Role of systems and operations management
Strategic management and systems and operations management are integral functions in any large company and are implemented collectively (Greasley 2007, 9). Strategic administration is that set of managerial decisions and measures that determine the long-run performance of the institute. It includes ecological scanning (both peripheral and domestic), strategy formulation (strategic and long-range planning), strategy execution, end evaluation, and control (Mahadevan 2005, 49). Large organizations have the task of integrating their departments and systems in a manner that will ensure the efficient and effective use of resources in order to derive the desired overall organizational goals (Steiner 1997, 88).
Airbus systems and operations management falls under the company’s functional strategy. The functional strategy is the approach taken by a purposeful area to accomplish corporate and trade unit objectives by maximizing resource output (Kerzner, 2009, 11). Functional strategies are involved in emergent and development of the distinctive competencies that will provide the company with a competitive advantage (Porter1998, 35). In Airbus, the various departments work independently of each other, whereby the output from given departments end up being used as inputs of other departments. Airbus has numerous assembly points and factories located in different countries in Europe (Slack et al. 2010, 18).
From a systems point of view, the output from one department should meet the requirements of the next department, through input-output analysis. This means that if the output from one department is defective, then the output of the whole organization will end up being negatively affected. Though departments are independent of each other, they should work collaboratively to ensure the attainment of the overall organizational objectives. Whenever a particular Airbus plant experiences a delay in manufacturing over the lead time, then the manufacture of the A380 Airbus planes will be overdue, hence making the organization incur avoidable losses because of lost customers and hence revenues (Mahadevan 2005, 56).
Operations management in the manufacturing industry deals with the management of production activities to ensure that they run smoothly without disruptions. Systems and operations management will tend to concentrate on the integration of the various departments and operational units in an organization through scheduling and coordination of activities and the allocation of resources (Teece 2008, 105). The efficient and effective allocation of resources throughout the organization may lead to cost savings and the production of high-quality products. In the aircraft manufacturing industry, safety is an important factor to put into consideration in the production process. The various Airbus factories may have to coordinate and ensure that parts produced meet the utmost quality requirements in order to meet industry requirements, as well as secure the firm’s reputation for manufacturing the best planes (Kerzner 2009, 46).
A good way to begin an organizational analysis is to ascertain where the Airbus’s products are located in the overall value chain. For Airbus, the value chain is the linked set of value-creating activities beginning with the basic raw materials coming from suppliers, moving on to a series of value added activities involved in producing and marketing the airplanes to prospective customers, and ending with distributors getting the final airplanes into the hands of the ultimate customer, in this case the airline companies (Sinkovics & Ghauri 2009, 64). Several support activities, such as procurement, technology development (R&D), human resource management, and firm infrastructure (accounting, finance, strategic planning) ensure that the primary value chain activities operate efficiently and effectively (Trott 2008, 38).
Each of a company’s product lines, for instance Airbus, has its own distinctive value chain (Capman 2005, 63). Because most corporations make several products or services, an internal analysis of the firm involves analyzing a series of different value chains. The systematic examination of individual value activities can lead to a better understanding of Airbus’s strengths and weaknesses. Corporate value chain analysis involves a number of steps, starting off with the evaluation of each product line’s value chain in terms of the various activities involved in producing that product or service. Charles et al,(2009, 72). Airbus has several factories located in different European countries, which all work towards adding value to the various Airbus A380 components.
Airbus should examine the linkages within each product or process in the value chain. Linkages are the connections between the way one value activity, for example marketing, is performed and the cost of another activity, for example cost control. In seeking ways for Airbus to gain competitive advantage in the marketplace and overcome operational interruptions, the same function can be performed in different ways with different results (Charles et al, 2009, 61).
For instance, quality inspection of 100 percent of output by the Airbus engineers themselves instead of the usual 10 percent by quality control inspectors may increase production costs, but that increase could be more than offset by the savings obtained from reducing the number of repair engineers needed to fix defective products and increasing the amount of sales personnel’s time devoted to selling instead of exchanging already sold but defective plane parts (Hakes 2005, 63).
Airbus could also examine the potential synergies among the value chains of different business units. Each value element, such as advertising or manufacturing, has an inherent economy of scale in which activities are conducted at their lowest possible cost per unit of output. If the Airbus A380 is not produced at a high enough level to reach economies of scale, than another plane could be used to share in the same production chain. This is an example of economies of scope, which result when the value chains of two separate products share activities, such as the same marketing channels or manufacturing facilities. For instance, the cost of joint production of numerous products can be less than the rate of separate production (Barkley 2004, 46).
Business process mapping in systems and operations management reveals the critical path in which the various Airbus A380 components are to be manufactured. The critical path method illustrates the key activities and the scheduling of such activities in project management. The critical path method takes time durations into consideration in the development of schedules (Campbell & Stonehouse 2002, 38), and in so doing management will be in a better position to establish or estimate a completion date for the project. The Airbus A380 project overrun its completion date, and often slipped the delivery schedules of the planes to its customers.
The delays in delivery of the planes are an indication that there are potential problems in coordination of the various factories and poor integration of production activities within Airbus. For example, the French and German plants implemented various incompatible computer systems in designing the cable system of the Airbus A380 during the initial design process (Blyth 2009, 77). This proves that there is a lack of integration and effective communication between the design and manufacturing processes, and this could be a major reason for the delays in the launch of the Airbus A380. As a result of the cabling problems, Airbus had to transfer two thousand German staff from Hamburg to Toulouse to resolve the problem, resulting into further delays in the production schedules and increased costs (Kerzner 2009, 63).
How Airbus information and operations management systems can be improved
The difficulties experienced by Airbus suggest that there are communication and integration problems within the organization (Slack et al 2010, 49). There were reported conflicts between the German and the French employees, which could have led to unhealthy internal competition and conflicts of interest within the aircraft manufacturer’s staff. Airbus has experienced incremental costs as a result of the production delays, and thereby overrunning the company’s estimated production budget. Airbus revealed that the project would cost £12 billion, which was £1.45 billion over the budget due to the delays in production (Anonymous 2003). Airbus will have to re-evaluate its systems in order to identify the root causes of the poor integration and coordination of the production factories if they are to prevent the reoccurrence of similar delays in future projects.
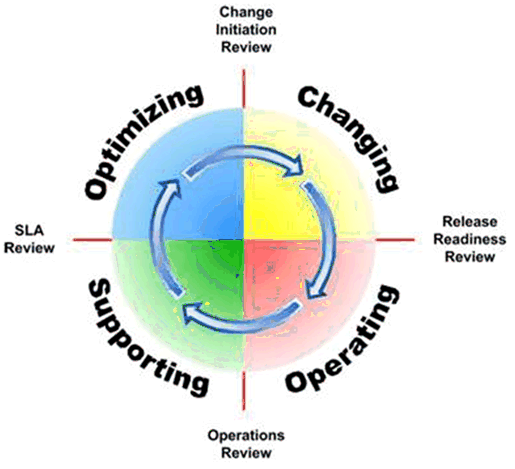
Scanning functional resources could begin with an analysis of the organization’s value chain by carefully examining its traditional functional areas from potential strengths and weaknesses. Functional resources include not only the financial, physical and human assets in each area, but also the ability of the people in each department to formulate and implement the necessary functional objectives, strategies and policies (Sinkovics & Ghauri 2009, 67). The resources consist of the knowledge of analytical concepts and bureaucratic techniques familiar to each department as well as the capability of the staff in each department to use them efficiently. If properly used, these resources serve as the strengths to carry out value added activities and support strategic decisions.
In addition to the usual business functions of marketing, finance, research and development, human resources and information systems, the organizational structure and culture form key parts of a business corporation’s value chain (Greasley 2007, 54). Airbus’s corporate culture provides little room for co-operation and performance within the company since it gives rise to conflicts between the different departments, in this case, between the French and the German factories. The corporate culture is the assortment of values, expectations and principles cultured and shared by a corporation’s associates and transmitted from one generation of workers to another (Deal & Kennedy 2000, 47). The corporate culture generally gives the company a sense of identity. Corporate culture has two distinct attributes; intensity and integration. Cultural intensity is the degree to which members of a unit accept the norms, values and other culture content associated with the unit (Ireland 2006, 26).
Cultural integration is the extent to which units throughout the organization share a common culture. This is the culture’s breadth. Airbus’s departments fall within different countries in Europe, giving rise to differences in culture among the various departments. Organizations with a pervasive dominant culture may be hierarchically controlled, power oriented and have highly integrated cultures (Felkins, et al. 1993, 68). This is in contrast to Airbus, which is structured into diverse units by functions and divisions, and therefore exhibits strong subcultures, for example design versus manufacturing, and a less integrated corporate culture. A less integrated culture may lead to communication problems, duplication of tasks and may even develop into conflicts of interest.
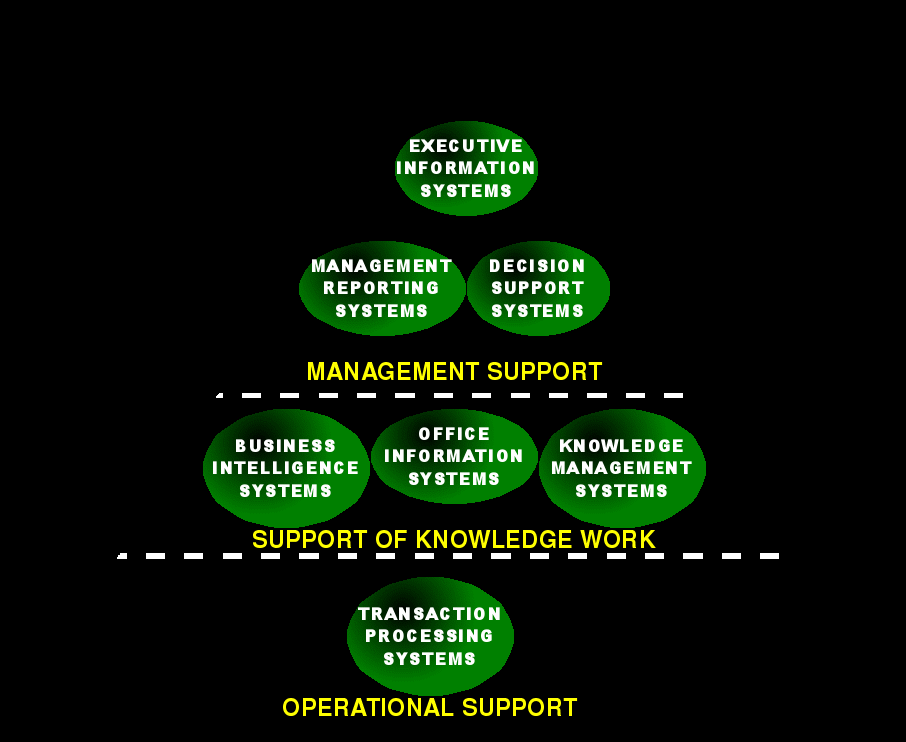
Soft Systems Methodology (SSM)
The soft system methodology may be used to identify specific problems within Airbus of a more complex nature. The major advantage of using the soft system methodology (SSM) is that it takes all the stakeholders into consideration when solving for inefficiencies in the company (Wilson 2001, 15). SSM provides a valid understanding of the organization’s system. Looking at the rich picture in the real world situation, and consequently develops a simple solution to the perceived problems within the organization. Airbus faces a number of challenges, such as the differences in cultures between its production facilities in the different European countries, distances between the factories and also the political implications of operating a large company in different countries.
The soft system methodology is used simultaneously with CATWOE, which is an acronym for clients, actors, transformation, worldview, owner and environmental constraints (Wilson 2001, 39). All stakeholders are represented in the CATWOE acronym, so their demands and requirements will be put into consideration in developing an operations and systems management strategy for the company. lack of coordination of the company’s various departments has made it a big challenge for the management to coordinate its activities towards achieving the large company’s goals, thus leading to holdups in its operations (Slack et al 2010, 54). The soft system methodology will recommend the information requirements of the organization and thereby facilitate the implementation of an information system that will improve communication and coordination among the enterprise’s factories.
Airbus will be in a better position to prioritize on key activities, and ensure that all departments meet established completion due dates. Planning will be more efficient since there will be more integration of the various units within the company. The primary task of the operations manager is to develop and operate a system that will produce the required number of components in the Airbus A380 project, with the specified quality, at a given cost, within the scheduled time frame. A strategic audit of the company could also be used to conduct an organizational analysis of Airbus in order to ascertain the company’s strengths and weaknesses (Deal & Kennedy 2000, 73).
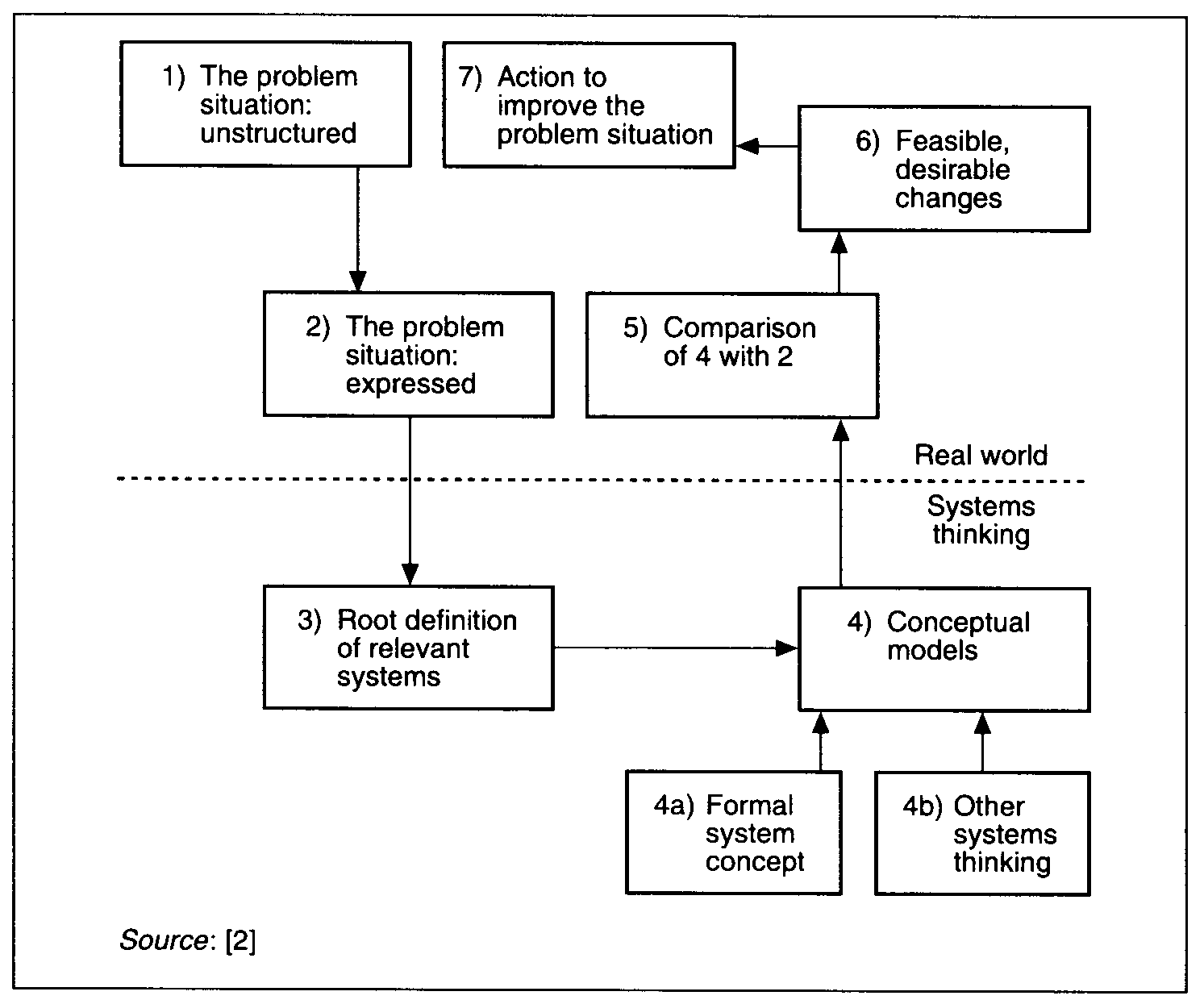
The soft system methodology can be used as a guiding tool in changing Airbus’s organizational design, information systems and integration and coordination of activities within the manufacturing company (Wilson 2001, 129). Airbus has experienced numerous problems in the A380 project, starting from lack of coordination, overrunning the project budget, and production delays that further upset the company’s stakeholders. SSM takes the needs of the various stakeholders into consideration in the development of a possible solution to the current problems. If the needs of all the stakeholders can be accurately be determined, then SSM can come up with a solution that will beneficial for all departments and stakeholders of the company. Airbus’s operations are divided among European countries, specifically France where the final assembly plant is located, Germany and the UK (Mahadevan 2005, 167).
As such, differences in culture and political differences are likely to arise, causing the integration process to be more difficult. SSM starts its problem solving technique by identifying the root cause of each problem, and then inputs the needs and requirements of the incorporated systems in the organization (Steiner 1997, 241). The second stage of SSM includes the expression of the problem situation, usually through rich pictures. Rich pictures assist the soft system methodology process by capturing all the relevant information pertaining to the identified problem, showing restrictions, information flows, organizational structure and the human activity system.
CATWOE helps the SSM process by summing up the root definitions and needs of the identified stakeholders (Camillus 1986, 176). Soft systems methodology has other advantages, for example it provides a valid structure for complex problematic situations, it suggests workable project management strategies and defines the information needs of the system, and can also be used as a performance evaluation tool. Despite its usefulness and benefits, SSM has a couple of limitations. For instance, SSM requires input from all participants which may necessarily not be attainable (Barkley 2004, 69).
The project manager may also have difficulties in assembling the rich picture without imposing a solution to the situation based on his experiences with the organization, meaning that the rich picture may not be as comprehensive as required. The SSM and CATWOE systems may be applied to Airbus to establish the causes of delays in the production and delivery of the planes, and also identify the causes of the lack of proper co-ordination within the company’s French and German factories (Greasley 2007, 98). The soft systems methodology may subsequently be used to design an organizational structure that will lead to the integration of the various production units in the company, and hence the timely accomplishment of the project.
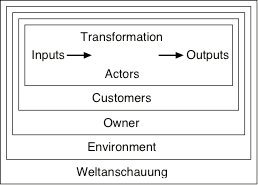
Airbus people, technological and organizational issues
How an organization manages its resources will determine how effectively and efficiently it can conduct business and achieve the set corporate targets (Blyth 2009, 32). Instead of developing planes in a series of steps, beginning with a request from sales, which leads to design, then to engineering and on to purchasing, and finally to manufacturing which could result into high loses when the plane is rejected by customers, Airbus could tear down the traditional walls separating departments so that people from each discipline can get involved in projects early on (Teece 2008, 141).
Through concurrent engineering, the once isolated Airbus specialist engineers can now work side by side collaboratively and compare notes in an effort to design cost effective and high quality plane components with features that customers and the parent company want (Capman 2005, 33). Through this approach, Airbus could reduce its product development cycle by several months through integration and cooperation of departments, which gives rise to team work.
People issues are highly critical to an organization. Technology has advanced and the extent of people’s activities has increased such that nowadays human factors issues are possibly more multifaceted. Airbus considers the Human Factors in the design, development, function and running of its planes. This involves a dedication from the highest levels of its organization to a Human Factors procedure encompassing all its functions. Airbus has tested this obligation by a formal and autonomous audit to make sure the Human Factors procedure is entirely put in place in all its operations. The aim of its human factors plan is to make sure that companies operating Airbus plane are assured of the utmost level of safety.
Management information systems and technologies help design and manage the flow of information in an organization in ways that improve productivity and decision making. In the current production sector, technology comes in handy and offers a competitive advantage to those who can effectively utilize technology; however poor implementation of technology can be a disadvantage to an organization. For example, the issues happening in the French and Germany plants are due to a lack of proper coordination and adoption of incompatible computer systems. Airbus needs to properly integrate its distant plants and coordinate their operations effectively; for instance, it could implement an Enterprise Resource Planning system that will manage all of its various activities together.
Airbus needs to invest in the latest technology if it is to efficiently manufacture and assemble quality components of its A380 planes (Teece 2008, 97). Using outdated technology may result in high costs and defective parts, which may result in high replacement costs, safety issues for the planes, and loss of market share due to a tarnished reputation (Camillus 1986, 84). Airbus needs to produce its products with zero defects, and accurate precision is needed, so proper production procedures needed to be followed with no room for mishaps.
Managing a large organization like Airbus is an intricate and multifaceted issue, and the recognition of their nature and major operations and processes is vital both at the preliminary facts finding stage of MLE creation and all through the projects execution. Hence, organizational issues deal with how well the design and manufacturing process is organized and managed (Jones 2010, 41). Poor harmonization of the French and the German plants causes major communication and incorporation problems between the different divisions and has even led to disagreements and production slugs.
Political interference, particularly by the French and German governments (Slack et al. 2010, 18), is also a potent problem for the company, as political forces try to manipulate the company’s policies. The company needs to create rapport with the governments and adhere to the local legislation and offer opportunities to the local markets. The company’s corporate culture may be evaluated in order to promote the sharing of information and co-operation between the various departments (Deal & Kennedy 2000, 63). In addition, Airbus needs to enable capacity building within the organization based on developing and putting in place efficient plans and procedures, which will see the organization better control its operations and its resources – capital, human resource, and assets, among others.
References
Anonymous, 2003. “Airbus A380 cost overruns of 1.45 bln euros”. PPRuNe. Web.
Barkley, B., 2004. Project risk management. New York: McGraw-Hill Professional.
Blyth, M., 2009. Business Continuity Management: Building an Effective Incident Management Plan. New Jersey: John Wiley and Sons.
Camillus, J., 1986. Strategic planning and management control: systems for survival and Success. Lexington, KY: Lexington Books.
Campbell, D. & Stonehouse B., 2002. Business Strategy: An Introduction, 2nd ed. Banbury Rd: A Butterworth-Heinemann.
Capman, C. S., 2005. Controlling strategy: management, accounting, and performance measurement. London: Oxford University Press.
Charles, E. et al, 2009. Essentials of Marketing. Natorp Boulevard: Cengage Learning.
Deal, T. E. & Kennedy, A. A., 2000. Corporate Cultures: The Rites and Rituals of Corporate Life. Cambridge: Perseus Publishing.
Felkins, K. et al. 1993. Change Management: A Model for Effective Organizational Performance, Quality Resources. New York, NY: White Plains.
Greasley, A., 2007. Operations Management. London: Sage.
Hakes, C., 2005. Total quality management The Key to Business Improvement’s. Suffolk: Edmunds bury Press Ltd.
Ireland, L. R., 2006. Project Management. New York: McGraw-Hill Professional.
Jones, G., 2010. Organizational theory, design, and change. Upper Saddle River: Pearson.
Kerzner, H., 2009. Project Management: A Systems Approach to Planning, Scheduling, and Controlling, 10th ed. New Jersey: John Wiley and Sons.
Mahadevan R., 2005. Operations Management: Theory and Practice. New Delhi: Pearson Education India.
Porter, M. E., 1998. Competitive strategy: techniques for analyzing industries and competitors. New York: The Free Press.
Sinkovics, R. & Ghauri N. P., 2009. New Challenges to International Marketing. London: Emerald Group Publishing.
Slack, D. et.al. 2010. Operations Management, 6th Ed. Harlow: Pearson.
Steiner, G., 1997. Strategic planning: what every manager must know. New York, NY: Simon and Schuster.
Teece, D. J., 2008. Technological know-how, organizational capabilities, and strategic. Kuala Lumpur: World Scientific Publishing Co.
Trott. P., 2008. Innovation Management and New Product Development, 4th edn. London: Pearson.
Wilson, B., 2001. Soft Systems Method: Conceptual model building and its contribution. Chichester: John Wiley and sons.