Outline
Country Classics, a furniture company with customized and standard furniture offerings is faced with the problem of not being able to cope with orders and also declining profits in its standardized furniture section. A team was formed to look into the problems and this paper forms their recommendations regarding solving the problems. They include sales forecasts, production planning, changes in plant layout, inventory control, productivity improvement, budgetary costing etc.
Introduction
The case study relates to the production and operation management problems faced by a furniture manufacturing company owned by Mrs. Gail Beaumont. The Company is known as Country Classics. The company has two product lines namely the standard furniture and customized furniture. There is enough demand for both these product lines and the manufacturing capacity of the firm is limited. The first problem faced by the company is how to allocate the scarce resource of company between these two product lines. The second problem faced by company is reduced profit margin from the standard furniture product line in spite of higher sales volume.
In the context of the above two problems the owner of the company had brain storming analysis with departmental heads as to how to come out of the present crisis. The managers were requested to offer solutions in the following key areas.
- What types of daily decisions must Gail Beaumont make for her company’s operations to run effectively?
- How did sales and marketing affect operations when they began to sell standard pieces to retail outlets?
- How has the move to produce standard furniture pieces affected the company’s financial structure?
- What might Beaumont have done differently to avoid some of the problems she now faces?
A task force was constituted with finance manager, marketing manager, production manager and human resource manager as members and owner Gail Beaumont as chairperson. The recommendation of the task force is the core of this case study. In the task force committee meeting the finance manager explained that they are losing heavily on inventory carrying cost in the standard furniture line and proper inventory control should be exercised. The marketing manager explained that there is heavy competition in the standard furniture line hence profit margin has to be low in line with their competitors. In spite of the low profit margin there is an assured market unlike the customised furniture line which depends upon the whims and fancies. He argued that the manufacturing cost has to be controlled to have an optimum profit margin to boost the low profit margin. The production manager explained that he finds it difficult to allocate capacity between these two product lines. While batch production technique can be utilised for standard furniture it cannot be used for customised furniture line, where the setup cost is high. The human resource manager wanted the labour productivity to be increased by having more and more quality circles.
The owner of the company having heard views of the departmental heads observed that the overall productivity of company’s operation could be improved by better production planning, rearrangement of layout, applying statistical techniques to market research, and ABC analysis of inventory. The Task Force was requested to draw up an overall action plan to include the above suggestions. She also wanted a budgetary costing system to focus on operations that escalate cost. The task force met on the first day of every week to review the implementation program and the company could make a turnaround in sales and profit. Operation management techniques could boost the operations of the company.
Operation strategy review
It is the long term plan for using the major resources of the firm for a high degree of compatibility between these resources and the firm’s long term corporate strategy. Some of the long term issues include:
- How large do we make our facilities?
- What type of process do we install to make the products?
- What will our supply chain look like?
- What will be nature of our workforce?
- How do we ensure quality?
Customers want more than the money’s worth and the more they receive for their money the more value they see in the goods they purchase.
Sales forecast
Starting point of any production is the sales forecast. Sales forecast is required for the following purposes:
- To know the likely demand of the finished goods in the market
- To know the requirements of the raw material necessary in the production and for the inventory levels.
- To make decisions on working capital needs
- To make decision about the size of workforce
- To take decision related to production planning and control
- To take decision about the location of facilities, the amount of advertising and sales promotion and the need to change prices etc.
- To determine the most economical production design of products, process, equipment, tooling, capacities and layouts.
Present forecasting method
The present practice of the company is to project a demand for current quarter based on the simple average of the last three quarters.
Suggested forecasting method
As the recent data contains more information than the old data management thought it prudent to assign different weightage for different periods. For example, if the demand for the first three quarters are 500, 600 and 700 respectively, then the demand for the fourth quarter will be (500+ 600+ 700)/3= 600. The management gives a weightage of 0.50 for the last quarter and 0.25 for the previous two quarters to project the impact of demand on the latest quarter. According to the weightage average method the demand for the fourth quarter will be 0.5x 700+ 0.25 x 600 + 0.25 x 500 =625. The weighted average method is more scientific than the simple average because it gives prominence to recent trends instead of blindly depending upon old performance. This method is successful for the standard furniture product line.
Production planning
- Production for stock: as the name implies, the finished parts are stocked and the customers are served from an inventory. For this a forecast of future customer demand is required and the parts are produced by keeping this forecast in view.
- Production for customer order: under this system, the process of production planning and control starts only after a confirmed customer order is received. However, such an approach will be impractical. If no work were done prior to the receipt of an order, it will be very difficult to meet the due date of the customer. To overcome this problem, it is customary to stock a certain amount of raw material, and in most cases, common parts are maintained in a finished or semi finished state. In this system, frequently all customer orders received during a given period (a week or month) are grouped for batch production of common parts in order to achieve greater production economies. The system for controlling production orders for finished goods has to provide the eventual control of individual customer orders. This usually means a more costly control system if production output does not approximately coincide with customer delivery requirements. ( a production model for a flexible production system and products with short sealing season). (Spencer, & Carlan 2008).
Plant layout
“The basic types of layouts are process layout, product layout, fixed position layout, cellular manufacturing layout and hybrid layout.” (Operations management: Chapter 6: Facility location and layout 2009). When similar types of machines in a factory are put together it is called process layout. In many cases, production is done in steps. When machinery is laid out according to the progressive steps, it is known as product layout. In more complicated production processes, different types of machines are put together, referred to as cells. In such cases, each cell will be more or less similar to a product layout. This type of layout is known as group technology layout. In some cases, everything related to production including men, machinery, and materials are put in a single location. This location is the place where the product will be made. This is referred to as fixed layout. When there is a combination or mix of one or more of the above mentioned layouts, it is referred to as a hybrid one. A major issue to be addressed in facility layout decisions in manufacturing is: How flexible should the layout be to adjust to future changes in product demand and product mix? Some have argued that the best strategy is to have movable equipment that can be shifted easily from place to place to reduce material flow time for near term contracts. Though this is appealing in general, the limitation of existing buildings and permanently anchored equipment, and the general plant disruption that is created, makes this a costly strategy.
The present layout
As the firm manufactures light weight furniture, the present system is product layout in which equipments and processes are arranged according to the progressive steps by which the product is manufactured.
Suggested layout
To minimise interdepartmental material handling cost, a new technique known as CRAFT (Computerised Creative Allocation of Facilities Techniques) can be used. Since layout problems in practice can be quite complex, software is required for designing effective layouts. Factory FLOW, Factory PLAN, Factory OPT and LAYOPT are examples of commercial softwares. (computerised analysis of discrete MRR optimisation for constrained due date) (Syung Lan 2008, p. 2606-2612).
Inventory control
Inventory is money in the form of raw materials, work-in-process and finished goods. Although zero inventory is an ideal situation because of the uncertainties of the market, there are two types of inventory system; they are fixed order quantity and fixed time period model. The basic distinction between the two is that the fixed order quantity model is event triggered and the fixed time period model is time triggered. That is the fixed order quantity model initiates an order when the event of reaching a specified reorder level occurs. This event may take place at any time, depending on the demand for the items. In contrast, the fixed time period, only the passage of time triggers the model. Advance information technology, including the bar-coding of products, bar code scanner and point of sale computers, have greatly reduced the cost and facilitated the use of the fixed order quantity model. As a result, there has been an increasing trend towards the fixed order quantity model, and away from the fixed time period model.
- L is the lead time
- R is the reordering level and Q is the number of units on hand.
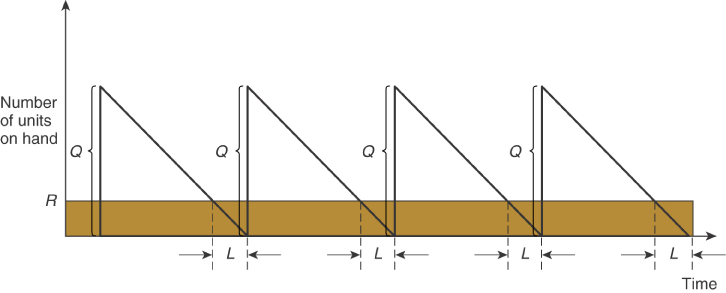
The fixed time model typically has a larger average inventory since it also must protect against stock out during the review period. The fixed time period model is preferred when several different items are purchased from the same vendor, and there are potential economies of scale savings from ordering all these items at the same time. The fixed order quantity model is preferred for more expensive items because average inventory is lower.
Country Classics has been following fixed time period model for both standard furniture and customized furniture components. The task force suggested to reduce inventory they would go for fixed order quantity for customized furniture components and fixed time model for standard furniture.
Inventory cost
Inventory cost include storage cost, capital cost and obsolescence cost:
Total cost = annual purchase price + annual ordering cost + annual holding cost
Or
TC=DC+D/QS+Q/2H
Where:
- TC= total annual cost
- D= annual demand in units
- C= cost per unit
- Q= quantity to be ordered
- S= setup or ordering cost
- H= annual holding cost per unit
Annual product cost, based on the size of order:
- D = annual demand in units
- S = setup or ordering cost
- H = annual holding cost per unit
(an economic order quantity under joint replenishment policy to supply expensive imported raw materials with payment in advance) (Taleizadeh et al 2008, p. 4263-4273).
This formula is used by Country Classics to decide on the economic order quantity of purchase and also economic batch size for batch production. In the later case S will be the setup cost and in the former case S will be the ordering cost.
ABC analysis
ABC analysis is an inventory system offering a control technique and inventory cycle counting that can improve record accuracy. It is a method for grouping inventory items by dollar value to identify those items to be monitored closely. In Country Classics A items (high value) account for 20% of the total number of items in which 80% of the value is locked up. 30% of the items classified as B account for 15% of value and balance 50% items classified as C items account for 5% of the total value.
The purpose of classifying items into groups is to establish the appropriate degree of control for each item. On a periodic basis, for example, class A item may be more clearly controlled with weekly ordering. B items may be ordered biweekly, and C items may be ordered monthly or bimonthly. Not that the unit cost of items is not related to their classification. An A item may have a high dollar value through a combination of either low cost and high usage or high cost and low usage, similarly, C items may have a low dollar value either because of low demand or low cost. With ABC analysis and EOQ support inventory cost of Country Classics came down drastically.
Productivity improvement
CAD (computer aided design) was used to minimize waste in selecting wood and planning maximum number of items from the same piece of wood. Machineries were rearranged to cater to the demands of standard furniture and customized furniture. Quality circles were formed with the voluntary participation of the workmen and the supervisors. This created a feeling of participative management among the work men and contributed to the improvement of productivity and quality. Theory of constraint scheduling was used to allocate machines for the two distinct product lines of standard furniture and customized furniture. Systematic production planning methods were implemented. (Sadjadi, Aryanezhad & Ziaee 2008, p. 3032-3037).
Budgetary costing
The profit margin for the customized furniture is high compared to the standard furniture. But they had a common costing system for both these items. So the individual contribution of these product lines to the overall profitability of the company was not ascertained. Marketing and production teams had a bias to the standard furniture segment. The task force decided that they will have independent costing system for these two items. Budgetary costing system was introduced in which a budgetary cost is compared to the actual cost and the projected profitability compared with the actual profitability. Each batch of manufactured items was assigned a specific manufacturing order number in which the actual quantity of material used, machinery time used and labor hours used where recorded. This will facilitate to calculate the actual cost of production which can be compared with the budgetary cost. (Quality circle 2009).
Conclusion
The problem faced by the Country Classic is that it has too much orders for low profit line of standard furniture and less orders for customized furniture line with higher profit. The company’s present brand image in standard product line is based on the confidence level among the customers for its customized furniture line which was known for the quality in material and workmanship. Basically the company was geared to manufacture customized furniture and hence they found it difficult to re- arrange the machinery for their standard furniture line.
The task force suggested a linear programming solution to allocate the resources according to the profitability of the individual product line. They also suggested rearrangement of machinery using CRAFT. (Davis, M etal 2004, p.369).
The day to day operations of the company are reviewed by the owner with the departmental heads. The cash flow for the day and the production for the day are specifically discussed. Depending upon the inflow of funds cash was allocated to purchase of materials, pay wages etc. To meet the seasonal demand, employment of additional labour by contract for outsourcing is also discussed. The sales department was requested to speed up the collection of receivables. When the company diversified into standard furniture segment it began to stock standard furniture in retail market. This enabled the company to offer furniture off the shelf to the customers. Although the customers were satisfied the company have to incur high inventory cost. ABC analysis and EOQ model are used to control the inventory carrying cost. When it manufactured customized furniture there were no inventory at all.
The standard furniture line is highly competitive and Country Classic had to face stiff competition from national and international brands. So it had to reduce the profit margin to be competitive. While cost plus profit was the motto for customized furniture, market price – profit was the motto for the standard furniture. To cut the cost, various suggestions are made by the Task Force including productivity improvement, quality circles, budgetary costing control and inventory control techniques. (Inventory management 2007). The problem faced by the owner is mainly extraneous. As she has no control over the external factors. she should analyze the internal problems, labour productivity, plant layout, inventory control, production planning and control, economy of purchase, control of agents’ commission etc.
Reference
Davis, M, Mark etal 2004, Fundamentals of Operations Management = Yun Ying Guan Li Ji Chu, Di 4 Ban, Web.
Inventory management 2007, Business Reference, Web.
Spencer, Dale & Carlan, Niki 2008, The complexities of the automotive industry: positive and negative feedbacks in production system, Canadian Journal of Sociology/Cashiers Canadians De Sociologie, 33, 2, Web.
Taleizadeh, AA et al 2008, An economic order quantity under joint replenishment policy to supply expensive imported raw materials with payments in advance, Journal Applied Science, 8, 23, pp.4263-4273, Asian Network for Scientific Information, Web.
Syung Lan, Tian 2008, Computerized analysis of discrete MRR optimization for constrained due date, Journal Applied Science, 8, 14, pp. 2606-2612, Asian Network for Scientific Information, Web.
Sadjadi, SJ, Aryanezhad, MB & Ziaee, Mohzen 2008, The general flowshop scheduling problem: mathematical models, Journal Applied Science, 8, 17, pp. 3032-3037, Asian Network for Scientific Information, Web.
Quality circle 2009, Answers.com, Web.
Operations management: Chapter 6: Facility location and layout 2009, Case Studies and Management Resources, ICMR, Web.