Introduction
Company ABC is part of a large multi-national American Organization that assembles transmission for the North American Truck market. The company is re-organizing and is moving part of its operations to another sister plant in Europe. The part of operations the business is moving is involved with the manufacture of gears and shafts. Previously, the company manufactured gears and shafts for the transmissions they produced. The re-organization is aimed at ensuring the introduction of a significant large number of parts that were previously produced at another plant in Manchester. This requires that the business move to a cell manufacturing process plant. The project will take 6 months, starting 10th October 2010 to April 2011 the same date or earlier. Any delays will cause significant problems to the supply chain of the organization. Therefore, the plant has to be in full production by the set date or earlier.
This paper has identified five processes that will have to be completed in different timeliness to ensure the plant is running on time. These processes include preparations for the new plant equipment setup and its equipment, finding new suppliers and increasing the capacity of existing ones, putting in place and organizing human resources, plant layout and production planning, and finally putting all the above mention processes together to come up with a complete and operational plant. The report briefly analyzes these processes, expected challenges and how they will be overcome.
New Plant layout
The new plant layout is aimed at ensuring easy and effective movement of people, raw materials and finished products from one point to the other. The Numerical control center will ensure proper coordination and communication of operations within the plant.
Shafts (60%)
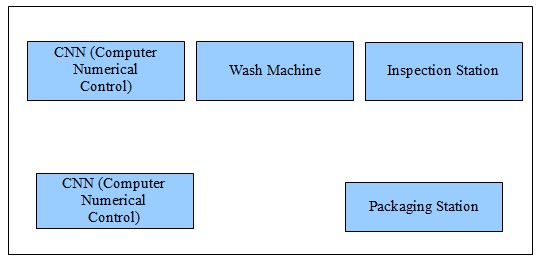
Gears (40%)
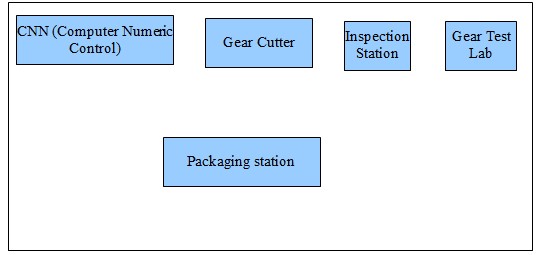
New plant equipment
This is the first step of the project and determines how the other processes will be run. It will include determining what equipment will be required, where they will be found and how they will reach the designated location. The foundation of any project determines the success of the other process and the final results that the project intends to achieve. For a successful plant layout, the business will first need to establish a good and accessible location for the project and ensure there is a well able and experienced project manager. The chosen site must have the basic facilities such as a well developed drainage system, a waste management plan, water, power and other basic amenities that the project will require. When all the basic necessities are in place, then the step will involve planning for the plant’s operations, site design and architecture, sourcing for materials and purchases for those available.
Gantt Chart
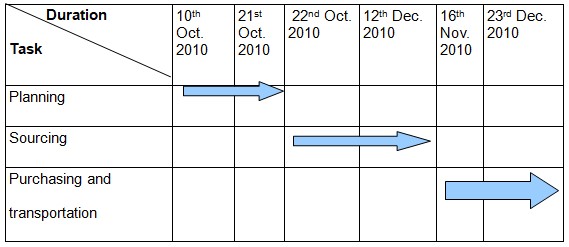
Problems that are likely to arise in this stage include lack of reliable suppliers, unprofessional designs and lack of proper human power. To alleviate these challenges, the work will be done by ABC designers and engineers who already have experience in setting up new plants and use their existing suppliers to get the equipment as well as refer new suppliers who can be trusted.
New suppliers and old suppliers increased supply
Good suppliers not only ensure quality, but also help the project manager stay within the set time limits when doing a project. A company whose procurement has a good relationship with its suppliers is bound to get products at a fair price and get them without delays. There are new equipment needed for this project and for this reason, the business will need to back-up its existing suppliers with new ones. Even though it is an expensive operation, the business will need to do it to ensure a consistent supply during construction and set-up of a new plant.
The process will involve determining how many parts the plant intends to create (capacity), the number of machines to be bought and what type. After that is done, a panel will be set to interview the new suppliers on their capacity to deliver, have them submit samples and negotiate prices. The existing suppliers will be provided with the list of required parts to have them deliver samples and negotiate prices. Since the project has a limited time-line,parts which are available in the shortest time possible will be preferred. Among the products that the new plant will require include 20-25 gear cutters, 50 CNC, communication devices among others.
Challenges expected include inconsistent suppliers, delayed deliveries and high prices. To curb these challenges, the business will use existing suppliers, who the business has established a good relationship with in the time it has been in operation. The suppliers will be used to get the required suppliers and refer new suppliers that can be trusted. The company will also try to source as many materials as possible from the local markets to minimize time needed to transport them. Sourcing from the local markets will also make it easier to return defective materials and have others in the shortest time possible. By choosing an accessible site, it will be easier to transport the equipment to the site hence save time.
Gantt Chart
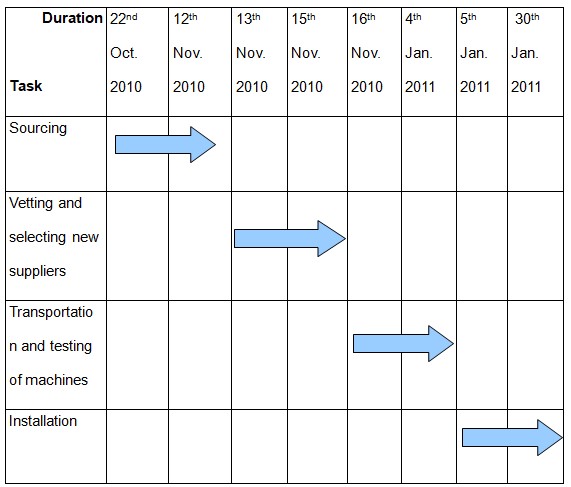
Human resource issues
“Human resources make up the workforce of an organization and help implement policies relating to effective use of resources to produce results”. This is the stage that will bind all the other processes together to produce a team that will be responsible for the day to day operations of the plant. The number of employees needed for the project is assumed to be established a month before the project begins. The rest of the process is expected to take up to four months for satisfactory completion.
Gantt Chart
The biggest challenge that the step is expected to face is lack of experienced personnel. This will be tackled by advertising for the jobs early to ensure many people apply, thus creating a big pool of people to choose from. Senior positions will be given to existing ABC employees from other plants who are already familiar with the company’s policies. From their experience with the company, they will be able to create consistency in the type of quality expected.After interviews are done and a team is established, ten of the employees are expected to go to Germany for training on how to run such a plant. They are then expected to return and train the rest of the team. Training is expected to end just on time to begin operations. It is expected that not all offers made will be accepted and therefore, the panel will give enough time for the process to ensure there is enough time to fill up gaps that may be left by those who reject their job offers.
Plant layout and production planning
Plant layout and production planning will be the last step of the process. According to Singh, plant layout and planning can save a business a lot of money and time by ensuring easy movement and minimum wastage. Planning designs are expected to be ready from the first step, suppliers are expected to be identified in the second step and orders made and delivered. This process will carried out by ABC engineers to ensure consistency with the company’s facilities structures and quality of work. Installation is expected to take one month, with an assumption that required materials will be delivered on time.
The number of equipment bought and installed is classified into three categories. There will be equipment needed for manufacturing the parts, those required for assembly and those needed to set up a storage facility. This stage of the process is expected to start late due to the fact that some equipment will take a few months to be delivered. The engineers will start with those equipment that will take less time to reach the plant such as gear cutters, and progress as others arrive.
Challenges expected at this stage include wrong specifications for delivered equipment and late delivery of material. The person in charge of this stage of the process will be expected to stay in touch with suppliers and inspect the equipment in their facilities before they are delivered. Suppliers will be given strict deadlines and earlier dates of delivery to provide allowance for lateness.
Gantt chart
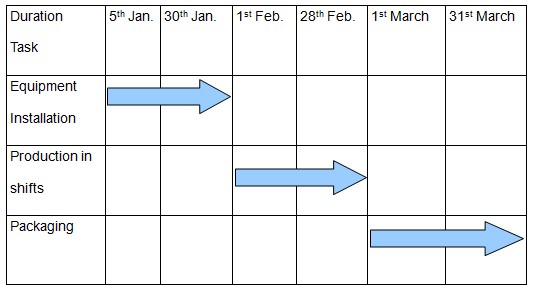
Overall plan
According to Lonergan, a project is considered successful if achieves its goals and objectives at the set time. The overall process is scheduled to end a month earlier than the set deadline. This is so as to give room for any lateness or delayed deliveries. From the designed Gantt charts, the project is expected to be complete by the set deadline so that normal operations can begin at the designated time. Challenges in the overall project will be avoided by ensuring well qualified and experienced teams on board and adhering to all set deadlines for the different stages of the project.
Overall Gantt chart
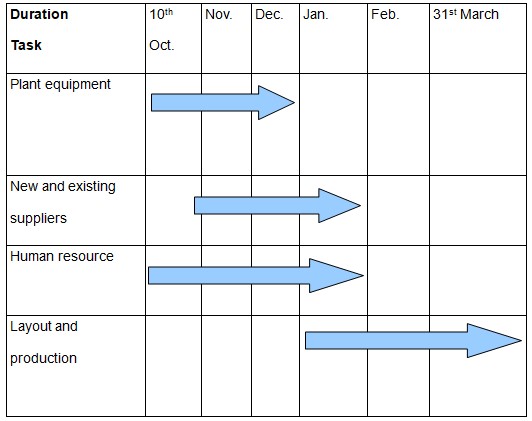
Tasks
Network diagram
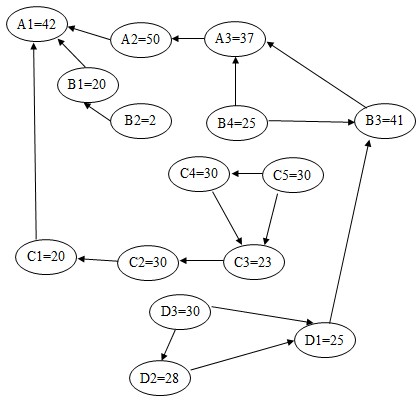
Bibliography
Harold, K. Project management: A systems approach to planning, scheduling and controlling. John Wiley & Sons Inc, Boston, 2009.
Heerkens, G. Project management: 24 lessons to help you master any project. McGraw-Hill, New York, 2007.
Lock, D. Project management. Ashgate, Burlington. 2007.
Lonergan, K. All about project management. 2011. Web.
Singh, P. Setting up a manufacturing plant, California State University, California, 2005.