History: The Need for Activity Based Costing
In the 1980s, many managers became disillusioned with their cost accounting system. This led to the adoption of activity-based costing systems because of dissatisfaction that these managers with regards to their existing cost accounting system. There are several reasons for this choice. The first and most major reason are the disadvantages with the previous cost accounting methods where the allocated fixed overhead, including labour, were usually subjective; not essentially related or directly associated to production. Therefore, the use of single pools of indirect costs and bases for the incidence of overheads e.g. direct labour hours were no longer a viable option. In modern day manufacturing milieu, resources used in production are often unrelated to direct labour and misallocations like these can cause management to place costs to the wrong products. Now, profit maximization can only take place via two mechanisms: one option is cost cutting. However, companies focused on cost cutting are only inviting trouble. We have the example of the Thornton Equipment Company who realized the need to decrease the overhead cost structure but were unable to do so because of the importance of overhead costs. Hence, cost cutting is not a viable solution. The other mechanism is correcting products prices. This mechanism directs the management to activity based costing. (Reyhanoglu, 2004)
The other major factor instrumental in this surge towards activity based costing is information requirements that are required. The purpose of cost accounting systems is to provide information to assist managers in executing optimal cost management. If manufacturing processes are redesigned and re-engineered, then the accounting systems must also fit the new specifications. Now, if the business activities are well executed, costs will invariably decline and products will be gain competitive advantage. Progress in the gathering of information gathering has made the gathering and processing of more detailed information demanded by activity-based costing a realization. These reasons have urged the companies to move to activity based costing as costs can be better managed and products more accurately appropriated their relevant costs. Some indicators can signal the need for a new costing system:
- Mistrust in the allocation of product costs
- A discontent marketing department as a result of the reported product costs.
- Despite charging market price, some products still generate a profit.
- Increasing sales and decreasing profits
- Despite high margins, products are still not being met by competitor interest
- High and consistently increasing overhead costs
- Variety in product mix
- Direct labour constitutes a small part of production cost
- Competitors appropriate a very low price to a firmsâ product (Reyhanoglu, 2004)
Implementing an Activity Based Costing System
An Activity-based costing system follows two steps. The first step identifies major activities and appropriates overhead costs to each activity depending on the proportion of the resources that are employed in that activity. The overhead costs that are assigned to each activity form an activity cost pool. After the assigning of overhead costs is complete, identification of cost drivers relevant each cost pool ensues. Then in step two, division of overhead costs from each cost pool to each product line in proportion to the cost driver consumed by the product line. (Diagram 1) (Roztocki, 2000)
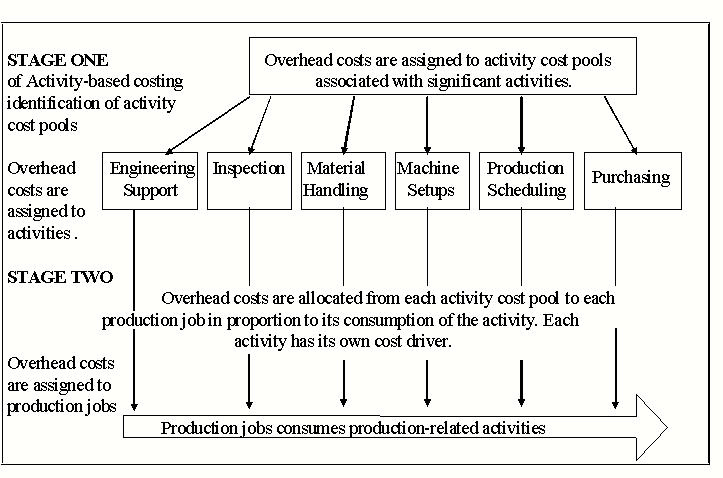
To do this, companies can create a new department called âactivity accountancyâ. This accounting mechanism calculates revenues and costs for each activity. They manage and control the planned activities of the business. In accordance with the requests of the managers of the company, they can organize each activity as a profit centre. The job of an activity accountant is broken down into three parts mentioned below:
- Resources determined on activities and then planning.
- Renewable activities are first determined and then planned.
- Costs are determined as based on functions.
As a result, the differentiation of above aids allocation of costs to costs places. General Motors Company practiced this system in their 50 of 193 factories and succeeded in decreasing overheads especially at high production factories.
Activity based costing has also been extended into activity-based management (ABM) to include other considerations, such as customer profitability, workforce utilization, distribution channels, and other management issues. Therefore, activity based costing is the system that shows the cost and profitability structure of products in a firm, whereas activity based management explains the actions to improve quality and reduce costs and production time. (Roztocki, 2000)
Conclusion
To sum up, we can see that activity based costing is not essentially a groundbreaking accounting concept; it just endeavors to look at the costing mechanisms from an entirely different perspective. Cost drivers which are determined in accordance with each organization certainly have their benefits which we have adequately determined in our paper, but the most important aspect of activity based costing which is sometimes overlooked is the readily ad-hoc system that comes as part and parcel of implementing an activity based costing system; the ability to change the entire system at any step of the way is certainly a benefit which cannot and preferably should not be ignored whilst one is conducting a cost/benefit analysis of the usage of an activity based costing system.
Bibliography
Reyhanoglu, Metin (2004) âActivity-Based Costing System Advantages and Disadvantagesâ Mustafa Kemal University-Faculty of Economics and Administrative Sciences, Turkey
Roztocki, Narcyz (2000) âImplementing an Integrated Activity-Based Costing and Economic Value Added System: A Case Studyâ State University of New York (SUNY) at New Paltz Department of Business Administration 75 South Manheim Boulevard New Paltz, NY
Hilton, Ronal W., Managerial Accounting, Second Edition, McGraw-Hill, Inc., New York, 1994.