Introduction to 21st Century Supply Chain
Inventory processing has undergone immense changes in the last century. From a process that was heavily reliant on manual processes, inventory processing has been entirely transformed in the age of information technology. Wait time has been immensely cut down together with operational faults, which lead to customer satisfaction. The passive role of the consumer in the supply chain and processing has been replaced by active participation completed by new standards and expectations (Xiao, Shi & Yang, 2010). Managers integrated into purchasing and logistics as well as other business processes such as marketing and manufacturing.
Supply chain management covers various strategies to ensure efficiency in operations. There is a need to establish appropriate logistics to ensure the success of supply chain management. Logistics encompasses functions that are aligned to proper timing and execution of the inventory (Seuring & Müller, 2008). As such, logistics comprises such functions as order management, transport, warehousing, goods handling as well as packaging. Integration creates economic value by reducing costs, market value by enhancing distribution as well as relevance value that ensures products meet customers’ needs. Integrated logistics operations need to be aligned and well managed in the very first stages of material procurement and inventory delivery (Mollenkopf, Russo & Frankel, 2007).
The logistics activity relies on the supply chain information system which comprises four levels. The first level is the transaction level that ensures all logistics activities are recorded. Some of the activities on the first level include order management, inventory assignment, order selection, pricing, and processing. The second level focuses on the measurement as well as reporting on the operations related to the supply chain. Some of the records include financial costs, quality measurement as well as customer service analysis (Linton, Klassen & Jayaraman, 2007). The next level involves decision analysis that focuses on leveraging information technology to enhance the performance of the supply chain. Some typical analyses include data on the routing of transports, profitability based on the customer segments, networking of facilities as well as third-party outsourcing. The final level is the strategic planning that focuses on activities such as alliance and supply chain formation while building customer relationships. The supply chain information system has several modules that include enterprise resource planning, communication, execution, and planning systems that allow the achievement of objectives of each level.
Role of Supply Chain Logistics. Logistics Value Proposition
Logistics focuses on the design and administration of the system to gain control over movement and positioning of raw materials, work-in-process as well as completed inventories to ensure the lowest possible costs. Logistics plays a significant role in adding value to the supply chain process by ensuring that stocks are placed strategically to achieve higher sales.
Logistics enables organizations to achieve service benefits when resources are provided. When proper logistics is provided, products are delivered to the identified customer in an acceptable time duration. Logistics can enable the organization to perform competitively compared to other groups on the platform of cost-effectiveness (Krause, Vachon, & Klassen, 2009). Proper logistics ensure the availability of the inventory with an increased level of flexibility that ensures customers’ requirements are met. Logistics ensure that there is improved operational performance to meet the delivery of customer orders. Organizations can prioritize which products require more investments in terms of logistics and profit margin. Logistic planning is critical in cost minimization that in turn ensures the general profitability of the organization.
For an organization to be effective in the competitive environment that exists in the business today, the customers and suppliers must be integrated into the enterprise management. The integration of customers and suppliers can only be achieved through logistics operations and as such exemplifies the function of logistics in the broad perspective in supply chain management.
Logistics in supply is connected with several functions that ensure the delivery of inventories to the clients. Some of the functions include movement and storage of materials, work-in-process as well as finished products (Hausman & Thorbeck, 2010). materials move from the supplier to the production process while adding value at every stage to meet the customization requests. Therefore, it can be argued that logistics involves three main steps that include customer relationship management, manufacturing as well as procurement.
Logistics in supply chain management ensures that work-in-process is well managed as materials move through the manufacturing process. Logistics creates a production schedule as well as arranges for the different requirements such as materials and parts to be in stock. The concept ensures that the questions such as what, when, and where are the basis of the process rather than focusing on how production is performed. As such, there is the creation of a manufacturing enterprise within the organization (Seuring & Müller, 2008). Establishing appropriate logistics of the supply chain management strengthens the procurement of materials from the suppliers. Procurement is similar to the process of purchasing, with only one difference that supply occurs in the government sector while purchasing is in the public sector.
The flow of information in logistics and supply chain management plays a role in identifying a particular location within the system that is needed to be modified. The information also plays a role in integrating different operating areas of the supply chain management and procurement functions. Information is critical to the ability of the organization to satisfy primary customer demands that are regarded as responsiveness. As such the organization can create a response based on strategies that ensure that there is a higher level of operational commitment that in turn accelerates the delivery of goods.
Logistics management is critical to the reduction of variance. The variance occurs as a result of failure to perform certain functions of the operations that are necessary to ensure that all customer’s requirements are met. Disruptions of the services, as well as its operations, are eliminated within the organization. The logistic system also ensures that assets are committed based on the financial value of the inventory that is needed (Hausman & Thorbeck, 2010). Thus, logistics operations ensure that an organization achieves economies of scale in the procurement and manufacturing processes. The application of logistics planning also ensures that the shipment is consolidated to reduce costs that are related to transportation. The reduction is based on the fact that shipping is used for a larger load and longer distances reduce the cost of transportation per unit. On the other hand, improvement of quality should be continued because it is a key to success (Carter & Rogers, 2008). Logistics also ensure that there is appropriate support for the product life cycle that ensures that some of the items used in the delivery of the inventory are recycled. As such, the process creates and enhances reverse logistics.
Customer Relationships
The term customer is applied to indicate an individual or a family that makes the purchases goods that satisfy their personal needs. On the other hand, an organization can perform as a customer when it orders commodities that enable it complete within its profile operations. The third level of customer is other organizations that exist within the supply chain such as the wholesalers and distributors (Hutchins & Sutherland, 2008). The supply chain management should emphasize meeting the customer’s needs regardless of whether the customer is an individual or an organization. The underlying force behind logistics strategies is to ensure that customers are served in the most efficient manner that ensures that their needs are met.
Logistics plays a supportive role in the execution of marketing strategies for any organization. An organization is effective in competing with others who operate in the same niche when customers’ needs are correctly identified, and the appropriate results are channeled to meet the needs. An organization must integrate most of its operations to achieve efficiency at all levels. The focus of logistics is to ensure that products and services are positioned in a perspective that takes customer specifications into account. For marketing to be effective, the goods need to be available to the customers and that can only be achieved through proper logistics (Hausman & Thorbeck, 2010). It can be argued that logistics is responsible for the provision of time and place utility value in any product or service. Logistics can significantly influence profitability that is the essential aspect of focus in marketing.
This concept is founded on the fact that the customers are given the best services which involve minimum costs. Logistics ensures that goods are available to the customer whenever the customer desires to have the goods. Logistics ensure that there is no stock out frequency in an organization and as such customers customize products in a wide variety supported by the same organizations (Carter & Rogers, 2008). The logistics also determine the fill rate that, in essence, is the ability for the organization to ensure that there are no stockouts. Logistics also enhances the customer experience by ensuring that all customer requests are met during the shipping. Failure to deliver on any item as required by the customer results in detrimental effects. Logistics also provides operational performance in terms of the ability of the supply chain to deliver goods in the required time while maintaining consistency and allowing for flexibility (Bernon, Upperton, Bastl, & Cullen, 2013).
Procurement
The role of logistics has shifted from the historical function of carrying out procurement activities on a clerical basis to employing various strategies in procurement. The modern focus on procurement considers total cost as well as the development of the relationship between buyers. The change in the role of supply is informed by the fact that procurement is the main factor for one of the highest expenditures in any organization (Mollenkopf et al., 2007). Applying appropriate logistics strategy enables any organization to be able to make an informed decision on outsourcing some of the operations that are involved in the procurement process.
The logistics strategy ensures that there is a continuous supply of raw materials in an organization by employing the right procurement techniques. The occurrence of downtimes during the production process creates unnecessary costs while affecting the ability of the organization to provide goods to its customers. The continuous supply of products is tied to both raw materials and other parts that are required to the production process which varies from one industry to another (Hutchins & Sutherland, 2008). Logistics, when applied strategically during the procurement process, enables an organization to be in a position to maintain continuous supply with the most minimal inventory investments. The ideal situation is when the raw materials are provided at the right time when they are about to be used.
Using an appropriate logistics strategy is necessary for ensuring that the quality of goods in any organization is maintained. An organization, therefore, will have an advantage by establishing a network of suppliers who are also committed to establishing and maintaining the quality of goods as required by the customer. Therefore, there is a need to create good suppliers who can ensure that the organization can achieve the objective and provide the required standard of products. The providers in such a case are viewed as the source of innovative techniques as well as technology that allows releasing the design for new products while at the same time improving the existing ones (Xiao et al., 2010).
The selection and assessment of suppliers have become an integral part of procurement and logistic strategy. It is necessary to identify suppliers and assess their ability to meet the organization’s requirements. The suppliers can also be ranked to ensure that they are easily monitored, and feedback is provided on their performance. Logistics also ensure that the organization can carry out regular audits which include checking the equipment used for the production of raw materials as well as the level of skilled labor that is involved in the process (Hausman & Thorbeck, 2010). The logistics strategy also allows organizations to carry out supplier quality management and assess the ability to improve the process over time. When appropriate strategies are applied, the organization works with a fixed list of suppliers which includes only reliable ones.
Manufacturing
Manufacturing is regarded as being competent if it creates the brand power, provides required volumes and variety as well as responds to the constraints while ensuring lead time is maintained. Brand power is described as the measure of purchasing power as it relates to the manufacture’s reputation, product quality as well as supply chain efficiency. The logistics requirements and strategies applied to the manufacturing process are key to determining the attractiveness of the final product. The brand power also relies on the ability to determine the amount of value-added services and timing which should be included in the manufacturing process.
The logistics strategy applied is critical in determining the volume of goods that are produced. In the end, the volume of goods produced also plays a critical role in determining the profitability of the organization. The supply chain logistics is responsible for evaluating the number of times a product is manufactured in a given period on top of the production volume (Krause et al., 2009). By considering the actual number of manufacturing times the organization can assess the effect on the inbound and outbound logistics requirements. The quantity of goods that are produced at the end also determines the volume that the supply chain structure should be in a position to handle.
The manufacturing process aims to provide the customers with a variety of goods by the use of flexible and reliable technology. The current practice has shifted to allow the manufacturing process to be in a position to create economies of scope. The economies of scope describe the ability of an organization to be in a position to move from one production to another with minimal effect on efficiency (Mollenkopf et al., 2007). The organization is empowered to deal with the common constraints of the manufacturing process. The constraints include the capacity of the organization which is the measure of production per unit time. The organization is well prepared to handle the equipment constraint which indicates the sequencing of the machines to perform the different operations.
The logistics strategy that is adopted by the organization is important to determine the lead time which specifies the amount of time required to ensure products are ready for shipping. An effective logistics allows the organization to accommodate both operational time and in-operational time. Logistics delays can affect the lead time as the effect harms the manufacturing process (Seuring & Müller, 2008). All logistics failure during the manufacturing process affects the lead time and as such can create unexpected delays in the delivery of the product.
The current manufacturing process has shifted from the traditional methods that were applied to the engineered-order techniques. The current practice seeks to establish lean systems which minimize the number of resources used during the manufacturing process. Flexible manufacturing has also become a common practice which ensures that organizations can use automated robotic systems that can be easily adapted to different manufacturing processes. Flexibility allows the manufacturing process to be in a position to achieve mass customization.
Integrated operations planning
The current crop of competitive businesses has to lead to the growth of the planning for logistics operations. The plan for operations is tailored to ensure that the organization operates based on product demands. Demand planning is critical to enable the supply chain that forecasts the processes. The demand planning also allows the organization to be in a position to ensure consistency in its manufacturing and warehousing procedures.
Organizations can apply production planning effectively by adopting the new measures of supply chain management. Production planning aims to ensure that the organization can match customer requirements with the existing production constraints. The plan provides that items that are to be produced within the current production constraints are well managed and inventory is minimized. When appropriate planning is combined with relevant logistics planning, there is coordinated transportation, warehousing, and proper inventory management (Linton, Klassen & Jayaraman, 2007). The plan implies a collection of sufficient data that allows the management to be in a position to make correct decisions and steer growth. The graph below indicates how a ten percent increase in retail demand with no communication to other members impacts other operations aspects such as warehouses and production lines.
Integrating planning in supply chain management is critical for the organization that wants to achieve the three main objectives. The objectives include the enhanced ability to respond to change, developing a comprehensive perspective, as well as proper resource utilization. The advantages emanate from the fact that logistics and supply managers ensure that plans for the supply are based on the lead times as well as scheduled freeze plans. The supply chain provides advantages to the organization given that the appropriate resources are utilized in the process of inventories delivery. Planning for a supply chain also confers an organization with performance improvements during the operations (Xiao et al., 2010).
The forecasting applied during the process of logistics operations relies on the application of several forecasting techniques. The first is the moving average techniques that rely on the previous un-weighted sales average to determine the amount to accommodate in the plan. Exponential smoothing shows that greater weights are applied to the recent demands, especially for large items. The time-series techniques are used for supply and seasonal goods planning. Other techniques such as regression base its prediction on the price and expected promotions and determine the quantity of inventory to be anticipated are also useful in forecasting.
Inventory Management
Logistics advancement has made it possible for inventory planning to determine the quantities that should be ordered and the right time. The planning is critical in establishing the new order of points in the whole supply chain. The establishment of the lot size allows an organization to be in a position to match the inventory with the actual cost of ordering. The formulation allows an organization to determine the actual inventory quantity which when combined with the carrying and ordering costs, allows the organization operates with the least costs involved.
Operations management also allows an organization to be in a position to handle the uncertainty that is related to inventory management. Some of the uncertainty is related to demand where safety stock is added to the base inventory stock to ensure no stock outs when the demand rises. Organizations also have the responsibility to ensure that performance cycle uncertainty is handled efficiently. Logistics planning is also critical in ensuring that both demand and the performance period are incorporated into the plan.
Transportation
Transport accounts for the largest cost expenditure in all logistics operations. By aligning the organization’s operations to the deregulated feature of the current transport system, the organization can be able to integrate the transport into the supply chain logistics. As such, to be effective in managing the total cost of the inventory management process it is important to ensure that transportation costs are given the utmost consideration.
Efficient logistics ensures that transportation economics is considered when making inventory delivery plans. Logistics planning enables the managers to be in a position to integrate several facets of transport as it relates to inventory management. The factors include the distance, volume, and other market factors that have a critical input in the cost of carriers. Logistic managers can integrate work familiarity with the line-haul as well as related specialized transport services.
Operational management is responsible for traffic administration. Transport managers leverage technology to achieve the objective and control transport costs (Krause et al., 2009). The role of logistics spans from the ordinary management of transport that involves negotiation, auditing as well as claims administration. The logistician aspect of the supply chain is responsible for setting prices. Logistics strategies have created the ability to unbundle the prices of the commodities under the inventory based on transport, as well as other related operations.
Warehousing
The current logistics strategies allow warehousing to function as a component of inventory management and aim at meeting customer requirements. this concept in the supply chain management ensures that products are stored for a minimal time which reduces the costs.
The goal of warehousing is to ensure that there is flexibility in the management of inventories. Organizations need to establish the right logistics strategies which in turn grant storage flexibility. The aspect of warehousing ensures that the customers are granted local presence that ensures that variances in customer requirements are well met. Apart from guaranteeing flexibility in the warehouse stocks, it is also critical for ensuring consolidation and sorting out inventories. The warehouse is essential to ensuring that seasonal goods are available throughout the year while that enables reverse logistics to be implemented.
When warehousing is incorporated in the logistics planning of supply chain management, products are assigned slots. Slots ensure that products are assigned a location based on the individual product characteristics. Logistics planning ensures that product velocity is factored in the layout of the warehouse where the high-volume products are positioned in an appropriate location which guarantees minimal movements (Linton et al., 2007). Proper logistics planning ensures that active storage is maintained to store the products for the least time possible. Dynamic storage allows sufficient inventory to be provided so that there are enough cushions against stockouts. Logistics planning is also necessary for ensuring that extended storage is available for seasonal goods.
Supply management ensures that an organization utilizes the right warehousing that best suits inventory management. An organization can opt to use a private warehouse, public warehouse, or contract warehousing. Supply chain management ensures that an organization makes reliable decisions on warehousing based on several factors. Some of the factors that are considered when choosing a warehouse which includes the site as it provides correct matching of the warehouse and the type of inventory handled. It is also important to evaluate the design of the warehouse and ensure that product moves with ease. The ability of the warehouse to be expanded should also be put into consideration given the critical role a warehouse plays in supply chain management.
Handling and Packaging
A product’s packaging confers protection on the product while at the same time giving the product an identity. The packaging can be done in a manner that is appealing to the customer or the industrial sector. When product packaging is done with the customer in mind, the primary aim is to give the product an identity that ensures that marketing strategies are easier to implement. Industry packaging ensures that the packaging is focused on easy to execute logistics. It also takes into consideration the size of the packaging concerning the master package. The objective of the process is to ensure that the number of units handled during the logistics process is minimized.
The supply chain logistics is responsible for handling inventory that ensures that products flow reaches the customer. Logistics provides a company with critical information technology to ensure that the demands of stock are met. As such, logistics can be said to provide companies with electronic fulfillment in their operations (Krause et al., 2009). It is the role of logistics to ensure that appropriate packaging is utilized to minimize the environmental impacts that result from packaging materials. Improper disposal of packaging materials can lead to unwarranted pollution liability for an organization.
The logistics strategy for handling materials takes into account the cost of return processing. Given that a good number of orders are requested via information technology platforms, there has been an increase in the percentage of returned orders. The challenge of return processing does not allow the organization a high number of items that warrant the use of digitized systems. As such, return processing is handled manually in most cases.
Operations Management. Global Supply Chain
When businesses enter the global markets, different challenges emerge such as complex logistics requirements, security concerns as well as new operational costs. Organizations engage in a global operation with the aim to increase sales volumes by opening up new markets. Global operations are also initiated to benefit from the economies of scale as a result of reduced indirect costs. When operating on a global scale organizations can access advanced technologies and have increased sustainability while cutting down on tax liability. Despite the advantages that the global platform offers to organizations, there is an increased cost of logistics accompanied by varied complexities.
Notably, the employment of strategic logistics approaches in the supply chain can enable the organization to maximize the benefits of globalization. Organizations can adopt a multi-domestic approach when operating in different countries (Linton et al., 2007). The strategies allow an organization to retain a dominant corporate headquarter while initiating operations in other countries. The approach allows an organization to create separate semi-autonomous supply chains in different regions of operation. As such the organization can be in a position to focus on local markets while reducing coordination requirements on the entire supply chain. The strategy, however, does not allow a company to take full advantage of the economies of scale as there is limited reach on the global scale.
Organizations are also able to adopt a cross-border operation strategy that makes local customization of the necessary activities possible. The model has one headquarters that coordinates services around the globe, but the actual operations take place in different regions. The supply chain in each country is focused on the market characteristics that define the area of operations. The strategy allows the organization the flexibility of focusing on different local markets while at the same time ensuring that the needs of the local customers are put into consideration. The main challenge in this approach is the fact that it is difficult for an organization responds in an integrated manner to global issues.
An organization can also employ a transnational strategy that allows the company to maintain regional operations around the globe by using strategically positioned headquarters to ensure optimum effectiveness. The goal of such a strategy is to grant an organization the ability to manage operations from the best place suited to offer effective coordination. The main advantage of this strategy is the fact that it ensures the organization is in a position to adopt a global approach to solution provision. The approach provides that the organization maximizes the economies of scale that are available when coordinating supply chain operations (Hausman & Thorbeck, 2010). The technique is limited in the sense that there is the need to provide substantial coordination as well as integration that in turn can limit the organization’s ability to offer unique solutions that are tailored to the particular markets.
Network Designing
Organizations that want to be maximum flexible in their logistics operations have to create a network of different facilities. The network can only be effective if the proper integration takes place. Integration of the network is critical for organizations that rely on logistics efficiency to gain an advantage over other organizations. The integration also exceeds the individual organization’s ability to include other organizations and suppliers in the supply chain logistics.
The creation of a network is dependent on the integration of procurement, manufacturing as well as customer relationship strategies. The organization seeks to achieve total cost, as well as service trade-offs within the limits of strategies. Warehouses have a critical function in the logistics design of the network system given the contribution that warehouses have in establishing cost reduction and improving operations.
An organization that intends to create an integrative network design must also pay close attention to the transportation as well as the inventory economies of the supply chain management. Not only warehouses are included in the network design transport, but they also have a central role in the logistics (Linton et al., 2007). The inventory economies that an organization must pay attention to the temporal effect of stocks on the logistics dimension of the supply chain management. A better understanding of the total costs of an integrated network is essential to establishing the effectiveness of the network design that is employed.
When attempting to calculate the total cost of a network there are various challenges that an organization must brace. Standard accounting systems fail to consider a considerable number of costs in any given network. To establish the actual costs, it is needed to ensure a comparison of different networks which helps develop a complete picture of operational efficiencies. The challenges can be overcome if all the functions are grouped during the analysis while making the analysis based on customer satisfaction.
Operational Analysis
When conducting an operational analysis, there is no ideal logistics system that can be used for all enterprises. However, some of the principles can be included in the process of problem definition and planning, data collection as well as analysis (Carter & Rogers, 2008). The process also includes the stage of making recommendations and implementing the results of the process. Problem definition and planning provide the foundation for the entire process. The initial stage includes a comprehensive evaluation of the logistics operations as they are carried out by the organization. The supply chain manager seeks to understand the environment, process, problems as well as the performance of the current system. The process also conducts market analysis as well as an assessment of the technological capabilities of the entire supply chain. The supply chain also needs to develop an integrated method of supporting the integration of the findings. The support logic plays an integral role in the evaluation of the existing procedures. The final phase of the process is to establish the cost and benefit estimates. The benefits are categorized in line with the improvements as well as the accruing cost reduction and cost prevention.
The next phase in the process includes the planning activities. The main functions of the stage revolve around setting the objectives as well as establishing possible constraints that could affect the entire process. The supply chain manager also needs to develop the supply work plan as well as specify the standards that will be employed in the entire process. The phase of data collection mirrors a similar process as used in other areas and utilizes common methods such as quantitative and qualitative methods (Carter & Rogers, 2008). The analysis phase is tasked with the process of establishing assumptions based on the outcomes of the data stage. The analysis is concerned with answering supply chain-related questions as well as validating the baseline analysis. The final stage which involves the recommendations is critical in identifying the best alternatives in terms of efficiency and ease of implementation. The supply chain manager is required to define a course of action, establish schedules and define further evaluation criteria.
Given the critical role that the supply chain is playing in the current scope of business operations analysis tools that ensure optimization of processes must be adopted. The supply chain is currently tasked to respond to variations and inconsistencies of global markets as well as changes in production demands. The changes require more tactical tools to assist in carrying out the operational analysis. Supply chain managers are critical in the development of comprehensive plans that drive operations in the entire organization.
Establishing Collaborations
The current perspective of the supply chain has shifted from a loosely linked group of the organization to a multi-enterprise that focuses on improving the supply chain to ensure competitive advantage. The belief that cooperation reduces risk and improves the efficiency of an organization is the key driver of the shift. The collaboration grants the organizations the ability to eliminate wastes and synergize their efforts.
Companies should establish a type of collaboration that suits their industry which allows the business to function optimally. The different methods of collaboration that an organization can adopt include, contracts, outsourcing, administrative, alliance as well as enterprise extension (Carter & Rogers, 2008). Each of the collaborative models has its unique advantages and disadvantages mainly tied to flexibility, as well as an organization’s ability to exploit economies of scale at its disposal and reduce operating costs.
For a network of organizations to effectively function in a supply chain logistics cooperation, there is a need to develop trust between the different organizations. The issues of trust are more significant when it comes to human behavior for the different organizations that enter into a collaborative engagement. When managing the logistics supply chain, trust must be viewed from a reliability basis rather than a character basis. Reliability-based behavior emphasizes the ability of the partner to perform and the willingness to perform as agreed.
The established relationships need to be managed effectively to sustain the business. The management of the relationship should rely on a leadership model that tends to foster cooperation. The initiation of the collaboration is mainly done by the organization that plays a customer role in the relationship. To ensure that the relationship is implemented successfully, an organization must choose the right partner who has similar cultures and shares the same vision. The maintenance of the relationship is dependent on the existence of mutual strategies as well as operation goals. The relationship between the two organizations requires having a two-way performance measure to assess both organizations. A successful relationship also requires ways of providing feedback to the involved organizations (Seuring & Müller, 2008). The management of any collaboration in the supply chain needs to bear in mind the fact that some collaborations can survive to the point where the initial objectives are not met and hence require termination. As such it is important to establish a method of terminating the relationship.
Performance Assessment
A revealing assessment of the supply chain can be achieved but the manager has to pay attention to several key factors that have input on performance. It is important to evaluate the significance of the supply chain in enhancing customer satisfaction. The supply chain should be in a position to deliver inventories that meet the customer’s requirements. The supply chain needs to ensure that the quality of the goods is maintained through the process so that the product can create and leverage brand power (Linton et al., 2007). The organization should also consider the cost of having the supply chain in place as opposed to different approaches to delivering the products to the clients.
A company that is keen on using the effectiveness of the logistics of the supply chain as a competitive advantage will also evaluate the ability of the system to accommodate customer requests. The modern era that is characterized by information technology has seen the level of consumer sophistication increase over time. As such, the supply chain should have the ability to provide customization at a minimal cost. To ensure that comprehensive results are achieved, the process must be evaluated across all the involved organizations. The supply chain manager in such a case can look at the inventory dwell-time, the cash-to-cash cycle as well as the total cost of the supply chain. The supply chain needs to be evaluated using activity-based costing methods rather than traditional accounting for profit and losses. As such it is possible to assess the impact of each activity on the profitability of the supply chain.
Risk and sustainability
Historically the role of logistics and supply chain has been to forge towards customer satisfaction while at the same time lowering the costs. As such the logistics managers have been traditionally involved in resource trade-offs. The role of logistics has however evolved to include functions related to risk management as well as security. The risk in the current logistics operations approach is beyond the demand cycle uncertainty as they relate to other functions such as finance, security, and protection. Logistics managers must ensure that they extend their functions to accommodate a triple-bottom-line sustainability model. The triple-bottom-line sustainability model involves focusing on issues such as environmental, ethical as well as economic dimensions. Some of the aspects that warrant consideration during risk assessment and management in the supply chain logistics revolve around regulation, taxes as well as finance strategies. There are also issues of varying complexities across different products as indicated in the graph below.
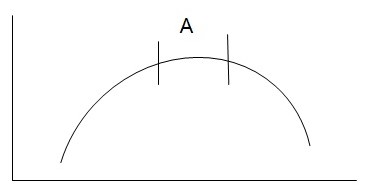
Regulation is central to risk management during the risk management in logistics management. Supply chain management calls for interactions between an organization and different parties such as consumers, suppliers as well as government agencies, and competitors. As such, the supply chain is highly regulated to ensure all the involved parties are well protected. The regulations are tied to the operations such as finances and taxes that relate to supply chain management. The taxes imposed by the authorities have an impact on the design of the supply chain. The supply chain manager is rightfully wary of any changes in the regulations as most governments keep altering the regulations in a bid to create more jobs for the citizens. The supply chain manager is also well poised when considering security issues as the global operations demand that an organization, its products as well as brand name be protected. Securing the supply chain at the global stage requires that an organization enhances its internal risk management processes while at the same time collaborating with other partners and government agencies. As such, the cross-border operations of the supply chain will be fortified.
A secure supply chain is established through the application of appropriate organizational policies, procedures as well as technology. A supply chain should also be resilient in that it can be in a position to recover from any incident that hits the established logistics. One of the major concerns of a modern supply chain is the threat that is posed by terrorism (Xiao et al., 2010). As such it is wise for any logistics manager to establish a method of preventing terrorism effects. The graph below illustrates the changes in logistics supplies.
When it comes to the sustainability of an organization, supply chain logistics have a central role that is critical to the success of the organization at large. An organization’s sustainability has several aspects ranging from the environment, ethics, education as well as economic dimensions. Under the environmental aspect, the organizations seek to guard against resources wastage and pollution. Ethics dictate that the organization should enhance employee relations as well as community involvement while under education an organization focuses on employee development and related management practices. The economic aspect calls for a balance in the tradeoffs between internal and external factors. As such, the supply chain manager is required to assess the impact of the decisions made on the different aspects that are related to sustainability. Supply chain managers can apply different methods of establishing strategies to be in a position to evaluate the necessary tradeoffs (Xiao et al., 2010). Adopting the rightful strategy is also critical in ensuring that employees are retained while at the same time growing the organization’s pool of talent by hiring new persons.
References
Bernon, M., Upperton, J., Bastl, M., & Cullen, J. (2013). An exploration of supply chain integration in the retail product returns process. International Journal of Physical Distribution and Logistics Management, 43(1), 586–608.
Carter, C. & Rogers, D. (2008). A framework of sustainable supply chain management: Moving toward new theory. International Journal of Physical Distribution and Materials Management, 38(3), 360–387.
Hausman, W. & Thorbeck, J. (2010). Fast fashion: Quantifying the benefits. In Innovative Quick Response Programs in Logistics and Supply Chain Management, International Handbooks Information System. Berlin: Springer.
Hutchins, M. & Sutherland, J. (2008). An exploration of measures of social sustainability and their application to supply chain decisions. Journal of Cleaner Production, 16(6), 1688–1698.
Krause, R., Vachon, S., & Klassen, R. (2009). Special topic forum on sustainable supply chain management: Introduction and reflections on the role of purchasing management. Journal of Supply Chain Management, 45(7), 18–24.
Linton, J., Klassen, R. & Jayaraman, V. (2007). Sustainable supply chains: An introduction. Journal of Operations Management, 25(5), 1075–1082.
Mollenkopf, D., Russo, I., & Frankel, R. (2007). The returns management process in supply chain strategy. International Journal Retail and Distribution Management, 37(9), 568–592.
Seuring, S. & Müller, M. (2008). From a literature review to a conceptual framework for the sustainable supply chain management. Journal of Cleaner Production, 16(8), 1699– 710.
Xiao, T., Shi, K. & Yang, D. (2010). Coordination of a supply chain with consumer return under demand uncertainty. International Journal of Production Economy, 124(1), 171–180.
Yang, D., Choi, T., Xiao, T., & Cheng, T. (2011). Coordinating a two-supplier and one-retailer supply chain with forecast updating. Automatica, 47(3), 1317–1329.