not only in the production process, but also in other areas such as management. Total Quality Management focuses on the overall structure of a firm, and means of streamlining all its operations to deliver the desired quality. Customers should be provided with quality products that meet their demand. One of the quality tools that have been used in the recent times is Six Sigma Quality.
According to Munro (26), Six Sigma has gained a lot of popularity in the recent past. This scholar says that this tool is the most widely used quality management tools by firms across the globe. The tool does not only help to ensure that there is quality of the final products, but also focuses on other areas of production, including the management process. It seeks to help firms achieve perfection in all their operational activities. In production, it seeks to eliminate any defect from the products by eliminating any form of deviation in the process of producing goods. In management, it seeks to create a clear path that should be taken by the responsible authorities when guiding other members of the organization towards success. As Bufman (58) observes, Six Sigma Quality is about everything related to improving value of the products given to the consumers.
Basic Principles of Six Sigma
Six Sigma Quality has become very popular in the recent past. It is important to understand some of the basic principles that guides this quality tool. The first principle of Six Sigma focuses on the customer. According to this principle, a customer is an important component of business units, and it is always necessary to ensure that he or she gets the best value for the purchase. This principle holds that customers should always be offered high value for their purchases in a consistent manner. As Morfaw (34) notes, at no given time should a firm compromise on the quality of products they offer to the consumers. This is because a satisfied customer will always turn out to be loyal to the firm. This loyalty will help build a pool of customers that enhances a firm’s sustainability in the market.
The second principle focuses on the process of production. According to George (55), understanding the process of production helps in minimizing mistakes by creating a clear mechanism through which they can be identified before they create any major defect. Quality should be managed from the first stage of production to the moment the product is delivered to the customer, in what Mukherjee (72) refers to as the value stream. In this value stream, a firm is mandated with the responsibility of ensuring that it sources for quality raw materials, engages in quality processing of the products, and employs good approaches of delivering the product to the customer.
The third principle focuses on management, improvement, and smoothing the process flow. In the process of achieving quality within a firm, there are processes that should always be given serious focus in order to achieve the desired result. It is important to manage these processes in a diligent manner to avoid any unfortunate scenarios when delivering products to the market. The management should always focus on continuous improvement of product delivery methods. The system should be smoothened to increase efficiency of a firm in the market. Another principle of Six Sigma Quality is elimination of any process that does not add any value to the final product. The production manager should be able to identify some of the steps that are wasteful, or do not add any value to the final product. As Cole (42) notes, another important principle of Six Sigma Quality is on reduction of any form of unplanned variations. This principle holds that in the production process, any form of variation that may lead to production of differing products should be eliminated. This eases the prediction process.
Six Sigma History
The history of Six Sigma has always been traced to Motorola Inc. in the mid-1980s. According to Burton (114), Motorola Company was concerned of how it could improve efficiency in its production process. Competition was getting stiff in the electronic market, and there was need to ensure that its products were of superior value, and that the production process was made as efficient as possible. In 1980s, engineers at Motorola developed the name Six Sigma as a name for the initiative that they had undertaken to reduce defects in their process of production. They used the term ‘sigma’ because it had become a common symbol of quality.
The engineers were trying to set standards through which variations in the production process could be minimized as a way of minimizing defects on the final product. Mikal Harry, and Bill Smith are credited for having developed the term Six Sigma at this firm. These engineers started by measuring defects per thousand products. When the need to improve quality further was eminent, this measure was enhanced to units of defects per million products.
They finally agreed that for a process to be considered as efficient, the number of defects must be less than 3.4 per million units of production. This firm realized that its production improved when this method was used. As Mukherjee (81) notes, the time taken to produce goods dropped, the number of defects per million products reduced, and the costs of production also dropped, especially after introducing Just in Time (JIT) strategy as part of this quality management tool.
In 1991, Motorola developed Black Belt Six Sigma Experts as a way of formalizing the accreditation in training of Six Sigma Methods of quality management (Charantimath 77). This method received a massive following when firms realized that it had worked successfully for Motorola. Some of the firms that would implement this method soon after it was formally introduced include Allied Signal and General Electric. By the year 2000, Six Sigma had become popular not only in the United States, but also in other countries around the world, especially in Europe and Japan. This tool remains very powerful in managing quality of products and production process. In United Arab Emirates, firms have come to appreciate its relevance in improving quality of the production process.
Application of Six Sigma by Starwood Hotel in Dubai
According to Mukherjee (40), the increasing popularity of Six Sigma has made several firms consider its application as a way of improving their efficiency. This quality tool was initially considered as a preserve for large engineering firms. However, it has become relevant to various firms in other industries, including the service industry. In Dubai, a number of firms have adopted this method in enhancing quality of their products. One of the firms that have been using this method to enhance its production is Starwood Hotels and Resorts in its Dubai branches. The hospitality industry is increasingly becoming competitive. New firms are coming into existence with better strategies that is forcing the existing firms to rethink their strategies. Starwood knows of this increasing competition, especially with the increasing expansion of Dubai City as a regional and international business hub.
The firm has been using Six Sigma Method to enhance its production processes within this city. As demonstrated in their website, the firm has been striving to streamline its operations using Six Sigma to ensure that any form of defect on their products is identified early enough, and corrective measures taken as would be appropriate. This has helped Starwood remained very competitive in the local market. This firm is currently one of the leading hospitality firms in this city. It has a large base of loyal customers locally and internationally, a clear demonstration that this tool is making it successful.
Critical Success Factors for Successful Application
Starwood is just one of the firms that have used Six Sigma to achieve success in their industries. Other firms such as General Electric have managed to remain dominant firms in their industries despite the changing environmental factors. Their secret is in the successful application of Six Sigma Methods of managing quality. One of the critical success factors of this tool is that it reduces the amount of defective production during the production process. For firms using this tool, the production process can only be considered as successful if the number of defects per one million units is less than 3.4 units. This is a very high degree of efficiency. The reduction of wastage helps in ensuring that the firm remains cost effective in its operations. As Stamatis (39) says, high rate of producing defective products in in a firm is one of the reasons that reduce profitability. Another key success factor of applying this method successfully is the easy of predicting the outcome of the production process.
This process seeks to eliminate variations in the production process. If this is achieved, the management will find it easy to determine the outcome of a production process. Improved efficiency is another key success factor. This method helps in identifying stages that do not add value to the product with the view of eliminating them. By eliminating these redundant stages, the total time taken to produce goods will be reduced, and the amount of labor or machines used will be reduced. This increases the efficiency of the production process.
Barriers to this Approach
Although Six Sigma has been considered as an effective tool of enhancing quality in the production process, a number of barriers that reduce its applicability in some firms still exist. One of the main barriers to this method is lack of trust between management and employees in some firms. This rigorous process need total corporation between management and employees. If this relationship is poor, then achieving the desired success may be completely impossible. Another barrier that has been identified when using this tool is poor communication. This method requires close communication between all the stakeholders. When this is limited, it may not be possible to understand what is expected of a given process.
As indicated earlier, Six Sigma entails having a clear vision of what a process should achieved, and poor communication can jeopardize this. Fear of the unknown is another barrier to this tool. When the management or other responsible stakeholders are not willing to try this because they are used to the current methods, then this tool may not be applied. Snee (79) also says that this tool needs people with relevant skills in order to be applied successfully. This means that individuals without technical expertise on this tool may not find it very useful. According to Munro (47), this explains why this tool has not become popular in the developing countries. The need to have the right knowledge has made various management units to consider using other simpler quality management approaches.
Key Performance Indicators
According to Mukherjee (87), it is necessary to have clear approach of measuring success of a given tool of management in order to determine its appropriateness to the firm. Six sigma has become very popular in the recent past. It is necessary to understand some of the key performance indicators of this tool as a way of bringing an understanding of its relevance within a firm. According to Taylor (112), key performance indicators are a measure used in tracking the abilities and overall success of a process. Key performance indicators are unique to individual firms.
Each firm will have its own key success factors when using Six Sigma Quality management tool. The key performance is determined based on a firm’s objectives. Six Sigma will help define how these objectives should be achieved, and it will measure how successful the process has been when it is finally brought to completion. For instance, Starwood Hotel and Restaurant has its own objectives in the market. One of this firm’s objective is to become a leading hotel for the local and international travelers visiting Dubai.
The key success factor will be determined by assessing the consistency in the growth of its customer base, and comparing this with the success that has been achieved by competing firms. A positive relationship between the current operational outcome and the desired outcome will be a clear indication that the firm is on the right path towards achieving the desired goal. It is important to note that key performance indicators would always be used to determine how successful this tool is to a firm. Morgan (71) says that individual firms have the responsibility of developing SMART objectives that should be achieved by a given period. Success will always be determined by how well the objectives are achieved.
The Pioneers in This Field
According to Munro (132), Six Sigma was developed on the floors of a factory. This tool was developed by a group of engineers of Motorola Company in the United States. This was the first company to develop and use this quality model in its operations in 1986. This tool helped Motorola improve its efficiency in the production process, and in 1991, Allied Signal realized that the tool could not be ignored. It started using it in that year. This was another American firm. It proved very effective, and General Electric, another engineering firm in the United States, realized that it could be useful in improving the efficiency of its production process. It started using this model in 1995. The tool soon became popular in Europe, especially in the early 2000s.
In the United Arab Emirates, this tool is still considered as a relatively new concept. The local business fraternity is yet to embrace it as an appropriate management tool as other firms in the developed countries. However, the concept is slowly finding its way to the local market. Locally, Starwood Hotels and Restaurants is one of the pioneers of this model. This multinational firm operates in Dubai and other cities around the world. This firm could have borrowed this concept from its other branches in developed countries where this concept has become popular. As Eckes (117) observes, one of the main reason that has made this concept not to become popular in the developing countries is its complexity. In order to use this model, a firm should have a workforce that understands it requirements. This is majorly lacking in this country, leading to slow implementation of the method by firms in enhancing their products qualities.
Six Sigma
Eckes (87) says, “Six Sigma is a highly disciplined process that helps us focus on developing and delivering near-perfect products and services.” Business environment has become very competitive that firms are forced to achieve perfection in their operation. This perfection must be exhibited in the production process, and even other processes such as human resource management and marketing. In logistics, there must be a near perfection in the operations. It is only through this that a firm can achieve a competitive edge over other firms in the market.
However, it is not easy to become perfect in the normal operations of a firm. As Charantimath (93) says, a firm would find itself making some mistakes in its operations. Such mistakes can cost a firm its sustainability in the market. Firms are employing every measure to ensure that they eliminate any form of mistakes, or disruptions in their operations. The management is also becoming more concerned of their abilities to predict the outcome of various processes within their firms.
This means that variations in the production processes or in other units should be avoided at all costs. As noted in the above quote, Six Sigma provides solution to all these issues. It offers an environment under which the management can predict time and understand the possible time limit that a production process may take. This quality management tool is slowly finding its way into this country, especially in the city of Dubai. Starwood Hotels and Restaurants is one of the firms operating in Dubai that are currently using this tool to manage quality of their products. In order to enhance its relevance to this firm, it would be necessary to analyze some of the merits and demerits of this tool.
Merits and Demerits of using Six Sigma at Starwood Hotels and Restaurant
A number of total quality management tools have been developed in various sectors and in various countries around the world. In the United Arab Emirates, a number of quality management tools have been developed by the government to motivate quality service delivery in the public sector. In the private sector, some firms have been keen on using other international total quality management tools. At Starwood Hotel and Restaurant, Six Sigma has been the common quality management tool used to monitor and improve the performance of the firm. This method has its merits and demerits. It is important to understand both merits and demerits in order to determine the appropriateness of the firm in achieving success through this method.
Merits
- This strategy helps in elimination of defects during the production process. According to Tennant (51), this tool demands that the number of defects in a production process should not exceed 3.4 per one million units. When this is exceeded, the system would be considered to be malfunctioning. This means that if Starwood Hotels and Restaurant is able to conform to these requirements, it will be able to eliminate excessive defects in its products. This will cut costs of its production, which would help it increase its competitiveness.
- This strategy emphasizes on the need to have consistency in the production process. Many firms have experienced massive losses because of lack of consistency in their operations. Some have even been forced out of the market because of this. The management should be able to determine what a given process will deliver when it is finally completed. This should be consistent with other previous results achieved through a similar system. This strategy offers firms ability to predict the outcome, and this helps in the planning process. Starwood Hotels and Restaurant will be able to achieve this consistency in its operations. This will increase the value of its products to the customers. These customers will know what to expect once they visit this firm. Their expectations would always be met, if not exceeded to increase their satisfaction. The firm will be able to increase its market share based on this.
- One of the principles of Six Sigma demands that a firm should identify processes that are redundant and eliminate them as a way of improving efficiency. At Starwood Hotel and Restaurant, the management would be able to analyze the entire activities in the organization with the view of identifying the redundant processes. By eliminating these processes, the firm would be cutting costs that were wasted in such projects.
- Six Sigma Quality Management tool holds that at the core of all organizational activities should be the focus to deliver quality products to customers. In this competitive industry, Starwood Hotels and Restaurant is always seeking for ways through which it can offer superior customer value. This tool will offer it a guideline on how it can deliver superior customer value in the market. This will give it an advantage over other firms in the market.
Despite the above merits, this tool has some shortcomings that should always be addressed if a firm is planning to use or is already using it to manage quality. According to Schonberger (91), understanding these demerits helps a firm avoid making misguided decisions based on a wrong application of this tool. The following are some of the demerits of this tool.
- Six Sigma Quality Management tool requires some form of knowledge in it, especially by the top management and operations manager. They must know its measures and such tools used in its analysis such as Pareto, Cause and Effect (fish-borne), or Check Sheet. This means that Starwood Hotels and Restaurant will have to outsource a team that understands this tool to offer training to its employees. This will come at an extra cost to the firm. Aruleswaran (81) says that Six Sigma has also been faulted for its complexity due to its inclination towards mathematics and engineering models. This may make employees of this firm avoid the tool.
- Another demerit of this tool is that it requires a heavy communication between different stakeholders. In the process of enhancing consistency and quality of a product, a lot of time is always consumed by the relevant stakeholders. A lot more time will also be consumed in teaching the staff how this model works. Starwood Hotels and Restaurant would use this time in other projects that can help increase its productivity.
- Employees who have learnt this strategy should always be kept within the firm. As Tang (52) notes, after learning about this tools, these employees become a very important asset to the firm. Their departure may cause a double harm to the firm. When such an employee leaves, he or she shall leave with all the resources the firm had invested in him or her through training and experience. It will cost the firm money and time to train another employee who would make replacement. When a rival firm hires such an employee, he or she becomes a threat to the firm because he or she will transfer this knowledge and experience to the rival firm.
Using Cause and Effect (Fish-borne) Diagram at Starwood Hotels and Restaurants
Kaoru Ishikawa introduced this analysis tool in 1990s as a way of solving problems in the process of managing quality within an organization. Starwood Hotels and Restaurant can use this tool to solve various management issues. For instance, this tool can be used to solve productivity problem in one of its many branches in Dubai. The management can use this diagram to identify the best solution for this problem. The diagram below shows some of the steps and stakeholders that will be involved.
Cause Effect Diagram
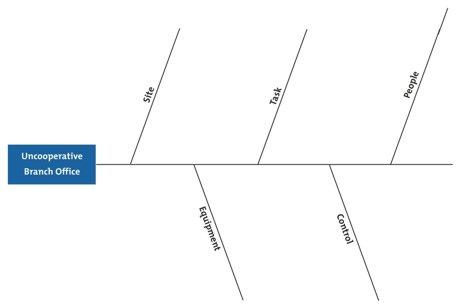
As shown in the diagram, the management will start by identifying the exact problem and the people involved. The management would then come up with tasks, equipment, control measures, and people who will be involved in solving the problem. In this case, the focus will be on finding the best way of making the incorporative branch or office function within the expectations of the management. The focus of this diagram is to find a lasting solution by eliminating the root-cause of the problem. This way, the problem will never be exhibited in the firm.
Conclusion and Recommendations
It is clear from the above analysis that Six Sigma is becoming very relevant in managing quality within organizations. Firms must be ready to embrace this approach of managing quality and efficiency as a way of increasing their competitiveness in the market. Motorola Inc. developed this tool in 1986, but it has become very popular in various fields. In the United Arab Emirates, this concept is still relatively new. The local Emirati firms should consider the following recommendations.
- Local firms should use Six Sigma Quality Management tool to improve efficiency of their operations.
- This tool should also be used when a firm is planning to streamline operations. It helps in identification of redundancy within the firm.
- Local firms should use Six Sigma to improve quality of the final product or service their deliver to customers. This will help in increasing customer satisfaction. This will create a pool of loyal customers to such firms.
- Human resource management should use Six Sigma in identifying employees whose inputs are least needed within the firm as at a given time. Such employees can be redeployed to other departments where they will be more useful.
Works Cited
Aruleswaran, Andrew. Changing with Lean Six Sigma. Selangor: LSS Academy, 2009. Print.
Bufman, Mark. The Lean Six Sigma Guide to Doing More with Less. Hoboken: John Wiley & Sons, 2010. Print.
Burton, Terence. Accelerating Lean Six Sigma Results: How to Achieve Improvement Excellence in the New Economy. Ft. Lauderdale: J. Ross Pub, 2011. Print.
Charantimath, Portia. Total Quality Management. New Delhi: Pearson Education, 2006. Print.
Cole, Brandon. Lean-six Sigma for the Public Sector: Leveraging Continuous Process Improvement to Build Better Governments. Milwaukee: ASQ Quality Press, 2011. Print.
Eckes, George. Six Sigma for Everyone. Hoboken, NJ: John Wiley & Sons, 2003. Print.
George, Michael. Lean Six Sigma: Combining Six Sigma Quality with Lean Speed. New York: McGraw-Hill, 2002. Print.
Harry, Mikel. Practitioner’s Guide to Statistics and Lean Six Sigma for Process Improvements. Hoboken: John Wiley & Sons, 2011. Print.
Larson, Alan. Demystifying Six Sigma: A Company-Wide Approach to Continuous Improvement. New York: AMACOM, 2003. Print.
Morfaw, John. Total Quality Management (TQM): A Model for the Sustainability of Projects and Programs in Africa. Lanham: University Press of America, 2009. Print.
Morgan, John. Lean Six Sigma for Dummies. Hoboken: John Wiley & Sons, 2012. Print.
Mukherjee, Paul. Total Quality Management. New Delhi: Prentice-Hall of India, 2006. Print.
Munro, Roderick A. Six Sigma for the Office: A Pocket Guide. Milwaukee: ASQ Quality Press, 2002. Print.
Sarkar, Debashis. Lessons in Six Sigma: 72 Must-Know Truths for Managers. New Delhi: Response Books, 2004. Print.
Schonberger, Richard. Best Practices in Lean Six Sigma Process Improvement: A Deeper Look. Hoboken: John Wiley & Sons, 2008. Print.
Snee, Ronald. Leading Six Sigma: A Step-by-Step Guide Based on Experience with Ge and Other Six Sigma Companies. Upper Saddle River: Prentice Hall, 2003. Print.
Stamatis, Daniel. Six Sigma Fundamentals: A Complete Guide to the System, Methods and Tools. New York: Productivity Press, 2004. Print.
Tang, Loon. Six Sigma: Advanced Tools for Black Belts and Master Black Belts. Chichester: Wiley, 2006. Print.
Taylor, Gerald. Lean Six Sigma Service Excellence: A Guide to Green Belt Certification and Bottom Line Improvement. Ft. Lauderdale: J. Ross Publishers, 2009. Print.
Tennant, Geoffrey. Six Sigma: SPC and TQM in Manufacturing and Services. Aldershot: Gower, 2001. Print.