Introduction
Nissan is a Japanese auto manufacturer founded in 1933, one of the largest in the world. As of 2018, it ranks the 8th in the global automaker ranking (3rd among Japanese manufacturers, after Toyota and Honda, according to the American Customer Satisfaction Index Home research (Sauter & Suneson, 2018). The headquarters of the company is located in Yokohama since 2011, and 44.4 percent of the company’s shares belong to the French company Renault.
This paper aims at analyzing Nissan’s disaster response made by its operations management based on the given case study and outside reliable sources. In particular, the earthquake, nuclear emergency, and tsunami occurred in 2011 significantly reduced the production of Nissan and allowed testing its preparedness to emergencies. In this paper, Nissan’s competitive advantage, operations, techniques and theories, supply chain strategies, and sustainability will be examined.
Generating Value
Operations management (OM) that refers to managing processes and operations includes a range of functions, among which there are strategy, finance, product design, operation, and forecasting. The effective operations management promotes accurate and successful product delivery and increases customer satisfaction (Heizer, Render, & Munson, 2016). In this connection, OM functions should be implemented by managers who are responsible for one or another area of operations. The review of the Nissan case study shows that this company applied several OM functions to respond to the disaster. It should be stressed, at the same time, that these functions are used not only to handle emergencies but also to create comprehensive product management.
The first function is a strategy that should be understood in this context as a way to plan tactics that will be used in case of difficult situations. The so-called crisis mentality that was adopted from the very beginning implies that Nissan conducts thorough research and analyzes potential threats and their impacts, which helps in revealing risks as soon as possible. As the case study demonstrates, the company conducted studies and was ready to implement countermeasures when the crisis occurred in 2011.
The second function may be identified as operation, which may be traced in how Nissan organizes and maintains overall control of its products. For example, it is possible to note that the company has a dedicated risk management, a great part of which is responsible for operations. Forecasting is another function utilized by Nissan, which is expressed in anticipating customer demand, costs, and other essential aspects.
Nissan achieves its competitive advantage through the globalization of its operations. Namely, when Japan’s politics become less protectionist, the company opened its manufactures in the US, India, and several European countries. This allows reducing the damage from disasters and economic crises since a range of branches may substitute the plants that were affected, thus providing necessary elements.
The identified strategy of achieving the competitive advantage proved to be successful in 2011, and Nissan continues to follow it today as well. The principles of just-in-time manufacturing also seem to be useful for Nissan that pushes processes and materials only when needed by the specific conditions on the market or inside the company.
Both service operations and manufacturing operations in Nissan focus on planning and designing the working environment by presenting mission and vision statements. For example, the company’s vision is associated with enriching people’s lives, and the mission is providing a unique and measurable experience in cooperation with Renault. Accordingly, this reflects how the company’s service operations and manufacturing operations are designed.
However, if manufacturing operations present tangible products and consider layout, service operations are more oriented on customers’ expectations. In terms of manufacturing operations, Nissan creates standardized products, while its service operations target an individual approach to provide value for different categories of customers: families, entrepreneurs, and so on.
Theories and Techniques
Gross-to-net calculations may be processed for material requirements planning (MRP) by identifying gross material demand and subtracting the inventory in stock. After that, the result should be added to the safety stock to calculate the ultimate numbers (Heizer et al., 2016). A set specific input files should be considered by Nissan in the given case. In particular, current inventory, expected receipts, production cycle, a bill of materials, and a master production schedules should be added. The MRP information may be utilized by Nissan to calibrate its delivery times and raw material requirements, thus enhancing the overall performance of the company.
Based on the case analysis, one may state that the critical path method (CPM) may be used by Nissan for a project that is known and clear. For instance, CPM is beneficial to identify and monitor the start time of the project to control costs and timeframe (Heizer et al., 2016).
This method suggests that factors affecting a product are predictable and should not be deviated. CPM is better to use in the period of development and expansion, for example, to compute the most relevant start of a new model introduction to the market. Since the program evaluation and review technique (PERT) is a more detailed strategy that contains three estimates for each of the aspects, it can be used by Nissan for complicated and structured projects. In case a project aims at creating a certain model of vehicle, the above option will be the most suitable one. The construction of a new model includes a lot of stages, and PERT is likely to allow monitoring and managing all the process from the very idea presentation to the ultimate product development stage.
Sequencing, also known as dispatching, means the specification of the work to be done by managers. There are four primary sequencing rules such as the earliest due date (EDD), first come, first served (FCFS), the longest processing time (LPT), and the shortest processing time (SPT) (Mahadevan, 2015). According to the FCFS rule, tasks are to be completed in the order they appeared, which is advantageous for customers who order early.
The company may use FCFS to attract more clients at the initial stage, yet it creates longer waiting times for others. EDD should be used by Nissan in cases for orders with the expedited due date; however, customers who did not require the above service would be taken out from the top list (Mahadevan, 2015). SPT is advantageous for smaller orders as they will be processed sooner compared to larger orders with greater value. Accordingly, LPT is the opposite sequencing rule that is relevant for larger orders.
Five steps of the theory of constraints (TOC) process are identifying the constraint, exploiting it, subordinating and synchronizing it, elevating its performance, and repeating the process. The constraint that limits the production should be found, critically examined, analyzed in the context of internal and external factors, eliminated, and the first four steps should be repeated as continuous improvement measures. Nissan may apply the described process to its supply chain management to ensure that even if some plants will be impacted by natural disasters, others will be able to substitute them and minimize costs. By arranging the transportation of necessary parts and scheduling of delivery, it is possible to reduce down times, which will affect the whole company in a positive manner.
Nissan used forecasting as an integral part of its OM, which includes a seven-step system. There are determining the use of the forecast, choosing the items, identifying timeframe, selecting the model, collecting data, making the forecast, and implementing the results (Lim, Alpan, & Penz, 2014). First of all, Nissan can decide which of the areas it should predict; it may be sales, new expansion markets, et cetera. Second, product demand after the disaster may be selected as the target item in the period of one year. The model based on quantity variables may be used, and data gathering sources may be pre-orders and the general economic behaviors. Ultimately, forecasting results should be validated to make sure that they are correct (Lim et al., 2014). In case forecasting is applied to the top-selling product line of Nissan, it will promote the maximization of sales as the future demands will be relatively clear. Also, the company will have some time to add features valued by customers.
Among the key categories of supply chain risk, one may list logistic delays, quality reduction, vandalism, natural disasters, theft, and terrorism. When Nissan encountered the earthquake and tsunami in 2011, it was able to handle the situation due to several plants located in different regions of the world. Along with the globalization tactics, Nissan utilized such risk-reduction tactics as personnel training, so when the emergency occurred, plants positioned outside Japan were able to provide high-quality products and avoid logistic failures. Nissan’s IT system is another tactics that is helpful to collect, store, and analyzed necessary data.
Just in time (JIT) is a theory directed to solve problems based on reducing inventory and a focus on throughput. Its main advantage for Nissan is the opportunity to reduce costs and implement customers’ preferences, while its disadvantage is essential coordination needs. Toyota Production System (TPS) refers to standardization and continuous improvement regarding people (Heizer et al., 2016). In Nissan, TPS helps to decrease waste and lead smooth production processes, while its drawback lies in high costs of implementing it. The Lean theory targets what exactly a customer wants by optimizing processes, which is the key advantage in the context of Nissan. However, Lean may cause employee frustration and inefficiencies while used in combination with JIT.
The use of the total quality management (TQM) with regard to Nissan’s latest product line may significantly improve its quality and increase sales. By employing such tools as Six Sigma, focus groups, and Pie charts, Nissan may track the improvements and failures and respond as soon as possible by adjusting its strategies (Oakland, 2014). A focus on customers, employee empowerment, communication, and constant improvement are the core principles that may be applied to ensure the highest quality.
Data Analysis
The fowling map may be used by Nissan while planning its operations management and focusing on all stages of manufacturing. In particular, it is expected that the given map utilization will reveal any weak points and eliminate logistics failures and delays. In addition, the company may adjust this map and use it to understand the amount of inventory required to ensure that the demand will be met by the supply.

The cause-and-effect chart below demonstrates why some of Nissan’s rivals failed to cope with the natural disaster of 2011. It should be emphasized that the earthquake caused nuclear meltdown and tsunami, which led to the fact that many suppliers were unable to provide products on time. Managers were concentrated on addressing the disaster consequences and made quick decisions which slowed the processes. In addition, employees and customers were also affected by the crisis either professionally or personally. The roots of import and export were obstructed by the difficulties. While Nissan had a properly prepared disaster response plan, its competitors had to build a solid foundation for recovering from its negative impact.
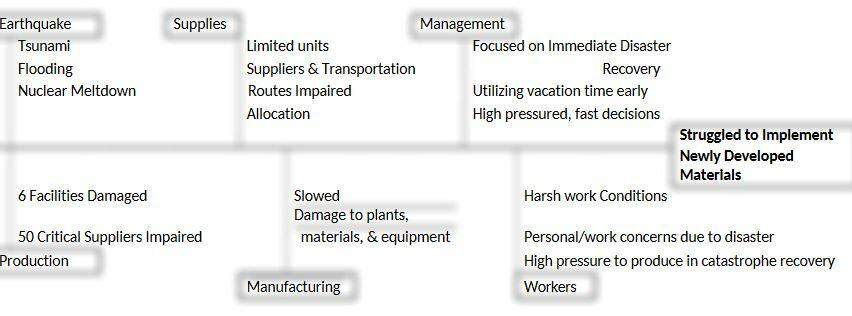
Based on the data from the suggested table, it becomes evident that Nissan should locate its new plant in Mexico City since it possesses the highest factor-rating compared to other places. Namely, there is less political risk, higher labor productivity, and transportation costs in the mentioned location. Therefore, it may be concluded that, probably, Mexico City is more relevant expansion place for Nissan compared to Columbia, SC.
ABC classification system is a ranking method that allows identifying the most effective solutions. The below figure shows the items that cost for than others, which is useful for Nissan to consider potential options in their business. It is possible to recommend ordering the item A2 as it composes only six percent of the whole company. As for the section B, one may recommend Nissan to continue ordering with the trend and store some surplus to use it in the future.
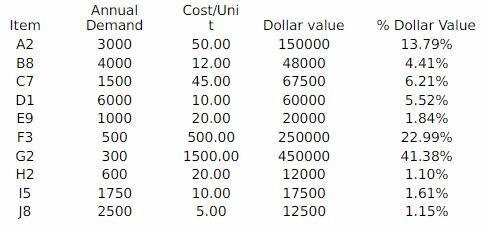
Sustainability
Currently, the concept of corporate sustainability is understood not only as a company’s approach to ensuring its long-term development but also as a field through which it works to improve the viability of communities. The triple bottom line (TBL) approach aims at building a business, according to which entrepreneurs and managers should take into account financial indicators as well as the social and environmental performance of a company.
The three elements of the identified theory that are applied by Nissan are people, planet, and profit (Heizer et al., 2016). The number of public initiatives that require companies to disclose information on the results of their activities in various aspects that are important to society is growing exponentially. To improve operations management of Nissan, TBL may be used to make contribution to global and local sustainability. The concept of TBL allows focusing on issues such as human rights, working conditions, and the deteriorating state of the environment.
ISO 14000 international standards set requirements for environmental management systems to provide organizations with tools for developing policies and reducing environmental pollution (Mahadevan, 2015). Nissan goes in line with these standards by building its operations management in consistence with them, which includes the organizational structure, planning, distribution of responsibility, and practical activities.
Also, its procedures, processes, and resources necessary promote the development, implementation, achievement of environmental policy objectives. Nissan Kama Operation, Nissan Research Center, and Nissan Advanced Technology Center manage the accomplishment of environmentally-friendly strategies. Some of the models integrate zero emission technology and use electricity to drive the vehicle.
One of the ways to support corporate responsibility is to launch a special program that was done by the company. Nissan Program 2022 calls for “actions to be taken on four challenges: climate change, resource dependency, air quality and water scarcity” (“Sustainability at Nissan,” n.d., para 7). The design of the operations of the company accordingly targets the mentioned actions. Integrity, honesty, and respect for others are the main principles of corporate responsibility, which are built in Nissan’s operations management. For example, by utilizing Lean, JIT, and TPS, the company not only reduces waste but also cuts fuel costs and spending on transport supplies (Mahadevan, 2015). It is possible to state that the use of JIT also provides the opportunity to effectively communicate with partners and work together on social and environmental problems.
Conclusion
In conclusion, Nissan is a company that successfully integrated a range of tools and strategies in its operations management, which allows not only develop but also withstand natural disasters. The case analysis shows that the company applies such strategies as JIT, Lean, and TPS to manage its operations, services, and procedures. The key idea that allows Nissan to survive from the crisis of 2011 faster than its rivals is the focus on the globalization of its plants.
While Japanese plants were damaged, the global suppliers provided necessary details and demonstrated a high quality fie to timely training. The company’s vision of enriching customers’ lives is implemented via a properly-designed supply chain and total quality management. Nissan’s corporate sustainability adherence is expressed in such areas as reducing emissions and waste in general as well as ensuring appropriate working conditions for its employees in all the locations.
References
Heizer, J., Render, B., & Munson, C. (2016). Operations management: Sustainability and supply chain management (12th ed.). New York, NY: Pearson.
Lim, L. L., Alpan, G., & Penz, B. (2014). Reconciling sales and operations management with distant suppliers in the automotive industry: A simulation approach. International Journal of Production Economics, 151, 20-36.
Mahadevan, B. (2015). Operations management: Theory and practice (3rd ed.). New York, NY: Pearson.
Oakland, J. S. (2014). Total quality management and operational excellence: Text with cases (4th ed.). New York, NY: Routledge.
Sauter, M. B., & Suneson, G. (2018). What are the best and worst car brands in the US in 2018?. USA Today. Web.
Sustainability at Nissan. (n.d.). Web.