Introduction
In this context, the focus will be on Nestle, Bangladesh. This firm’s operations involve multiple stages and inevitably areas where value is made or lost. This report will provide a value stream map (VSM) detailing the procedures and steps in delivering the Nestle product to the Bangladesh market. The firm operates within the food industry when such items as time and standardization of product quality make a huge difference in customer satisfaction (Navaneetha et al., 2017). Through the VSM, Nestle Bangladesh can identify the opportunities to eliminate waste, accentuate customer focus, and lower logistics costs.
Value Stream Map
As shown in Figure 1, Nestle’s VSM is displayed. The firm’s core processes are shown with orange lines. These are the stages and direction flow of processes as overseen by the production supervisor on blowing bottles, filling, quality assurance, and labeling and packing. These aspects are critical and must be completed without error each day. This makes the decision-maker—the production supervisor—a crucial part of the entire process. The supervisor is responsible for value creation or loss (Islam, 2017). The VSM shows that the production control is responsible for the management of orders per week. Through it, the determination of the weekly order is made so that the production supervisor can determine how to manage the following operations blowing bottles, filling, quality assurance, and labeling and packing.
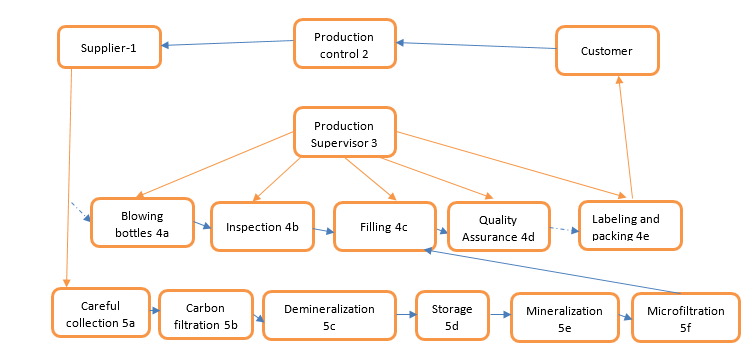
Value and Non-Value Items
The item of value worth considering in the VSM is time. As shown, most of the production at the firm is done weekly. Managing time is critical to the success of the whole process (Romero & Arce, 2017). There are areas in the entire process where time management can lead to time efficiency. These are the six activities at the bottom of the figure: collection, carbon filtration, demineralization, storage, mineralization, and microfiltration.
Since these activities are not directly linked to the production supervisor, other people are put in charge. If these people do not share the same conviction and timeliness as the production supervisor, the whole process could face challenges. Additionally, if the people in charge of these processes are suddenly changed, there is a high likelihood of errors or mishaps occurring (Meudt et al., 2017). Clearly, the biggest weakness of the VSM at Nestle concerning time management is the overdependence on the production supervisor.
A non-value item (waste) in this VSM is the inspection stage. This stage between blowing bottles and filling can be combined with the quality assurance stage. It is because the activities of inspection are similar to those of quality assurance. Due to this reason, it is recommendable to combine the two to avoid wasting time and resources in doing two similar activities (Valmohammadi & Dadashnejad, 2021). The best way forward would be to combine inspection with quality assurance. This means that the map would exist without inspection. The production supervisor would conduct inspection and quality assurance activities to save time to prevent time wastage.
Customer Focus and Costs Management
The importance of being customer-focused in the VSM used in this case is that it helps the firm to deliver quality products to the market on time and in standard quality (Bulcke, 2018). With these two aspects as the main goals, the firm’s value is created and maintained through automation to ensure that standard quality is achieved in all products and used efficiently (Romero & Arce, 2017). The use of minimal authorities in the process is also key to the fast decision-making achieved in the firm.
Managers’ Elimination of Waste
As mentioned previously, the most significant waste in the process is the use of additional resources and time on inspection when it could be done during quality assurance. A possible solution to this challenge would be to hire an assistant production supervisor. The assistant would be in charge of the six steps that the supervisor does not tackle directly, plus the help out during quality assurance.
This arrangement would extend the same centrality of authority and control exercised by the production supervisor on the four core steps (Valmohammadi & Dadashnejad, 2021; Galli & Vousvouras, 2020). These steps will help in ensuring that the firm eliminates waste. This approach can be used in other firms as well. When it is found that some activities can be combined to lower the time taken, it is critical to add more workers. Doing so ensures that the firm will not overwork some workers. Additionally, it means that the firm will be able to maintain the motivation of the workers high as well.
Conclusion
In conclusion, this paper has analyzed the VSM as applied at Nestle Bangladesh. It has been shown that the firm’s orders are handled weekly. However, these activities are primarily dependent on the skills of the production supervisor. This overdependence is likely to lead to challenges. It is challenging to eliminate wastage of time if the dependence remains. Hiring an additional worker to act as an assistant would help stop wastage of time as identified. This principle can be adopted in different organizations to prevent overworking some workers while maintaining the integrity of the production method.
References
Bulcke, P. (2018). Nestlé and its response to megatrends in water. In Assessing global water megatrends (pp. 231-244). Springer.
Galli, C. C., & Vousvouras, C. (2020). Nestlé caring for water. International Journal of Water Resources Development, 36(6), 1093-1104.
Islam, M. (2017). Critical evaluation of the supply chain of Nestlé Bangladesh Limited. Routledge.
Meudt, T., Metternich, J., & Abele, E. (2017). Value stream mapping 4.0: Holistic examination of the value stream and information logistics in production. CIRP Annals, 66(1), 413-416.
Navaneetha, B. N., Punitha, K. P., Joseph, R. M., Rashmi, S. R., & Aishwariyaa, T. S. (2017). An analysis of cost volume profit of Nestlé limited. Management and Administrative Sciences Review, 6(2), 99-103.
Romero, L. F., & Arce, A. (2017). Applying value stream mapping in manufacturing: A systematic literature review. IFAC-PapersOnLine, 50(1), 1075-1086.
Valmohammadi, C., & Dadashnejad, A. A. (2021). Value stream mapping implementation: An operational view. International Journal of Productivity and Quality Management, 32(3), 307-326.