Introduction
Based on the analysis of the case study provided, Airbus A380 has been experiencing many challenges as it strives to gain an edge against its competitors in the air travel industry. Despite the numerous challenges encountered, the management has always sought to improve operations to guarantee success. The unwanted delays in the development of super jumbo aircraft are due to poor operations management, system failures, and low staff morale (Leask et al., 2008). However, not all is lost since the situation can still be contained when effective measures are implemented. This report assesses the current situation with the aim of making recommendations towards remedying pitfalls in the system or addressing existing problems.
Input-process-output model
Any manufacturing project requires an elaborate system, which consists of well-detailed and laid down processes. To achieve this, Airbus A380 needs to adopt the input-process-output model (IPO) to enable streamlining of operations. Frank J. Landy and Jeffrey, M. Conte (2007, p. 550) contend that IPO enhances team effectiveness as well as in the optimization of performance. While working with IPO, the team should clearly outline their inputs, the transformation processes, and the desired outputs. When outlining inputs, managers should not forget the organization’s content, team duty, and team composition because they are primordial (Landy & Conte, 2007, p. 551).
Inputs are vital components in any organization system. Inputs in an organizational context entail all components transformed in the production processes, the tools used, and all factors that stimulate the morale of employees (Landy and Conte, 2007). Some of the factors that Airbus A380 should keep in place are; staff reward system, training facilities, and viable working environment (Landy and Conte, 2007). All these would facilitate marvelous performances and rapid output (Landy and Conte, 2007).
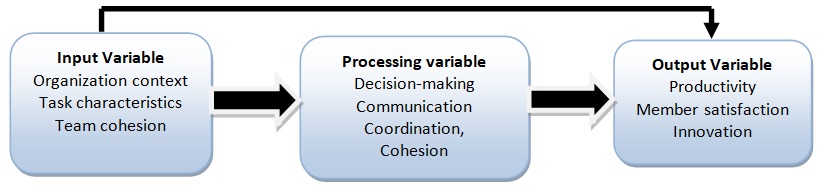
The second area of interest is the processing variables and transformation processes in terms of how they are organized and interlinked (Prasad & Sasidhara, 1997). When looking into transformation processes, one has to consider keenly the criteria used in arriving at any decisions related to how they are organized or scheduled. Moreover, the manager has to consider how he or she is to deal with issues of communication while coordinating the processes. All these factors determine production procedures, selection of methods, and measurements.
Most critically, by streamlining the transformation and output processes, staff cohesion, and mutual understanding among the workforce is enhanced. The processing variable package produces the best in-group performance (Landy and Conte, 2007). Furthermore, when an organization has clearly outlined output variables, it facilitates timely and efficient production. Finally, through streamlined processes, the organization enhances member satisfaction, which in turn enhances innovation and creativity (Prasad & Sasidhara, 1997). Without a well-designed output variable, Airbus A380 research and development (R&D) have not been performing optimally due to related confusion (Prasad & Sasidhara, 1997. Conceptually, a typical input-process-output model should be as shown below.
Processing Map
The processing map is a schedule on how airbus A380 should plan its processing phases (Prasad & Sasidhara, 1997). All the processing phases should be organized in a logical way, including all the action points and respective cost variables related to each activity. The processing map should also outline the time limits through which each activity should take. Since the management is responsible for all activities that take place, accountability should be maintained to avoid blame-shifting games. Nonetheless, the entire processing map should all-inclusive (covering all processing regions) to avoid leakages that can thwart the entire process. In addition, processes should be interconnected to avoid unnecessary interruptions (Prasad & Sasidhara, 1997, p. 16). Despite the pivotal role of processing maps, good communication should be adhered to to streamline operations.
System Support
Conventionally, many organization uses manual decision making, but the invention of computerized decision-making systems simplified the tough process (Cook et al, 2007). One such system is the Decision Support System (DSS). DSS allows the crew to react aptly to the available information and utilize it accordingly (Cook et al, 2007, p. 81). Despite using a Decision Support System (DSS), Airbus A380 has experienced an extremely tough time due to a lack of cohesion between the German employees and the French counterparts. The continuous wrangles and misunderstanding have led to the delayed production at the largest airline in the world. The unnecessary delays in the production process are responsible for Airbus’ poor performance when compared to its fierce competitor Boeing. Since Boeing opted to invest in smaller airlines, it has been able to operate them according to plan, leaving behind Airbus struggling to launch substantial competition (Cook et al., 2007).
Jain (2010, p. 259) asserts that DSS helps the management to better use aggregated information in a more comprehensive manner. In addition, all the historical data is captured in massive databases to offer better decisions making. DSS not only provides a well-organized schedule of completing activities, but it also simplifies complex organizational problems (Marcomoni et al, 2009, p. 257).
DSS breaks decision making into four systematic phases, which are interdependent. The first step is the intelligence system, where all the relevant information is gathered for further action (Marcomoni et al, 2009). The second step is design whereby collected information is designed into a comprehensive format suitable in the real world situation (Marcomoni et al, 2009). At this point, a prototype is developed to form a basis for final output. The third step is choice; here, the R&D makes alternative approaches in which decisions are derived (Marcomoni et al, 2009). The implementation stage is the final step, where all agreed outcome is practiced. Although DSS assumes a linear path, some steps and decisions are referred back to previous stages when deemed less viable (FAO, 2010).
Manufacturing of airbus A380 experienced completion delay due to the regional dispersion from where parts were made. Coordination of process was a tough decision as the operation was hampered by political differences. However, the adoption of DSS ensures the organization has all the relevant information at their disposal.
Updating the Airbus A380 Information system
Continuously updating of the information system is a necessity when working with any information system, for it to operate efficiently. Airbus A380 needs to periodically update its system to ensuring adjustments of the operation to meet the current economic condition. Lack of continuous updating of the organization’s information management system is to blame for the sluggish development pace. To avert the situation, Airbus A380 needs to consider improving the current approach to operations. In an attempt to understand the core of the problem, a soft system method (SSM) may be used. However, adequate security measures should be implemented to avoid internal and external security risks (ISO/IEC 27002, 2005).
Soft System Method
A Soft System Methodology (SSM) is used to structure and sustain thoughts, innovation, and compound organizational problems (Orsoc.org, 2011). The SSM helps the management to revolutionize problem solving and understanding. Lester (2008. p.1) outlines the seven SSM iterative steps as follows;
Problem identification
This is the first and main area of concern in the formulation of problem formulation. A wrong problem definition would result in an erroneous solution. Most often, identification of the right problem is half the mêlée; when the problem is known, there is a higher likelihood of identifying and understanding the solution (Hicks, 2004. P. 87).
Research the situation
Once the problem is formulated, the task force needs to carry out an in-depth study to exhaust all relevant information. This forms the basis for developing the rich picture, which helps to conceptualize the situation (Mycoted, 2006).
Select perspective
The other vital step is generation of the root definition. Root definition entails major processes that should take place in the system (Mycoted, 2006). Airbus A380 root definition is generation of an excellent airliner that will offer exemplary services to travelers and businesspersons.
Developing conceptual model
At this stage, the organization endeavors to alter the lengthy and manual processes used and replace them with simplified and automated processes (Mycoted, 2006).
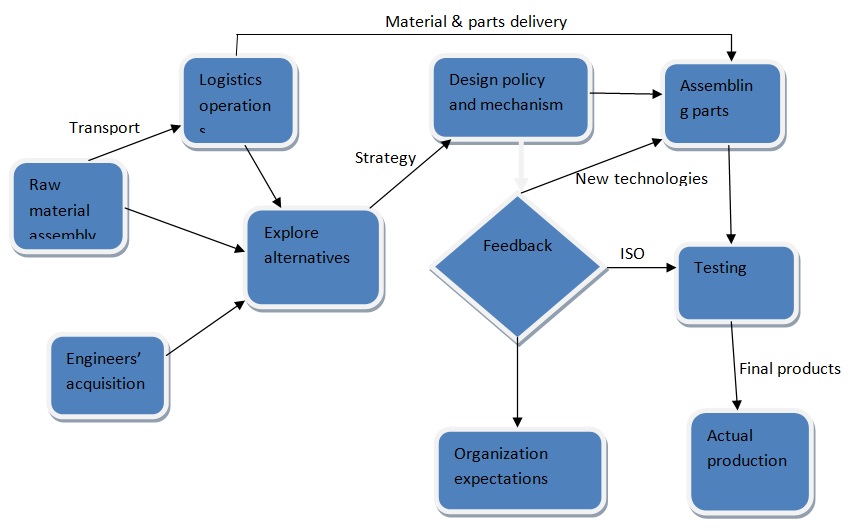
Model comparison
After the model is developed, the task force strives to ensure the system is formulated to fit real world situation. Any deviations detected area addressed promptly to avoid future problems (Orsoc.org, 2011).
Effecting changes
During implementation phase, some changes are deemed necessary to readjust the processing according to the current world. Airbus A 380 should consider all the changes in material availability, staff turnover and technological shifts that may affect processing (Sachenko, 2011). The task force cannot take this process since it requires the organization to deliberate on it.
Taking action
This is the final step in SSM but it is of great importance as it translates the decisions made into practical reality. The organization needs to deliberate on the decision arrived at. Deliberation on decisions and plans is critical in order to determine whether and how to adopt them or nullify them. However, since in this case there is no organization, the task force will just make recommendation on how Airbus A380 should overcome inherent challenges.
Successful development of SSM not only alleviates delay but also helps in development of quality and well thought products (Mycoted, 2006). Thus, Airbus A380 should therefore endeavor to restructure the entire processing to come up with an integrated system.
CATWOE Analysis based on Airbus Case Study Provided
Root definition
Root definition is a statement that provides element functions in the system, Forbes (1995, p. 8) defines root definition as the activity and the reason why it is perceived highly in the system. Airbus A380 root definition is to revolutionize the entire processing activity to develop a world-class air transporter.
Role of SSM in understanding business requirements
The main challenge in any problem resolution is to understand the problem and its constituent requirements. Should Airbus A380 opt to use SSM, the production process will be very easy and all-inclusive. SSM requires an in-depth evaluation of the problem before proceeding with further analysis of the problem. William (2005, p.5) a renowned system analyst asserts that SSM moves real world into the world of systems. Thus, all the practical problems are structure into system perspective. Sachenko (2001, p. 9) a renowned professor asserts that in seamless integration of SSM and information system provides three things; enhance business processes, decision making, and actualizes strategic advantage.
Recommendations
From the above analysis, the following recommendations are presented to better or improve Airbus A380 related operations. To enhance continuous innovation, Airbus A380 should use hypertext model that provides in-depth analysis of idea limit to improve operation efficiency (Fred et al, 2010, p. 343). Another way that the crew can ensure all aspects are considered is embarking on a rigorous brainstorming exercise to generate a knowledge bank. On the same note, Rodan (2002, p. 152) suggests that any process resolution requires a cohesion in the various alternative approaches, as conceived by different employees, before any further operations.
Although most scholars emphasize on innovation, developers have hailed continuous development since vital lessons are learnt in the process. Indeed workers learn through mistakes until perfection level is attained. Through continuous development Airbus A380 will eventual overcome succeed though after a long time. However by incorporating both innovation and continuous learning Airbus will hit a milestone easily. Leask et al (2008, p.3) contend that knowledge sharing does not only link individuals with information but also enhances collaborative working.
To enhance rapid development of the super jumbo jet, Airbus should carry out extensive research (Foesteris, 2008). The research would not only facilitate timely and rapid achievement of the organization’s goals but will also add on the existing skills. The research will provide the organization with new mechanisms or new ways of doing things. Staff morale is also a vital component that determines individual performance and group output. Many organizations fail due to low employee morale and Airbus is not exempted. An effective staff survey should expose all the grievance and dissatisfaction that might have led to slow performances. By stimulating the staff, Airbus will enjoy higher levels of employee performance and productivity.
To avoid redundancy in operations, information systems should be updated regularly. Since Airbus A380 uses multidimensional XML, the Xpath should be used to update the system (Foesteris, 2008). This process requires updating the database through the SQL. To do this, the R&D department should carry out routine surveys to make sure the operations remain abreast with the technical dynamics.
Information technology management is also another area that is experiencing rapid changes and therefore R&D is compelled to keep its system current. To manage this, Airbus needs to carry out extensive research and benchmarks to ensure the organization applies the best practices in the industry. For instance, the French wing used incompatible software to do 500km wiring requiring updating computer blue prints (Sachenko, 2011). This operation was costly since the organization was force to transport engineers from German to Toulouse. An operation schedule to take two weeks ended up using four, which attracted a high cost. Thus, it is inevitable for the organization to update its systems.
Should the organization decide to employ the aforementioned recommendations, both time and money will be saved. First, the duration of developing the aircraft will be reduced dramatically. This will allow the company to compete with its competitors better and in a more aggressive manner. Secondly, instead of using outdated technology updating the system will enhance the processing to integrate both current and old technologies to develop ultramodern design (Sachenko, 2011). Since the information system will generate immediate feedback, all processing branches will get timely information. Finally, updated information system fosters coherence between the Germany and the France based locations.
Updating information management systems helps any organization to improve its performance. According to an economic survey which was done by Organization for Economic Cooperation Development (OECD) (2004, p. 177), it was found out that a firm increases competitive advantage by up to 92 per cent. Although airbus trail Boeing, effective implementation of the above recommendations would narrow performance between the two airlines. Thus, by continuously improving its management system Airbus will enjoy reduction in costs and improvement in production rate. In addition, a management system will also capture the market situation and therefore the management will be able to make informed decision on where to operate.
Company Analysis
People Issues
All organizations depend on staff to carry out mission specified by the organization. However, many a times, organizational aspirations suffer from low workers morale. After considering the situation at Airbus, most employees are demoralized leading to the slow pace of performances. Unless this situation is addressed Airbus will struggle to live true to its potential. Several measures could help towards boosting employees’ morale. As per the Hygiene theory, these factors include motivation incentives as well as hygiene factors (Fiore, 2004, p. 68).
Airbus needs to provide incentive services to all its employees to enhance performances. As shown in the case study, although, the organization offers competitive remunerations; employees who have special capacity or talent and who discover new technologies go unrewarded. These not only discourages innovation but, to some extent, it also spurs employee turnover as gifted employees seek green pastures. On the other hand, Airbus need to introduce hygiene factors such as facilitating job satisfaction. The work environment should be good where managers and employees interact and share freely. Finally, all promotions should be purely based on merit and seniority.
Technology issues
Conceptually, all airlines are awash with technology and technical appliances. Despite being equipped with state of the art technological resources, Airbus’ condition has been wanting to some extent. For instance, the launch of Airbus has been rescheduled time after time. The case study indicates that in 2005, a delay of six months was announced while in 2006 the launch was further delayed for a further one year. All these delays were attributed to adoption of wrong technology. Therefore, the organization need to be innovative to ensure current technology is applied to avert unnecessary delays.
It is also evident that Airline has a defective information system and lacks sound coordination. For example, it was economical for the Hamburg office to issue directions to the Toulouse processing site on how do the wiring rather that transport engineers. Apart from incurring extra costs, the entire operation delayed production of the airbus. Thus, there is need to have an effective information system to ensure all stakeholders get the required information and acts in a timely manner. The above problem can be addressed by ensuring the organization takes a total overhaul of the old system and install a new system (Hannington & Voehl, 2006, p. 35)
Technological advancement also offers competitive edge. From the case study, it is evident that Airbus’ main competitor has also been suffering from application of inappropriate technology. For instance, it is shown in the case study that 787 Dreamliner aircraft had 8,000 fasteners fixed in the wrong place and engineers were hired to readjust them. The entire process delayed the completion for two year. Thus, incase Airbus A380 adopts up to date technology the organization can take advantage in the market as Boeing stumbles.
Organizational Features
Organization and resulting organizational structure forms the backbone of any organization. Prevalence of a faulty organization leads to misunderstandings and differences that affect performance. In the case of Airbus A380, the organization has inherent differences that have affected the organization in a great way. For instance, coordination between two processing sites i.e. Toulouse and Hamburg, is wanting. From the case study provided, it is clear that the organization is also suffering from poor leadership that forced the then CEO Mr. Gustav Humbert and his immediate team to resign in 2006. This implies that Airbus lacked a leader with the ability to motivate staff to perform to their potential.
Based on the case study provided, constant infighting between the German and French staff is an indication that Airbus lacks proper leadership. There is need to urgently contain the differences between the employees from different sites. The only way this problem can be addressed is by adopting hierarchical organizational structure with regional managers. The regional managers should ensure his team is highly motivated and performs according to the expectation. In addition, the regional manager should strive to reducing infighting thus enable employees to focus on their work.
References
Cook, M., J., Noyes, J., M., & Masakowski, Y., 2007. Decision Making In Complex Environments. Ashgate publishing Ltd: Hampshire
FAO. 2010. Chapter 9: Marketing Information System. Web.
Fiore, D., J., 2004. Introduction to Education Administration: Standards, Theories and Practice. Eye on Education, Inc: Larchmont
Forbes, P. 1995. Strategic Thinking: A Role for Soft Systems Methodology. Web.
Foesteris, N., 2008. Updating Multidimensional Xml Documents. Web.
Fred, A., Dietz, J., L., G., & Liu, K., 2011. Knowledge Discovery, Knowledge Engineering And Knowledge. Springer: Berlin.
Harrington, H., J., Voehl, F., 2007. Knowledge Management Excellence: The Art of Excelling In Knowledge Management. Paton Press LLC: Chicago.
Hicks, M., J., 2004. Problem Solving and Decision Making: Hard, Soft and Creative Approaches. Cengage Learning: London.
ISO/IEC 27002. 2005. Information Technology – Security Techniques – Code of Practice for Information Security Management. Web.
Jain, L., C., 2010. Handbook on Decision Making: Vol 1; Techniques and Applications. Springer: Berlin.
Landy, F., J., and Conte, J., M., 2007. Work In The 21st Century: An Introduction To Industrial And Organization Psychology. John Wiley & Sons: New York.
Leask, L., Milner, T., Norton, M., & Rathod, D., 2008. Knowledge Management Tools and Techniques. IDEA: London.
Lester, S., 2008. Soft System Methodology. Web.
Marcomoni, A., Sutter, G., Q., Critto, A., 2009. Decision Support Systems For Risk- Based Management Of Contaminated Sites. Springer: New York.
Mycoted. 2006. Soft System Method. Web.
OECD. 2004. Knowledge Management Measuring Knowledge in the Business Sector. Organization for Economic Co-operation and Development: Paris.
Orsoc.org. Introduction to Soft system methodology. Web.
Prasad, Y., K., & Sasidhara, S., 1997. Hot Working Guide: a Compendium of Processing Maps. ASM international: Columbus , OH.
Rodan, S., 2002. Innovation and Heterogeneous Knowledge in Managerial Contact. Springer: New York.
Sachenko, A., 2011. Foundation of information system Business. Web.
William, B., 2005. Soft System Methodology. Kelong Foundation: Michigan.