Abstract
Deere-Hitachi Construction Machinery Corporation relies on inventory management and inventory controls which determined its competitiveness and profitability. These capabilities are useful in understanding and improving all production systems. Its inventory operations involve work-in-progress inventory, inventory control and the drum-buffer-rope approach. The company has complete database, a higher level of data integrity, and an excellent ability to monitor the inventory flows in the production process. Improvements are more typically discussed in terms of inventory turns, manufacturing lead times, and buffer times.
Introduction
Hitachi Ltd. is a global leader in engineering and electronic technologies delivering quality products to its customers all over the world. One of its subdivisions is Hitachi Koki India Ltd (Hitachi India Home Page 2008). Inventory control plays a crucial role in this subdivisions working with construction technologies and deliver operations. Recent years, there is a major focus on tools for coping with variation, such as safety stock formulas (or, equivalently, safety lead time formulas), input and output control systems, and closed loop material requirements planning systems.
Operations Strategies
Good production and inventory control is characterized by a synchronized flow of materials through the production process with a minimum of idle inventory. It is also characterized by short manufacturing lead times and productive use of the available work capacity and materials (Slack et al 2003). Improvements in production and inventory control translate directly into customer value through better product quality, cost, and delivery. At Hitachi Koki, this impact dictates that the production and inventory control system must be a focal point in a manufacturing firm’s strategy to compete through customer value. Inventory is a barrier to improvement in customer value (Calingo 1996).
Work-in-progress inventory increases manufacturing lead times. This fact is often counter to intuition. Typically, the response to a demand for shorter customer lead times is to increase inventory levels. However, inventory located upstream from an operation represents a waiting line through which each order must pass. The longer the line, the longer the order will take to get through the system. For example, if a manufacturing process has six weeks of work-in-progress inventory, then materials released at the first step of the process will exit as finished goods, on average, six weeks later (Chase and Jacobs 2003; see Appendix 1). This means that in order to produce to customers’ orders, the customer lead time must be six weeks, that is, orders must be placed at least six weeks in advance. If the customer lead time is to be shortened without reducing the work in progress, the production schedule must be developed from a forecast that may be very unreliable. Either alternative is costly (Johnston 2003).
At Hitachi Koki, inventory control is typically viewed as a process that makes tradeoffs between high inventory costs and low utilization of capacity. This tradeoff is an important aspect of all production scheduling techniques. For example, material requirements planning relies on long predetermined lead times between operations that create buffer stocks as cushions against variation. Just-in-Time systems use less-than-capacity scheduling of equipment (in conjunction with worker flexibility. The slack capacity and the ability of the workers to do more than one job serve as a cushion against variation (Johnston 2003; see Appendix 2).
The drum-buffer-rope approach of Goldratt and Fox (1986 cited Johnston 2003). The company uses buffer stocks to protect bottleneck operations and less-than-capacity scheduling at nonbottleneck operations. With excess capacity the machine time used for extra setups does not reduce the overall production rate of the process and is, therefore, virtually free. Similarly, since the work center uses its excess capacity to recover from disruptions to its schedule, it also accommodates periodic starvation caused by upstream disruptions. On the other hand, any lost production at bottleneck work centers translates into lost production for the entire process. Thus, the scheduling is focused on ensuring that the bottleneck operations remain productive at all times (Johnston 2003; see Appendix 3).
Implementations of Operations
The purpose of inventory is to insulate each step of the production process from the other steps and to protect the production process from the suppliers and the customers. Although this protective barrier may make life easier in the short run, it is an obstacle to understanding and improving the systems involved. If an easy method of achieving good production and inventory control existed, it would be like the philosopher’s stone — capable of creating gold from base metal. Unfortunately, there is no quick fix. Certainly, effective production and inventory control cannot be accomplished by simply installing new production scheduling software. What is required, however, is improvement in those systems whose deficiencies give rise to the problems (Johnston 2003). Hitachi Koki has gone far beyond the point where the potential reductions in inventory holding cost, as traditionally computed, are used to justify continuing improvement efforts (Slack et al 2003).
There are human tendencies to emphasize the tangible over the intangible, the visible over the invisible, and the short term over the long term. It follows that an important role of the manager is to create systems to overcome these biases. When a machine is shut down owing to a stockout, it is immediately and clearly visible. Furthermore, the resulting drop in utilization shows up as a tangible “cost” in the monthly utilization and efficiency reports (Slack et al 2003). On the other hand, the costs of having too much inventory are more insidious. For example, the cost of losing customers owing to poor quality and long lead times is not immediately visible and certainly not recognizable as inventory holding cost (Naylor 2002).
Effectiveness Priorities
Reducing inventories and achieving a synchronized flow of material through the production process enhances the ability to detect and track quality problems. Conversely, improving product quality reduces the need for “just in case” inventories and padded production schedules as protection against scrap losses and unpredictable yields Elimination of inventories makes quality problems more visible. For example, in the absence of buffer inventories, the production of a batch of defective parts may cause a shutdown of the entire production process (Slack et al 2003). Although this may appear to be a costly experience (and may be in the short run), in the long run it can actually be a very profitable experience. The shutdown may draw attention to the problems that cause the defects and, therefore, lead to the problems being fixed. In fact, the knowledge that a batch of defective parts can shut down the process may be sufficient to stimulate proactive efforts to improve quality. On the other hand, when large buffer stocks are present, a batch of defective parts may simply be scrapped while the production process continues uninterrupted. Thus, the problems that caused the defects remain invisible and unsolved while losses resulting from poor quality accumulate. These losses may, in the long run, far exceed the cost of a shutdown. No production scheduling system will in itself solve the problems of inventory control. For example, variation will result in either large inventories, wasted capacity, or both, regardless of the production scheduling mechanism used. If the performance measurement system is biased toward high inventories, then there will be high inventories. However, the production scheduling mechanism used will have an impact on the ability to locate systemic problems and implement improvements (Naylor 2002). On the other hand, when large buffer stocks are present, a batch of defective parts may simply be scrapped while the production process continues uninterrupted. Thus, the problems that caused the defects remain invisible and unsolved while losses resulting from poor quality accumulate. These losses may, in the long run, far exceed the cost of a shutdown (Slack et al 2003).
Measurement of Operations Strategies
KPI’S means of performance measurement tend to bias the decision-making process in the direction of higher inventories. For KPI business activity monitoring is used. These means include the cost accounting system as well as the local measures of performance used on the floor. The following scenario could occur in a multitude of industries: An order is received for five hundred pieces of a certain item (Slack et al 2003). A 100,000-piece production run is made. One year later most of the extra pieces produced have still not been sold. The reasons why this seemingly irrational waste of raw material and capacity has occurred lie in the performance measurement system. First, the performance of the plant is measured in pieces (tons or square feet) produced, not in pieces shipped or sold. The 100,000 items contributed to production for the month, even though they did not lead to comparable shipments and, in fact, may have delayed shipments of other orders. Thus, a setup for only five hundred units would have resulted in a heavy penalty in overhead cost allocation (Eboch, 1998). By making the longer production run, the standard cost per unit was reduced. Third, the work centers involved in the production of the items are evaluated on efficiency (standard hours/actual hours worked) and utilization (direct time charged/clock time scheduled) for machine time and labor time (Slack et al 2003).
Inventory holding costs, as traditionally measured, are so incomplete in their representation of the real cost of inventory that they are misleading. The real cost of inventory, stemming from its role as a barrier to improvement, is the waste caused by these hidden problems. Inventory is used to cope with the symptoms of problems, for example, unpredictable product quality. However, its effect is to make these same problems less visible and much more difficult to track (Slack et al 2003). The absence of inventory will also permit defects to be discovered as they occur (Naylor 2002). This facilitates tracking the causes of defects, so that process improvement becomes easier. Thus, any inventory between these two steps is a barrier to improvement, and a cost of inventory is incurred. Inventory makes it possible to live with machine breakdowns, unreliable vendors, inaccurate inventory records, unpredictable yields, long and unpredictable setup times, absenteeism, unreliable forecasts, long and unpredictable lead times in processing customers’ orders, poor quality, and poor scheduling (Hage, 1999).
Conclusion
Hitachi Koki deliberately plans a competitive strategy based on excessive inventory levels and long customer lead times. Thus, there are some deficiencies in the organizational systems that can be solved only through a process of systems improvement. The applicability of operations strategies mentioned above is obviously greater in processes producing high volumes. The ideas for waste reduction used in conjunction with these systems are generally applicable: setup time reduction, better quality control, flexibility of workers, and flexibility of the production process. The benefit of operations strategies introduced by Hitachi Koki is that they focus attention on the need for accuracy of the inputs — inventory records, customers’ orders, forecasts bills of materials, and yield formulas.
References
Calingo, L. M. (1996). The evolution of Strategic Quality Management.” International Journal of Quality & Management, 13 (9), pp. 19-37.
Chase R.B., Jacobs R.F. (2003). Operations Management for Competitive Advantage with Student-CD, Hill/Irwin; 10 edn.
Hitachi Koki Home Page. (2008). Web.
Eboch, Karen, (1998). “The TQM Paradox: Relations among TQM Practices, Plant Performance, and Customer Satisfaction.” Journal Of Operations Management, pp. 59-75.
Harris N. (1989). Service Operations Management, Cassell.
Hage, J.T. (1999). Organizational Innovation and Organizational Change. Annual Review of Sociology. p. 597.
Johnston R. (2003). Cases in Operations Management, 3rd Edition Pearson Education Limited.
Naylor J. (2002). Introduction to Operations Management, 2nd Edition Pearson Education.
Slack N., Chambers S. Johnston R. (2003). Operations Management FT Prentice Hall.
Appendixes
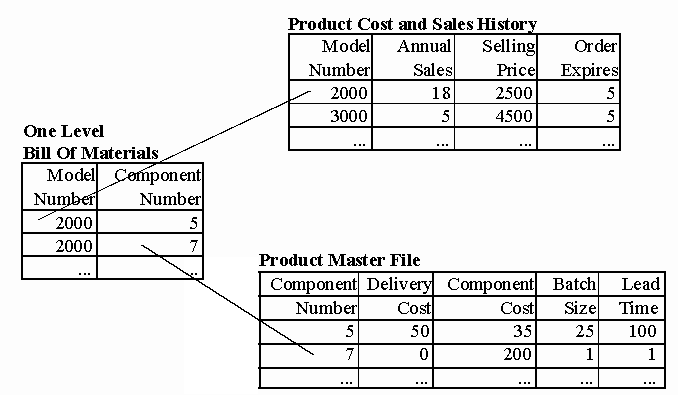
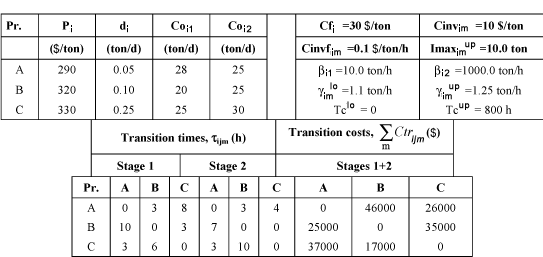
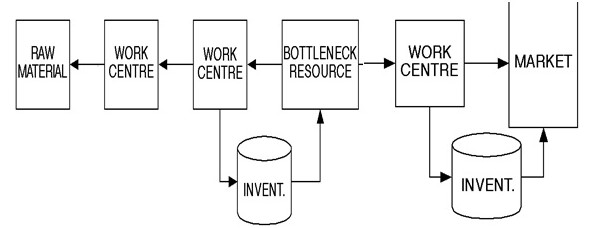