The firm’s reputation and changes in the external environment can affect Aberfact’s financial stability because the company may experience difficulties in retaining customers and exploring new market possibilities. Evans (2018) states that Aberfact’s competitor Renewable Parts has opened a wind turbine recycling center. It is part of the company’s strategy to revolutionize the industry by introducing a new manufacturing model. Additionally, Dutch researchers created a new design for wind turbines, which is more efficient (Solon 2013).
Currently, Aberfact is known for its poor reliability, quality, processes, and delivery time. This can obstruct the company from continuing the work with existing customers and suppliers. In addition, the issue would make it more difficult to expand and achieve sustainability, because the current model of processes has many flaws.
Quality Control Management
There are several perspectives from which Aberfact can view quality control management. TCQ does not merely focus on improving technical processes, in this case, the manufacturing aspects that affect Aberfact’s products. The main aim of the approach is to change the management’s perception of the issues that currently exist and introduce a tool that would help resolve them.
Fundamental Principles and Concept of Quality Control Management
The focus on customers should include both services that Aberfact provides and the needs of the company’s clients. Thus, the practices that guide Aberfact’s return policy and product maintenance for the wind turbines should be improved.
The leadership component refers to the direction of the organization. It means that Aberfact should have a clear strategic vision for development.
It is crucial to involve Aberfact’s employees in the management process of the company. It means that Aberfact should share its vision for the future with its personnel to ensure their engagement.
Key Principles and Concept of Quality Control Management
Both systems and process approaches focus on identifying and improving the current operations. The processes that guide the company’s daily activities should be examined thoroughly to determine approaches to ensuring efficiency. Improvement should be among Aberfact’s primary objectives as it allows to respond to challenges presented by the industry. As was previously mentioned, in the UK, wind turbine industry is evolving towards applying rentable resources.
Furthermore, Dutch scientists have introduced a new design that would improve the turbine’s efficiency. To be able to adjust the business model to this new development, Aberfact should ensure that the firm is capable of changing its manufacturing. Factual approach implies data analysis in decision making, which leads to a better understanding of market conditions.
The final principle – relationship with suppliers, is especially crucial for Aberfact, because currently, the establishment is experiencing issues due to poor reputation. It can be changed through supply chain modification to ensure that inventory levels are adequate. Through this, Aberfact will be able to minimize costs spent on parts for wind turbines and assure that suppliers regard the company as reliable.
Quality Improvement
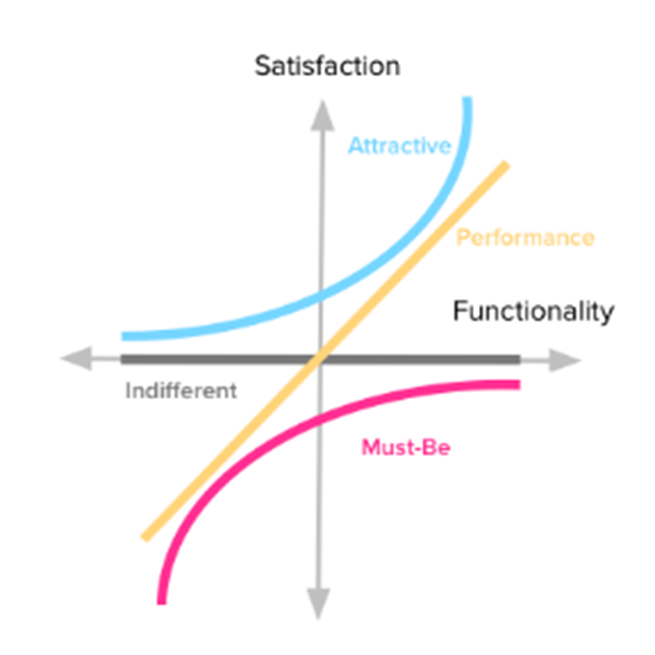
The new strategy of the company should focus on examining customer’s needs and adjusting manufacturing to meet them.
According to Mitra (2016), Kano model can help improve quality management by identifying the customer’s needs. Figure 1 displays a visual presentation of the Kano Model. Three primary categories affect this aspect: basic needs, performance needs and excitement needs. Those are things that consumers take for granted, expect, and additional benefits.
In the long-term perspective, quality control measure will allow Aberfact to achieve better sustainability. In addition, the mechanism of design improvement would allow the company to adjust its manufacturing to the changing demands of the market (Mitra 2016). Currently, Aberfact has a manufacturing facility that employs 400 people.
Aberfact would have to prepare for the implementation of ISO 9001 and total quality control system.
Sustainability is among the primary concerns of Aberfact’s CEO, which should be the center of the company’s strategy. Additionally, financial incentives should correspond to the realistic capabilities of employees.
According to Adirim et al. (2017), quality measures should focus on one of the three factors – structure, outcome, or process.
Berenson and Rice (2015) state that policies should focus on enhancing professional intrinsic motivation, which should be promoted by an organization.
Performance excellence models examine an organization as a whole and identify its commitment to deliver excellent results to the stakeholder.
ISO 9001
It is crucial to understand that having an ISO 9001 certification does not guarantee quality improvements and process efficiency. Aberfact should make certain that the eight principles mentioned above are part of the corporate culture to engage each employee in quality improvements. According to Dalmau, Gimenez, and De Castro (2016) some firms adopt the certificate because of customer pressure, which results in additional spending while not affecting the quality outcomes. The ISO 9001 standard provides tools and guidance to ensure that an organization can achieve its goal (ISO 9000 family – quality management n.d.). However, it is the management’s responsibility to adhere to the advised course of development.
ISO 9001 in the Wind Turbine Industry
The company should evaluate the approaches that other establishments in the industry take. According to Woods (2018), one of Aberfact’s competitors – Duke Energy recently obtained an ISO 9001 certificate.
Aberfact can examine the experience of other organizations in the wind turbine industry in regards to quality control and ISO 9001. Duke Energy is praised for their excellent services and products as the company has received the 2018 Wind Technician Team of the Year Award. The certification that the firm obtained allowed them to ensure that services they provide correspond to customer’s needs.
This initiative aims to create a culture of quality, in which Aberfact’s employees can understand the importance and value of TCQ. According to Srinivassan and Kurey (2014), “a company with a highly developed culture of quality spends, on average, $350 million less annually fixing mistakes than a company with a poorly developed one.” This means that the company’s revenue will increase by both reducing costs spent on replacing faulty equipment and by obtaining new customers.
Benefits and Challenges
Applying the business excellence model can help Aberfact achieve outstanding results in its manufacturing. Award programs are an example of such practice, in which a particular company is praised on a national or local level for its achievements. EFQM is an approach to constant improvement used by many companies across the world. The primary objective of it is a critical evaluation of an organization’s performance and identifying components that require advancement. There are eight fundamental concepts that EFQM consists (EFQM excellence model n.d.) In addition, Business Excellence Matrix can be used as a self-assessment tool for Aberfact. It would allow to critically examine the current position of the company and compare it to the EFQM. By doing so, Aberfact would be able to identify critical areas that require additional attention.
Challenges of such models are presented by the need to reevaluate the existing operations and alter them. Due to the fact that Aberfact is a large manufacturing facility the method may require additional time.
Sustainability
Abefact’s board can address the company’s issues by adjusting policy, strategy, leadership, motivation and measurement. Siva et al. (2016) state that quality management can help support sustainability in product development. This would address the CEO’s concerns regarding the matter because the approach balances innovation and constant level of product quality.
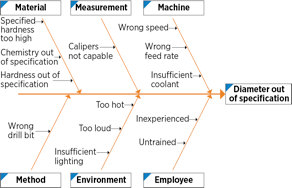
The primary problem of Aberfact is the poor quality of wind turbines, which affects customer satisfaction. Figure 2 presents a Cost and Effect Diagram, which can be applied to identify components of manufacturing that require improvement (Fishbone (Ishikawa) diagram n.d.). This may be due to the unsatisfactory characteristics of materials or a large number of manufacturing errors. The diagram allows analyzing six primary components that contribute to the outcomes of product development.
Pareto chart can help analyze the development and manufacturing process to identify error frequency in particular areas (Pareto chart n.d.) the approach can help Aberfact find solutions to its manufacturing issues. In addition, this method can be applied by the company to analyze supply chain management and identify problems that cause adverse outcomes for the supplier relationship.
Summary
The culture of quality implies that every employee within Aberfact understand the importance of control measures and the goals that the company aims to achieve. This is done through proper leadership and management, which involves setting clear goals and supporting the implementation of new approaches in the company. Thus, Aberfact should set a purpose of identifying manufacturing errors that occur within its production and revise the existing structure of supply chain management. By applying the proposed tools, the company will be able to perform the required analysis. In addition, Aberfact should measure the outcomes to identify whether the strategy was successfully implemented. The ISO 9001 certification can help the organization by introducing new approaches to its operations.
Reference List
Adirim, T, Meade, K, Mistry, K, Council on Quality Improvement and Patient Safety & Committee on Practice and Ambulatory, 2017, ‘A new era in quality measurement: the development and application of quality measures’, Management Pediatrics, vol. 139, no. 1, p. e20163442.
Berenson, R, A & Rice, T, 2015, ‘Beyond measurement and reward: methods of motivating quality improvement and accountability’, Health Services Research, vol. 50, pp. 2155-2186.
The 8 principles of QMS. 2018. Web.
Dalmau, J, Gimenez, G & De Castro, R 2016. ‘ISO 9001 aspects related to performance and their level of implementation’. Journal of Industrial Engineering and Management, vol. 9, no. 5. pp. 1090-1106.
EFQM excellence model. n.d.. Web.
Evans, S. 2018. ‘UK opens first wind turbine recycling centre’. Power Technology. Web.
ISO 9000 family – quality management. n.d. Web.
Fishbone (Isikawa) diagram. n.d. Web.
Mitra, A. 2016. Fundamentals of quality control and improvement, John Wiley & Sons, New Jersey.
Pareto chart. n.d. Web.
Sivaa, V, Gremyra, I, Bergquistb, B, Garvareb, R, Zobelb, T & Isakssonc, R. 2016. ‘The support of Quality Management to sustainable development: a literature review’. Journal of Cleaner Production, no. 138, pp. 1-19.
Solon, O. 2013. ‘Bladeless wind turbine produces energy with no moving parts’. Wired. Web.
Srinivasan, A & Kurey, B. 2014. ‘Creating a culture of quality’. Harvard Business Review. Web.
Woods, A. 2018. ‘Annual wind operations: Duke Energy recognised for operational excellence’. Energy Digital. Web.
Zgodavova, K. 2013. Principles, concepts and standards of quality control management: quality, metrology, information security. Lambert, Saarbrücken.