Background and Objectives
Contact lenses are alternative to glasses as portable, lightweight lenses that correct the visual defects by being directly applied to the eye. Both the soft and rigid contact lenses are made from polymers. Contact lenses are global and used by many people, with over 125 million individuals wearing them worldwide. Their market value is significantly high and estimated to be above $7 billion with an increasing growth rate in sales. The figures show the growing popularity of these lenses, with the literature search indicating that since 2000, more than 100 patents have been filed (Musgrave & Fang, 2019). The lenses are applied in various functions leading to demands from the users for handling, durability, comfort, and wear length. They have been found effective in correcting myopia, and they are more preferred compared to glasses. With the increased numbers of people using the lenses, most potential users may turn to this industry for innovative products.
CooperVision has been involved in the production of contact lenses as an independent company. In 2016, the organization used about 37% of the revenue collected from sales and other support activities, which was equal to the amount other firms spend on consumer products (Musgrave & Fang, 2019). The significance of the institution as a lens maker is its bigger footprint in the supply of materials. They include a plastic polymer, where hard and soft lenses are made from different polymer material qualities.
However, as the public increasingly accepts contact lenses, a potential health risk concern has arisen among the users since they were introduced. The risk encompasses keratitis, which is an infection caused by wearing the lenses, which has the potential of causing corneal injury (MadridâCosta et al., 2018). Another danger is associated with dry eye syndrome. This, therefore, has called for improvements in the production process for the contact lenses. The increased contact lenses applications have also attracted manufacturers’ demands, including the need for ease production, material costs, and reliability. The emerging issues have affected both the quality and total quantity because of the defectiveness of these lenses and the packaging cartons. Thus, to minimize the arising challenges in the production of contact lenses and their demand, there has been the adoption of lean implementation and product flow optimization.
Lean implementation entails the process of maximizing the value of customers while keeping wastage at the lower level. Through the process, more value of the contact lenses is created for customers even when the resources are fewer. This is because much attention will be paid to understand the value of customers and the processes that can increase the same to eliminate the issues of defective quality of lenses and cartons (Musgrave & Fang, 2019). Similarly, the focus on product flow optimization allows the change in the way management operates to increase production. Optimization will entail meeting the demand of consumer products while creating a positive customer experience and competing on the market. With the optimization, the company reduces out of stock items, increases the turn rates fulfillment and carrying costs minimization, and ensures preserving margins. This is achieved when wastes are eliminated along the entire value streams and creating processes that require less space, human effort, and time.
Therefore, the current project involves applying the lean implementation and product flow optimization in the manufacturing of contact lenses to minimize the defectiveness during and after production and when packaging by focusing on the value and reducing wastage. The implementation of product flow optimization will take special test requests where the new products and the components will be validated following the introduction of the new production lines. In the case of the new supplier, the monomer supply will be assessed to ensure that the material is fit to be used in production. A similar assessment and test of the shipped monomer will be conducted in the on-site Chemistry Lab so that to have the assurance that the packaged and shipped material meets the procedural requirements. The project shall also involve another optimization process, such as identifying matter and sizing of the material, testing of water content, testing refractive index, ultraviolet light testing, and decanoic acid testing.
Project Objectives
The focus of the project is to minimize the chances of shipping defect contact lenses and cartons and ensure that they are of the right quality and the total quantity as per the expectation of the ordering agency. Therefore, this project focuses on achieving the following objectives:
- To ensure lean implementation and optimize the flow of product in the production process for contact lenses
- To prevent the packaging of the defective contact lenses and cartons for the clients through the investigation by the in-process hold
- To put in place enhanced and appropriate control measures and ensure that they conform to the quality and quantity checks as expected.
- To prevent any potential future recalling of the packaged and shipped cartons of the contact lenses to the client since this interferes with the company’s reputation.
Method
The DMAIC problem-solving methodology will be used to ensure the conformance of controls to the quality and quantity packaging. The process will involve investigating the sample amount of the contact lenses and the cartons packaged alongside shipment orders. Every parcel comes alongside a sampled amount, checked against the required features that define the good products based on the quality and the quantity levels.
The investigation will entail checking the defective contact lenses and cartons. The process will be referred to as in-process hold, which includes all the activities from the time the order is made for the lenses to be supplied until they are ready for collection by the ordering agency. The qualification for shipment will involve a batch of cartons containing lenses with not more than 11 defects. This means that if the sample of cartons has less than 11 defective items, then they will be allowed for shipment. However, if the batch has cartons of contact lenses that show more than 11 or at least 12 defects, they will be rejected and sent back for reworking.
On the other hand, when the batch is accepted for shipment, there must be the issuance of the certificate of conformance, which meets the criteria for the control measures that have been set in place. The rejection of the batch, on the other hand, attracts the requirement that the supply issues a new certificate of conformance showing that the batch that was found defective has been segregated and is awaiting reworking and releasing for shipment once again.
An example of this project procedure can be that if a batch of a carton of contact lenses is checked, and for instance, 15 cartons are found to be defective, it means that they will be rejected and sent for segregation. The supplier is under obligation to rework the returned lenses before releasing them again. This will, however, mean that the old certificate of conformance is irrelevant, and another certificate is required.
For lean implementation, the process will involve conducting various tests that will ensure that the monomer meets the requirements as set out in the procedural process. The initial step will involve assessing all new monomer suppliers to confirm that the material has been used in the production. The consideration of the type of material used determines the category of the contact lenses being shipped and the conformance.
After assessing the supplier, the next step will involve testing the monomer to ascertain the material quality and establish if it meets the standard expectations. The testing will be conducted in the on-site chemistry lab. The lab has the standardized tools which establish if indeed the material is the actual one used. The testing is followed by identifying any foreign matter in the material for the right quality. The next process will be sizing the material to the required standard level. More tests will be conducted to ensure that defective content lenses are detected and returned to the supplier for segregation. The Gantt chart in the appendix shows the flow of events for the project and the timeline used.
Student Contribution
The student will contribute to the project through research and providing knowledge about the content lenses and the impacts of lean implementation and product flow optimization. The production of content lenses has been examined widely in various studies because of its significant benefits. Students will investigate the conclusion about production, companies that are involved, and the materials used. This information will be critical in ascertaining procedures to enhance production to meet the quality and quantity standard in the project. It will also be critical in preventing the shipping of defective lenses and cartons by ensuring the right materials have been used.
References
MadridâCosta, D., GarcĂaâLĂĄzaro, S., AlbarrĂĄnâDiego, C., FerrerâBlasco, T., & MontĂŠsâMicĂł, R. (2018). Visual performance of two simultaneous vision multifocal contact lenses. Ophthalmic and Physiological Optics, 33(1), 51-56.
Musgrave, C. S. A., & Fang, F. (2019). Contact lens materials: A materials science perspective. Materials, 12(2), 261.
Appendix
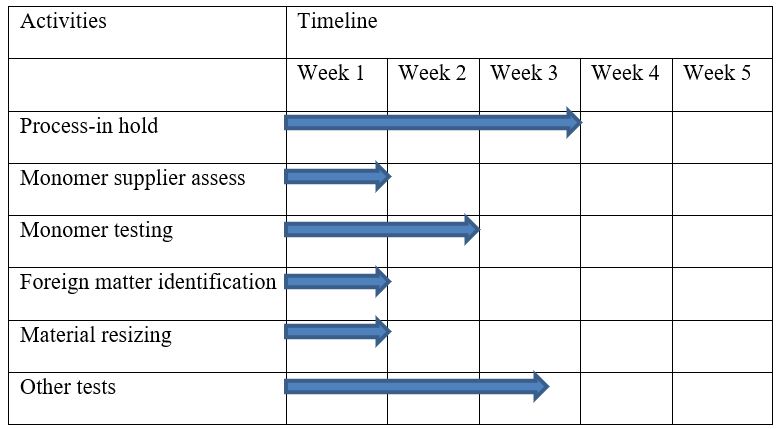