Introduction
Integrated business systems and enterprise resource planning (ERP) have emerged as critical aspects of logistics and operations management in the current competitive business environment. According to Guggilla (2017), the ability of a firm to achieve a competitive advantage in the market currently depends on how well it can manage its logistics. The necessity to ensure that the needed raw materials are availed at the processing plant at the right time and the final product delivered to the market on time has forced companies to redefine their supply chain management systems. Briffaut (2019) argues that understanding supply chain principles are one of the important ways of achieving the desired level of success in logistics management.
In this paper, the researcher seeks to investigate systems and operations management processes at Toyota Motor Corporation with a special focus on its supply chain management. The paper will review how this company can achieve a sustainable competitive advantage on its supply chain management using the necessary cost.
Task 1: Approach to Material Management
Toyota Motor Corporation is one of the largest car manufacturers in the world. Its products are sold in the global market and the firm has come up with a unique strategy of developing cars depending on the target market. Having access to the materials needed for the manufacturing and then ensuring that these cars are available in North and South America, Europe, Asia-Pacific, and Africa are very challenging tasks. When analyzing the approach to Toyota’s material management, it is necessary to look at the structure of its supply chain, approach to the management of intermediaries, and how lean and agile practices might produce a competitive advantage for the firm.
Structure of the Supply Chain
The company has a complex supply chain management structure that helps it in ensuring access to all the materials that it needs to facilitate the manufacturing and assembling of its cars. As shown in the figure below, some of the parts are gained from local vendors while others are imported. The first step is to identify and form a business relationship with vendors, both locally and in the international market. One of the products that this firm often purchases from these vendors in large quantities is car batteries (Vecchi, 2017). Toyota Motor Corporation does not manufacture its car batteries. As such, it relies on these vendors to have access to this critical component of its cars.
The firm also purchases other materials such as metal, plastics, electric wires and equipment, fiber, leather, and care tires among other materials. Figure 1 below shows that once these materials are made available, the next step is the actual production process. At the plant, different components are manufactured then assembled as a complete car. The company then ships the finished products to local, regional, and global dealers. The final stage in this supply chain is when customers have access to the care they need from the dealers. The entire process is complex and based on timely delivery of the raw materials to the plant and finished products to customers to achieve specific organizational goals.
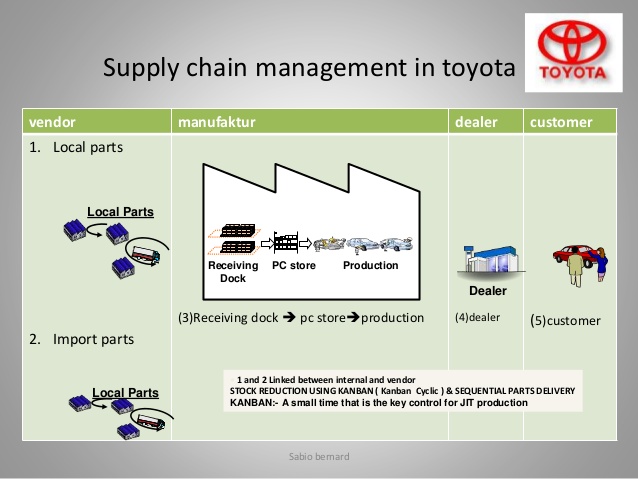
Approach to Management of Intermediaries
Toyota Motor Corporation specializes in the manufacturing and assembling of cars. Its global market reach and the popularity of its cars in different markets make it necessary for this company to use intermediaries to achieve specific goals (Reid, 2019). However, it has to ensure that these intermediaries across the world share its corporate vision and mission. They have to help this company to achieve its strategic goals in the highly competitive market.
As such, it requires an effective approach to the management of these intermediaries. The company must ensure that they are operating in Toyota’s best interest and that customers are taken care of appropriately. Using the 7 principles of supply chain management can help in ensuring that the company achieves its strategic goals while working with these intermediaries by setting specific principles that must guide their operations.
The first step is to adapt the supply chain to customers’ needs. These intermediaries are responsible for regular interaction with customers. As such, they must be effective representatives of Toyota Motor Corporation. They have to ensure that they understand the individual needs of customers at all times and be capable of responding to them. These intermediaries should also communicate with the company about any changes in customers’ needs and preferences.
The second principle is the necessity to customize the logistics network for each segment (Parker, 2018). Some clients may need immediate delivery of their custom-made cars while others may be comfortable choosing from a wide range of products at the dealership. Toyota should work closely with these intermediaries to ensure that each unique need of clients is met effectively.
The third principle is the need to align demand and planning across the supply chain (Harris and Harris, 2015). The supply chain must have the capacity to sustain the demand in the market. Toyota Motors should have a logistics system that can ferry the cars from the manufacturing plant in Toyota City in Achi Prefecture to the global market (Neckermann, 2015). That may require close coordination with some of the leading shipping companies. The fundamental goal should be to make certain that its products are available in the global market at the right time. The fourth principle is to differentiate products closer to the customer (Zijm et al., 2019).
Toyota has a wide variety of cars that meet different customers’ requirements. Dealers should understand how to approach each of the market segments. The next principle is to develop information technology that can support multi-level decision-making processes (Motoyama, 2016). When making critical decisions relating to the management of the dealers, it will be necessary for the management to have access to facts to avoid making mistakes. Having an IT system that helps in monitoring the activities of the dealers and communicating with them will help in ensuring that the management makes sound decisions at all times.
The sixth principle of supply chain management is to outsource strategically. In the process of managing the intermediaries, the company must use its staff to make certain that these dealers are following the guidelines set by the firm. However, it may be necessary to outsource the services of other companies to help in monitoring and evaluation of the intermediaries. The final step is to embrace both service and financial metrics when evaluating the significance of the relationship with each intermediary (Briffaut, 2019). The management of Toyota should ensure that its relationship with the intermediary not only results in the generation of revenues but also strengthens the company’s brand in the market. The seven principles are summarized in figure 2 below.
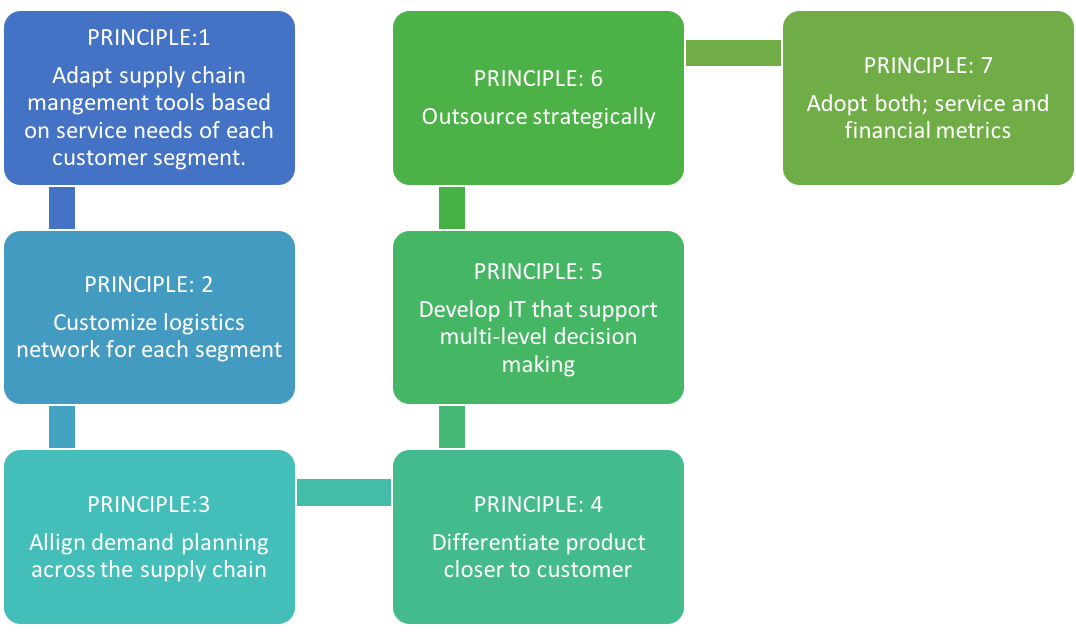
How Lean and Agile Practices Might Produce Competitive Advantage for the Firm
In its approach to material management, one of the areas that Toyota Motor Corporation should take into consideration is how to embrace lean and agile practices that might produce a competitive advantage. One of the fundamental goals of this firm has always been to produce quality cars for its customers at affordable prices. The management of the company has often focused on achieving sustainable competitive advantage at necessary cost.
Embracing lean and agile practices offers this firm a unique opportunity to achieve this goal (Guggilla, 2017). However, it would require it to embrace emerging technologies. The aim is to reduce the number of employees at different points of the supply chain by the introduction of unique technologies.
It is estimated that Toyota Corporation uses approximately $ 15,000,000 every year to monitor and evaluate the activities and effectiveness of its dealers around the world by using specific agents. The cost can be reduced significantly if this firm introduces online technologies to monitor the trends and activities of its dealers. The fact is that the majority of the dealers now use online platforms to conduct their sales, thus, Toyota Motor Corporation can consider applying online technologies to monitor their activities.
With the concept of enterprise resource planning, this company should consider using Pipedrive or similar software to monitor the sales activities of its dealers. This software will reduce the need for the firm to hire agents to conduct a manual review of the dealers. The initial price of installing and making the system operation may be expensive, as shown in figure 3 below.
In the first year, the expenses will be high, and the company will experience a negative reduction in the cost of operation. However, expenses in the subsequent years will drop significantly because it will mainly be the cost of running and maintaining the system. On the other hand, the firm will enjoy a significant reduction in the cost of operation. The agents who were undertaking these tasks may be redeployed to other assignments, helping the company to be more productive.
Reid (2019) argues that the use of this software is often more effective than using people because they cannot be easily compromised through bribes unless the system is breached through hacking. The use of an information system will improve the functionality of the supply chain management system at the firm about material management. The company will achieve a competitive advantage in the market because of the reduction of cost and improved efficiency. The reduced cost will enable the firm to lower its prices but in a way that does not compromise its profitability.
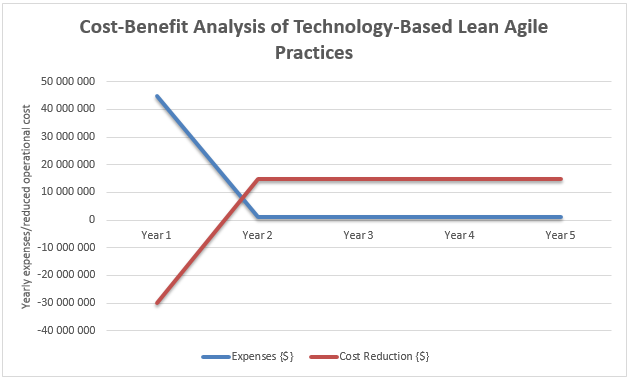
Task 2: Relationships in the Organisation’s Approach to Materials Management
Toyota Motor Corporation has to maintain a close relationship with various entities in its approach to material management. As explained above, the firm relies on the efficiency and effectiveness of its various partners to ensure that its products can reach customers at the right time, in the right place, and at the right price (Briffaut, 2019). The management must consider the need to achieve a competitive advantage but at the necessary cost. Briffaut (2019) argues that sustainable competitive advantage can only be realized if a company embraces practices that enable it to make profits while at the same time lowering its expenses consistently.
The relationship that this firm embraces with these parties should be based on trust and there should be a clear mechanism that shows how each party would benefit. The mutually beneficial relationship will be a motivation to its partners, and it will ensure that they remain committed to Toyota Corporation. The relationship may also require a complex integration of technology to make certain that the use of the human resource is reduced to the bare minimum.
Contractual Arrangements
Toyota Motor Corporation has a contractual arrangement with various entities within the supply chain management to achieve its strategic goals. Suppliers are some of the most important parties that this firm has developed a contractual arrangement with to guarantee that its productions are not interrupted. The contract helps in ensuring that the partners do not inflate products’ prices unfairly at the expense of Toyota Corporation.
The company has a contractual arrangement with dealers around the world to facilitate the sale of its brand new cars. As Neckermann (2015) observes, some of these contractual arrangements restrict these dealers from selling other car brands. Their stores can only have different models of Toyota cars meant for a wide range of customers based on their tastes and financial capacity.
Toyota Motors has also developed a unique relationship with some of the global traders to facilitate reverse logistics. In its effort to reduce pollution and be actively involved in environmental protection, the company has been working closely with some of its customers in the developed economies and some dealers to facilitate the refurbishment of second-hand cars for refurbishment and sale in the emerging economies (Reid, 2019). Second-hand cars are very popular in parts of Asia and Africa. As such, Toyota Motors has developed an arrangement where customers can return their used cars to the company, add some money, and get a brand new one. The old but functional car would then be refurbished and shipped to the markets around the world where they are popular.
The strategy helps in lowering pollution and over-exploitation of resources while at the same time making products of this company more affordable to a wide market. It also helps to increase the number of customers purchasing new cars. The incentive of getting a brand new car by simply returning the old one to the company and paying a little extra money for the car will attract more customers. Figure 4 below shows activities involved in the reverse logistics supply chain. At the factory, the company will have to develop a unique supply chain system that would facilitate the movement of the used product from the end-user back to the company for processing and recycling before it can once again be released back to the market.
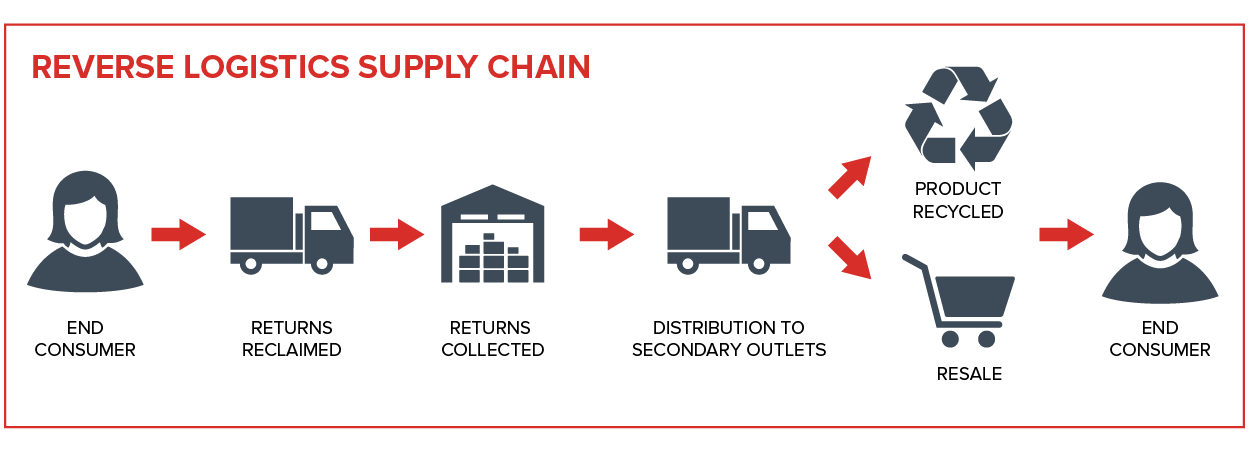
How Activities Such as Outsourcing Impact upon the Operations
Toyota Motor Corporation is committed to producing affordable quality cars for its local, regional, and global customers. In its quest to lower its cost of operations and improve the overall quality of products that it offers, the firm has embraced the practice of outsourcing (Briffaut, 2019). The company understands that to achieve sustainable competitive advantage in the market, it has to focus on what it can do best, and outsource other activities. One of the areas of production where Toyota Corporation has perfected the practice of outsourcing is in the manufacture of car batteries.
The management of this firm understands that its clients need long-lasting and powerful batteries on their cars. As such, the company outsources the services of some of the local and regional car battery manufacturers (Reid, 2019). The strategy is meant to ensure that Toyota Motors maintains a team of highly skilled workers in car manufacturing instead of having to have to develop another team responsible for the manufacturing of batteries. The firm also outsources many other components of the car such as the tires and the lighting system. Maintaining a close and mutually beneficial relationship with each of these suppliers has proven beneficial to Toyota Motors. It ensures that it has access to the needed materials at the production plant within the right time.
The company has also been keen on embracing IT solutions from various vendors in the market to meet varying needs in its production and logistics units. In 2012, the management of Toyota Motor Corporation announced that it will start using Microsoft software to facilitate its on-premise and cloud data management for over 200,000 workers around the world (Motoyama, 2016). The move was meant to ensure that all the employees of this company could have access to data in real-time irrespective of their location. This approach was also meant to help dealers around the world to understand the new trends and practices in the industry.
The strategy has had a positive impact on the overall performance of the firm. It has also improved the relationship between the company and its customers in the market. Instead of waiting for a communication from the headquarters in the form of phone calls or emails, these dealers only need to log in to their account and check the updates (Neckermann, 2015). The strategy has significantly improved supply chain activities because all parties involved have access to the information they need. Dealers can track their consignment in real-time and provide their clients with accurate information about when their products will arrive. As such, it eliminates cases where clients feel cheated when offered promises that are not kept.
Task 3: Role of Emerging Technologies in Toyota Motors’ Approach to Supply Chain
The emerging technologies have proven to be critical in enhancing the management of supply chain activities. According to Akkucuk (2019), many large companies are moving away from manual time-consuming, and labor-intensive approaches of managing their operational activities to approaches based on the emerging technologies. Concepts such as robotics, big data, smart warehousing, 3D printing, and artificial intelligence have gained massive popularity in the field of supply chain management because they help in improving the overall performance and in reduction of cost (Reid, 2019).
At Toyota, the management has been keen on using emerging technologies to ensure that it can have access to materials needed for its operations. It also uses these technologies for its cars, manufactured in Japan, to be delivered to the global market in a cost-effective way and within the right time.
Application of Information Technology to Manage Supply Chain
Toyota Motor Company is actively using information technology in its supply chain management to improve various aspects of operations management. As Briffaut (2019) observes, one of these areas is in monitoring the flow of goods and determining its relationship with the demand. The company has a sophisticated system that enables it to understand what the market needs against what is already available.
The information is then sent to the head office where a decision is made about the number of cars that should be manufactured within a given period. The head office then communicates to the head of the production, informing them about the number of products needed in each of the categories of cars that the company offers. The company has also embraced the use of cloud-based cargo-in-transit software that enables it to determine the movement of goods while being transported.
The dealer and other stakeholders involved can easily know when to expect their cargo and if there are issues that have emerged during the process of transportation that may affect the delivery time. According to Reid (2019), the application of information technology in the supply chain has helped in improving communication among different offices within the firm. The fact that data is made available in real-time and at a centralized location means that all authorized individuals can have access to it without having to go through long processes. Any issue can easily be detected at the earliest point possible and an appropriate solution developed.
These steps have made it possible for the company to deliver its cars in the global market at the right cost and within the right time. It has also made it easy for the company to understand emerging market needs (Motoyama, 2016). The introduction of hybrid cars, such as the one shown in figure 5 below, was a result of the ability of the firm to use this system to understand emerging trends in the industry. These cars are meant to lower carbon emissions and reduce the cost of operating them.
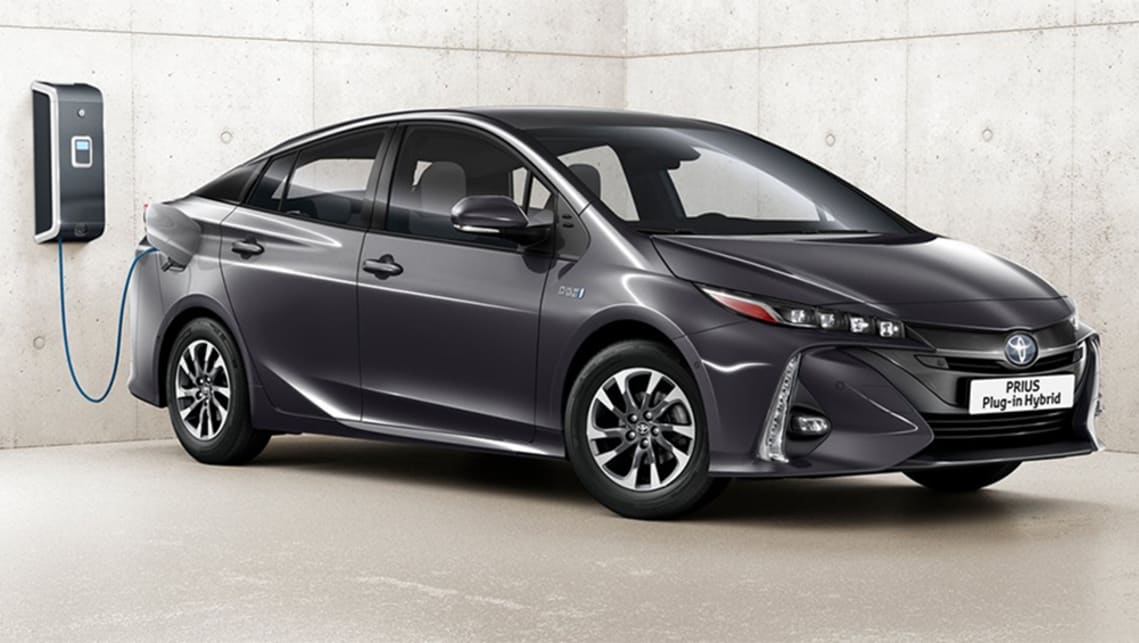
Application of Materials Planning to Manage Supply Chain
Material planning, according to Briffaut (2019), is a scientific approach to determining the requirements of raw materials, spares, parts, and ancillary components in advance. It helps a firm to ensure that there is a smooth and consistent flow of the materials needed to avoid interruptions in the production process. This technique provides steps that this company can use to enhance its material management strategies.
As shown in figure 6 below, it starts with embracing various forecasting techniques. Weighted averages, exponential smoothing, trend analysis, and correlation are some of the possible forecasting techniques that this firm can use. In this automotive industry, trend analysis has proven more popular in forecasting demand for cars and related materials (Briffaut, 2019). The next step is the sales forecast. At this stage, the firm is required to determine product requirements, production mix, and product structure. The firm will focus on determining the possible sales that it will make within a given period.
The information can then help in developing bills of materials, explosion charts in cases unforeseen issues emerge, material requirements, and delivery materials. An effective material planning will help the management of Toyota to plan its supply chain effectively.
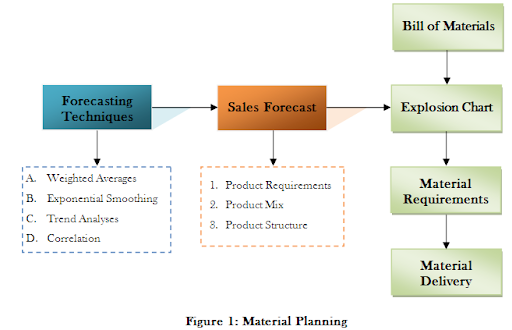
Application of Systems Development to Manage Supply Chain
The management of Toyota Motor Corporation should also consider the use of systems development to enhance its supply chain management and relationship with all its stakeholders. The use of the system development life cycle can help in the process. Reid (2019) explains that system development life-cycle can take different approaches using the basic structure depending on the nature of the company and what it needs to address. Figure 7 below identifies the seven steps that the company will apply when using this model. The first step is to identify potential problems and opportunities in the market. The information will be needed to determine human information requirements, which is the second step.
The team will then analyze systems needs based on the identified problem/opportunities and human information requirements in the third stage. The fourth stage involves a recommended system based on the information obtained in the first three stages. It may be necessary to develop and document software that will help in managing the developed system. In the sixth stage, the team will be tasked with testing and maintaining the developed system (Akkucuk, 2019).
The final stage is to implement and evaluate the system when it is confirmed that it can achieve the desired goal. Rolling out of the new system requires involvement and the support of all the stakeholders, including Toyota car dealers around the world.
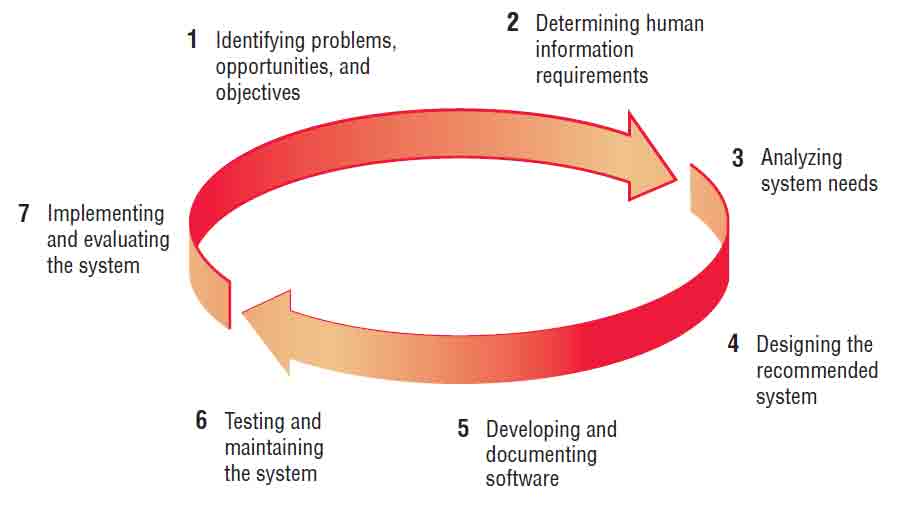
Conclusion
The current competitive business environment requires a firm to have an understanding of systems and operations management to achieve sustainable growth and development in the market. In this paper, the analysis has focused on how Toyota Motor Corporation can use the concept to achieve success in its supply chain management. As a firm that sells its products in the global market, it is necessary for the company to have a robust logistics system that will ensure that its products reach its customers at the right time. The use of technology and various models of management have been identified as means through which this firm can achieve its supply chain management goals.
Reference List
Akkucuk, U. (2019) Ethical and sustainable supply chain management in a global context. New York: IGI Global.
Briffaut, J. (2019) From complexity in the natural sciences to complexity in operations management systems. Hoboken: John Wiley & Sons.
Guggilla, A. (2017) Service now it operations management: demystifying IT operations management. Birmingham: Packt Publishing.
Harris, C. and Harris, R. (2015) Capitalizing on lean production systems to win new business: creating a lean and profitable new product portfolio. London: CRC Press.
Motoyama, Y. (2016) Global companies, local innovations: why the engineering aspects of innovation making require co-location (ed.). New York: Routledge.
Neckermann, L. (2015) The mobility revolution: zero emissions, zero accidents, zero ownership. Leicester: Matador Business.
Parker, D. (2018) Service operations management: the total experience (2nd ed.). Cheltenham: Edward Elgar Publishing.
Reid, D. (2019) Operations management: an integrated approach (7th ed.). Hoboken: Wiley.
Vecchi, A. (2017) Advanced fashion technology and operations management. New York: Cengage.
Zijm, H., Klumpp, M., Regattieri, A. and Heragu, S. (2019) Operations, logistics and supply chain management. Switzerland: Springer.