Introduction
Providing an analysis of the process of designing and manufacturing Airbus A380 in the context of systems and operations management, it can be stated that such process is an exemplary case of the lack of full integration of systems and operations. A system is defined as “a set of interrelated parts that must work together” (Stevenson, 2008), which application to the case of Airbus, might imply that such system is composed of various manufacturing sites across Europe, those sites each had their lower subsystems, such as design and manufacturing departments (Slack et al., 2009). The lack of integration between the operations implies that the systems approach was not used in the company, with interrelation being absent between their subsystems. The total lack of integration was an acknowledged problem in the company (Schwalbe, 2010).
In order to understand the deficiencies in the operations processes during the manufacturing of the Airbus A380, the Input-Process Output (IPO) model, sometime called Input-Transformation-Output, might be applied in this case. The IPO model is universal in depicting the processes of all sorts, the main aim of which is simplifying a relatively complex process (Fundamentals of Technology, 2010). A graphical depiction of the model can be seen through Fig 1.
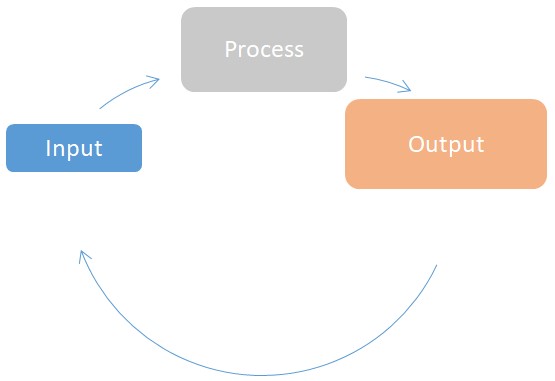
The explanation of each of the component can be seen through filling out the processes with information from the case (Slack et al., 2009), in which a few examples such as the following might be insightful:The support of systems to the strategic, tactical, and operational levels of the business can be seen through the case of Airbus, through the what-if scenarios. Certainly, with the way operations were managed in the case, there was a massive impact to the strategy of the company and its decision making process; a negative impact in that matter. In an ideal condition, i.e. system integrated with business systems will support the business through providing accurate estimates of the company’s outputs, according to which decisions are made. With the strategy of the company being revolved around economic benefit, through matching supply with demand, systems are support business through the coordination of such process (Stevenson, 2008).The implementation of subsystems in that regard should ensure the taking into account all of the parts of the systems. Integrating the IPO model with the systems view, the latter should ensure that the outputs of each subsystem should be considered as an output in another subsystem in a seamless fashion. In modular process such as the design and the manufacturing process of an aircraft, where each component of the aircraft can be manufactured separately, taking into account each separate subsystem is essential.
On the strategic level, systems can provide an insight on the basis of which future capacities can be planned, the way inventory and raw material purchase decisions can be made, and the costs and reliability of the company c (Brown, 2004). It can be seen that in each of the aforementioned component Airbus was lacking. Future capacities decisions might be compromised, where with more than 189 orders placed by companies, such as Emirates, Qantas, Singapore Airlines, Air France, and others, which they included in its strategy, the failure to deliver on time might prevent Airbus from making future predictions on capacities (Done, 2007). In terms of costs, the program of the company targeting cost reduction and the fact that the company will have to manage “two years without the revenue that the company had expected” is an indication that the system in the company did not support business on the strategic level (Slack et al., 2009).
On the tactical level, systems can support the business through managing the day-to-day activities, in scheduling and tack allocation and through managing the changes in the process technology (Brown, 2004). Similarly, the systems of the company did not support the business on the tactical level, which can be evident through the unplanned changes the company had to go through, e.g. moving two thousand German staff from Hamburg to Toulouse, and the inability to streamline many processes in the company (Slack et al., 2009). Such aspects indicate the deficiencies of in the company’s management of operations. Thus, the operations and the systems of the company are weakly integrated, where the main apparent strengths can be seen through the company’s dedication to quality standards, considering the reviews the aircraft received, despite the two years delay.
Airbus Operations Management Drawbacks
In order to identify the areas for improvements in the organization there are many methodologies that help analyzing the situation through focusing on the root of the problem. One way to achieve the latter is through the Soft System Methodology (SSM), an approach designed by Peter Checkland and his colleagues at Lancaster University, which main aim is providing a structured solution to unstructured problems (Lester, 2008). The core of the methodology, as with many other methods, is the comparison between the real world and some models of the world (Williams, 2005). The attributes that distinguish SSM from other systems is providing evaluators the ability to apply the experience of the company to structure and model a view about a problem in a company and compare it to the real world (Williams, 2005). The advantages of SSM can be seen through the following (Checkland, 1999):
- Providing structures to complex organisational problem situations and allows responding to them in an organised way, forcing users to search for solution for such problem.
- Providing particular and specific methods.
- Can be used as an instrument for unstructured problems (Checkland, 1999).
The map of the SSM applied for a real world situation can be explained through the sequential steps of presenting a situation, analyzing it, identifying the root definition, presenting a conceptual model, compare it with reality, defining changes, and implementing the changes, see Fig 2 (Dick and Swepson, 2000). It should be noted that not all steps of the methodology can be provided by external parties, where the last three steps need the involvement of the organisation itself.
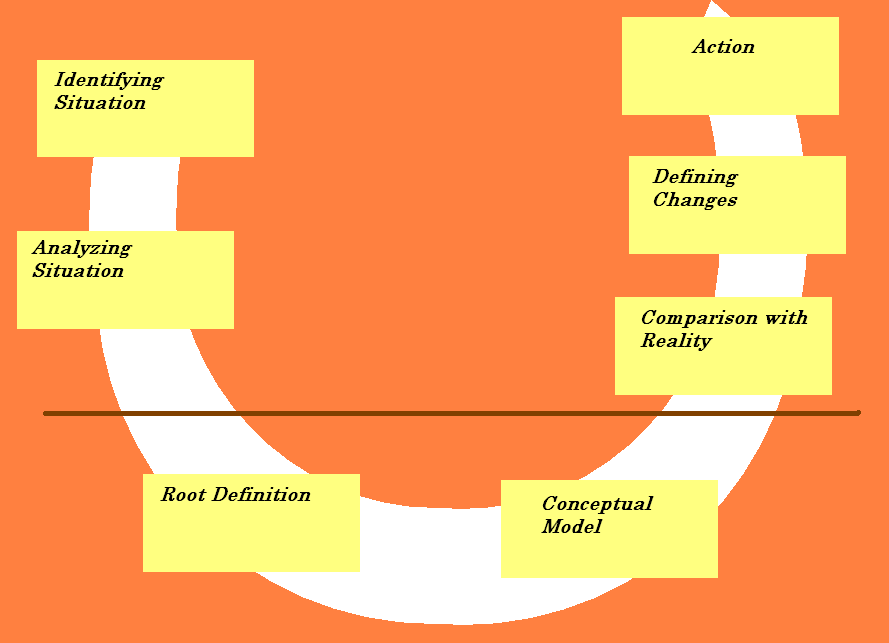
The applicability of the system is explained through complex organisational situation in which a significant social, political, and human element is existent (Checkland, 1999). In that regard, the SSM can be summarized as the process of applying hard systems components to human activity systems. Analyzing the case of the Airbus, it can be stated that it perfectly fits the criteria for problems in which SSM might be applicable, there is the involvement of the political factor, evident through the constant political infighting, particularly by the French and German governments (Slack et al., 2009). There is the social factor, which can be seen as the result of the previous factor, and resulted in the tension between staff and management of the two manufacturing sites. Finally, the human factor can be seen through the mistake in manufacturing cables, the overcrowded working conditions, with more than two thousand employees transferred from one plant to another, from Hamburg to Toulouse at the early stages of design (Slack et al., 2009).
An SSM instrument that can be used to analyse the situation is CATWOE, which is an abbreviation of the main components of the instrument, Customers, Actors, Transformation process, World-view, Owners, Environmental/external factors (Lester, 2008). Thus, CATWOE is the stage related with identifying the situation, and which components can be seen through the following table (Creating Minds, 2010, Maqsood et al., 2006):
The stage at which the situation can be analysed through SSM might benefit from the illustration of the situation through diagrams, an approach in SSM called Rich Diagrams. A rich diagram can be defined as a tool that can be which structure a situation through drawings in a way that enables understanding the components and processes involved (Couprie et al., 2000). The rich diagram of the situation can be seen through Fig 3.
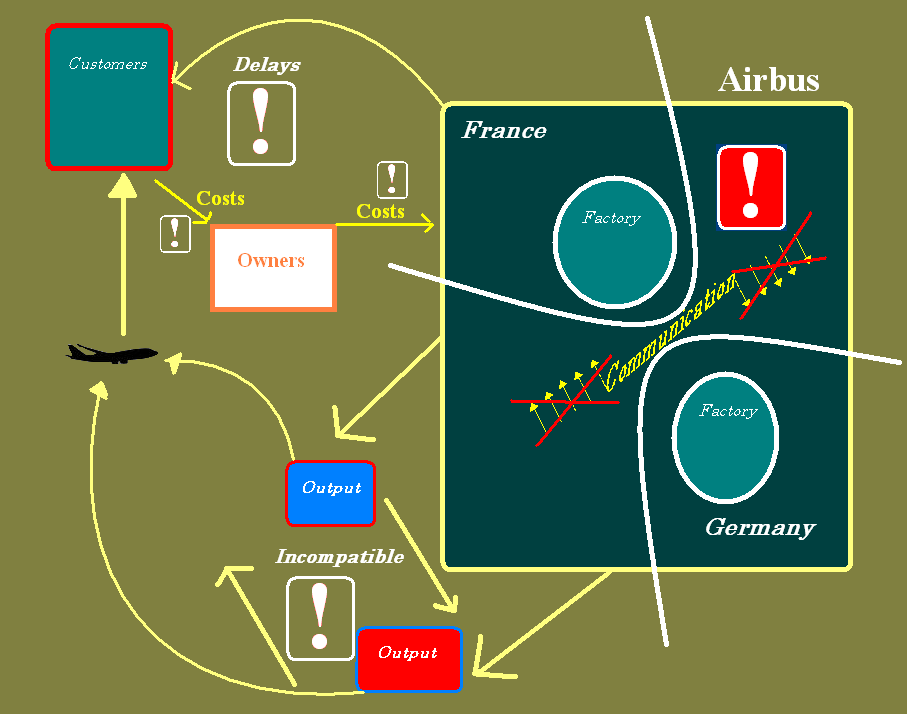
The aforementioned rich problem is used to communicated the problem, and indicate its root within the situation, which leads to the next stage of the SSM – root definition. The root definition can be defined as a well articulated statement about the area of concern, its activities and components (Jarvis, n.d.). In that regard, a root definition is an important outcome of the SSM process, which lay out the development of the conceptual model of the system (Williams, 1999). The root definition of a system that involves the actors and the transformation process described in CATWOE can be seen as:
Airbus Operations Management Improvements
Analyzing the areas of concerns identified through the rich picture is related to three areas which are communications and knowledge management. In that regard, it can be stated that despite the fact that the problems are connected to social, political, and human factors, its solution can be purely technological. Thus, such improvements can be described as more of a breakthrough, rather than continuous, where the communication process of the company will be reworked and integrated into the proposed system, which is a corporate portal. The core of the proposed improvement is integration. With the core deficiency in the operations in Airbus is management disintegration; the proposed solution will focus on integrating communication processes.
The barriers between the staff result in the lack of coordination between functional areas in the business, which can be seen through the case of Airbus (Young, 2009). The suitability of the proposed improvement can be seen through the typical imperatives for a corporate portal implementation, which are identified as reducing costs, integrating decision making processes, increasing the speed of delivery to the market, and improving collaborative work and communication (Terra). It should be noted that there are other imperatives, while those mentioned are specifically applicable to the Airbus case. Taking the wiring case in Airbus as an example of disintegration management, corporate portals can be defined in the light of such cases as a central hub for organizational information, where each employee will have an access to information related to their business processes, which will be standardized and unified for all departments in the company. Such portal will improve the process of sharing such information in the organization as well as their knowledge management capabilities (Nemati et al., 2002).
The implementation of the corporate portal model and the way it fits within the operation of the defined system can be seen through Fig. 4.
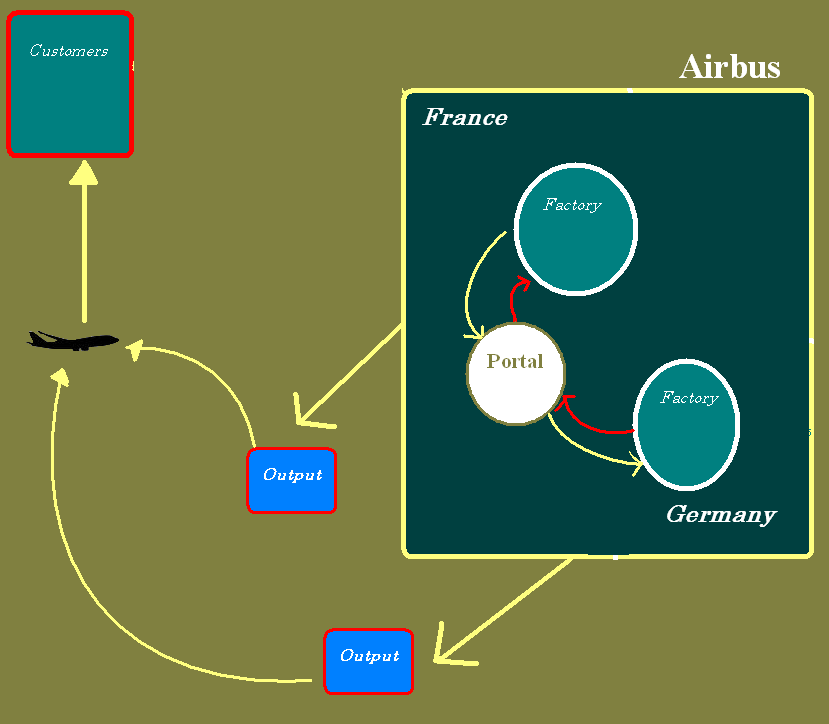
The use of SSM provided an outlook of the way the system shall operates, its concern areas, and the direction for the desirable outcomes. In that regard, the information exchange between plants was improved through putting an intermediary point between both internal actors in the system, in that matter unified the standards for the information exchange between different subsystems within the organisation, and improved the efficiency of the management functions.
Accordingly, the integration of the knowledge in the organisation, subsequently will integrate the related processes in the system. The latter will lead to the system supporting the decision making in the business on all levels. Having a single view on the organisation will allow the company plan its actions. On a tactical level, an efficient communication between different plants will improve the day-to-day scheduling activities and task allocation, reducing incompatibilities to the minimum, providing the possibility for them to be resolved instantaneously. The fragmented structure of the organisation will be irrelevant as the knowledge on the output of such structure will be in a single location in real time. Corporate portals allow integrating different systems, both through the interface, and on the data level (Terra). If measuring the impact of the improvements through the IPO model, it can be stated that those improvements are aimed at making increasing the desirable outputs, decreasing the unexpected, and unifying the standards for the inputs and the outputs used.
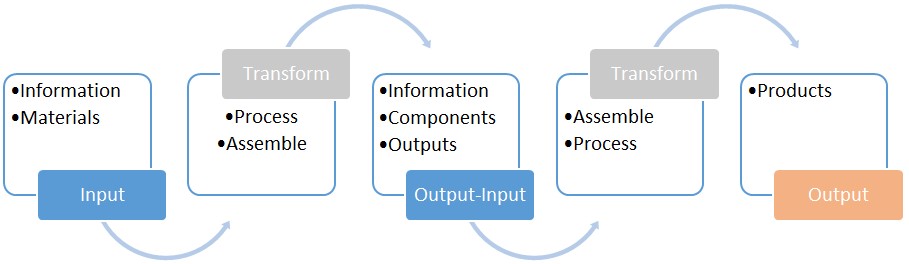
It can be seen from the figure that the standardisation of information exchange contributes to the integration of several processes in the organisation. The latter might be reflective of the example of wiring, where the output of one sub-system was used as an input in another. Information in that matter can be used as a common denominator, as it will be centralised at all stages of operations in the organisation, facilitating the monitoring process. Thus, it can be stated that the implementation of SSM allowed structuring the situation in Airbus according to a specific model. Such model in turn, allowed identifying the issues of concern and areas of weaknesses in the organization, as well as the methods such weaknesses can be overcome. Additionally, the selection of a corporate portal as a solution was driven by the requirements and the need for improvements and the capabilities of corporate portals. It should be stressed out that SSM does not enforce a particular solution, where other methods of improvements could be equally proposed.
Airbus Operations Management Issues
It should be noted that the improvements proposed are not limited to simply suggesting a software solution that will eliminate areas of concern for Airbus. There are other issues involved as well, a due consideration of which will contribute to improvement of operations at Airbus. Such issues can be divided between people, technology, and organisational.
The human aspect in the Airbus case played a significant role, and thus, improving the quality of work life should be among the priorities in the organisation as well. One of the important aspects of quality of work life is the way employees get along with their co-workers and working conditions (Pigford, 2001). Looking at the tense relationships between various departments of Airbus, specifically if those departments were geographically and politically dispersed, and the overcrowded conditions in which employees worked at a certain point of time, it can be stated that a corporate portal alone will not be sufficient to resolve such conditions. Thus, work redesigns should be considered to address such problems in the workplace. One of the elements of redesign proposed is related to cultural change in the organisation. Cultural change will focus on imparting the collaborative, rather than competitive, and conducting appropriate relationship management (Bettley et al., 2005). One area for improving the teamwork in the company is through strengthening a sense of common purpose throughout the whole organisation, and the adherence of a shared vision. The responsibility of HR management along with operations in that matter will be in redesigning the workplace, improve top-down communication, and building trust and motivation among employees, through empowerment (Bettley et al., 2005).
Considering the fact that the proposed improvements are based on a technological solution, the role the technology plays in that matter is enormous. In that regard, not only the technology will facilitate certain aspects of the job such as communication and information exchange, many processes in the organisation will be redesigned. One example can be seen through that design stages between the different facilities will be simultaneous, rather than sequential. Technology in that matter is an aspect in which investments might be quite impressive, and thus, determining the level at which the technology will be implemented is essential.
The way such technology will be utilised is more important than the fact of utilisation itself. In that regard, the approach taken to analyse the situation at Airbus, outlined the needs first, addressing which the technology was proposed. An important element that should contribute to a successful implementation of technology is organisational learning that should occur at the same time, where the best fit will be achieved when there is technology and the context in which it is used are getting along (Bettley et al., 2005).
The organisational context presupposes that the management of the organisation should adopt its structure to suit the improvements proposed. In that regard, management issues played a significant role in the problems Airbus had in the first place, where the management of different departments emphasised a competitive approach in the company. The structure of the management and poor decision making process led to managerial changes in the company, which can be seen through the resignation of such executives as Gustav Humbert, Airbus’ Chief executive, Noel Forgeard, EADS co-chief executive, and Charles Campion, the A380 programme manager (Slack et al., 2009). The changes in the structure of the management should include a clear distinction of roles and the way decisions should be compatible and aimed toward a single goal. Thus, the improvement of information exchange and knowledge management that will be achieved through the corporate portal should be accompanied by policies that will govern the communication between the managerial levels as well.
Conclusion
The present reports provided an analysis of the situation in Airbus during the development of their A380 aircraft. The report assessed the role of systems and operations management in the case, using Soft Systems Methodology (SSM) to identify areas that should be updated. After using SSM it can be concluded that the operation of the company had deficiencies and areas of concern. The use of SSM allowed structuring the problem and identifying problems and the way such problems can be tackled. Corporate portal were found to be a suitable solution that addresses the problems of the company. Thus, the use of SSM allowed presenting a clear picture of the situation in Airbus, which would have allowed them coordinate their work better and avoid the problems and the delays they have gone through during the design and the assembly stages of Airbus A380.
Reference List
Bettley, A., Mayle, D., Tantoush, T. & Open University. 2005. Operations management : a strategic approach, London ; Thousand Oaks, CA, SAGE Publications.
BROWN, S. 2004. Strategic operations management, Boston, MA, Elsevier.
CHECKLAND, P. 1999. Systems thinking, systems practice, John Wiley.
COUPRIE, D., GOODBRAND, A., LI, B. & ZHU, D. 2000. Soft Systems Methodology. Web.
CREATING MINDS. 2010. CATWOE. Web.
DICK, B. & SWEPSON, P. 2000. Appropriate validity and its attainment within action research: an illustration using soft systems methodology [Online]. Southern Cross University. Web.
DONE, K. 2007. Airbus hopes its troubles finally take flight. Web.
FUNDAMENTALS OF TECHNOLOGY. 2010. Technology Competencies Problem-Solving. Web.
JARVIS, C. Checkland and Smyth’s CATWOE and Soft Systems Methodology. Business Open Learning Archieve. Web.
LESTER, S. 2008. Soft systems methodology. Stan Lester Developments. Web.
MAQSOOD, T., FINEGAN, A. & WALKER, D. 2006. Applying project histories and project learning through knowledge management in an Australian construction company. Learning Organization, 13, 80 – 95.
NEMATI, H. R., STEIGER, D. M., IYER, L. S. & HERSCHEL, R. T. 2002. Knowledge warehouse: an architectural integration of knowledge management, decision support, artificial intelligence and data warehousing. Decision Support Systems, 33, 143– 161.
PIGFORD, L. 2001. The successful interview & beyond, Albany, NY, Delmar.
SCHWALBE, K. 2010. Information technology project management, Boston, MA, Course Technology.
SLACK, N., CHAMBERS, S. & JOHNSTON, R. 2009. Operations management, Harlow, England ; New York, Financial Times Prentice Hall.
STEVENSON, W. J. 2008. Operations management, McGraw-Hill/Irwin.
TERRA, J. C. Developing a Business Case for Corporate Portals. Web.
WILLIAMS, B. 2005. SOFT SYSTEMS METHODOLOGY. The Kellogg Foundation. Web.
WILLIAMS, M. C. 1999. Composite Case Study Demonstrating the Use of Soft Systems Methodology for Analysing Information Management. Web.
YOUNG, S. T. 2009. Essentials of operations management, Thousand Oaks, Sage Publications.