This report documents my team’s project on global supply chain management and value network analysis for Samsung group of companies, an international conglomerate in electronic consumer goods, shipbuilding, textiles and insurance. The company is ranked among top 20 companies worldwide, employing over 200,000 people across 65 countries (Samsung, 2011).
This report will particularly focus on how in-house SCM solutions have transformed Samsung from a small-sized company of yesteryears to the huge multi-national firm of today, all in the span of two decades. Some of the issues to be discussed include advanced process design, scheduling and metrics such as Six Sigma which have ensured permanent benefits in various stages of the business. In analyzing these issues, I will highlight major advantages and disadvantages of Samsung’s management strategy while observing limitations of methods.
Finally, the report also takes a look into future prospects of the Samsung Group in a global arena and based on my own project work, offer recommendations on how goal-based improvements can be made in future. To do it, I will highlight a description of intended objectives and the targets that can be reached using methods like Balances scorecard. The implementation should have an impact on parameters like lead time, customer service level, cycle time and labor expenses. The implementation plan would be depicted by a Gantt chart.
Methods of Research: To get best results for Samsung’s existing project, I did my internship at ______ in ________. I was in close touch with the Regional Warehouse Manager who has been managing supply chain activities for key parts such as semiconductors, LCDs and mobile chips, all of which go to service electronic consumer goods. The Samsung group of companies have a gigantic, vertically designed structure where each business division is responsible for its own targets and objectives, similar to the Toyota model of manufacturing. The advantages of a vertically designed structure include lower procurement costs, enhanced design speed, development, design and production with the components business being able to serve the end products in a much better way (Chang, 2011, p.71; Chang, Makatsoris and Richards, 2004, p.133).
My warehouse manager has made extensive contact with several external collaborators from whom he buys components which enable him to ensure appropriate service value networks across the factory chain. He has included his own process innovations such as customer-driven lean production at each stage of the components’ development. Using lean methods in a service environment enables organizations to reduce waste, achieve faster turnaround and improve the value chain over a period of time (George, 2003, p.81; Macintyre, Parry and Angelis, 2011, p.60).
Gap analysis: Despite the current lean methods available at the warehouse, the following areas of improvement are visible in plain sight. I gathered these observations through surveying research subjects (factory employees) and the warehouse manager on how best they thought improvements could be made over a long period of time. They came with the following areas of constraint:
- Material costs which have been experiencing a huge growth over the past two years. This is a parameter on which they had little control since Samsung’s global supply chain ensures that the best materials are imported from other countries, particularly China and Taiwan.
- The other parameter of concern was the slower paced roll-out time of new products based on design inputs. The management felt that design processes have to be automated to a certain extent. That may save on time but would lead to gradual elimination of skilled local workforce which would prove an unpopular move, not withstanding the fact that some of these people have been instrumental in guaranteeing the high quality of Samsung’s innovative products. A trade-of between the two situations had tobe pursued.
Analysis of existing learning lessons: To discuss the roadmap of my own suggested methods, it is important to understand the present delivery methods of production at the factory. As discussed earlier, the integration of Six Sigma with lean methods of production was the dominant vision for Samsung’s factory, affecting several processes from design stage to final production. Key advantages of the Six Sigma methodology include high level of product discrimination and differentiation, business competitiveness and very low margin of error, around 1 in 1 million (Creveling, Slutsky and Antis, 2003, p.6; Akpolat, 2004, p.136).
The Samsung factory where I did my research has a Design for Six Sigma (DFSS) program which aligns the company’s technology development and product design processes with DFSS tools and best practices. Statistical tools like ANOVA, fishbone diagram, T-tests and other disciplinary tools are extensively being used to get desired results. The processes have been optimized to manage flow for an entire category of work, reducing business cycle time and enabling monitoring of performance through score cards. Tangible benefits include delivering technological platforms, world-class capabilities and managing risks through waste reduction.
The core of Six Sigma is the DMAIC process, standing for Design, Measure, Analyze, Improve and Control. Each stage of the DMAIC methodology ensures one is able to use the right tools at the right time to get best results (Creveling, Slutsky, and Antis, 2003, p.18; Akpolat, 2004, p.78). The Samsung factory has an entire team dedicated to the implementation of Six Sigma methodology to achieve best results.
Apart from Six Sigma, the factory has adopted some of the best techniques in lean manufacturing, thus, the overall work planning assumes a Lean Six Sigma character. The advantage of lean thinking at the factory include a customer-centric focus, reduced wastage and high relevance for design and service deliver teams (George, M., 2003, p.34; Wedgewood and Wedgewood, 2007, p.76; Taghizadegan, 2006, p.78). This incorporates steady changes in scheduling systems, packaging, quality inspection and other important processes documenting detailed activities at the Samsung plant. In my stint there, I observed that most Samsung employees are very methodical in their theoretical pursuit of Six Sigma methods, taking it down to the T’s but many have not been trained well in the actual implementation of Six Sigma, as applying to the final destination which always leads to huge interdependence, thus, wasting of time. To ensure top line quality and bottomline improvement, some drastic measures have to be taken, especially at a training stage where most design lapses are common.
For the purpose of our project, I have outlined the following problems which have to be addressed through some improvement methodology in SCM. These include waste reduction where I would be covering topics like reducing wait time between two consecutive production batches, inventory management, buying supplier needs, and overhauling quality for excellent results. Another goal to be addressed is minimizing purchase cost of components by simple strategic alignment of inventory with better feasibility studies of customer demand for Samsung products, especially for the factory under study. Once the batch units have been properly analyzed, further course of action can be taken.
Implementation plan: To design a well thought-out implementation plan at the Samsung factory, I knew that it was essential to consult the warehouse manager, my project incharge at the factory. He gave me guidelines on what used to work in the past, and how may customized improvements be incorporated into Samsung factory’s design processes. Some of the solutions include smoothening the work flow, shrinking product life cycle, improve customer service levels, increase outsourcing efforts. In order to gain optimum benefit, the following approaches were considered by me.
The system approach
This approach means “the evaluation of an organization’s effectiveness by its ability to acquire inputs, process the inputs, channel the outputs and maintain stability and balance” (Robbins and Barnwell, 2006, p. 191). What we basically want here is an alignment of the organization’s key dimensions with its strategic and financial targets (Robbins and Barnwell, 2006, p.191).
Some key dimensions in Samsung’s structure are identified as following; a multitude of autonomous departments, the rubric like centralisation which allows top management to control the reins of power and the company’s knowledge domain expertise in various IT technologies such as SAP, Oracle, Internet applications and more. These strategic targets have been identified for incorporation into a long-term Six Sigma improvement process.
Clearly, if one has to compare Samsung’s growth over the past two years, the systems approach would yield a net positive result
The strategic constituencies approach
Robbins and Barnwell (2006) suggest that “an organization’s effectiveness is determined by how successfully it satisfies the demands of those constituencies in its environment from which it requires support for its continued existence” (Robbins and Barnwell, 2006, p. 85). As has been already covered in other sections, the various strategic constituencies of this company are currently aligned to its larger business goals, shaping its market focus and helping it achieve a clearer strategic direction for future times ahead.
The balanced scorecard approach
Robbins and Barnwell (2006) state that the balanced scorecard approach “seeks to balance the various demands on the organization with its capabilities” (Robbins and Barnwell, 2006, p. 85). It’s a design methodology which takes into account the areas of finance, customer, internal employees and learning/growth values to achieve the optimum result from all parameters (Robbins and Barnwell, 2006, p. 210).
As far as Samsung is concerned, the most pressing demands in its present functioning come from its various constituencies that are currently bottlenecked by bureaucratic elements and need to be brought under control. Out of the four mentioned design parameters, Samsung scores a little less in the internal employee count. This needs to be corrected if the factory has to achieve a perfect balanced score card value.
As covered in this paper, the present organizational structure in the Samsung factory led to the following problems:
- Too much vertical differentiation at times which led to a) isolation of top management from important human resources and international financial markets b) Shortage of skilled workforce for further development of organizational business c) Problem in accessing better supply vendors.
- Growing spatial dispersion due to increased geographical growth. The organization has done little to cope with challenges of the future.
- Too much interference from finance department in the everyday affairs of a few departments such as quality control, inventory and supply deparment.
Presently, there is a need to remove above bottlenecks by making the structure more resilient to future problems. Accordingly, I was able to identify the following solutions.
- Reducing the vertical differentiation gap between top management and key project executioners.
- Appointing skilled personnel in key markets to align the organization’s business goals with the demands of the constituencies.
- Changing the reporting structure to ensure the departments of quality control, inventory and supply deparment get considerable autonomy from the CFO.
Description of proposed future state: As been covered in the previous sections, Samsung has a Lean Six Sigma organizational structure to deal with its current and future business growth demands. The same will be explained using Mintzberg’s typological theory which makes communication processes much simpler in the overall organization(Minstzberg, 1981, p.81).
Robbins and Barnwell indicate in their book Organization Theory that Mintzberg mentions five essential elements to any organization (Robbins and Barnwell, 2006, p. 120) which are:
- Operation core: the core operations of the organization
- Strategic apex: the main management top of the organization
- Middle line: the team of executioners at the helm of project undertakings
- The technostructure:
- Supporting staff
Consequently, there are five coordinating mechanisms that apply here: direct supervision, standardization of work processes, outputs, skills and mutual adjustments (Robbins and Barnwell, 2006, p. 120). Mintzberg asserts that various parts of the organization, empowered by specific coordination mechanisms, exert certain “pressures” or “pulls” on these mechanisms (Mintzberg, 1981, p.81). Eventually, Mintzberg tries to prove that a degree of decentralization is related to increased vertical communication which will build the strategy and environment of the organization. As a holistic concept, Mintzberg’s theory speeds up decision-making activities without compromising on formalized rules within the organization.
Samsung, due to its Lean Six Sigma structure, has a formalized set of rules which qualify it to fall under Mintzberg’s theory based on the roles of various departments. The relationship between top management and various departments, especially finance, legal and quality assurance, are based on how much “push” or “pull” can be influenced through a routine activity. However, since, the departments themselves are fairly independent from each other’s interference, there has to be little or no adjustment done whenever various departments are to be brought together for collaborative work.
Two more business terms apply to organizations such as Samsung
One of these terms is Machine bureaucracy which refers to “an organization with very routine and formalized operating tasks, rules and regulations, which is highly centralized” (Robbins and Barnwell, 2006, p.187). As has been already covered in a previous section, the company is bound by a strict set of formalised rules and regulations for some of its departments, and their relationship with the CFO. However, other departments which have considerable autonomy from the finance team, because of their direct liaison with the clients, run on a traditional theory which envisages that these entities face minimum hassles when they get a new client contract or have urgent business matters at hand.
Another term of interest is professional bureaucracy which is defined as “a structural form that has highly skilled professionals, high complexity, decentralization and the use of internalized professional standards in place of external formalization” (Robbins and Barnwell, 2006, p.187). Clearly, as suggested in above statement, Samsung has a professional bureaucracy that looks after the inter-relationship between various departments and the finance team. At the same time, other departments do not suffer from this problem. The entire organization aims to run on a simple, pre-defined value system which cherishes autonomy and independence. The autonomy has to be brought in place by adopting a combination of methods including the Systems approach, the balanced score card approach and the strategic constituencies approach.
Measuring effectiveness of proposed future state: Robbins and Barnwell (2006) define organizational effectiveness in their book as “the degree to which an organization attains its short-term (ends) and long-term (means) goals, the selection of which reflects strategic constituencies, the self interest of the evaluator and the life stage of the organization” (Robbins and Barnwell, 2006, p.76). The judgements of organizational effectiveness serve as an important social function in that they guide social similarly ast individual judgements of performance guide individual behavior (Robbins and Barnwell, 2006, p.76).
If an organization is performing effectively, it is meeting the demands of its constituencies in terms of what they feel could be desirable outcomes of performance. On the other hand, if an organization is unable to satisfy constituent preferences for performance, they will seek alternative sources to satisfy their preferences (Robbins and Barnwell, 2006, p.76). If alternatives are not available, constituents will in turn create pressure on the organization for better alternatives.
Accordingly, with the adoption of suggested methods, severe impact can be felt on various parameters like lead time, customer service level, cycle time and labor expenses. The implementation plan would be depicted by a Gantt chart (fig. 1 and 2) between July-September as below.
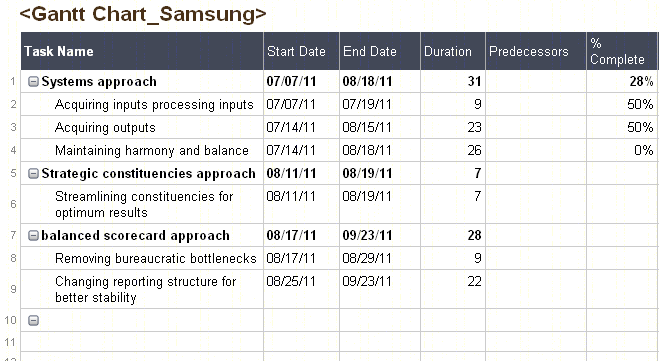
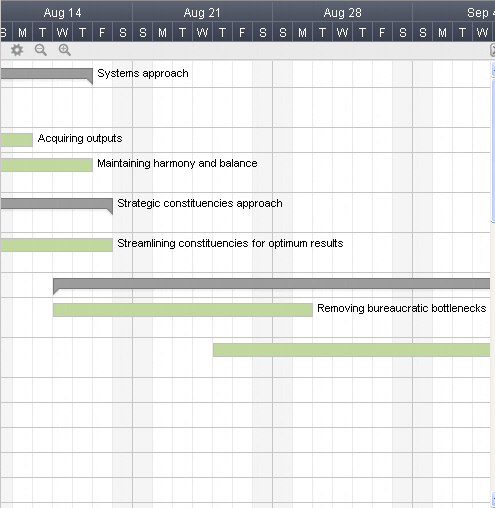
The Gantt chart summarizes the following objective metrics that will enable us to reach optimum targets with detailed activities, activity duration, milestones and responsibilities. As discussed earlier, I had three methods in mind that would go in alignment with Samsung’s Lean Six Sigma approach: Balanced score card, Systems method and strategic constituencies method.
Recommendations and managerial implications: Along with a series of recommendations that will go on to improve the overall quality experience at Samsung, I have made the following set of recommendations for senior management.
- Deploy process finalization engineers: To execute various tasks as underlined in the Gantt chart, the management should be asked to deploy resources who have experience with scheduling to go ahead with implementation of final plan. This would incur temporary recruitment expenses. This is a vital step towards achieving desired targets (Brock and Rosemann, 2009, p.81; Bussler and Haller, 2005, p.92; Becker, 2010, p.45).
- Further literature study: In order to outline an effective framework of what would constitute a multi-purpose evaluation strategy for rudiments of the Samsung’s overall process improvement goals, a major part of the effort was directed at understanding the basic objectives spelled out earlier in the proposal. As far as this research is concerned, both qualitative and quantitative methods have been applied. Currently, the literature that is available on this subject involves experts involved in Lean Six Sigma industry as well as the academic sources for topics like Balanced Score card which have been addressed in this report.
- Improvised data collection methods: I was limited in my data collection methods to rudimentary surveys. They can be improved by using important data mining tools. To analyze the data, it is important to rely on the theoretical propositions of the study and then analyse the evidence based on these propositions. The success of the project, the drawbacks and the successes of the team would be evident from the study being conducted.
Reference List
Akpolat, H., 2004. Six Sigma in transactional and service environments. Sydney: Gower Publishing Company.
Becker, P., 2010. Integrating new asset classes into an asset allocation framework: using scenario methodologies in the case of microfinance. Dusselfdorf; Gabler Verlagg.
Brock, J.V. and Rosemann, M., 2009. Handbook on business process management: strategic alignment, governance, people and culture. New York: Springer.
Bussler, C. and Haller, A., 2005. Business Process Management workshops. BPM International workshops. Nancy, France: 12 (2), pp. 92.
Chang, S.J., 2011. Sony vs. Samsung: the inside story of the electronics’ giants battle for global supremacy. New York: John Wiley and Sons.
Chang, Y.S., Makatsoris, H.C,. and Richards, H.D., 2004. Evolution of supply chain management: symbiosis of adaptive value network and ICT. New York: Springer.
Creveling, C.M., Slutsky, J. and Antis, D., 2003. Design for Six Sigma in technology and product development. Princeton, NJ: Prentice-Hall Professional.
George, M., 2003. Lean Six Sigma for service. London: McGraw-Hill Professional.
George, M.L., 2003. Lean Six Sigma for service: how to use lean speed and Six Sigma quality to improve services and transactions. London: McGraw-Hill Professional.
Macintyre, M., Parry, G. and Angelis, J., 2011. Service design and delivery. New York: Springer.
Mintzberg, H., 1981. Organisation Design Fashion or Fit?. Harvard Business Review 34 (12), pp.81.
Robbins, S. P. and Barnwell, N., 2006. Organisation Theory: Concepts and Cases. Frenchs Forest, NSW: Prentice Hall.
Samsung, 2011. Corporate Ethics. [online]. Web.
Taghizadegan, S., 2006. Essentials of Lean Six Sigma. Los Angeles: Butterworth Heinemann.
Wedgewood, I. and Wedgewood, I.D. Lean Sigma: a practitioner’s guide. Princeton, NJ: Prentice Hall.