Introduction
As technology has continued to change and improve over time, so to do the operational processes of corporations change along with it. In the case of inventory management, companies are no longer limited to processes involving log books, line of sight, and written labels to categorize and store products. Instead, new processes have entered into the field of inventory management as a direct result of influences from information technology.
Such processes have enabled companies to immediately know how much of a product they have, where in the factory it is and what would be the best process to retrieve it and deliver it to their customers.
It is based on these improvements that this paper will examine aspects related to RFID tag usage, information systems, as well as other applications of information technology in modern-day inventory management processes. It is expected that through this paper, a greater understanding can be developed on how information technology has helped to enhance current inventory management processes.
RFID Tag Technology and Inventory Management
An RFID (Radio-frequency identification) chip can be considered an ingenious device due to its overall simplicity yet wide applicability in a variety of fields and applications. The chip, no bigger than a grain of rice, works via a system of query and transmission wherein the chip releases a coded identification number when it is queried by a reader device that produces the necessary type of signal (Ben-Daya, Hassini, Hariga & AlDurgam 2013, pp. 1347-1365).
The result is a method of package tracking and identification which enables companies, medical institutions, and even government agencies to immediately identify and track a particular object or person based on the RFID signal transmitted by an embedded. Companies such as Amazon, Wal-Mart, and Costco have been utilizing RFID technology as a means of tracking their products in their various warehouses and department stores.
From corporations, the use of tracking “chips” is a positive facilitator of customer care since not only can warehouse managers respond quickly and efficiently to product requests but they can avoid utilizing particular procedures or methods of product retrieval that are laborious or time-consuming.
Aside from their use in warehouses and factories, RFID chips have been utilized extensively in the package transportation industry via installed electronic sensors on in warehouse systems (Ben-Daya, Hassini, Hariga & AlDurgam 2013, pp. 1347-1365). Such devices are commonly seen on vans that deliver packages through highways and various areas and deposit their products in the store requesting them.
These systems allow companies to identify the transmitted code attached to the driver’s RFID systems and automatically allow them to pass through security gates while at the same time creating a “mark” within their systems indicating the arrival of the truck. This system is often utilized by FedEx, DHL, and UPS to tracking transports and packages across long distances to inform customers where their packages are and their estimated date of arrival.
Other more subtle methods of RFID technology use has been their implementation in-store tracking systems and large scale agricultural operations. The technology in effect has made it easier to easily track both equipment and goods as they are transported from one location to another, thus facilitating easy identification leading to access to particular ports of entry.
Application in Company Information Systems for Inventory Management
Information systems can be described as the interface between people, organizations, and technology, enabling the business to accomplish a specific task or action. One example of an information system are the various applications and websites utilized by Amazon in selling products, accepting client payments through credit card processing applications, contacting their warehouses and shipping bought products to the correct addresses indicated by their consumers (Lödding & Lohmann 2012, pp. 909-919).
This sort of system is integral in Amazon’s inventory management process since it enables the company to determine how much of a particular stock has at any one time, where it is located among Amazon’s assortment of warehouses and what processes can be implemented to get the product from the warehouse and to the customer.
While this is only one example of the plethora of information systems that have been integrated into inventory management processes out there, what must be understood is that information systems act as methods of integration for a company helping to streamline specific processes so that they can be controlled, influenced and improved when necessary (Lödding & Lohmann 2012, pp. 909-919).
This is evident in the case of inventory management since it has revolutionized how the process helps companies to track packages across multiple locations that would have otherwise been impossible or time-consuming if they had relied on the use of company log books.
In essence, the use of information systems in inventory management has revolutionized the process to such an extent that companies can use bigger and bigger warehouses in order to store a variety of products since information systems now allow them to track them more efficiently and effectively which reduces the necessary effort in having to go through upon row of products manually in order to find the product that a client ordered.
Developing proper information systems is an essential aspect for a company for without it a company will be unable to properly deal with the buying, selling, and the utilization of resources across various locations in the country.
Due to the varied and often complicated nature of company operations, it becomes a necessity to streamline and integrate product delivery processes, methods of operation, customer service and various other operational capacities (Lödding & Lohmann 2012, pp. 909-919). It is based on this that it can be seen how important and integrated information systems are in present-day inventory management.
Combination of RFID and Information Systems in Inventory Management
Through the use of embedded RFID chips within shipping containers, IDs and even vehicles companies have in effect integrated RFID technology into their information systems thus resulting in far more efficient methods of tracking, sorting and granting access to appropriate individuals for the use of particular facilities.
This establishes a distinct precedent and shows that RFID chips can be utilized and integrated within already present information systems and, as such, can be implemented with little, if any difficulty, should the technology be modified in order to conform to already present processes (Fernandes, Gouveia & Pinho 2013, pp. 2578-2592). During the inventory management process, RFID chips have helped to enhance the process of product tracking since it enables companies to track a product from start to finish.
This refers to the process wherein when a product arrives a sticker with an RFID chip is placed on it to facilitate tracking within the warehouse, during the transport out of warehouse and to confirm delivery to its intended destination. The result is a system of inventory management that is superior to what was present 20 years ago when the technology simply was not present, and corporations had to rely on archaic processes related to the use of physical ledgers and computer records that lacked any means of significant customization.
Inventory Tracking and Theft Prevention within Stores
Fernandes, Gouveia & Pinho (2013) indicates that research and development into new ways of producing and utilizing technology is one of the practices most often seen in technology intensive enterprises. This is because technology has as of late been under a constantly accelerating level development and as a result, has enabled new players to enter into markets whereas in the past distinct barriers to proper entry would have been present (Fernandes, Gouveia & Pinho 2013, pp. 2578-2592).
As such, failure to sufficiently innovate along with new technological trends and products can be thought of as a failure on the part of the managerial practices at a company since being able to anticipate trends and use them to either reach greater inventory tracking efficiency or keep the company relevant to consumers is a necessity in today’s technology intensive market economy.
In this regard, authors such as ( ) state that corporations are the vanguards of such a practice due to their ability to utilize already existing technology in ways that were not originally perceived by the inventors but have in effect spawned very successful niche markets. One of the more interesting cases where this was utilized was explained by the case study of Gagliardi, Renaud & Ruiz (2012) which focused on an examination of how RFID technology was popularized as a way in which to track items within a store to prevent their theft.
As Gagliardi, Renaud & Ruiz (2012) explain, the companies, who implemented this type of innovative procedure sought to fulfill a market niche within the retail industry involving lost or stolen clothes, gadgets, etc. Since an RFID chip can be embedded within the packaging of an item with no ill effects, embedded chips placed on certain strategic locations on certain products enabled them to be easily identified and tracked utilizing the sensors available within the store.
Such a process has helped corporations within one of the most annoying problems they have to deal with in inventory management daily, namely product theft. By placing scanners within a store or storage facility and ensuring that only once a product with an RFID chip has been confirmed by the system as being allowed to be taken out of a certain area, can that item be removed (Gagliardi, Renaud & Ruiz 2012, pp. 879-892).
If it is removed from a particular location (i.e., outside of a store) without the RFID tag either being removed or being confirmed at the store’s counter, alarms within the store will immediately go off indicating that a theft has just occurred. Through this process of inventory management, loses equaling several billion dollars a year in lost revenue have been mitigated. This shows how the use of I.T. within the context of inventory management is not isolated merely to warehouses and delivery trucks; rather, it can also be incorporated into retail locations as well.
Other uses of I.T. in inventory management within stores has taken the form of the development of small scale RFID trackers which can be utilized to track objects within a small area. Since an embedded RFID chip can be read and located via a reader within a 10-meter radius (provided that there are no blockers surrounding the chip) this, as a result, enables the immediate detection of a particular item. This has become a popular method for stores to track the location of their inventory.
Similar types of products are also available to the general public via small scale RFID devices that can be placed within certain items such as a laptop, iPod case, and a variety of other types of electronics. This is more along the lines of a small scale version of inventory management meant for either home use or small businesses.
Analysis of RFID Chips and General Usability in Inventory Management
This section details how RFID chips function within the context of inventory management, the justification for usage in current product inventory systems, its interaction with the readers, and the inherent limitations of the technology.
RFID Chip -Functionality and Process
Construction
RFID chips, given their size, has two main components: its integrated circuit which is used for storing and processing information (i.e., the RF signal that is being broadcasted by the readers) and the antenna that is used for receiving and transmitting signals to and from the reader. Combined, these two parts act as how the chip can function without the use of other extensive components.
How information on the chip is queried
Information on an RFID chip is queried via an RFID reader sending an encoded signal to the chip. Once the RFID chip receives the query from the reader, it responds to the signal with its identification number, tag designation, etc. and other relevant information that is on the chip. Do note that with present-day technology, the total amount of information that can be stored on the chip is limited to 128 bits (Niranjan, Wagner & Nguyen 2012, pp. 939-951).
As such, this limits the capabilities of the tracking system to add more extensive identifying information onto the chip. Thus, the only means of tracking within the system itself is via a set of serial numbers which are then associated with the product’s file and item history.
Benefit in Usage for Inventory Systems
The benefit of using this particular type of technology in present-day inventory management processes is that ceiling mounted readers that are utilized in a variety of warehouse, such as those used by Amazon.com, can immediately find the exact location of a product, utilize either an automated crane or a service team to retrieve it from its location and track the progress of the delivery from the warehouse to the customer.
Such a system creates a far better level of process control and identification resulting in better storage and record-keeping processes (Niranjan, Wagner & Nguyen 2012, pp. 939-951).
Placing the serial number on the tag
There are actually two methods by which the RFID chip can acquire its serial number which is then assigned to the database The first method is that assigned serial number transmitted by the tag can be assigned within the factory that created it or the tag can have read/write capabilities wherein specific data within the chip itself can be included via a special encoder.
For this project, the latter method has been chosen due to the possible problems that may occur should an error occur in the factor, and repetitive serial numbers are used in the tag. By having the numbers assigned within a warehouse itself, this adds an extra level of security in ensuring that there will not be issues of mistaken identity when tracking the movements of a particular product (Niranjan, Wagner & Nguyen 2012, pp. 939-951).
Benefit in Usage for Inventory Management Systems
The benefit of this particular technology in inventory management systems is that it enables immediate identification regarding what type of product is inside a container without having to undergo the process of having to physically look inside the container or having to write labels on the side.
This makes the process of determining what is currently in a warehouse that much easier resulting in packages that are immediately identified and delivered to clients within a far shorter period (Niranjan, Wagner & Nguyen 2012, pp. 939-951)e. Not only that, by being able to easily determine the identity of a product without having to open particular containers, this ensures that the contents remain undisturbed and are not subject to the various problems that are associated with leaving products out in the open.
Limitations of the RFID Chip
As with all processes, even the RFID tracking system has limitations. The limitations of the RFID inventory management system will be detailed in this section and will showcase how its use in the system does come with a few vulnerabilities.
Lack of direct access
One of the main problems with utilizing the tracking chip system as compared to external tracking methods (i.e., box labels) is the fact that there is no direct physical access between the chip and those monitoring it. This means that if the chip malfunctions the ability of the system to track the product would cease. To get it back up and running again, it would be necessary to physically remove the old RFID chip and place in a new one which could cause problems with product tampering.
Taking this into consideration, the lack of direct access and the inability for the chip to be replaced is a serious flaw in the system that needs to be taken into consideration during inventory management processes. One way of preventing future problems would be to place multiple chips into other areas of the package, which is often utilized by warehouses to mitigate such a problem.
Lack of sufficient range
Another issue that needs to be taken into consideration is the lack of sufficient range on RFID chips. Given its limited transmission capability, the RFID chip is only capable of transmitting up to a maximum of 5 meters which severely limits the capacity of the system to effectively track packages after a certain distance between them, and the tracker has been reached.
Do note though that this is not an inherent limit of the RFID tracking system in general, rather an issue is primarily due to the passive nature of RFID chips that are normally selected by warehouses as the primary tracking component of their inventory management systems since they are affordable and disposable.
Active RFID tags with their independent power source (i.e., an internal battery, circuit, etc.) are capable of interacting with readers at a much great distance with active RFID tags that can be tracked up to 100 meters or more. Unfortunately, passive systems are utilized in the case of this project given the need to insert the tracking mechanism directly into packages thereby preventing malicious individuals from removing the chips without causing significant physical harm by literally cutting open the package to get to it.
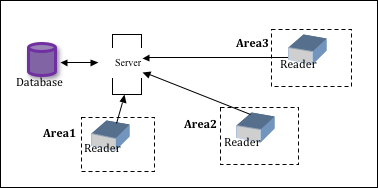
As seen in the diagram provided, the design of the system is pretty straightforward. Once an object approaches the range of the reader, their RFID chip is scanned and is unique identifying marker is searched for within the system. Once the system matches the identifying market on the chip with the one in the system, the movement of that package is logged within the server and then placed into a map grid that is unique to that particular product.
When queried regarding the movement of a particular product, two windows will appear: one will show the log history of the product’s movements while the other will show a virtual representation of the movement of the product based on its logged movement within the warehouse.
Through this system, every area that a product goes to, its movement patterns and other information related to its location within the general facility can be tracked. This information is invaluable in present-day inventory management processes since it allows the company to know where a product is at all times and allows them to determine how best to store or take it out of storage for delivery.
I am tracking Products in Present Day Inventory Management Systems using I.T.
Tracking utilizing the present-day item management systems occurs through a “logging” mechanism instead of in real-time. The inherent issue with real-time tracking is that it would require a far larger tracker than the RFID chips current in use since the components would need to be more complex. The various micro trackers that are often seen in movies, cartoons, and television shows are fictitious given that an effective real-time tracking mechanism would need to be able to emit a far stronger signal.
Such devices, while available, are often half the size of a standard mobile phone and inserting them into packages would, of course, be difficult. It is based on this that each time a package passes by a scanner within a corridor, its location is immediately logged into the system which will have to indicate the precise time, location and date of movement.
Such a means of tracking can be considered appropriate within the context of package tracking since it creates an item history log through an inventory management program that tracks locations and how long certain items have been placed in particular locations.
This particular type of system has been utilized extensively within various super stores such as Wal-Mart, Costco, and other supermarket chains to determine when products have been placed on shelves and when they are likely to expire. This helps them to manage their inventory in such a way that products that are nearing their expiry date are removed before they are sold to consumers.
Use of Information Systems in Inventory Management
A company cannot just simply develop and market a product without taking into consideration how best to allocate specific resources in determining where a product needs to go, which branch needs it most, and how will a product be processed. A company requires an efficient and up-to-date information system to integrate the factors mentioned into an efficient and effective operational strategy to better serve its clients and reduce the inherent costs of operation.
What must be understood is that the larger a company gets, the more hectic and haphazard it’s inventory management operations tend to become, especially in instances where its operations are located in different countries. Organizations need to understand how to properly allocate resources to specific international locations, how suppliers can be contacted, what are the limits of delivery daily and how will each branch know where to send a product and when.
In other words, information systems can be classified as solutions to identified problems or necessary methods of integration within the context of a company’s inventory management needs. What must be understood is that while managers and CEOs are great at coming up with specific solutions to problems they are lost when it comes to implementing these particular solutions when they require computer programming as one of the factors behind the implementation.
Information systems and information system specialists bridge this gap by being able to integrate the ideas of managers and CEOs into viable inventory management applications that can be implemented on a company-wide basis.
For example, if a company is currently having problems with its archaic method of form-based ordering in order to get products from the warehouse to consumers, a manager or CEO would think to implement a faster and better means of getting orders to warehouses without having to rely on someone physically going there and handing them the orders. They would, of course, think to apply a computer-based system for this particular solution, and this is where information systems come in.
An information system in this particular situation becomes an applied solution where it is developed to help a company resolve a particular problem. On the other hand, if the company was to expand and have a more diverse array of products and factories further development of the initial information systems becomes necessary to adapt to the growing needs of the company.
It is based on this that it can be seen that information systems act as a necessary method of process integration for inventory management which enables a company to do its job better and as such it is essential to have it within a company.
Digital Distribution Systems and Inventory Management
One of the latest trends in inventory management has been the use of new methods of online digital distribution. Sites such as Amazon.com and the Apple App store readily allow publishers to distribute their content through their systems, which allows access to the millions of online subscribers within their database.
Since digitized content can be endlessly replicated, this allows companies to reduce the costs inherent in inventory management while at the same time gives them greater access to a potentially huge market for their products.
Another alternative would be for companies to develop their digital means of subscription distribution thus enabling it to be far more independent in terms of its ability to distribute the type of content the companies want to publish without having to follow the strict guidelines of distributors such as Amazon.com or Apple Inc. Digital distribution of created content can be considered the “new frontier” so to speak of inventory management since it enables companies to replicate inventory on a massive scale while at the same time gives it the ability to instantly sell products to consumers.
Conclusion
The use of I.T. systems in present-day inventory management can be described as the implementation of digital processes and technologies in order to increase the efficiency, reliability, and coverage of internal and external package tracking services and security, while at the same time implementing a concept known as “lean operations” wherein wasteful spending, processes and methods of operation are in effect eliminated as a direct result of utilizing digitized procedures and systems to remove the “human component” which is usually the largest cost in maintaining an efficient and effective warehouse facility.
Basically, the use of automated inventory management systems is a means of making the process of storage and delivery more secure and efficient by creating a means by which packages are monitored at all times which creates a far better means of ensuring that none of them are ever stolen or misplaced (which does happen in warehouses where such a system is not in place). Thus, by utilizing the RFID chips and information systems in modern-day warehouses and factories, it creates the following positive effects:
- Greater citizen satisfaction in the way in which services are provisioned (i.e., getting packages and products to them in a faster and more expedient fashion).
- Fewer stockholder complaints regarding the inefficiency of services (i.e., through the lower cost of package storage and fewer instances of lost merchandise).
- Better connectivity technology and inventory management operations which result in better efficiency and effectiveness.
- Lastly, fewer resources wasted on inefficient processes and procedural “red tape.”
Overall, this paper has shown that I.T. is an essential aspect of modern-day inventory management systems and, as such, it is more than likely that it will continue to be utilized to improvement company operations well into the future.
Reference List
Ben-Daya, M, Hassini, E, Hariga, M, & AlDurgam, M 2013, ‘Consignment and vendor managed inventory in single-vendor multiple buyers supply chains’, International Journal Of Production Research, 51, 5, pp. 1347-1365.
Fernandes, R, Gouveia, B, & Pinho, C 2013, ‘Integrated inventory valuation in multi- echelon production/distribution systems’, International Journal Of Production Research, 51, 9, pp. 2578-2592.
Gagliardi, J, Renaud, J, & Ruiz, A 2012, ‘On storage assignment policies for unit-load automated storage and retrieval systems’, International Journal Of Production  Research, 50, 3, pp. 879-892.
Lödding, H, & Lohmann, S 2012, ‘INCAP – applying short-term flexibility to control inventories’, International Journal Of Production Research, 50, 3, pp. 909-919.
Niranjan, T, Wagner, S, & Nguyen, S 2012, ‘Prerequisites to vendor-managed inventory’, International Journal Of Production Research, 50, 4, pp. 939-951.