Introduction
The purchasing function is one of the most important aspects of business performance because most strategic resources associated with operations management are contingent on supplier performance. This is especially true in the manufacturing industry because the quality of goods delivered to the market depends on the eminence of raw materials (De Felice et al., 2015). Consequently, experts estimate that the purchasing function could be responsible for up to 50% of all corporate costs in the manufacturing sector (Modgil and Sharma, 2017). These insights show that the purchasing function has a significant impact on how effective or efficient companies can be.
Based on the importance of suppliers to the manufacturing sector, firms have developed unique models and techniques for evaluating supplier performance (Gopalakrishnan and Haleem, 2015). Although the scope of this study does not include their mention, most of them have been designed to address unique supply chain management issues faced by respective companies. Additionally, they have focused on improving accounting performance and bolstering operations and supply chain management programs, as alluded in the works of Shore and Freije (2016). Coupled with the findings of other researchers, such as Mukherjee (2017), these scholars have focused their attention on the selection of new suppliers through supplier evaluation programs. To this end, supplier evaluation emerges as an integral part of developing good relationships between companies and their suppliers.
The relationship between Industrial Products Corporation (IPC) and Branco is premised on the same idea because supplier evaluation is designed to promote good relations between both parties. However, recent concerns about Branco’s performance have necessitated a re-examination of IPC’s performance evaluation model to find out better ways of safeguarding the quality of goods produced.
This review has been further underlined by the need to maintain good relations with Branco, as it is IPC’s main supplier. This report underscores this goal by evaluating three key areas associated with Branco’s performance: the role and application of supplier evaluation, business risks associated with poor performance and how to manage the aforementioned issues. These three key areas of assessment build on each other. The section below explains the role and application of supplier evaluation.
Role and Application of Supplier Evaluation
As highlighted in the introduction section above, supplier evaluation is integral in safeguarding business performance because it makes suppliers accountable for their role in supply chain management. Relative to this statement, Barsing et al. (2018) and De Felice et al. (2015) say it is important to undertake supplier evaluation processes to assess the quality of contractual relationships, monitor the progress of strategic relationships development, and minimize business risks associated with future purchases.
Broadly, supplier evaluation is often linked to 7Cs of information categories in supply chain management, which include the capacity to deliver an order, competency of the supplier, consistency in providing the right output, controlling the procurement process, demonstrating a commitment to quality, cash (supplier’s financial base) and cost of the supplies. In some cases, these 7Cs may be transformed into 10Cs, which include culture (compatibility of supplier and buyers’ culture), clean (ethical practices of the supplier) and communication (via virtual platforms).
Most pieces of literature that have investigated supplier evaluation processes have focused on highlighting its benefits as opposed to describing how it could be practically used to complement organizational performance (Freije, 2016; Mukherjee, 2017; Modgil and Sharma, 2017). This limited academic focus has made it difficult for companies to identify the best evaluation model that meets their needs. Furthermore, the lack of contextual empirical evidence has made it difficult for firms to understand the extent of supplier evaluation on business performance.
IPC relies on supplier evaluation processes to safeguard its product development strategy. However, unlike other companies that use supplier evaluation to select the right supplier (Li and Wang, 2018; Lambiase et al., 2016), IPC only has one supplier – Branco. Therefore, the evaluation process is conducted with the aim of monitoring performance, as opposed to selecting the best supplier for a job. To the extent that Branco remains the sole supplier, IPC’s evaluation process plays an important role in identifying areas of supply chain management that could benefit from supplier development. Consequently, the insights that emerged from the supplier evaluation process have to be analyzed within the context and functions of IPC.
Evaluating Branco’s performance would also provide IPC with a framework for comparing its operations with those of other suppliers in the market. Thus, the firm can benchmark Branco’s performance with those of other players in the market. By adopting this strategy, IPC can pay the lowest cost of materials delivered to the company – a strategy, which would then improve its competitiveness through a reduction in overhead costs. This plan could also improve the quality of products manufactured by IPC because the evaluation process would highlight key performance areas that can be improved to generate quality inputs.
The information obtained from this process also has the potential to improve the relationship IPC shares with Branco. Indeed, the use of evidence-based decision-making in managing supplier relationships has the potential to improve relations between companies and their suppliers. Therefore, the supplier evaluation process would provide IPC’s managers with the evidence needed to improve its relationship with Branco.
Schuessler, Frenkel and Wright (2019) highlighted the role of supplier evaluation in improving relationships between companies, their suppliers and employees. Their work is significant to this discussion because their investigations focused on improving human relationships using better supply chain management practices – similar to the relationship between Branco and IPC. Additionally, their research manifests the unique supply chain management conditions present in the manufacturing sector and that impacts how different parties within the value chain synchronize their inputs to create superior products (Schuessler, Frenkel and Wright, 2019).
IPC has similar conditions because it is also in the manufacturing industry and experiences the same unique challenge of improving relationships among different stakeholders in a stressful work environment. Supplier evaluation provides a unique opportunity for the company to deescalate some of the pressure of working in such a stressful work environment and improve the quality of engagement between the firm and its supplier. Subject to this relationship, the supplier evaluation process presents an ominous opportunity for IPC to improve its relationship with Branco.
This supplier evaluation framework developed by IPC reflects the internal operational dynamics of the company as it relates to supplier management. At the end of each evaluation phase, Branco can determine its performance and make necessary improvements, if need be. However, like most other evaluation models highlighted by researchers, critics have argued that some performance assessments use the wrong criterion of evaluation (Li and Wang, 2018; Lambiase et al., 2016). Differences between actual performance and projected evaluation results have emerged between firms and their suppliers because of the merits used to adopt specific weighted criteria for analysis (Freije, 2016; Mukherjee, 2017; Modgil and Sharma, 2017).
A common theme espoused by these critics is the use of supplier evaluation processes that are similar to most customer-centric techniques to review performance across multiple sectors (Freije, 2016; Mukherjee, 2017; Modgil and Sharma, 2017). They argue that these generic models fail to account for the unique operational challenges that suppliers encounter when doing their job. Therefore, their criticisms emphasize the need to adopt evaluation models that address unique industry-specific challenges that affect supplier performance.
Alternatively, their views propose the use of evaluation models that are unique to the operational requirements and needs of the manufacturing industry. Relative to the aforementioned concerns, the managers of IPC deem it critical to measure Branco’s procurement attributes that are important to the organization, as opposed to relying on standard weighting criteria to evaluate its performance. Therefore, their evaluation process is based on a contextual assessment of the relationship between the firm and its primary supplier.
Branco’s Performance and Business Risk to IPC
Part of IPC’s success has been pegged on its strict adherence to high-quality standards in procurement. However, Branco’s poor performance undermines this link because the last three evaluations have shown a steady decline in the quality of materials delivered. Although Branco is aware of the issue, problems reported in one quarter keep compounding on the next. Poor quality standards exhibited in the supplier’s performance also imply that the company has failed to meet product-packaging specifications outlined in its contractual agreement with IPC. Deviations of Branco’s performance from expected quality standards have been reported in the non-conformance actions report.
Typical evaluation procedures used by IPC to evaluate Branco’s performance use three significant assessment criteria: quantity of goods produced, delivery time and the accuracy of paperwork involved in the purchasing process. These weighted assessment measures are categorized into three broad categories: quality, delivery and performance. Quality is deemed the weightiest evaluation item in the framework of review because it accounts for at least 50% of the total weighted index for supplier performance. Out of a total score of 4, a minimum output of 3.2 was expected from Branco. However, in the last three quarters, the firm’s performance has been below par (a score of 3). Figure 1 below provides a graphical representation of this performance.
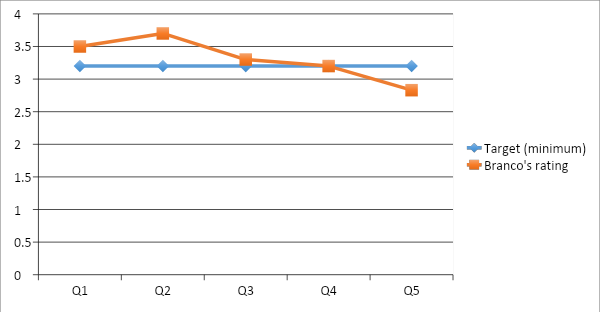
The graph above shows that Branco’s performance has dipped below the target in the last two quarters (Q4 and Q5). This score stands out from the rest of the quarters because, in the first three, the supplier’s performance was consistently above the target (blue) line. The best performance was reported in Q2 when its total score was 3.7/4. According to IPC’s supplier scoring performance criteria, this result meant that less than 5% of Branco’s shipments did not conform to the specified standards. In the last three evaluations, this performance had declined to 20% of all shipments failing to conform to the set criteria.
Branco’s poor performance has many implications for its future relationship with IPC because it affects the firm’s reputation through the low quality of products sold to the market. IPC’s supplier scoring criteria also suggests that Branco’s poor performance increases “out of control limits” in the company’s supply chain link, thereby compounding quality problems because the company has little time to address packaging issues because Branco’s shipments are integral to IPC’s value chain.
Therefore, Branco has the potential to undermine IPC’s process capabilities. Coupled with the issue of non-conformance to quality requirements highlighted above, the company could suffer a negative brand image because, over the years, it has built a solid reputation that is predicated on good quality. For example, the poor quality of Branco’s deliveries was costly for IPC because it led to the cancellation of some orders, as customers complained about some of the packages having defective flaps and edges. This problem slowed down the company’s operations because it was identified when production had already commenced.
In other instances, it was detected when there was damage to machines and equipment. Since IPC’s production processes are fully automated, through a line management system, most of these issues, identified at the latter stages of production, significantly impacted activities at the higher end of the value chain. For example, they resulted in a 30% loss of production capacity for defective products used within two days. This statistic means that over a long period, the loss in production capacity would have exceeded 30%. At full production, the company can use up to 2,000 cartons in three operations with £18 being charged per hour.
The potential for Branco’s mistakes to override most of the gains made by IPC is also demonstrable in its delivery schedule because Branco’s boxes are critical to the company’s delivery model. Particularly, they will undermine the firm’s ability to ship products in correct quantities as dented packages may not have the capacity to hold the specified quantity of products needed. These errors could be linked to Branco’s poor record in quality performance because of the company’s poor score in “shipment condition” for all materials delivered to IPC’s warehouses.
As one of the key weighted supply chain attributes, a poor score on shipping quality undermined the company’s performance. Although Branco’s quality performance had deteriorated over the five quarters assessed, its delivery record has been consistent throughout the analysis. For example, it posted a score (3.5) for providing good paperwork. However, “delivery” did not have a significant weight on the overall score.
Branco’s poor quarterly performance contravenes some of the principles espoused by Yang et al. (2018) about good suppliers. He says that they should provide consistent quality, give a good price, have a stable background, have good service backup, be responsive to needs, keep promises, provide technical support and inform buyers about the progress made in improving their performance (Yang et al., 2018). Branco’s poor performance has been attributed to poor quality. Therefore, it does not meet the threshold for being a reliable supplier according to IPC’s suppliers scoring criterion. Therefore, based on the potential negative effects of poor quality on the company’s operations, it poses significant business risks to IPC.
How to manage the Issues Moving Forward
The quality issues identified in this report could be addressed by adopting sustainable supply chain management. In other words, IPC and Branco should consider embracing sustainability as the basis for all future engagements because it will address future procurement issues through quality and value proposition perspectives (Okwu and Tartibu, 2020; Zeng, Tse and Tang, 2018).
This statement stems from research studies, which have linked quality performance and sustainability in supply chain management (Barney and Harrison, 2020; Reinecke et al., 2018; Alves-Pinto, Newton and Pinto, 2015; Biswal et al., 2018; Koster, Vos and Schroeder, 2017). In other words, the success of future engagements between IPC and Branco should be predicated on the interaction between quality and sustainability, as a core supply chain philosophy.
For example, sustainability could address wastages that exist in supply chain linkages between IPC and Branco’s operations that affect quality. Mahajan and Vakharia (2016) support this view by drawing a link between effective waste management and improved quality.
The aforementioned suggestion is predicated on the adoption of the grey systems theory to solve supply chain management issues. Originally developed by Julong Deng in the early 1980s, the theory has been used in supply chain management to address uncertainties and ambiguity (Kachitvichyanukul, Sethanan and Golinska-Dawson (2015). Thakur and Anbanandam (2015) add that this theory is useful to corporations that have incomplete or unknown information about their product management processes.
The uncertainty is directly related to the “grey” concept because it is neither “black” nor “white.” Stated differently, the grey systems theory portrays a business environment characterized by scanty information, which should ideally inform decision-making processes. The other two are “white” and “black” environments that are defined by the availability and the lack of information about supply chain management processes, respectively. Thus, a “grey” system is characterized by the use of unknown or uncertain information in decision-making.
IPC’s supplier evaluation is characterized by uncertainties, which means that it is also a form of grey system. The importance of the rating system used by IPC to rate Branco’s performance is to express the flexibility of expressing decisions about supplier performance easily. Relative to this assertion, Bhaskar and Jain (2018) say that a resilient supplier evaluation process should investigate issues pertinent to the buyer and supplier, subject to factor expandability. The grey systems theory explains how such scoring criteria can be developed because it explains how series compatibility could be used to undertake the best supplier selection reviews and generate a “grey” strategy.
An evaluation matrix may aid in developing this strategy and the supplier selection process may be dependent on finding a supplier who will provide the best balance between the characteristics of the materials sourced and the prevailing market demand. This strategy has been associated with the identification of critically important areas of supply chain performance from researchers who have demonstrated its efficacy in improving sustainable practices across the value chain (Etzion and Aragon-Correa, 2016). Overall, having a broad view of IPC’s supply chain processes through the adoption of sustainable supply chain management techniques would be critical in addressing its present concerns.
Summary
The adoption of sustainable supply chain management techniques is highlighted in the triple bottom line approach, which emphasizes the need to review environmental, social and economic costs of supply chain management. For example, from an economic perspective, it is untenable for IPC to continue depending on Branco as the only supplier. This stringent requirement has to be reviewed because it makes the company’s operations vulnerable to its supplier’s errors.
Therefore, IPC needs to have alternative options of engagement by renegotiating the terms and conditions for its product packaging options. This strategy would make its operations more sustainable. Nonetheless, it is important to recognize the long time it has taken to solidify the relationship between Branco and IPC because it would equally take the same level of investment to develop another one. Consequently, the renegotiating of terms should take a long time to give enough room to formulate better terms of engagement or an alternative and reliable supplier.
Reference List
Alves-Pinto, H. N., Newton, P. and Pinto, L. F. G. (2015) ‘Reducing deforestation and enhancing sustainability in commodity supply chains: interactions between governance interventions and cattle certification in Brazil’, Tropical Conservation Science, 3(2), pp. 1053-1079.
Barney, J. B. and Harrison, J. S. (2020) ‘Stakeholder theory at the crossroads’, Business and Society, 59(2), pp. 203-212.
Barsing, P. et al. (2018) ‘Cross-docking center location in a supply chain network: a social network analysis approach’, Global Business Review, 19(3), pp. 218-234.
Bhaskar, K. and Jain, N. K. (2018) ‘Conceptualizing a resilient supply chain for single-fuel biomass power plant’, Journal of Operations and Strategic Planning, 1(1), pp. 3-14.
Biswal, J. N. et al. (2018) ‘Interpretive structural modeling-based framework for analysis of sustainable supply chain management enablers: Indian thermal power plant perspective’, Journal of Operations and Strategic Planning, 1(1), pp. 34-56.
De Felice, F. et al. (2015) ‘Performance measurement model for the supplier selection based on AHP’, International Journal of Engineering Business Management, 7(1), pp. 1-10.
Etzion, D. and Aragon-Correa, J. A. (2016) ‘Big data, management, and sustainability: strategic opportunities ahead’, Organization & Environment, 29(2), pp. 147-155.
Gopalakrishnan, P. and Haleem, A. (2015) Handbook of materials management. 2nd edn. New York, NY: PHI Learning Pvt. Ltd.
Guo, Y., Wang, L. and Chen, Y. (2020) ‘Green entrepreneurial orientation and green innovation: the mediating effect of supply chain learning’, SAGE Open, 10(1), pp. 1-10.
Kachitvichyanukul. V., Sethanan K. and Golinska-Dawson P. (eds) (2015) Eco production: environmental issues in logistics and manufacturing. Cham: Springer.
Koster, M., Vos, B. and Schroeder, R. (2017) ‘Management innovation driving sustainable supply management process studies in exemplar MNEs’, BRQ Business Research Quarterly, 20(4), pp. 240-257.
Lambiase, A. et al. (2016) ‘Bees algorithm for effective supply chains configuration’, International Journal of Engineering Business Management, 8(1), pp. 1-10.
Li, L. and Wang, H. (2018) ‘A parts supplier selection framework of mechanical manufacturing enterprise based on D-S evidence theory’, Journal of Algorithms & Computational Technology, pp. 333-341.
Mahajan, J. and Vakharia, A. J. (2016) ‘Waste management: a reverse supply chain perspective’, Vikalpa, 41(3), pp. 197-208.
Modgil, S. and Sharma, S. (2017) ‘Information systems, supply chain management and operational performance: tri-linkage – an exploratory study on the pharmaceutical industry of India’, Global Business Review, 18(3), pp. 652-677.
Mukherjee, K. (2017) Supplier selection: an MCDA-based approach. New York, NY: Springer.
Okwu, M. O. and Tartibu, L. K. (2020) ‘Sustainable supplier selection in the retail industry: a TOPSIS- and ANFIS-based evaluating methodology’, International Journal of Engineering Business Management, 12(1), pp. 1-10.
Reinecke, J. et al. (2018) ‘Global supply chains and social relations at work: brokering across boundaries’, Human Relations, 71(4), pp. 459-480.
Schuessler, E., Frenkel, S. J. and Wright, C. F. (2019) ‘Governance of labor standards in Australian and German garment supply chains: the impact of Rana Plaza’, ILR Review, 72(3), pp. 552-579.
Shore, J. B. and Freije, J. A. (2016) Proactive supplier management in the medical device industry. New York, NY: Quality Press.
Thakur, V. and Anbanandam, R. (2015), ‘Supplier selection using grey theory: a case study from Indian banking industry’, Journal of Enterprise Information Management, 28(6), pp. 769-787.
Yang, C. et al. (2018) ‘Negotiation model and tactics of manufacturing enterprise supply chain based on multi-agent’, Advances in Mechanical Engineering, 10(7), pp. 1-10.
Zeng, W., Tse, M. Y. and Tang, M. (2018) ‘Supply chain quality management: an investigation in the Chinese construction industry’, International Journal of Engineering Business Management, 10(1), pp. 1-10.