Warehouse Receiving Process
In this age, many firms try to satisfy and win customers by reducing the time between an order and product delivery. Although there are different types of warehousing, logistics companies use a cross-docking strategy to achieve a competitive advantage through efficiency. Optimized supply chain management reduces material handling and storage, creating the speed needed to deliver fast-moving goods on time.
Due to this customer-driven approach, warehouse cross-docking has become an essential logistics strategy in supply chains. Warehouse cross-docking involves the direct delivery of products from a manufacturing plant to customers with minimal material handling. The design of the warehouse should allow faster offloading and loading of material. Cross-docking warehousing is ideal when an efficient receiving process and progressive performance indicators are adopted.
Principle of Successful Warehouse Layout and Process Design
Cross-dock Design and Layout
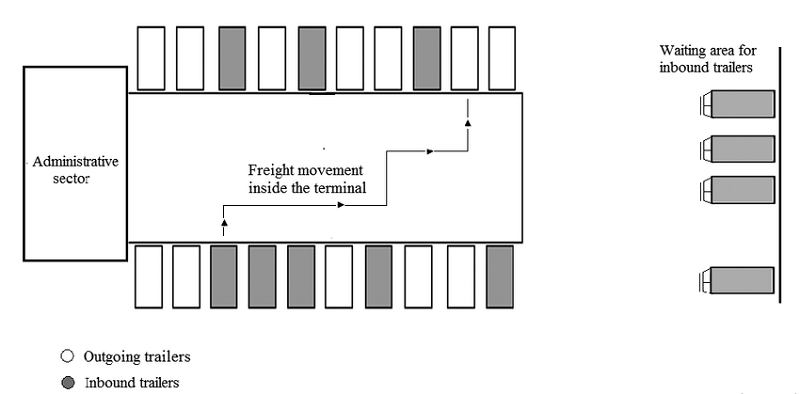
The process design of the cross-docks can influence the facility’s efficiency and productivity. According to Slack and Brandon-Jones (2018), warehouse operators need to align their process designs to meet customer needs (p. 6). A Markov process design is recommended as the best process design for cross-docks facilities (Sahin, 2017; Sharma & Vishwakarma, 2014; Seyedhoseini, Rashid, & Teimoury, 2015). The model accurately accounts for variable changes to determine process outcomes. It adequately addresses effective inbound and outbound processes by outlining the number of docks loading and offloading docks.
A warehouse’s design and layout have wide-ranging implications on a company’s supply chain’s tactical and operational activities. Experts contend that warehouse’s productivity and improve order fulfillment rates through an efficient design (Kawa, 2017). The principles considered while designing a warehouse layout include space, flow, accessibility, equipment handling, and personnel. The economic argument here is that an effective design (the cross-dock shape and size) will reduce labor costs and costs generated from per square foot expenses. Bartholdi and Hackman (2019) reveal that a warehouse tallies expenses by square-foot (p. 51). The per-square prices in a warehouse include rent, climate control costs and cleaning costs (Bartholdi & Hackman, 2019, p. 51). Since warehouses tally expenses by the square foot, designs that minimize the warehouse space should be considered the most efficient.
A design that eases freight movement and handling will eliminate operational inefficiencies. Achieving a seamless freight flow requires a balance between the inbound and outbound door capacity. The capacity of cargo flowing out of the cross-docks should balance with the cargo flowing into the docks (Bartholdi & Hackman, 2019, p. 223). Companies can use two approaches to balance flow rates to achieve a seamless freight flow. First, they can balance the sum total of docking doors. Additionally, they can have a strategic number of workers. The number of outgoing doors should be twice the number of incoming entries. Alternatively, warehouse operators can hire twice as many workers if the cross-dock facility has equal numbers of incoming and outgoing doors.
The Receiving Process in the Cross-docking Warehouse
Receiving is probably the most important process in warehousing because a faulty receiving system or process in a cross-docking warehouse will create trouble for picking and shipping. An efficient receiving process is imperative to reduce delays and product damage in a warehouse (Yang, Li, & Rasul, 2021). The strategy is used to improve the “just-in-time” supply chain, ensuring the inventory does not stay in the cross-docking center for more than 24 hours. Standardization and specialization in the receiving process will eliminate operational inefficiencies in a cross-docking warehouse. The main objective is to receive products in the right quantity, weight, size, and condition to reduce errors and complaints.
Pre-receiving
Cross-docking warehouse thrives on enforcing strict receiving requirements for suppliers, carriers, and shippers. The delivery should be in a way that is easy to process with specifics on label position, the number of packages per pallet, items per carton, label information, and the package size and weight (Sunol, 2020). If the shippers cannot influence the packaging requirements, the supplier should provide clear, detailed information to the transporter. The warehouse can solve the packaging challenge by requesting the supplier to provide palletized goods that will be easier to sort. Furthermore, the delivery note’s order should be strictly followed by the carrier to avoid unnecessary unloading. Documentation by the driver indicating the load details should be accurate to ensure an organized outbound system (Sunol, 2020). For instance, if a warehouse can specify that a truck should load a specific number of cartons and pallets, the knowledge that the goods will be delivered to a single client. A disorganized perceiving system will force the warehouse to unload the products from different trucks then load the required customer quantity.
Labor and booking
An adequate workforce is a critical component of an efficient cross-docking system. Each cargo should have adequate human resources to offload on arrival. Over or under-assigning laborers can result in substantial expenses for the warehouse. A few staff members will collapse the receiving process, while an oversupply will result in unutilized human resources (Sunol, 2020). Therefore, the manager should have the dates and times when cargo is expected and their quantities. A booking or scheduling software for the shippers will guide the manager on when to expect specific consignments.
Unloading
The correct number of human resources and equipment will ensure the warehouse unloading process is efficient and without delays. Typically, inbound shipments arrive at the receiving dock (located at one end of the facility’s terminal) through trucks. Once the trucks have been loaded, the shipment is taken to the outbound destination (mostly located at the distribution center) to be unloaded, sorted, and screened for identification. During sorting, the receiving retailers collect and record data of the shipment. The shipment is then transported to the other end of the facility’s terminal via material handling equipment (MHE) such as forklifts, pallet trucks, and conveyors. The MHE pass through these highways while making their way to the outbound destination via the distribution center (Bartholdi & Hackman, 2019, pp. 23-24). For a cross-dock to efficiently carry out these processes, it needs to have an efficient design layout. A poor design will affect the distance and time taken by the MHE to go through the distribution center. Most receiving processes, including receipting, sorting, identification, and unloading, occur at the distribution center. This center can use a warehousing management system to ease the cross-docking operations and maximize efficiency
Material handling equipment
(MHE) in a cross-docking warehouse are tools and vehicles used to move goods and products from the inbound area to the outbound dock (Bartholdi & Hackman, 2019, p. 220). The right tool for the right material is necessary to move the product efficiently. Cartons can be moved effectively with a conveyor belt, while pallets should be moved with a pallet truck. A conveyor belt is a bulk handling system used to move heavy products to a specified warehouse. Additionally, forklifts are used to lift massive loads that would otherwise be impossible to lift by hand. Such heavy loads are unloaded and loaded using the forklift.
Verification
This is the final step in the receiving process, and it involves a description of goods, quantity received, and cargo condition. In cross-docking warehousing, manual counting is not viable as it is time-consuming and unattainable. Using bar code scanners will speed up counting and eliminate errors (Sunol, 2020). All damaged goods should be counted, documented, and returned to the supplier or disposed of. Cross-docking warehousing often incorporates good faith receiving in their process to save on time.
Performance Measures
Since the ultimate objective of a cross-docking facility is to achieve same-day receipt and dispatch. Operational metrics will include the number of cases dispatched in a day, number of on-time shipments, the number of pallets delivered in a day, and the percentage of vehicle utilization. The above performance measures are “hard measures” because they are quantifiable. However, Richards (2014) recognizes the importance of having qualitative measures as well (p. 16). Measuring intangible attributes such as customer satisfaction can help the warehouse optimize operational efficiency. The qualitative performance indicators include delivering products as promised, distribute products at the right time, and reliability in handling customer problems.
However, optimal performance cannot be achieved by using a single metric. Finding a relevant KPI is challenging due to the complexity of logistic systems and information load. These challenges can lead to judgment bias when choosing a relevant KPI, affecting performance management. Integrated performance models are the best approach to performance management (Chen, Huang, Yu, & Hung, 2017). They combine actual performance data and customer perceptions, which can help companies, align their measures with customers’ demands and expectations (Richards, 2014, pp. 308-309). Such an approach can provide the best decision-making strategy and improve performance management.
The second advantage of using an integrated model is that the KPIs can be weighted based on a performance score. A study conducted by Anjomshoae et al. (2019) showed that an integrated performance model allows for performance benchmarking. The authors proposed using an integrated performance model based on the balanced scorecard. The balanced scorecard (BSD) can be used to record performance based on four dimensions: customer satisfaction, finance, internal processes, and personnel innovation ((Kopecka, 2015). Obtaining data from each of these dimensions can generate quantitative data (data from financial and internal operations) and qualitative data (from personnel innovation and customer satisfaction) (Savkin, 2019). On the BSD, an operator first develops objectives in each of the above dimensions. Each goal will be assigned a target measured against an actual performance score on the BSD.
The balanced scorecard is appropriate for cross-dock facilities because of the nature and set-up of the facilities. Since they avoid freight storage, operators need to focus on warehouse processes to expedite the next stage’s shipment. According to Terziev and Stoyanov (2017), the BSD model is best suited for such process-oriented facilities. Using the BSD model can help cross-dock operators to concentrate on the efficiency and effectiveness of warehouse processes.
Future Areas of Innovation
Companies need to manage their operations in the current global economic market to achieve a competitive market effectively. It is projected that automation will be the corner-stone of future logistics management (Chen &Zhao, 2019; Dekhne et al., 2019). Warehouse management systems (WMS) are used to facilitate cross-docking operations. Typically, cross-docks operators manually enter freight identification numbers while receiving cargo. Procedures such as cycle counting, receipting, and cycle counting are done manually. Manual data entry increases the likelihood of human errors, which can result in inaccurate supply chain data.
The best system for automating the receiving processes is the advanced system notification (ASN) software. The ASN can reduce the receiving time by 60%, which translates to saving 65,000 receiving hours for a 250-door cross-dock (“Improving Cross-Docking Efficiency”, 2014). Using an ASN system during the receiving process involves capturing identifiable data via hand-held device. The scanned data is then automatically conveyed to a central data repository (the ERP system) through an electronic data interchange (EDI) or automatic e-mails. Since data collection is automated, it is easier for the receiving retailer to ensure efficient inventory handling. A common problem in multi-door cross-docks is differences between the physical cargo received and the reported cargo data. However, with ASNs, such problems including imperfect transactions, cargo misplacement, lost inventories, and wrong entries can be resolved.
Automating the data collection during the receiving process may also involve the use of devices that allow for a two-way communication system. Agnostic-devices such as handheld computers, ruggedized tablets, and GS1 barcode scanners are examples of technologies that foster two-way interactions between the receiving retailers and system administrators (Pandian, 2019). For example, integrated GS1 barcode labels can link every logistical unit to the purchase orders. This approach allows the retailers and administrators to track and follow-up on shipment across the supply chain. Integrated GS1 barcode labels can link every logistical unit to the purchase orders (Korzeniowski, Praiss, & Żmich, 2018).
The main benefit of using the ASN and GSI barcode is that they expedite the receiving process, quicken order fulfillment, and increase inventory visibility (“Improving Cross-Docking Efficiency”, 2014). The GS1 barcodes labels are inscribed on cartons, and the information is scanned by a hand-held agnostic device and then communicated to the ASN. Data can also be received through RFID tags placed on cartons, physical automation equipment such as vertical lifts, and carousels. Increasing accuracy in inventory data can improve efficiency and productivity at the warehouse.
Another area of innovation is automating the shipping and receiving process at the distribution center. Expediting the flow of goods to the distribution center is critical to the facility’s productivity since the receiving process is a labor-intensive but a low-value process (Caudell, 2018). Companies are using the A-frame machine to expedite freight flow through the distribution center. An A-frame machine, an automated dispensing machine, automatically drops cargo onto a conveyor or forklift truck (de Koster, 2018). A control system schedules conveyor or forklift intervals for each customer offer. As the conveyors or forklifts pass through the cross-dock highways, the customer’s orders are deposited onto them and carried away to the distribution center.
Conclusion
The design of the facility- its size and shape- can maximize the facility’s efficiency. However, integrating internal operations with the facility’s plan is not an easy task. For a cross-dock facility to operate efficiently, it must have adequate personnel, the suitability of systems, and cross-dock designs. The best plan for a cross-dock depends on its size (number of doors). The Markov model should always be used to determine the most suitable process design. Finally, ERP systems are the most suited software for optimizing receiving processes in cross-docks.
References
Ahangamage, N., Niwunhella, D. H. H., Vidanagamachchi, K., & Wickramarachchi, R. (2020). Implementing a cross-docking system in a warehouse: A systematic review of literature. In Proceedings of the International Conference on Industrial Engineering and Operations Management Dubai, UAE, March 10-12, (pp. 1005–1012). IEOM Society International. Web.
Anjomshoae, A., Hassan, A., & Wong, K. Y. (2019). An integrated AHP-based scheme for performance measurement in humanitarian supply chains. International Journal of Productivity and Performance Management, 68(1), 1–20. Web.
Bartholdi, J. J., & Hackman, S. T. (2019). Warehouse & distribution science: Release 0.89. The Supply Chain and Logistics Institute.
Caudell, D. (2018). Warehousing 101: An introduction to warehouse automation. RFgen. Web.
Chen, J., & Zhao, W. (2019). Logistics automation management based on the internet of things. Cluster Computing, 22(6), 13627-13634. Web.
Chen, P. S., Huang, C-Y., Yu, C-C., & Hung, C-C. (2017). The examination of key performance indicators of warehouse operation systems based on detailed case studies. Journal of Information and Optimization Sciences, 38(2), 367–389. Web.
de Koster, R. (2018). Automated and robotic warehouses: Developments and research opportunities. Logistics and Transport, 38, 33-40. Web.
He, M., Shen, J., Wu, X., & Luo, J. (2018). Logistics space: A literature review from the sustainability perspective. Sustainability, 10(8), 1–24. Web.
Improving cross-docking efficiency in four key areas. (2014). Cognizant. Web.
Kawa, A. (2017). Fulfillment service in e-commerce logistics. Scientific Journal of Logistics, 13(4), 429–438. Web.
Kopecka, N. (2015). The balanced scorecard implementation, integrated approach and the quality of its measurement. Procedia Economics and Finance, 25, 59–69. Web.
Korzeniowski, A., Praiss, A., & Żmich, J. (2018). Comparative analysis of the quality of digitally printed barcodes. Business Logistics in Modern Management. Web.
Pandian, A. P. (2019). Artificial intelligence application in smart warehousing environment for automated logistics. Journal of Artificial Intelligence, 1(02), 63-72. Web.
Richards, G. (2017). Warehouse management: A complete guide to improving efficiency and minimizing costs in the modern warehouse. Kogan Page Publishers.
Savkin, A. (2019). Warehouse KPIs and balanced scorecard. BSC Designer. Web.
Sharma, S. P., & Vishwakarma, Y. (2014). Application of Markov process in performance analysis of feeding system of sugar industry. Journal of Industrial Mathematics, 2014, 1–9. Web.
Seyedhoseini, S. M., Rashid, R., & Teimoury, E. (2015). Developing a cross-docking network design model under uncertain environment. Journal of Industrial Engineering International, 11(2), 225-236. Web.
Slack, N., & Brandon-Jones, A. (2018). Operations and process management: Principles and practice for strategic impact. Pearson UK.
Sunol, H. (2020). Warehouse operations: optimizing the receiving process. Cyzerg Warehouse Technology. Web.
Yang, J. X., Li, L. D., & Rasul, M. G. (2021). A conceptual artificial neural network model in warehouse receiving management. International Journal of Machine Learning and Computing, 11(2). Web.