Assess the role of systems and operations management at Airbus and its integration within the business
The manufacturing and assembly industry today is required to achieve a high degree of efficiency and produce products with a high degree of accuracy with close to zero defects per product or even per process (Wang 2000, 44). Particularly, the manufacturing of large aircraft by companies like Boeing and Airbus is a big undertaking since a single aircraft can have close to a million parts which must be accurately assembled/ manufactured and letter fitted to the plane itself. Airbus Company is a company that has a reputation of manufacturing the world’s largest and most complicated aircraft and therefore it is paramount that operation management practices and project management principles that run their Airbus assembly lines are defect-free and highly efficient ( Slack, Chambers & Johnstone 2010 154).
Airbus is a large company operating not only in one factory or assembly point but rather many factories that were formed as a result of a collaborative business agreement between partnering countries. The whole of Airbus therefore in itself is a system having its plants in the three respective countries as interdependent subsystems which are very important to the existence and functioning of Airbus as a company (Tonchia & Cozzi 2008, 155). Thus, if the output of one system is defective then the output of that system which is the input of another system will affect the outcome of the whole process. Systems are mutually dependent and as a result are required to collaboratively and cooperatively work together to create a synergy that will boost their output to a level that would have not been achieved if they worked separately (Slack, Chambers & Johnstone 2010 148). In layman’s terms, Different departments of Airbus are not islands and therefore inputs of other departments may be used after being ejected as outputs from other departments (Slack, Chambers & Johnstone 2010 124).
Operation systems management is a discipline used in business especially in the manufacturing industry to ensure that the production system occurs smoothly, on time, and with a high degree of accuracy in quality (Roy 2005, 187). In the absence of systems and operations management then a lot of resources may be lost and manufacturing processes may end up being mixed up just as it was the case when employees in the Airbus factories in France and Germany developed two cables with different specifications 500km long that resulted to a lot of wasted resources(Wilson 2001, 111). Hence Operation management and project management practices such as Business process mapping assists the organization to create a good plot/chart that describes every step of production and whose responsibility is it to carry out certain processes of production and assembly ( Ronen & Pass 2007, 88)
Systems engineering is a discipline of operations management used in the commercial world to achieve optimal manufacturing levels through the application of statistical models and accurately plotted flow charts (Civitello & Levy 2007, 82). Most of the time these systems work perfectly when they are computerized and all employees are assigned unique un-conflicting tasks that ensure no duplication of roles occur. It is through business process mapping and operational research usually unveils the critical path of manufacturing processes is discovered to achieve tasks within the stipulated timeframe. Nevertheless, it seems that the systems at Airbus companies had overlooked important disciplines falling under project management and operations management, therefore, leading to a massive waste of resources and time, therefore, disappointing their customers who included many world airlines (Slack, Chambers & Johnstone 2010 154-180).
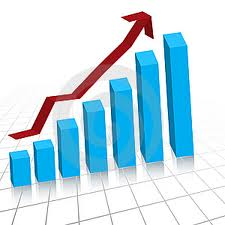
Systems are put in place in an organization to assist each other in carrying out tasks/functions/duties which one department cannot do and therefore they are collaborative/ co-operative agencies that are not in competition but rather play a complementary role(Wilson 2001, 88). The politicking and rivalry of the German and French departments, therefore, were deleterious to the operations of Airbus. The strategy, therefore, exists to control existing systems within the organization with a high degree of efficiency with the mission vision and goals of the organization in mind (Slack, Chambers & Johnstone 2010 154-180). The Airbus case is a good example of lack of integration in the highest, middle, and lowest levels of strategy that proved costly to their corporate goals (Blyth 2009, 12)
The case of Airbus illustrates that a poor operation management strategy is present within the organization and has therefore affected how the inputs of various interdependent systems are converted into output efficiently (Slack, Chambers & Johnstone 2010 140). Wastage of resources, poor coordination (of various departments like finance, production, assembly, and management), poor management, lack of cooperation, and delays are enough evidence to suggest that the operation management system that has all business processes not well mapped to achieve a lean production system (Mahadevan 2005, 77). It is, therefore, necessary that a complete overhaul and design of a new system be put in place to oversee the production of the Airbus A380 thereby ensuring inefficiency and interdepartmental integration is realized.
Explain how the Airbus information systems and operations management should be updated to support and improve their business efficiency
Manufacturing and assembly organizations which do not accept and embrace the role which is played by operations management are most likely to continue facing hurdles in their production activities and its therefore necessary to come up with appropriate operation management strategies that will guarantee a lean production system that is optimal (Capman 2005, 15). It hence becomes necessary to develop perfect operations and information management systems that will enable organizations such as Airbus to save money, time, number of defects, and accuracy of manufacturing. For the Integration of various systems and subsystems which exist in their organization to be successful then the organization must embrace the discipline of planning production which is production operations management for efficiency to occur (Mahadevan 2005, 127-134). It is with the same zeal that information management systems are necessary for the overall integration and interaction of various systems within the organization to give rise to the culture of co-operation and high performance within an organization. The current situation in Airbus Company indicates that there is both a communication failure and operation management systems failure (Slack, Chambers & Johnstone 2010 148-154).
Due to the existence of poor information a management system duplication of tasks in France and Germany has even led to conflicts and competition between employees injuring the corporate goals of Airbus as a company (Slack, Chambers & Johnstone 2010 160). It is thus necessary for a complete overhaul of existing systems to occur if efficiency is to be realized in Airbus for even the parent company EADS and Airbus top management to be in tandem (Slack, Chambers & Johnstone 2010 160-166). A Soft System Methodology is an effective methodology that is used to identify particular problems in entities such as Airbus which have their operations being handled by different departments, which exist as semi-independent systems and assist airbus to embrace manufacturing concept planning embrace factory layout planning and analysis to optimize production (Wilson 2001, 15). The Soft Systems Methodology is thus an effective technique of pinpointing where inefficiencies arise from by looking at the rich picture consequently play a big part in forming the solution. The advantage of using the Soft systems Methodology to identify and resolve inefficiency within various systems in the organization is that it doesn’t ignore the needs of various stakeholders who are involved with the organization (Wilson 2001, 20-24).
The term CATWOE is as result used to define the actual publics/stakeholders that the problems within the systems affect and these are the Clients in this case those purchasing the Airbus, Actors individuals such as employees and suppliers, and Transformation, Worldview, owner and Environmental constraints (Wilson 2001, 40-54). The end process of the Soft Systems method of solving a problem is the realignment process within the organization (Wilson 2001, 113-121). The pivot of SSM and CATWOE is that this problem-solving technique insists on accurately identifying the needs of every stakeholder within the system and subsystem within the organization (Wilson 2001, 89) Information can empower individuals within the organization and thus by identifying the exact needs of various individuals within an organization it then makes it easy to set up necessary mechanisms to respond to these needs. If the needs of each department will be accurately defined using the Soft system Methodology then the management will effectively supply the various departments with accurate information at the right time.
The needs of every manufacturing and assembly system within Airbus differ and therefore those departments assembling wings, wiring, and cockpit instruments have different requirements and needs and it is, therefore, necessary to understand them and deal with them at a personal level for production efficiency to transpire (Kerzner 2009, 99-106). Thus, business efficiency can only be achieved when each department and system will have their needs looked into, and then the appropriate information system requirements are developed to create better functional departments that consist of empowered individuals who are armed with relevant information to carry out production operations with a high degree of accuracy. The same applies to the current operation management systems because each process of assembly is different and unique and thus their needs have to be distinguished using a Soft Systems Methodology so that each important point of assembly have the necessary mechanisms and resources assigned to them for them to operate with a high level of accuracy (Wilson 2001, 47). With all needs identified then solutions can be formulated to help each department get the necessary information from updated information systems to construct a more tangible operations management strategy. For that reason Airbus will more effectively rejuvenate its operations by ensuring that business processes mapping is correctly done and even using operational research it will be possible to save time by operating with the critical path during the assembly process thereby achieving a lean production process. Additionally frequent evaluation using Soft Systems Approach and CATWOE will make it possible for Airbus to continuously improve its operations management until the organization achieves the desired level of production (Wilson 2001, 115).
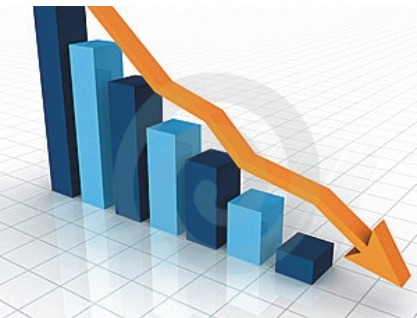
Evaluate the role of Soft Systems Methodology in analyzing and defining the business requirements of Airbus
The current level of inefficiency and poor performance in the assembly and production of Airbus A380 IS quite disturbing and if no effort is taken to correct the current situation then the production operation system is not changed then future projects may be in jeopardy (Kerzner 2009, 132). Manufacturing of aircraft is very delicate because air safety concerns usually take center stage during the process of manufacturing a single mistake emanating from the smallest component such as a wire or a screw may turn catastrophic in the future. Knowing it is the duty of production line managers and the corporate management to embark on a problem identification process and thereby create long-lasting solutions that will assist Airbus to streamline production and integrate the operation of various systems and subsystems that operate within the entire organization (Kerzner 2009, 112-114). Knowing that Airbus assembly activities are triangulated between Britain, France, and Germany any efforts to improve production and operation management practices within the company must be carried out in Unison (Slack, Chambers & Johnstone 2010 160-166).
A Soft System Methodology is a good holistic technique that can be used to handle especially people issues such as culture, psychological differences, and even at some instances social conflicts that may arise in situations such as Political difference that usually end up hurting the production process (Wilson 2001, 76). SSM usually embarks on problem identification by looking at the symptom that indicates the existence of a problem and hence proceeds to attack the root cause that has caused the symptom. Consequently, when the root cause of the problem is identified then the need of each system can accurately be identified for a suitable organizational design, information system design, performance evaluation, education, and training of staff to be adopted within Airbus (Chase, Jacobs & Aquilano 2006, 72-85). Thus, through entering the problem situation and expressing the actual problem using SSM it becomes plausible to formulate the root definitions of all systems and subsequently create suitable conceptual models to govern operations within these various systems and subsystems (Slack, Chambers & Johnstone 2010 160-166). It is these conceptual models that are compared with the actual situation on the ground and if deviations exist then corrective action is applied to bring about positive change.
Having understood how SSM works then these are the necessary recommendations to Airbus. The organization needs to establish a clear route of communication by computerized information management systems and giving access codes to relevant departmental heads that will act as the main source of information for their departments and thus coordinate Britain, Germany, and France (Chase, Jacobs & Aquilano 2006, 22). The current system is quite muddled and thereby affecting the optimization of production. The wastage of funds and time delays are due to poor communication and different department compete instead of working together for the good of the organization. A fragmented structure is thus harmful because due to the complex nature of assembly roles all systems must be in a constant exchange of information to minimize errors (Chase, Jacobs & Aquilano 2006, 198). Training programs aiming to alter the current culture of the organization is also necessary for the organizations (Appelbaum, St-Pierre & Glavas 1998, 293).
The benefits of competing and politicking are far much less substantial than the benefits of collaborating and working together for the greater good organization. Employees should be enlightened on the overall strategies of the organization (that is, corporate, business, and functional area) and then have a new culture that is in harmony with strategy fostered within the organization for all employees to understand the direction in which they are headed to (Chase, Jacobs & Aquilano 2006, 72-76). A clear business mapping process should be drawn at the highest level ensuring that every production plant’s role in the assembly of A380 is well defined. Furthermore, each assembly plant should have its entire business processes mapped out so that every employee is empowered by knowing what they are required to do (Fink 2002, 65; Kerzner 2006, 89-93).
This is expected to reduce the level of conflict between various systems because role clarity will be enhanced and duplication will be reduced, consequently, time and money will be saved automatically. Additionally, calculating the critical path of various business processes and setting targets for employees on the assembly plants will enable Airbus to work with more accurate time frames (Fink 2002, 25; Kerzner 2006, 103).The lack of integration and poor coordination between the various countries where there are manufacturing plants Airbus A380 can be improved by changing the organizational design and the Organizational structure and appointing a centralized because the nature of complexity that accompanies the production of Airbus A380 requires the kind of command flowing through the hierarchy of leadership to originate from one source to avoid conflicts (Campbell & Stonehouse 2002, 312). In conclusion, a more lean system of production can be achieved if SSM identifies the root problem and the resulting strategies of Operation management are based on the needs of each department.
Analyze the people, technology, and organizational issues involved in improving the operations at Airbus
People issues
For operational efficiency to become reality in Airbus the level of organization, technology, and people-to-people relationships must be well structured (Campbell & Stonehouse 2002, 222-234). Human resources are a very important part of an organization and therefore workers must maintain a good relationship for them to work together for the greater good of the organization (Allen & Jarman 1999, 166) The Airbus case is a good example of how people issues can affect the quality of output in an organization. The competition and politicking between the French department and the German department led to a loss of millions of dollars simply because instead of the employees realizing that they are part of the same organization they instead operated with a culture of rivals which injured the actual performance of Airbus (Slack, Chambers & Johnstone 2010 132-150).
Organizational behavior and theory are disciplines that insist that even if an organization had all resources and all other systems perfect it would ultimately fail and not achieve its goals (Camillus 1986, 23-34). This is because it is people who are the driving force behind the other systems, and their effort towards organizational performance is irreplaceable. The lack of appropriate coordination, proper communication, and leadership within Airbus has resulted in the current stalemate between the parent company and Airbus top management executives and is also responsible for the existing conflict between various systems of the organization and is, therefore, necessary to change the way the organization is handling human to human interaction to resolve all human issues (Barkley 2004, 88). Thus, the introduction of lucid people relationship strategies and also improving coordination is key to the performance of the organization.
Technology issues
For operation management practices within Airbus to achieve a high degree of efficiency the right kind of technology must be used within the organizational operation systems ( Allen & Jarman 1999, 65). The introduction of computerized information systems and accurate software within various functional areas is very appropriate. Technological compatibility is hence vital (Kerzner 2009, 188). The current technology has a lot of cons and has even led to the accidental manufacturing of 500km of wiring cables that have the wrong dimensions thus unsuitable for the assembly of Airbus A380 (Slack, Chambers & Johnstone 2010 132-150). For lean manufacturing and streamlining manufacturing to be successful, the organization will be required to use the latest statistical manufacturing processes that allow the manufacturing process to use highly accurate by introducing arm robots to handle most of the assembly processes thus reducing human errors (Greasley 2007, 124-133)
With the right technology also comes efficiency, but only if the right personnel is trained to match the capabilities of the technology. Training therefore should be organized for all employees within the organization to make sure that employees who have the necessary knowledge are competent to effectively handle the entire assembly process (Capman 2005, 87-89). Technology’s role in manufacturing is to simplify work and save on time and therefore if the right systems are put in place and all the organizational employees have trained then the desired levels of performance will be easier to achieve (Kedrick 2009, 104).
Organizational issues
The arrangement of roles, relationships, and the distribution of power are very important in the performance of an organization (Capman 2005, 56-58). The current system in Airbus is poorly organized thereof making it hard to achieve targets due to the existence of conflicts that arise out of a fragmented management system. It seems that there are too many centers of communication and the roles of the German and French departments are conflicting (Apgar 2006, 55). The top management in its part is also guilty as charged because the level of communication and coordination between the parent company and Airbus is also paralyzed.
Leadership thus cannot be effective if Airbus is poorly organized, with the complexity that is characteristic of manufacturing aircraft Airbus must show a high degree of organization whereby the roles of individuals and the flow of power and processes are accurate so that every employee can be held accountable for his/her part (Dittmer 1997, 199) Duplication of roles, conflicts and politicking are signs that the current organizational structure should be scrapped and redone so that the existing level of chaos in Airbus can be a thing of the past (Appelbaum, St-Pierre & Glavas 1998, 34).
References
Allen, G. & Jarman, R., 1999. Collaborative R&D: manufacturing’s new tool, 5th ed. New Jersey: John Wiley and Sons.
Apgar, D., 2006. Risk Intelligence: Learning to Manage What We Don’t Know. Boston, MA: Harvard Business School Press.
Appelbaum, S., St-Pierre N. & Glavas, W., 1998. “Strategic organizational change: the role of leadership, learning, motivation and productivity.” Management Decision Vol. 36, no. 5 pp. 289–301.
Barkley, B., 2004. Project risk management. New York: McGraw-Hill Professional.
Blyth, M., 2009. Business Continuity Management: Building an Effective Incident Management Plan. New Jersey: John Wiley and Sons.
Camillus, J., 1986. Strategic planning and management control: systems for survival and Success. Lexington, KY: Lexington Books.
Campbell, D. & Stonehouse B., 2002. Business Strategy An Introduction: 2 edition. Title Linacre House, Banbury Rd: A Butterworth-Heinemann.
Capman, C. S., 2005. Controlling strategy: management, accounting, and performance measurement. London: Oxford University Press.
Chase B. R., Jacobs, F, T., & Aquilano N.J., 2006. Operations management for competitive advantage, Volume 2006, Part 2. Indiana: McGraw-Hill/Irwin.
Civitello, A. M., & Levy, S, M., 2007. Construction operations manual of policies and procedures. New York: McGraw-Hill Professional.
Dittmer, H. W., 1997. Goldratt’s theory of constraints: a systems approach to continuous improvement. Great Barrington, MA: ASQ Quality Press.
Fink, S., 2002. Crisis management: planning for the inevitable. 2nd ed. Bloomington, IN: iUniverse.
Greasley, A., 2007. Operations Management. London: Sage.
Kendrick, T., 2009. Identifying and Managing Project Risk: Essential Tools for Failure-proofing Your Project, 2nd ed. New York, NY: AMACOM.
Kerzner, H., 2006. Project Management: A Systems Approach to Planning, Scheduling, and Controlling, 9th ed. New Jersey: John Wiley and Sons.
Kerzner, H., 2009. Project Management: A Systems Approach to Planning, Scheduling, and Controlling, 10th ed. New Jersey: John Wiley and Sons.
Mahadevan R., 2005. Operations Management: Theory and Practice. New Delhi: Pearson Education India
Ronen, Y. & Pass, S., 2007. Focused operations management: achieving more with existing resources. New Jersey: John Wiley and Sons.
Roy, R. M., 2005. Operations Management: Theory and Practice. New York: New Age International.
Slack, N., Chambers, S., Johnstone, R., (2010) 6th Ed. Operations Management. Harlow: Pearson.
Tonchia, S. & Cozzi, F., 2008. Industrial Project Management: Planning, Design, and Construction. New York: Springer.
Wang, J. X., 2000. What Every Engineer Should Know About Risk Engineering and Management. New York, NY: Marcel Dekker.
Wilson, B., 2001.Soft Systems Method: Conceptual model building and its contribution. Chichester: John Wiley and sons.