Introduction
Japan has been successful in its manufacturing industry over the past years, with its carmakers like Toyota controlling the automotive market for a long period. This can be attributed to the management practices and business models adopted by its manufacturing industries. The rapid growth in the manufacturing industry in the country has clearly borrowed from the Toyota model and the management practices adopted by the company. The same trend has been witnessed in other Asian nations whose industries have been thriving very well against their Western competitors.
Western countries, on the other hand, have emerged as leaders in the service industries with robust financial institutions and effective regulations. This paper will, therefore, try to examine the Japanese Management practices with a keen interest in its giant automobile maker Toyota. It will also identify the key strengths and weaknesses of the Japanese Management practices and compare them with those of the Western countries. The paper will also provide statistics about the key successes made by the application of the various management theories and practices.
The study will, therefore, seek to merge the positive aspects of the Japanese and Western Management practices to come up with a universal theory that will set new standards in international management.
Discussion
Toyota is the current world leader in the manufacture of automobiles and accounts for more than 15% of world automobile production. This remarkable performance was achieved within a short period of time thanks to the change of its management and production processes from being just a mass producer of cars to a manufacturer of quality cars that sells the world over. The management had to transform its systems from the Toyota production system to a Toyota way model, which has since become one of the most respected models in management and production planning.
Japanese Management Practices
The paradigm shift in its management processes finally paid off when the company became the world leader in automobile manufacturers and also leading in quality, productivity, and profitability. The Toyota way model is developed in four main pillars that define the key factors to success in its operations. They include philosophy, process, people and other partners, and problem-solving.
Philosophy
The company management style is strongly anchored in the long term, and hence the firm handles all aspects of management from a long-term perspective. In this regard, the company has developed processes that ensure that all stakeholders exhibit a sense of purpose in the company; therefore, they take responsibility for the future direction of the firm. The company also focuses on the future of its customers, who are the most important stakeholders in the company activities.
Process
The company has always strived to continuously improve its production processes in such a way that wastes are minimized, and hence visual management is a key component in its processes. This ensures that all processes in the production system are under control. The firm has, therefore, managed to improve the quality of its products as well as its performance. The guiding factors have been lean production systems that ensure efficiency in the utilization of all resources involved in the production process. Toyota has been the pioneer of processes such JIT, Automation, and Kaizen, which have been used to improve its production systems.
People
The company puts a lot of emphasis on its people and other partners and recognizes the critical role that people play in the company’s success. The company has, therefore, defined the key factors that guide its relationship with human resources. They include challenges, respect, and grow them. In this regard, Toyota provides a working environment where its staff can freely explore their talents and challenge their thinking and bring in new ideas in the processes. The firm also respects its employees and tries to keep them along as possible. Promotions are based on years of service; hence there mutual respect among the members of staff. Contrary to other practices, the company will never retrench its workforce, and this gives all staff a sense of security (Pheng and Shang, 3).
Problem-solving
This is related to its second principle of enhancing its processes. The company has developed various tools that can be used to improve its processes to ensure high-quality productivity. Toyota has developed processes for continuous improvement in all stages of its production system. The firm is guided by five steps to problem-solving. They include:
- Finding out what is happening on the ground
- I am trying to find explanations for the happenings or underlying causes of defects in processes.
- Establishing various alternative solutions to the problems
- Engaging in team deliberations to reach consensus on the next action
- We are using the power of communication to implement the agreed solutions.
The above principles have led to remarkable success seen in Toyota and forms part of global practices that can lead to success in the management of organizations.
The Japanese management practices have been clearly demonstrated by the Toyota case and the subsequent successes that the company has gained over the past ten years. It’s, however, worth noting that management theories and practices existed for over 100 years, with western nations leading the pack in discoveries on management best practices. Western management thinking is mainly contained in the four schools of thought developed by different authors. They include the classical management school of thought, the human relations approach, the contingency theory, and the systems approach. All four management theories were based on production systems and tried to come up with the best practices in the management of production systems.
Western Management Theories
Classical theory
This management practice was developed by Taylor in early 1911. The classical approach to management was developed during the industrial revolution in the US and became a key pillar in the expansion of industries in the country during that period. This theory emphasized the application of scientific methods of solving problems in the production systems. The key aspects of this theory included: Scientific allocation of duties and corresponding wages, Application of scientific methods in solving management and production challenges, systematic training and education that could rationally determine the work rate and production capacity per worker, and cooperation among the stakeholders to ensure that production processes are driven accordingly.
The scientific approach to management was supported by well-organized bureaucracies that provided controls. This approach provided formal groupings within an organization that was independent; hence there were high levels of specialization in the management and production processes.
Human relations approach
This theory of management was mainly anchored in the human resource management side and the important role that people play in organizations. It was, therefore, based on how to motivate employees and enhance their commitment to the organizational work. The approach recognized the importance of collective decision making in an organization.
Systems approach
This theory attempted to reconcile the classical and human relations approach. In this regard, it considered organization as a system that comprises many subsystems which must work together to achieve the ultimate goal of the organization. It therefore covers both human and operational concerns in a business.
Contingency theory
This was a continuation of the systems approach and emphasized on the ability of organization systems to operate without interruptions. The contingency theory therefore explains how organizations can continuously review their operational environments and make necessary adjustments for the better. It therefore thrives on extensive research about production and management processes.
The four management theories can be combined to make up the larger western management practices. It’s however worth noting that they address specific areas of management. The human relations approach for instance deals with the human side of management and has nothing to do with other organizational processes such as production and efficiency.
Matching the two practices
The Japanese management practice on the other hand addresses all the aspects of management comprehensively and this has been seen in the success of Toyota. The Japanese framework comprises of the following key aspects: External forces such as industrial organization, cultures and government structures. This is depicted by the strong philosophy which is one of the guiding principles of Toyota way of management.
The Japanese management practices also make use of the general management practices such long term planning, well organized structures and control systems. Another important aspect of the Toyota way is the manufacturing systems which are highly automated. The firm uses systems such as Just in Time, Total Quality Control, Kaizen and the Quality Control Circles among others to achieve efficiency in its production processes.
Just like the human relations approach the Japanese management practices are anchored on strong human resource policies. They therefore advocate for long life employment practices and well defined career paths that are based on seniority.
Based on the above practices, the Japanese management differs sharply with that of the Western Counterparts with the main areas of difference being their philosophy, processes, people relations and their problem solving techniques.
Recommendation
The comprehensive management practices that covers all aspects of the organization has been the driving force to success in the Country’s Manufacturing industry which has seen Toyota grow rapidly to become the world leading automaker. Although the Western Management practices are also very important, they are disjointed and only address specific areas of management. This makes them in appropriate for global management challeneges.Its therefore advisable that countries adopt the Japanese style of management as this is the only way of addressing the dynamic management challenges.
Exhibits
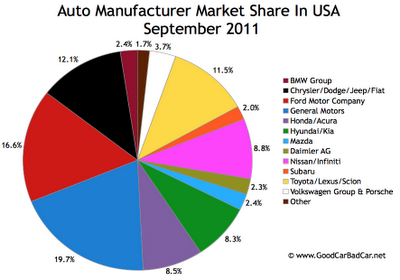
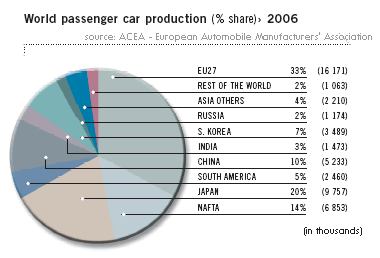
Global Car productivity since 2000:
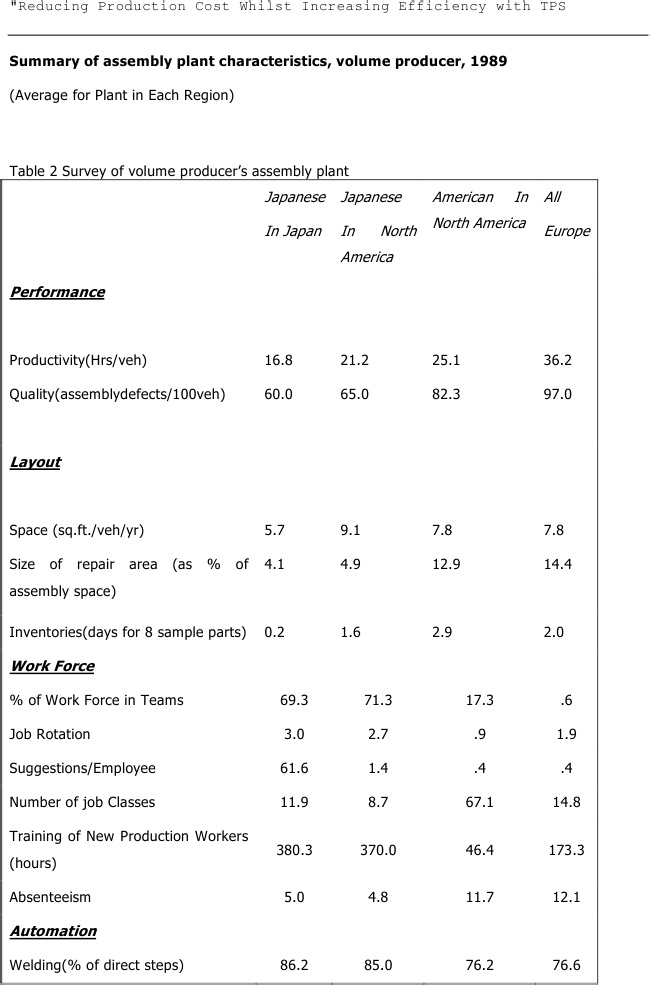
Work cited
Pheng, L.Sui and Shang,Gao. ”Bridging Western Management theories and Japanese Management Practices: Case of the Toyota Way Model.” Emerald Emerging Markets Case Studies.1(1). Emerald Group Publishing Limited, 2011.