Introduction
Research Title
A Study on implementing Total Quality Management and its effect on performance.
Background
In order to realize the necessity of the degree of improvement that is required in the modern-day corporate environment that prevails across almost every industry, it is essential to delve into a process that involves the consistent observation and analysis of the problems that plague this corporate environment. In order to do so, it has become common for managers to spend massive volumes of their time seeking out modes, methods, and techniques to bring about improvements in performance. As recessions eat into the economic foundations of organizations causing them to file for bankruptcy, costs are rising, and quality management has become all the more tedious and expensive. Causes such as these cause financial drains that eliminate the benefit that could be obtained from revenue streams.
Generally, such cases include disputes over either a generation of a quantity level that is not feasible or a generation of products that do not adhere to the quality standards that were required to make the product a success. Once problems such as these have taken root in the organization, it is only natural that the organization attempts to solve them, which causes a further drain of resources when either negotiation, arbitration, or litigation are used as a solution to the problem.
Organizations are searching for, developing, and spending resources in the acquisition and implementation of management styles that cater to the levels of customer satisfaction that they are required to meet while ensuring that no excess causes the surplus utilization of the limited resources available. The idea is to develop a method that allows the upper management to develop strategies that permit employees and departments throughout the organization to make a contribution to the numerous processes of the organization.
However, the perimeter is not limited to merely the departments and employees within the organization but also spans owners, designers, prime contractors, specialty contractors, and suppliers. This approach allows quality management to be brought about as a combined result that not only is the end product in complete compliance with quality standards but also ensures that the numerous layers of the production process are set to deliver an end product that agrees to the demands of the rapidly evolving and increasingly demanding consumers.
Problem Statement
The world of business is rapidly evolving, and it is not uncommon to see managers hold meetings and brainstorming sessions or hire consulting firms to find ways to improve the operational productivity of the organization so that the maximum amount of productivity possible can be obtained from each working element of the organization.
However, the management may not always be able to identify the roots of the inefficiencies present in the infrastructure of the organization and leading to problems such as errors, dissatisfaction, high costs, slow responses, and defecting customers. Inefficiencies such as these continue to evolve within the organization if they remain unnoticed, and it is for the same reason that they eventually reach a point where they become a major issue once they are recognized. Yet, even though they become issues of significant concern to the management, it does not change the fact that the management is still unable to put their finger on the exact cause of the problem.
Scenarios such as these exist because the problem is not isolated at any point within the organization and is not an irregularity at all. It is, in fact, the actual working procedure that is being followed within the organization, in light of which the results being obtained in the form of errors, dissatisfaction, high costs, slow responses, and defecting customers are only natural.
Research Problems
- What hurdles does the management face in implementing a Total Quality Management strategy?
- What should the nature of the model for Total Quality Management be developed and implemented by an organization?
- What are the implications and influences of the implementation of Total Quality Management upon an organization?
- How can a Total Quality Management strategy implementation model be demonstrated in practice?
- Does the implementation of a Total Quality Management strategy serve to influence the performance effectiveness that pertains to the quality level of the output that the organization is yielding?
Significance of the study
The study will serve to establish the reasons which Total Quality Management should be considered for implementation across different industries.
It will serve to highlight the significance of effectiveness and efficiency checks within the organization, particularly those that relate to Total Quality Management. In doing so, the research will also delve into the numerous ways that one can delve into the measurement of the effects of the implementation of a Total Quality Management strategy.
Structure of the research
The paper has been designed to follow the following structure of chapters.
- Chapter 1: Introduction to the Dissertation assisted by background, significance, and objectives of the research.
- Chapter 2: Discussion on previously performed research studies on brand loyalty to identify basic elements and types of brand loyalty and the variables that it is influenced by.
- Chapter 3: Elaboration upon the research methodology adopted for the research study and the aspects of the research that the research methodology will cover.
- Chapter 4: Presentation of findings observed from adopted research methodology and literature review.
- Chapter 5: Conclusions and recommendations drawn from the findings and presented in light of the literature review.
Research Methodology
Introduction
The research methodology adopted in research is one of the most essential and fundamental building blocks of any research. The research methodology serves to not only determine the degree to which the research will delve into the subject of concern but also serves to establish the techniques that are to be used in the research (Kothari 2005). Since the research is intended for the purpose of the accumulation of knowledge, therefore it would not be unreasonable to conclude that the significance of the research relies quite appropriately upon the research methodology that is used in the performance of the research (Ketchen and Bergh 2004).
However, it is essential to note that when a research methodology is being established for a research project, there are a number of limitations that exist and that merit being considered before the research can be either initiated or referred to in later research. These limitations are not only those that are particular to the subject of research at hand and hence to the subject research but are also from previous research that is used in the course of the subject research as well (Goddard and Melville 2004). Even though the results derived from the research may be of considerable significance on their own, it is imperative that the limitations experienced either directly or indirectly at the time of the research are kept in consideration throughout the research process.
It is for the same reason that it is essential to establish the research methodology before the actual research can take place since there is seldom any capacity to return to the drawing board once the actual process of research has begun and the channeling of resources towards the research has commenced. It is, however, possible to divert the direction of the research in cases where a faulty hypothesis has been formulated or a similar situation has been encountered; however, doing so may cause the credibility of the research to deteriorate to a significant degree. We can therefore conclude that a judgment of the credibility of the research can be made by assessing the research methodology used in the research.
Research Methodology adopted
The research methodology adopted in this research is one that comprises the multilateral use of two sources: the primary source and the secondary source. The research initiates by establishing ground knowledge about the subject through the literature review. The literature review serves as a process that allows for the development of a comprehensive understanding of Total Quality Management and provides an insight into the research and findings that exist pertaining to Total Quality Management.
The literature review allows for the compilation of results obtained from research that was performed on the subject in the past, and once the literature review has been complete, the primary sources are brought into use. The purpose of the primary sources is that while the literature review presents the bigger picture pertaining to Total Quality Management, the primary sources allow the research to be directed towards the area of Total Quality Management that the research requires.
Primary Sources
The primary sources for this research paper shall be gathered by making use of a survey questionnaire that will be implemented to gather data from volunteer participants. During the implementation of the survey questionnaire, all participants will be approached with their permission, and any and all information accumulated in the implementation of the survey questionnaire shall be used strictly for research purposes. The aim of the implementation of the survey questionnaire will be to collect data from personnel who are associated with varying industries in order to obtain a view of the bigger picture with regard to the implementation of Total Quality Management, and the approaches that are presently being used to implement is as well as the perceptions that prevail with regard to Total Quality Management across varying industries.
Secondary Sources: Former Research Studies
A large part of the research comprises the accumulation of the literature review. The research forms its gradients in the later parts of the paper through the information accumulated in the literature review. The secondary sources used in the paper hold relevance because of the fact that they are used as the foundations of the research and as well as the inferences derived from the research.
Limitations
No matter how many precautionary measures are taken, one cannot escape the fact that there will be a certain number of limitations that should be kept in light before the scope and the credibility of the research can be judged.
Since the research is based heavily on former research studies that have been performed with regard to Total Quality Management in the past, it is essential to note that certain possibilities may have existed at the time when those former researches were carried out, and therefore one cannot rule out the possibility that those limitations may have an indirect implication upon this research study since inferences derived by them will be used as the foundations for this research study. We can therefore conclude that it would be unjust to ignore the fact that the inferences presented at the end of this research will be indirectly influenced collectively by these limitations.
Also, when analyzing the inferences that this research concludes upon, it is essential to note that there may be an element of bias or prejudice that may go undetected during the research and may play serve as a limitation in the process of the research. This factor may not only have implications on the end results and the perspectives used in the research but may also have an implication on the analysis of the findings of the research.
Summary
The scope of the research is dictated by the scope of the research methodology since it serves to not only determine the techniques used in the research but also serves to establish the nature of data that is used in the research and the instruments of analysis to which the data is subjected. The research methodology for this particular research has been designed so that it facilitates the research as it proceeds with the analysis and data accumulation stages without causing a compromise on the credibility of the research and seeks to assist the research in avoiding succumbing to the limitations that pertain to the research.
Literature Review
Introduction
Today’s market is becoming far more than simply competitive; it has become hyper-competitive and demands that consistent quality is supplied to the end-users. This unique yet aggressive form of demand had led to a decrease in the effectiveness of the rudimentary quality management techniques that were being applied for decades and centered on a quality control department whose personnel would inspect random samples of the finished product before it was shipped out to distributors or other channel members. This has led to the incorporation of quality management in a manner that entails the implementation of continuous checks and balances (Hakes 1991). This particular can be referred to as Continuous Improvement and is more commonly known as Total Quality Management.
This method of operation necessitates that the primary objective of an organization is formed in the mold of the quality standards that it is required and/or expected to meet. Consumers are seeking products that adhere to higher quality standards and provide them with a higher value for their purchase through a low price tag (Goetsch and Davis 2005). In order to provide consumers with this blend, it is essential that the organization adopts total quality management as the core philosophy that it uses in its functioning and implements it across all the stages of its value chain so that quality checks and balances can be executed on a department level as well as on the value chain level.
Introduction to Total Quality Management
Total quality management is not merely a management technique that can be applied through an already established and predetermined series of steps that an organization or a part of the organization can be subjected to in order to increase productivity. In fact, Total Quality Management is a complete management philosophy that requires complete adherence to the principles that it holds as its constituents. Successful Total Quality Management requires that it is not used as a contingency plan but as one of the fundamental pillars with which the organization or the division of the organization is being run.
Therefore, Total Quality Management can be concluded to be a complete road map that should be adhered to completely if the desired results are to be achieved (Williams 1994). If an organization or a firm was to consider adopting Total Quality Management as a contingency plan or a strategy that is to be used only partially or briefly, then Total Quality Management cannot be expected to fully serve the purpose for which its application was considered in the first place.
If one was to consider a scenario where a Total Quality Management strategy is applied only partially, then there is little doubt that the Total Quality Management strategy will serve to only partially succeed in deriving the results required, and any results received will be of a nature that will wither with time unless the time periods of the application of the Total Quality Management strategy is prolonged significantly (Ross and Perry 1999). The concept can be understood to be of a nature in which solving one problem at a time may help to move the organizational process along but will not serve to eradicate the root causes from where the problems are originating.
Principles of Total Quality Management
Organizations that are turning towards the adoption of Total Quality Management as the core management philosophy for their organization are doing so because of the fact that Total Quality Management serves as a management philosophy that is based on four major principles that can be observed in the following figure..
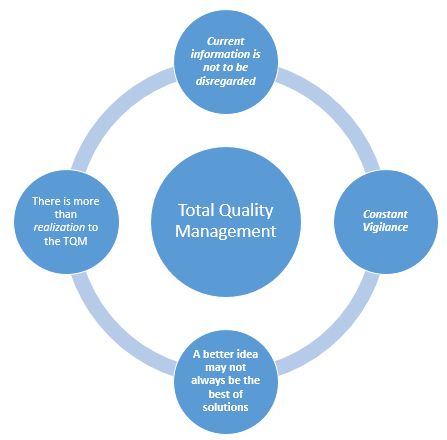
Current information is not to be disregarded under any circumstances
There are often times when a think tank or a quorum present during a conference or a meeting is either brainstorming or in the process of formulating and suggesting ideas. In times such as these, it is only natural to attempt to seek out a solution that is as out of the box as possible and is multilateral in its approach (George and Weimerskirch 1994). The quest moves from solving the actual problem to finding an undeniable solution. In times such as these, it is imperative to keep the basic most fundamental facts regarding the problem in the limelight since the Total Quality Management philosophy seeks to save time and resources by opting for methods and techniques that can serve to solve a problem without having to go through the expense of valuable time and resources that may become part of solutions as they get all the process of the formation of the solution becomes all the more rapid and vast in its evolution.
Constant Vigilance – The primary mindset is to be challenged continuously
Continuous testing and validation that are otherwise considered to be undeniable ground facts are imperative in the Total Quality Management philosophy. This fact remains because there is more than often the issue of the difference in the frame of reference that is kept by each observer of the same situation (Oakland 2003). Through continuous evaluation and assessment, one issue will be eventually subjected to multiple frames of reference when it is under observation and can therefore be expected to be completed within the grasp of those who are assigned to solving and simplifying the problem. This perspective serves to encourage employees involved in an organization or a department of the organization to assess their modus operandi every time an irregularity or a peculiarity is observed instead of attempting to find an external cause and make amendments by tightening procedures. The perspective allows areas of the organization to sharpen their functioning in order to deal with problems instead of pressurizing other areas of the business.
Doing something better may not always be the best solutions
Total Quality Management centers on finding the appropriate way that a problem needs to be solved rather than spending time and resources on redesigning or rethinking the entire system. However, this approach does not mean that the focus should only be on the problem and not on the bigger picture (Rajendra and Babu 2006). What this approach means is that the problem has to be solved from the perspective of the frame of reference within which it exists rather than attempting to replace an entire system. A problem encountered in a system of a process in the organization may not always mean that the entire system is of no use and is faulty. A simple tweaking may be all that is required in order to bring the system to its optimum level of productivity.
Do not make the mistake of the following realization with the termination of the Total Quality Management strategy
Realizing problems as they occur is an imperative part of Total Quality Management; however, Total Quality Management is a management philosophy that highlights the fact that the realization of problems is useless unless and until it is immediately followed by action (Comité euro-international du béton 1998). Most organizations realize the problem and spend considerable amounts of time and expenditure in preparing reports that single out the problem, yet once the problem has been identified, the scenario is abandoned at its standing.
The Total Quality Management focus
Total Quality Management serves as a management philosophy that focuses solely on quality and centers on the continuous incorporation of quality in the structure of the organization (Gitlow 2000). What was formerly known as a desire to incorporate continuous improvement has now evolved to a point where it is a management philosophy altogether. It is essential to note that Total Quality Management does not simply base upon the use of statistical instruments and procedures to continuously validate and assess the quality standards being exercised in an organizational structure but, as mentioned earlier, focuses on a much bigger picture in which the management philosophy adopted by an organization and includes the following elements (Lawler, Mohrman and Ledford 1992).
Total Quality Management focuses on the formation of strong bonds with the customers as well as the suppliers in order to bring about a balance between the costs incurred in the production process and the quality of the end product at the end of the production process so that consumers can be kept satisfied while ensuring that the supplies understand the position of the organization and the costs being incurred are kept under control (Born 1994).
Total Quality Management has two primary fundamentals, the first is the fact that Total Quality Management is supposed to be adopted as a management philosophy by the organization, and the second is the attribute that it is mandatory that the application of Total Quality Management is continuous and that in doing so, internal as well as external working elements of the organization are kept as an active part of the Total Quality Management implementation process (Lighter and Fair 2004). Hence the Total Quality Management philosophy serves to increase employee dedication to the organization as well through the continued involvement of staff at all levels of the organization.
In order to perceive the organization from the Total Quality Management perspective, it is essential that the organization is viewed as an internal system rather than as a concoction of numerous departments where each department is functioning to prove its own individual effectiveness and efficiency. By allowing managers to take a step back and look at the bigger picture, Total Quality Management allows them to perceive the inflows and outflows of information that exist in the organization and allows managers an opportunity to determine the sinks in the system where more resources are being utilized than are required (Dawson and Palmer 1995).
By focusing on the causes of the problem, Total Quality Management allows managers to concentrate on determining the degree of utility of each decision rather than simply the tedious process of making a decision (MacDorman, MacDorman, and Fleming 1995). This encourages managers to promote teamwork in the organization and gives employees opportunities to contribute to the decision-making processes and the quality assertion processes in the organization.
Quality Circles
The implementation of Total Quality Management serves to establish the organization as a complete infrastructure and serves to break away any boundaries that may exist between the departments (Nanda 2005). The implementation of Total Quality Management eliminates friction between departments and serves to allow them to function as one unit. Since Total Quality Management is implemented not as a department-based strategy or as a quality control management strategy for a limited time period, it allows the departments to establish a core of operations around which they can operate.
More than often, the core of operations is constituted of department heads or other employees in the organization who desire to ensure the optimum execution of the Total Quality Management strategy. Groups such as these that are formed voluntarily and function independently of any official intervention are referred to as quality circles.
These quality circles are usually present at one or the other level within the organization even when the organization is not using Total Quality Management as its core management strategy; however, the application of Total Quality Management encourages the involvement of quality circles in quality control and management measures (Rogers 1995). As a result of measures such as these, it is natural for an improvement to be observed in the functioning of the organization. At other times, the organization decides to establish formal quality circles that are designated for the task of regulating the implementation of Total Quality Management in the organization.
Implementing Total Quality Management
Organizations have begun to make use of Total Quality Management quite commonly. The reason for this is that the management philosophy of Total Quality Management is highly multipurpose and multilateral and can be implemented across an organization belonging to any industry. For instance, a prominent utilization of Total Quality Management has been observed in the healthcare sector, where hospitals and other medical institutions have chosen to implement Total Quality Management.
It is essential to note that facilities such as these are those that belong to the service industry, and in cases such as these, the scenario tends to become highly volatile in cases where the implementation of Total Quality Management goes in a manner that was neither projected not expected. In cases such as these, Total Quality Management is implemented rigorously, and while Total Quality Management may hold the attribute of flexibility to a certain extent, Total Quality Management strategy implementations are more than often supplemented with rigid guidelines and are made to function with pre-established thresholds beyond which a certain utilization of resources is not allowed to go.
According to a report on the implementation of Total Quality Management in a healthcare facility, there were profound results experienced throughout the functioning of the organization (Ismail and Maling 2001). According to the report, the implementation of the Total Quality Management strategy in Baskent University Hospital began with the accumulation of information regarding the billing operations of the facility and other administrative operations of the facility. Elements such as check-in times and check out times, lengths of stay, the number of successful cases, and a number of failed cases were recorded closely, and the readings were used as a threshold to decide the standing of the facility and to gain a perspective of the position where the Total Quality Management strategy would initiate from.
It is important to highlight that as this process was carried out, it served to determine several sinks in the facility where one or the other resource was going to waste. This phase also served to highlight the areas where two or more departments were being unable to coordinate because of one or the other reason. Once this phase concluded, the next phase was to root out and eradicate the highlighted problems. Inter-departmental problems were solved by familiarizing staff across the departments that served a similar role and could be taken as counterparts of one another.
In order to eliminate scenarios where incomplete, frequent, or irregular forms were causing an undesired level of stock control, quality circles were established in the departments that contributed to stock control in the facility. This served to bring about a decrease of over fifty percent in the excess resources that were being used up as a result of undesired form frequencies.
The journal article reported that as a result of the implementation of Total Quality Management, the department heads in the unit became conscious of the quality level that their department operated upon and began to serve as a quality circle in the same regard. This served to bring about an improvement in the number of successful operations and also contributed to improvements in bed occupancy rates alongside. In order to meet demands, the facility decided to supplement its working elements with external mechanisms to perform an out-sourcing of sorts in order to handle the excessive influx of patients with which the facility had previously been unable to cope, resulting in the loss of precious time and lives.
Total Quality Management or Total Quality Management is basically defined as a business strategy that aims and engraves awareness of the process of quality throughout an entire organization. Total Quality Management is applied on an extremely large scale when it comes to the professional fields of manufacturing, production, government and service industries, hospitals, call centers, as well as NASA space and scientific projects and programs.
Taking it word for word: Total Quality Management
Total: Encompassing the entire organization or corporation, the supply chain, and the product life cycle.
Quality: refers to the degree of excellence or worth of the product and all its complexities.
Management: this refers to completing all the necessary steps of management, planning, leading, controlling, organizing, staffing and provisioning. The word-for-word breakage of the entire phrase sheds considerable light on the process that Total Quality Management really is. The main aim of this process is to ensure the excellence in quality throughout all processes within the organization in order to succeed in providing the customers with what they want and succeeding in satisfying the consumers and, in exchange for that pleasure at high-quality supply, achieving customer loyalty and largely increasing its customer equity which gives the organization a competitive edge and a hitch over the other corporations still struggling with competitive necessity.
Total Quality Management is basically a steady approach to the art of management that was uncovered in the Japanese Industry during the 1950s. However, its popularity stretched to the west in the early 1980s. Total Quality Management describes a culture, a basic attitude to provide satisfaction and provide excellence, the best of its kind. It exerts the importance, promotion, and application of excellence in all aspects of a corporation’s activities.
Skeptics often tend to stay aloof from the process of Total Quality Management; the reason for this is that surveys performed by consulting companies have come up with not very encouraging evidence. According to recorded data, only 20-36% of companies that have implemented Total Quality Management have found any significant improvements in their tangible activities; therefore, Total Quality Management is not very widely exerted (Pyzdek 2003). However, contradictory proof that when largely successful companies were studied, it was found that they implemented Total Quality Management on extensive levels, which goes to show that their success depends on the awareness of quality embedded within the very core of their organizational strength.
Every successful organization bases its success on the degree of importance the organization gives to customer satisfaction, and this is what Total Quality Management promotes; after all, Total Quality Management, at its core, is a basic management approach in order to achieve long term success. But Total Quality Management is never brought about by a lone participant; it calls for teamwork. It depends on a joint effort on the part of all the members of the organization that corresponds to the various activities a corporation performs. Total Quality Management, when embedded in the culture of the organization, becomes an important part of it.
However, not many are adopting Total Quality Management under the umbrella of their corporation, and for this very reason, it has become almost extinct in the United States, while in Europe, it is used extensively and is applied thoroughly to all aspects of European corporations. The United States of America has adopted the factor of only Quality Management and focuses on it. Total Quality Management remains rampant in Europe.
Quality Management basically functions on three main components, Quality Control, Quality Assurance, and Quality Improvement. It remains focused on the improvement of quality and also on achieving it. QM, therefore, uses these three major components in order to bring more consistency into the process of all-rounder quality achievement and supply. And these are the criteria that the USA depends on and implements.
Fundamental understanding of Total Quality Management
The importance of understanding Total Quality Management is that in order to apply Total Quality Management, one must understand the revolutionary principles that Total Quality Management brings about, the core fundamentals that Total Quality Management corresponds to and depends on, corporate attitudes being at the heart of it. Total Quality Management possesses the strength to bring about huge success and exudes immense power, but only if understood and applied correctly (George & Weimerskirch 1994). Like any other field, a complete understanding of the main concepts makes it easier to perform and implement.
But no know-how only results in sloppy mishaps and accidental failure. Commitment to quality, as mentioned above, is high and is very necessary for the company to survive in an extensively commercial and ever-changing environment. A fact of importance is that with the changing times, perspectives change, priorities change, attitudes change, yet in all aspects of these currently changing times, Total Quality Management will be required to stay the same.
The reason for this is with all changing aspects of time the same aspect of improvement of quality will be demanded. And this is what Total Quality Management will have to cater to (Goetsch & Davis 2005). This is because, in all different professional fields, consumers demand high quality; therefore, the only thing that remains unchanged is an updated version of quality improvement to take care of the satisfaction and pleasure of consumers.
Quality Management V/s Total Quality Management
Total Quality Management basically corresponds to various factors that, in turn, depend on quality improvement. For example, the overall development, deployment, and maintenance are what Total Quality Management takes responsibility for. Six sigma, which is a Quality Management initiative, is more than just a process; it focuses more on the concept of quality improvement and basically yields more consistent results (Pande, Neuman, and Cavanagh 2000).
The main difference between the two is the approach both them adopt. Total Quality Management takes quality as conformance to internal demands and internal requirements, while Six sigma simply focuses on improving quality by reducing defects and mishaps. It is more focused on the organized trend of quality improvement. Benchmarking is another strategy of Quality Management that involves one organization studying the success curve of its competitor to see where its corporation is lacking and focusing on those points to achieve maximum improvement, customer equity, loyalty, and ultimate success.
From the above, it is clearly visible how the two processes are differentiated from each other. Total Quality Management focuses on the overall aspect of production, while Quality Management focuses on improving only the aspects that are lacking in order to gain a maximum degree of high quality (Creveling, Slutsky, and Antis 2002). It serves as a troubleshooter, where after extensively studying the competition, focuses on the regions that create room for failure and strive to improve what is lacking.
Summary
Total Quality management serves to bring about a significant degree of multilateral cooperative efforts in the functioning of an organization. Although Total Quality Management may be a management philosophy that requires that the subject organization adheres to it completely, it is not uncommon to see a department manager attempt to exercise Total Quality Management as a test run and be followed by department heads of other departments.
We can therefore conclude that Total Quality Management is a management philosophy that is rooted in the cooperative functioning of the numerous working elements of the organization. It is for the same reason that it is observed that organizations choose to establish Total Quality Management strategies in a manner such that they are designed to bring about a revolution in the functioning of the organization. This allows the organizations to observe a complete redesigning of their infrastructure through the regulation of quality standards at different stages of the functioning of the organization.
TQM allows organizations to implement measures that allow organizations to gain more than simply adhering to the quality standards that consumers expect. The implementation of Total Quality Management allows the organization to attain a degree of professionalism that pertains to the internal working of the organization as well as the final product or service that the organization has to offer. While previous quality management strategies were designed to perform quality checks, total quality management allows organizations to perform quality standard assessments at each level of the organization so that the chances of error at each level can be minimized.
As the chances of error at every next level of the organization continue to decrease, the productivity continues to increase, causing the organization to make room to increase operating effectiveness and efficiency. By saving up on resources, the organization.
Findings and Analysis
The implementation of Total Quality Management has implications for a number of areas within the organization; these include top management commitment, social responsibility, strategic planning, customer focus and satisfaction, quality information and performance measurement, benchmarking, human resource management, training, employee involvement, employee empowerment, employee satisfaction, teamwork, employee appraisal, process management, process control, product and service design, supplier management, continuous improvement and innovation, quality assurance – preventive, quality culture, communication, quality systems, just in time inbound and outbound delivery systems and flexibility.
If one was to classify these areas within the organization as those that belong to one of three levels of the organization, then we could consider the three levels to be employee level, process level, and organization-wide level.
When confronted with the question that was designed to gather the participants’ opinions on the areas of the Employee level of an organization level on which Total Quality Management has the most significant implications, it was observed that there was a significant degree of the participants chose to opt for employee involvement as the prime area where the implementation of Total Quality Management has the most profound effects.
Areas of the Employee level of an organization undergoing significant implications
The participants were of the opinion that around twenty percent of the implications of Total Quality Management are on the human resource management, whereas training merits only five percent of the implications of the implementation of Total Quality Management on the infrastructure of the organization. Another area of the employee level of the organization where Total Quality Management was considered to hold profound implications was the aspect of the degree of involvement that the employees had in the workings of the organization. Twenty percent of the participants believed that Total Quality Management helped to increase employee involvement in the organization to a significant degree.
It is important to highlight the fact that human resource management and employee involvement were the only two areas where the participants appeared to find the greatest degree of implications in an organization. Only two percent of the participants believed that Total Quality Management allowed organizations to make room for employee empowerment, while ten percent of the participants chose to state that the implementation of Total Quality Management in an organization allowed for an increase in teamwork within the organization. Another five percent of the participants were of the opinion that Total Quality Management assisted in employee appraisal functions. A tabular description of the results obtained from the survey can be seen in the following table.
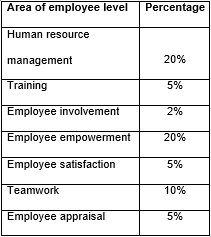
Areas of the Process level of an organization undergoing most significant implications
When the survey participants were asked to highlight which area they considered to be the most influenced within the organization at a process level when the organization was subjected to Total Quality Management, it was observed that the highest number of participants were for those who believed that the implementation of Total Quality Management allowed the organization to exercise continuous improvement and process control in the organization. The area of the process level of the organization to follow was that of the quality assurance that prevailed across the organization. It is important to note that this quality assurance was of a preventive nature rather than that of an aggressive quality assertion nature.
The participants also believe that the implementation of Total Quality Management allowed for a significant improvement in the communication within the organization. It is essential to highlight at this point that while numerous management models allow managers to facilitate the departments of an organization to work productively, very few allow the improvement of communication across the numerous processes of the organization. Fifteen percent of the research survey participants believed that the implementation of Total Quality Management in the organization allowed for the improvement of the overall quality culture that prevailed in the organization. The development of the quality culture of an organization is a significant area of development in the organization since it allows the processes to establish a foundation that supports the implementation of Total Quality Management in the later stages of its implementation.
Eight percent of the survey participants believed that the implementation of Total Quality Management allowed process management to improve, while another eight percent were of the opinion that Total Quality Management allowed process control to improve. The area of product and service design is influenced to only a minor degree as a result of the implementation of Total Quality Management, and the area of supplier management appears to be influenced even lesser in the same regard since only two percent of the participants seemed to view supplier management as an aspect that Total Quality Management addressed. However, six percent of the survey participants did appear to view flexibility as an area of the process level of the organization to be an element that Total Quality Management addressed. The tabular presentation of the results obtained from this question can be observed in the following table.
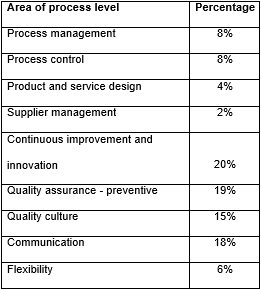
Areas of the organization-wide level of an organization undergoing the most significant implications
The next question that the research participants were asked to answer was that of the exact areas on the organization-wide level of an organization level that they considered Total Quality Management to have the most significant implications. The research survey participants had the option of choosing from Top management commitment, Social responsibility, Strategic planning, Customer focus and satisfaction, Quality information and performance measurement, Benchmarking, Quality systems, and Just in time transport systems.
It was observed that the implementation of Total Quality Management allows organizations to exercise procedures that are based upon quality information and performance measurement. Twenty-three percent of the participants believed that the implementation of Total Quality Management allows organizations to comply with customer quality standards and hence satisfy the customers. Another fourteen percent were of the opinion that the implementation of Total Quality Management allows the organization to implement just-in-time systems and hence, save up on costs that would otherwise have drained away revenue streams.
Eight percent of the research survey participants were of the opinion that the implementation of Total Quality Management served to increase the commitment that the top management had to the organization, while another eight percent were of the opinion that the implementation of Total Quality Management allowed organizations to exercise effective strategic planning. A comprehensive elaboration of the results obtained from this question in the survey questionnaire can be observed in the following table.
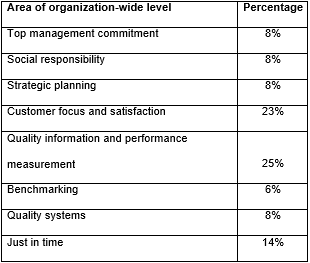
Conclusion & Recommendations
As an outcome of the observations made through the literature review and the results obtained from the implementation of the survey questionnaire, a number of elements can be concluded with regard to the implementation of Total Quality Management. If we were to bring into use the results obtained from the primary sources and the information accumulated through the literature review, we could conclude that the implementation of Total Quality Management for any industry center on a certain set of principles that serve to establish the foundations of the implementation of Total Quality Management in an organization.
Principles of the implementation of Total Quality Management
The principles of the implementation of Total Quality Management with an organization are comprised of the following elements of perception (Oakland 2003).
The standards of quality that an organization adopts shall be dictated by the expectations of the consumers.
Interests of any and all parties concerned with the end product of the organization have to be considered in the decisions made by the organization.
The implementation of Total Quality Management shall be one that is continuous and not used as an instrument that is used temporarily and then abandoned.
The production process is one of the key phases in the organization’s system where the Total Quality Management strategy of the organization shall center on the most.
Gradients shall be established in the quality standards, and the quality standards shall not be limited to the quality of the end product but to the degree of involvement that employees are exercising in the production process.
Leadership at all levels shall be motivated to adopt Total Quality Management and shall be convinced of the effectiveness that Total Quality Management holds before its incorporation can be carried out in the organization.
The organization shall realize that unless they adhere to quality standards and provide consumers with the quality that they desire, the consumers will eventually choose to opt for an alternate product that they find more compliant with the quality standards that they desire.
Quality management has become the center of attention for modern-day organizations because of the fact that it has evolved considerably in recent decades. Quality management was previously considered as a quality standard to which the end product was supposed to adhere, and the organization would make use of quality control departments in order to make sure that this was made possible. However, this approach has a drawback in the fact that it serves to limit the scope of the quality management operations of the organization to only one department or at one point in the organization. The quality control department was considered as one that was kept isolated from any other operations and functions of the organization and was to serve only at the point where the end product or a part of the end product would be finalized to pass on to the next stage of the value chain.
However, with passing time and the increasing number of obstacles and hurdles that an organization is now faced with, there is little doubt left in the fact that quality control cannot be successfully implemented unless it is implemented not as a department with a limited number of personnel but as a management philosophy that is spread across every department. This allows the organization to experience multiple benefits.
Firstly, the implementation of quality control is spread out across the numerous departments, processes, and functions of the organization, and this serves to decrease the load from each department through teamwork and coordinated efforts. Secondly, the organization is able to train its employees in quality control techniques and operating procedures so that a quality control department does not have to be established altogether.
Recommendations for the assessment for the implementation of Total Quality Management
To initiate with, leadership present in the organization should be assessed in the areas of Company Mission, Vision, and Values, Senior Management Involvement, Leadership Feedback and Improvement, Living the Mission, and Public Responsibility. Strategic Planning should be addressed in the following areas within the organization if total quality management is to be established as the organization-wide management philosophy.
Company-Wide Success Drivers and Performance Measures, Strategic Plans, plan deployment, and monitoring progress to plan. With regard to Customer Satisfaction, an organization evaluating its standing for the implementation of total quality management should be concerned with the areas of Market Research, Product Design Processes, Customer Satisfaction Drivers, Customer Relationship Management, Customer Satisfaction Measurement, Sharing of Customer Satisfaction Feedback and Customer Satisfaction Results.
In the area of Performance Management, an organization wishing to implement Total Quality Management needs to assess itself in the areas of Creating High-Performance Work Processes, BenchMarking Business Processes, Performance Management, Process Improvement, Improvement Results, and Financial Improvement Results. Factors that an organization should consider with regard to Quality Construction Process include Setting Quality Expectations, Assuring Quality Results, Quality Problem Prevention, Warranty Service, and Product and Service Quality Results.
List of References
Born, G. (1994) Process management to quality improvement: the way to design, document, and re-engineer business systems. J. Wiley.
Comité euro-international du béton. (1998) Quality Management: Guidelines. Thomas Telford.
Creveling, C. M., Slutsky, J. and Antis, D. (2002) Design for Six Sigma: in technology and product development. Prentice Hall PTR.
Dawson, P. and Palmer, G. (1995) Quality Management: The Theory and Practice of Implementing Change. Longman Australia.
George, S. and Weimerskirch, A. (1994) Total quality management: strategies and techniques proven at today’s most successful companies. Wiley.
Gitlow, H. S. (2000) Quality management systems: a practical guide. CRC Press.
Goddard, W. and Melville, S. (2004) Research Methodology: An Introduction. Juta and Company Limited.
Goetsch, D. L. and Davis, S. (2005) Quality Management. Prentice Hall PTR.
Hakes, C. (1991) Total quality management: the key to business improvement : a Pera International executive briefing. Springer.
Ismail S. and Maling, E. (2001) An investigation of the total quality management survey based research published between 1989 and 2000. International Journal of Quality & Reliability Management 19, (7) 902-970.
Ketchen, D. J. and Bergh, D. D. (2004) Research methodology in strategy and management. Emerald Group Publishing.
Kothari, C. R. (2005) Research Methodology: Methods & Techniques. New Age International.
Lawler, E. E., Mohrman, S. A. and Ledford, G. E. (1992) Employee Involvement and Total Quality Management: Practices and Results in Fortune 1000 Companies. Jossey-Bass.
Lighter, D. E. and Fair, D. C. (2004) Quality management in health care: principles and methods. Jones & Bartlett Publishers.
MacDorman, L. C., MacDorman, J. C. and Fleming, W. T. (1995) The quality journey: a TQM roadmap for public transportation. Transportation Research Board.
Nanda, V. (2005) Quality management system handbook for product development companies. CRC Press.
Oakland, J. S. (2003) Total quality management: text with cases. Butterworth-Heinemann.
Pande, P. S., Neuman, R. P. and Cavanagh, R. R. (2000) The Six Sigma way: how GE, Motorola, and other top companies are honing their performance. McGraw-Hill Professional.
Pyzdek, T. (2003) The Six Sigma handbook: a complete guide for green belts, black belts, and managers at all levels. McGraw-Hill Professional.
Rajendra, N., & Babu. (2006) Total Quality Management. New Age International.
Rogers, R. E. (1995) Implementation of total quality management: a comprehensive training program. Haworth Press.
Ross, J. E. and Perry, S. (1999) Total quality management: text, cases, and readings. CRC Press.
Williams, B. R. (1994) Essentials of Total Quality Management. Amacom.
List of figures
- Figure 1: The four fundamentals of Total Quality Management.
List of Tables
- Table 1: Which of the following areas of the Employee level of an organization level do you consider Total Quality Management to have the most significant implications upon?
- Table 2: Which of the following areas of the Process level of an organization level do you consider Total Quality Management to have the most significant implications upon?
- Table 3: Which of the following areas of the organization-wide level of an organization level do you consider Total Quality Management to have the most significant implications upon?.