To idealize operations strategy, we need to first think about its two major components- operations and strategy. Operation means activities and procedures implied in regular process of commodities manufacturing. Strategy refers to the planning for achieving organizational objective. Stevenson, W. J. (2006), argued that combining those aspects, operations strategy is narrower in scope dealing primarily with operations aspect of the organization. It is related with the products, technique, method, quality, and value and scheduling. A core model of operations strategy development has presented here as follows:
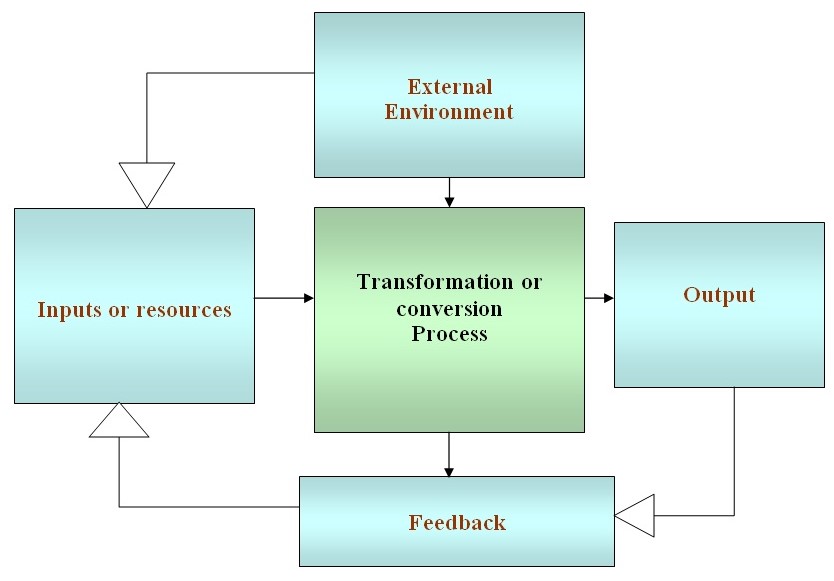
Stevenson, W. J. (2006) also mentioned that operations strategy must be consistent with the entire strategy of the company that requires the senior managers’ work with functional units to formulate strategy. They will support, rather than disagreement with, each other. They should support the overall approach of the company.
For better understanding the detailed form of the model would be as follows:
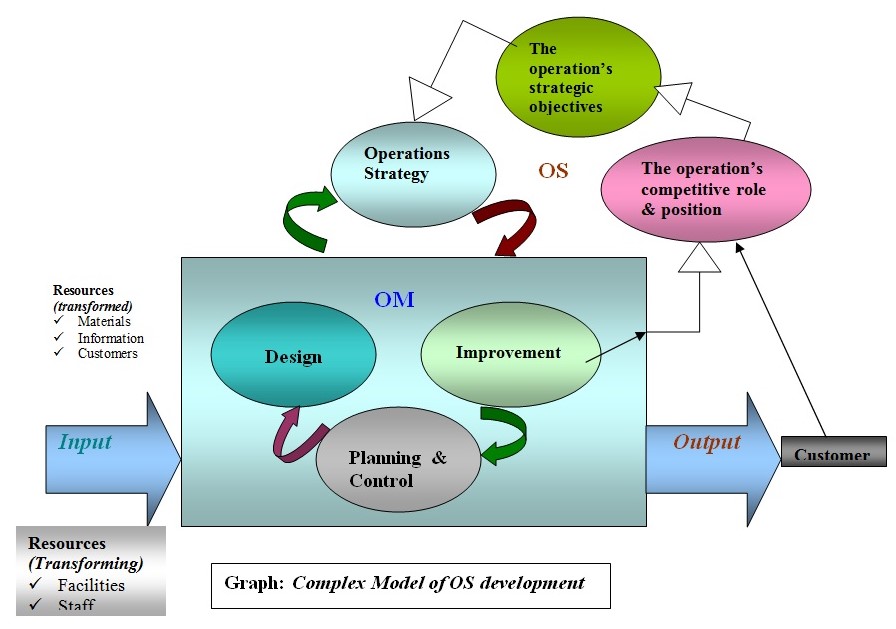
This model emphasizes on operation regarding frequent level of capacity as well as responsibility involving the global and domestic cases. It also enables the international and the national managers to pose certain responsibilities at a top position that reflects newer managerial challenges.
The presented operations strategy model has been developed on the basis of market timing, services and cost purposes that can be derived from commodity demand supply complexity. Here, “demand factors” has involved differentiation, planned obsolesce, freshness etc. and “supply factors” involve cost factors, materials and other complexities.
In this aspect, we can exemplify “Zara”, a top fashion oriented Spanish company as a better performer of developing operations strategy in the light of this model. The company has focused on business goals for an individual line of goods at an optimistic level. It introduces up to 11000 of exclusive designs yearly. Thus, it has considered a model of 5 weeks for product development purpose reversing the benchmark’s ratios of 9 months. As average fashion items place short run sales and profits, a time to market model of supply on the basis of urgent review from shops has been deployed by the company. In such case, the manager of every store locates customer review and transmits it to the regional manager who is responsible of passing that information to the product development unite that can spontaneously produce new design which would be enable to satisfying the updated needs.
For this primary model, Zara basically utilizes Spanish onshore manufacturer as well as in Portugal accompanied a number of Asian suppliers because of the increased demand in Far East. Additionally, it records advanced capacity of manufacturing with the word of producing a specific number of blouses previous to the knowledge of styles and colors. Contracting instants customer feedback and recording the advance onshore capability enables Zara to place updated goods on store within 4 weeks of the time a store manager recognizes a popular trend in fashion. The European, American and Asian stores are replaced at the average of 2 in weeks while the general self life of items is 2 to 3 weeks.
The base line products, like- underwear and T- shirts consists a category representing below 30% of profits while the company believes on low- expense offshore or closer- shore producers in China and Morocco.
Following Zara, many automobile marketers also maintain such basic model rather than supply or purchase operations as their strategic development.
Adoption of postponement
Postponement can be defined as a task of handling the complete product configuration till to the original order as it is, making the firm eligible of responding instant to the market need through a reduction in inventory costs and delayed scheduling.
Since forecasting of international demand is confined with uncertainty, for the efficient management, anticipation of demand enhancement and taper off can be attempted. Regarding this, merely many people had fallen in problem that made them understood for accepting postponement tactics.
Insufficient inventory in product cycle can loose market share associated with planned obsolescence for which many businessmen are adopting postponement by which they can swiftly move to market scopes with a larger mass customization facility. By adopting postponement technique, companies can avoid cost pressure as well as limited life cycle. Other issues are:
- It offers a better competitive advantage in the market through enlarging customer service and decreased inventory.
- Enables to gain small forecast cycles through a move of upward stream of inventory to the less costly condition. Thus, it can combine benefit of a reduction of the impact of market instability by accepting the marketers to satisfy customer demand for managing the expenses of logistics and supply chain appropriately.
- Enhanced flexibility that can be born by postponement offers the marketers capacity to provide a broad circle of customized products which is the benefit that affords significance for the first point.
Christopher, M. G. (2005) addressed that to creating an effective supply chain management requires linking the markets, distribution channels, processing and suppliers. The design of a supply chain should enable all participants in the chain to achieve significant gains, hence giving them an incentive to cooperate. It should make possible for contributor to:
- allocated forecasting;
- shaping the category of orders in real time;
- right of entry to the inventory data of allies.
Cohen, S., and Roussel, J, (2005) make it clear that a company’s strategy is the fixture plan of management to design a make out of market position, carry out its operations, create a center of attention, and entertain the customers’ needs. It successfully competes and achieves organizational objectives delivered from its mission statement. Postponement in SCM required putting into practice several tasks. In short, these tasks are:
- Designing a strategic vision to fixed the goal,
- Organizing objectives to carry out this vision,
- Designing a strategy to achieve the most wanted outcomes,
- Put into practice and carry out adjustments in vision.
Finally, it can be said that this approach is very much effective as it can minimize supply chain costs, reduce procurement, shipping, infrastructural and manufacturing expenses along with better order filling accuracy with high degree of satisfaction although most of the businesses are incapable of adopting so.
Adoption of mass customization
It is the replacement version of mass production for adopting in present turbulent markets, rapid product differentiation and e- commerce scopes. Other features are:
- Used for individual customer service like- bicycle.
- Customization of niche market like- telephone companies.
- Variation in “standard” goods like- electronic products.
In short, it would enable to serve customized products as well as a speedy re- provide the stores with required goods which have passed with the replenishment of built- to – order system and finally, for the suppliers of industrial units, it introduces demand responsiveness on pull basis as a supply chain module by which a market can be served in better way to meet the target customers.
Typically saying, operation management works with the business area associated with goods and service production, responsibility relative to optimum business efficiency. For, that purpose of effective planning, use, timing and control, an operation manager must asses his/ her performance in the context of competitors through the relative importance of goods and services to the target customers. In this regard, marketing of the company must influence competitiveness in several ways. Like:
- Identifying customer needs and wants is a centre of competitiveness. This ideal is to achieve a perfect match between those wants and needs and the organization’s goods and services.
- Pricing is usually a key factor in consumer buying decision. It is important to understand the trade- off decisions consumers make between price and other aspects of a product or service such as quality.
- Advertising and promotion are the ways managers can perform potential consumers about features of their goods and attract buyers.
Operation can influence competitiveness through a number of factors as shown below:
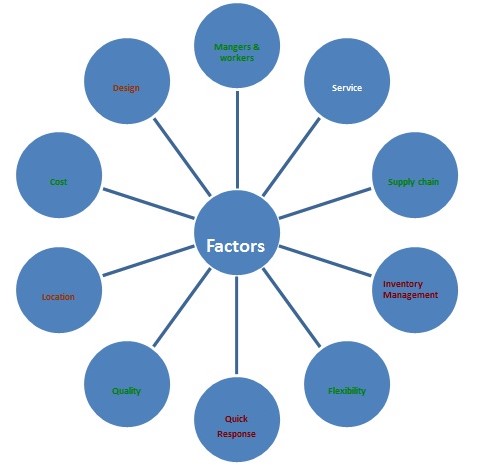
- Product and service design should reflects joint efforts of many areas of the management working together to achieve a match between financial resources, operations capabilities, supply chain capabilities and consumer wants and needs. Also, special characteristics of a product or service can be a key factor in consumer buying decision.
- Cost of a company output is a key determinant of price, productivity and profits.
- Location can be vital in aspect of cost and for the convenience of customers. Location near inputs can result in lower input cost. Location near markets can result in lower transportation cost and quicker delivery times. Convenient location is particularly important in real sector.
- Quality offers a large competitive advantage since customers are normally willing to give high for a commodity or service if they are perceived as higher feature comparatively better than the competitors.
- Quick response can be ensured in number of processes. Firstly, launching of a new item. Then, quick delivery of current goods after ordering and finally, attention of customer complains.
- Flexibility offers a drive to change. Changes might be alternative features in design, or to the quantity as demanded by people, or a traditional mix of items by the company.
- Inventory management can be a competitive advantage by effectively matching supplies of goods with demand.
- Supply chain management involves coordinating internal and external operations (buyers and suppliers) to achieve timely and cost- effective delivery of goods throughout the system.
- Service might essential after- sales of the products. These are perceived by customers as value- added, for example delivery, set- up, assurance work, any technical support, development, and informing the customers and attention to detail etc.
- Competent managers and staffs are the heart and soul of the entire process because if they are experienced and motivated then they can provide a distinctive competitive edge by their skills, proficiency and ideas.
However, the overall corporate strategy should focus on distinctive competitiveness like the following:
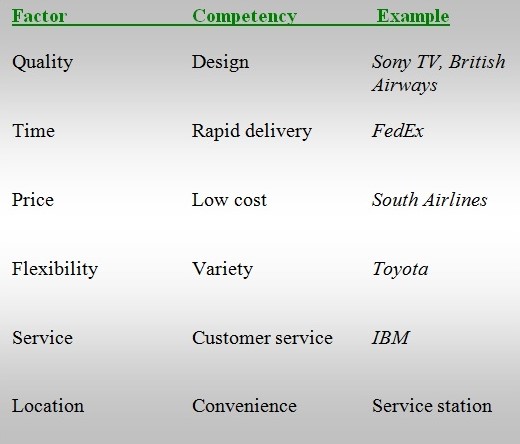
Additionally, the importance of ethical behavior is very much important that works as a catalyst in such case.
An inventory is the stock of store of products. Not only are they necessary for operations, but also they contribute to customer satisfaction. The versatile functions of inventory are describe as follows:
- In order to meet anticipated customer demand: Inventories are indicated as anticipation stocks because they are held to fulfill predictable demand.
- To decouple operations: Recently, companies have taken a closer look at buffer inventories.
- In order to smooth invention requirements: Some garments produce jackets, over coats and sweaters are example of seasonal inventories.
- In order to protect against supply out: there are many reasons which create crisis in market. To overcome this risks of shortage holding safety stock play vital role to reduce it which are in surplus of average demand of the market.
- In order to hedge against price increase: It allows a company to take benefits of price discounts for larger order.
- In order to take benefit of order cycles: Stevenson, W. J. (2005) argued that inventory storage facilitates a company to purchase and manufacture in economic lot sizes to reduce price without having to try to match manufacture with demand necessities in short run5.
- To permit operations: Intermediate stocking of goods leads to pipeline inventories throughout a production- distribution system.
- In order to obtain benefit of quantity discounts: Suppliers may give discounts on larger order.
EOQ method to minimize inventory costs
The basic inventory costs are of three types- holding, transaction and short- age costs which incurs a high amount. Therefore, to minimize that costs, EOQ model is used which identifies the fixed order size. It will reduce the sum of the annual expenditure of holding inventory as well as ordering inventory. The unit purchase price of items in inventory is not included in TC (Total costs).
Assumptions:
- Only a single product is involved.
- Known demand requirements per annum.
- Demand has extended all over the year etc.
Inventory procedure and practice goes through cycles, such as:
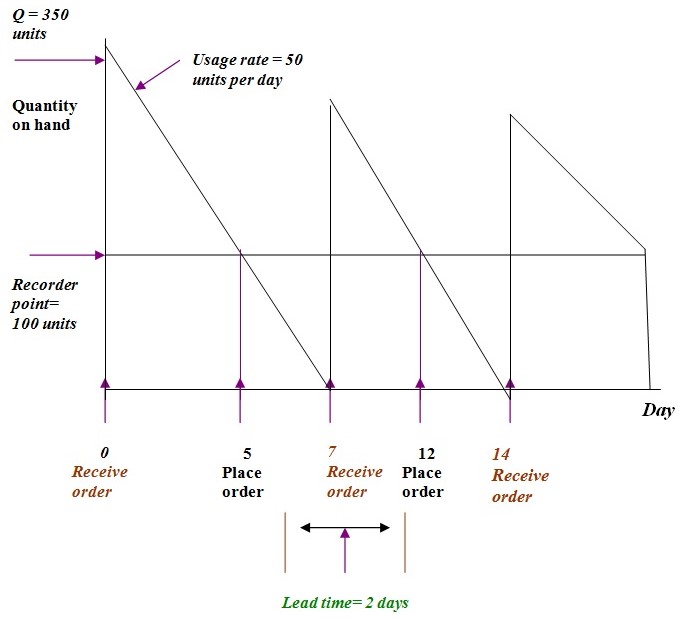
Christopher, M. G. (2005) pointed out that a cycle begins with a receipt of an order of Q units that are withdrawn at an invariable rate over time. While the quantity on hand is just adequate to gratify demand during lead time, an order for Q units is submitted to the seller.
The optimal order quantity reflects a balance between carrying costs and ordering costs. As order size varies, one type of cost will increase while the other decreases. As a result, the idea solution is an order size that causes neither a very few large orders nor many small orders, but one that lies somewhat between. Fred, C.P. M. Sollish et al (2007) stated that the average inventory is just half of the total order quantity. The amount on hand decreases gradually from Q units to 0, for an average of (Q+0)/2, or Q/2. Then by using the symbol H to illustrate the average annual carrying cost which is as follows,
The carrying cost is as a result of linear function of Q. Stevenson, W. J. (2006) stated that these costs are expand or reduce when the order increases or decreases because for a given demand per year, the larger the order volume, the fewer the size of orders required.
Christopher, M. G. (2005) said that these annual ordering cost is the function of the number of orders for each year and the ordering cost for each order:
Christopher, M. G. (2005) also mentioned that the total annual cost connected with carrying plus ordering inventory while Q units are ordered every time is:
TC = the Annual carrying cost + The Annual ordering cost
The following figure will reveal that the total- cost curve is U- shaped and thus it reaches its minimum at the quantity where carrying and ordering costs are equal:
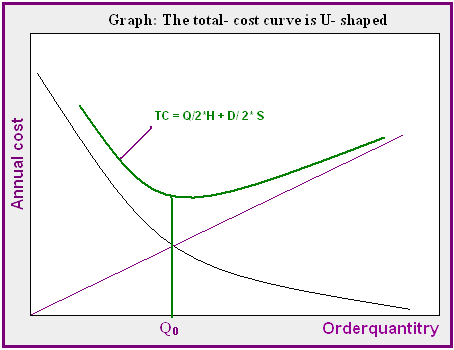
An expression for the optimal order quantity, Q0 be obtained using calculus and the result is Q0 = √ 2DS / H. Thus, with the above points, one can compute economic order quantity that can be used for holding inventory at a minimum level.
Conceptual view
Operation management is the management of the part of an organization that is responsible for producing goods and services. Regardless service and manufacturing context, each company has 3 basic functional areas as following:
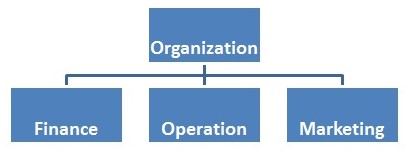
Similarly, the operation function involves the conversion of input into outputs in the following manner:
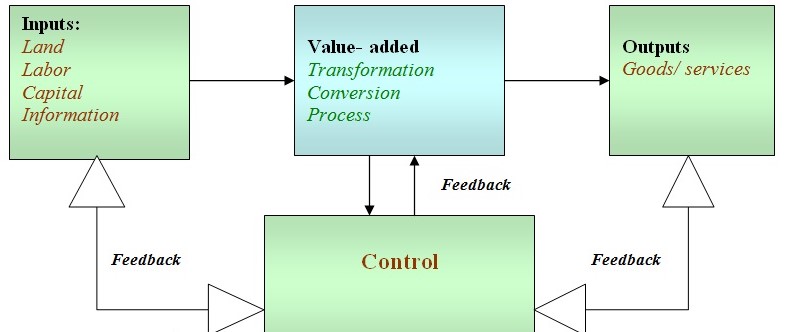
Thus, the concept of operations management for both types of businesses will focus on design engineering, industrial engineering, quality management, management information system, accounting etc. It also emphasizes on producing output through value- addition which describes the difference between cost of inputs and value of outputs. Thus, the design engineering will command a group of designers for the essential prototypes for construction or building with solid modeling software, CAD, CATIA etc. for every organization.
In case of industrial management, along with manufacturing system, industrial or management engineers are also active for service centre like hospital.
MIS is a set of internal control of people, procedure, technologies, to solve project problems and it typically supports the decision making, support system, executive information and executive system.
Accounting is any procedure, judgment, measurement or statement regarding financial data used by investors, managers, tax department, creditors, and general public regardless types of the company.
Model view
It is an abstraction of reality which is the simplified version of something.
Schematic model involves graph and charts, blueprints, pictures and drawings which are commonly used for solving service context. Mathematical models are more abstract which includes numbers, formulas and symbols that are easiest to manipulate and are important forms of computers and calculators.
They can be applied for such purpose as:
- Systematic approach of problem solving.
- Increase understanding of the problem.
- Consistent tool for evaluation.
- Analysing the ‘what if’ question and
- Bring the power of mathematics to bear on a problem etc.
Tools and techniques view
The operation management requires a number of decision tools and techniques for solving a problem. By using the quantitative approach, it is possible to solve optimal solution to the managerial problems. Linear programming and mathematical techniques are widely used for this. As manufacturing firms use inventory models, service agencies can use project models (PERT and CPM) for planning, forecasting and control projects. Additionally, forecasting and statistical models are currently used for decision making.
Therefore, both types of criteria involve design and operating decisions while manufacturers decide on size factory and service companies decide on size building as an effective application of operations management.
The ‘Lean’ strategy
Normally, lean is defined as a way which is streamlined for the reduction and isolation of invaluable activities with the flow of supply chain and product placement. Such wastage can be assumed in stocks of inventory, time and unusable costs. Thus, lean is the process that benefits larger, small and the middle wholesalers, retailers and distributors.
Mainly this process is appropriate for the removal of useless inventory and time. Thus, a lean strategy of supply chain will be pull which draws back from the shop by buying orders have been submitted to the suppliers. Factors that delay such flow should be evaluated as a non- valuable one. And, while the company has an option to pose more time, like a year, then lean strategy will be fruitful.
The ‘Agile’ strategy
It can be viewed as a concept that is less visible on the output of the process while the supply chain acts as a major function. A number of agile control tools are CVS, subversion, which posses confined but adequate effectiveness. The agile incorporation can be realized by the following criteria:
- It is helpful for version management through the security, control and recognizing the assets of project.
- It is perfect to capture and recognize all sorts of changes in project.
- It is reliable and stable in software management through the output and feature.
- It is also effective in coordinating challenges, milestone history by rendering the capacity of customization of working procedure.
In short, it can be implemented in:
- A simple branching strategy as supply chain tools branches can be formulated with low cost. Implementation in the active development line can also be effective.
- It should work in incremental inquiry.
- Configuration or design within the optimistic lock is also useful9.
- To evolve the integration problem, continuous integration is necessary.
- It normally “stage” and utilize repeatedly pre- formed binary process.
- Revealing and deployment at a continuous basis etc.
The advantages of both the procedures can be combined to manage effective supply chain. Reduction of time, blending of several distinctive competencies, like- cost, quality and reliability, flexibility, equipment, innovation and product mix can make an effective application of those procedures.
As we know that polar diagrams are helpful for measuring the potential necessity of performance goal to the process while competitiveness is an important factor in whether a company prospers, barely gets by or falls.
Thus, marketing influences competitiveness in many ways, including identifying consumer wants and needs, pricing, and advertising and promotion. To make a comparison between a subway service and a taxi service in the light of polar diagrams, we need to consider first the 5 performance objectives regarding this issue like the following-
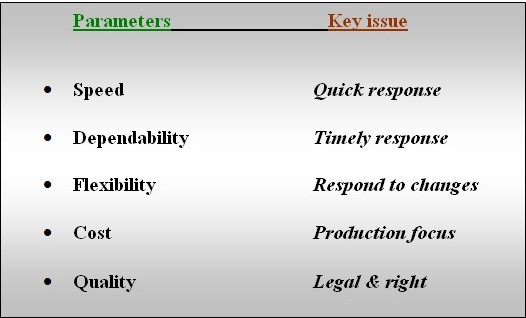
Details
Speed: Speed can be competitive advantage. Christopher, M. G. (2005) specified that quickly bringing new product or service in the market, instantly delivering existing product and service to convince the intended purpose and rapidly handling customer complains are some ways to amplify speed. Thus, subway service is quicker than taxi service that works as an important competitive advantage for it.
- Dependability: It reflects on timely response while subway provides the best time conscious service to the customers than taxi.
- Flexibility: It is the ability to respond to changes. It can be a competitive benefit in a variable environment. Changes might relate to alteration in design of the transportation service, or to the volume demanded by the customers. In this regard subway is somewhat rigid that taxi service relating schedule, ways or other means.
- Cost: Cost is an important determinant of price decisions, productivity and profits. Cost reduction efforts are generally in taxi rather than subway system.
- Quality: it means to material, objectives, workmanship plus design11. Customers normally judge the quality of a transportation service while it satisfies their intended purpose. So, regarding quality subway is more efficient than taxi to satisfy customer belief or purpose to travel.
Thus, taking such variables in mind, the Polar diagram for taxi and subway service can be drawn below:
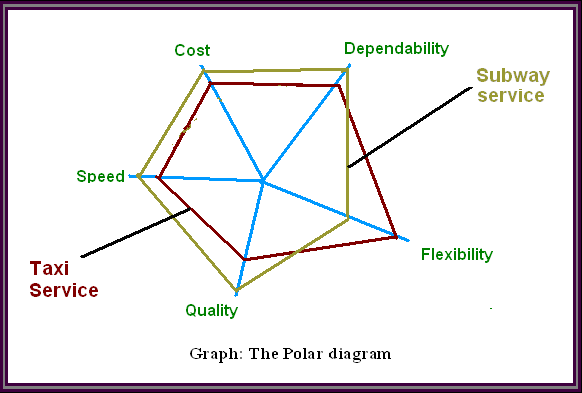
Among a number of functions of inventory management, the question of how much to order is frequently determined by using an EOQ model. The next figure will demonstrate how inventory is affected by occasionally producing of batch of a specific time:
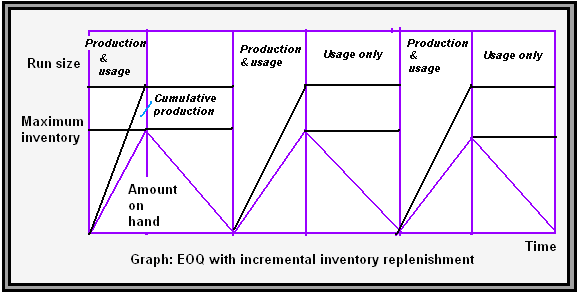
Ferrer J. and Karlberg J. (2008) stated that during the production phase cycle, inventory makes up at a rate equal to the distinction between production and usage rates. For example, if the daily production rate is 20 units and the daily usage rate is 5 units, the inventory level will build up at a rate of 20-5 = 15 units per day. Chopra, S., Meindl, P. (2008) argued that providing production occur and the inventory level will persist to construct when production ends and the inventory level starts to decline. Therefore, the inventory levels will higher at the point when the production stops. The manufacture is resumed when the number of inventory on hand is exhausted and the cycle reiterates itself.
Apparently there are no ordering costs where the manufacturers produce their product. However, there are set up costs for each production. The costs needed to prepare the tools for the employment for example cleaning, adjusting and altering tools and fixtures. These initial costs are related to ordering costs since it is free of the lot size. The greater the run amount, the fewer the total of runs desired and the lesser the annual set up costs. The number of runs per year is D / Q, and the annual set up cost is equal to the number of runs per year times, the set up cost, S per run: (D/Q) S.
The total cost is, TC min = Carrying cost + Set up cost = (I max/2) H + (D/Q0) S
Where, I max = Maximum inventory
The EOQ is:
The function of the run size and usage rate demonstrates the cycle time:
Equally, the run time depends on the function of the run size and the manufacture rate:
Here the greatest and the standard inventory levels are:
From the above argument it can be said that the significance of EOQ model can be idealized in modern management ground.
Ferrer J. and Karlberg J. (2008) addressed that the operations capabilities of the organization are very crucial for the designers to take into account in order to achieve designs that on top form with those potentialities. It is every so often referred as operation method blueprint. The go down of taking this into deliberation could be consequence among condensed efficiency, concentrated quality as well as greater than before cost.
Several factors taking the decision of operation process designing as below:
- Legal, ethical and environmental factors: Designers must be careful to take into account a wide array of ethical and legal considerations. In addition, if there is a forthcoming injury to the environment then those factors are also considered as significant. Among them, the most familiar factors are the Occupational Health and Safety Administration, the Environmental Protection. Cohen, S., and Roussel, J, (2005) addressed that the agency as well as a diversity of state of local agencies are apprehensive with government conventions have need of the use lead- free paint, electrical cabling and plumbing and safety glass in entry ways, etc. as a control of the design of a process.
- Life cycles: Fred, C.P. M. Sollish et al (2007) mentioned that with the passage of time, design enhancements habitually generate more reliable and a reduced amount of costly output. The demand is then grows for detailed rationale as well as ever-increasing attentiveness of product and service. At the maturity phase there are a small number of demand changes, and demand altitude would be off. On the decline phase, some firms will adopt defensive research posture for improving reliability. The life cycle concept can be shown below for process design:
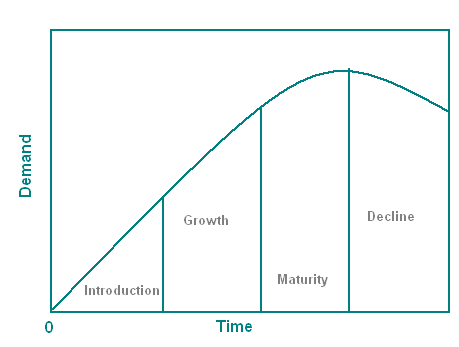
- Standardization: An important issue is the degree of standardization. Stoner, J. A. F., Freeman, R. E., Gilbert, D. R. (2006) explained that standardization refers to the degree to which there is nonattendance of diversity in a product, service or process. The standardized processes deliver homogeneous or fabricate identical goods. Ease of use, compact timing and low down cost to train employees, forecasted schedule of work, regular accounting, dependable quality, and inventory treatment are major advantages.
- Designing for mass customization: Stevenson, W. J. (2005) pointed out that Mass customization is the strategy of fabricating requisite goods in the procedure. It integrates some measures of customization in the concluding purpose through delayed segregation and modular design.
- Reliability: Thompson, A. A., and Strickland, A. J. (2003) added that reliability measures the capability of a total system to carry out its intended function within a prescribed set of preconditions. It is always explicit and is called standard operating environment together with load, humidity changes, temperature, and maintenance of timetable.
- Cultural differences: Process designers of global companies must take into account cultural clauses.
- Degree of newness: It means a fairly easy and quick transition. Bowersox, D. Closs, D., and Cooper, M. B. (2002) explained that delayed arrangement or discrimination is a postponement diplomacy by which the progression could be redesigned as it is the process of manufacturing product, process or service. The postponing completions in anticipation of customer preferences or specifications are known. For goods, more or less completed units must be apprehended in inventory until customer’s orders are established. The customized features are integrated as per customer request. The consequence of deferred demarcation of output with adapted features that can rapidly produced and functional to the customers’ longing for diversity and speed of delivery. The most elements are standardized, facilitating the producer to comprehend the reimbursement of the homogeneous production. Many celebrity firms like HP, Dell, and Wal-Mart have been espoused such practice for the lessening in manufacturing, inventory as well as shipping expenses for the enhancement in rates of order satisfying.
The thought of business innovation mainly emphasizes the newer process regarding specific criteria that can be served for a global purpose. Several authors who have expertise in this topic have identified innovation differently. We may also well-known about the multiple definitions about this concept which seem to be much simpler while they are also vague. Simply, innovation can be any item, thought, & process which are new to a specific area but not essentially to the whole world.
There exist some important principles of successful innovation. Such as:
- Teaming of cross- Company and function.
- Recognition of suppliers as partners.
- Recognition, motivation and rewards.
- The matrix of performance and
- Obtaining the customer’s comment.
- Scrutinizing the design.
- Collective knowledge.
- Technological review on the basis of numerous channeling etc.
In other words, those features can be explained as:
- Innovation is characterized with a vision that reflects risk and change and must not done for any sake rather than a influencer to compress the organization for the system development. In modern context, it should be the driver of vast changes.
- It is customer- oriented that seeks the way to meet customer as well as stakeholder demand through the formulation of financial viability.
- It should be based on ethical structure, that is, an internal organizational trust as well as a pure motive to problem solution and scope must be recognized.
- It should reflect innovative thought which a skill is needed by all within the firm. It refers to the capacity of gradual looks for generating new ideas, productive thinking, effective decision and successful implementation.
- It should focus the entire system through the cause- and- effect relationship.
- It should be associated with versatile, data and interactive environment regarding variability of people, objective and tools.
- It should be risk- tolerant and reward offering to each personnel within management.
- It should be on- going and reflect future trend.
- It should be learning oriented that teaches each person to know something about the product, customer, process, service, company, industry and both external and internal issues.
To discuss the overlap between the design of product and service and process design, we need to understand the following graph first:
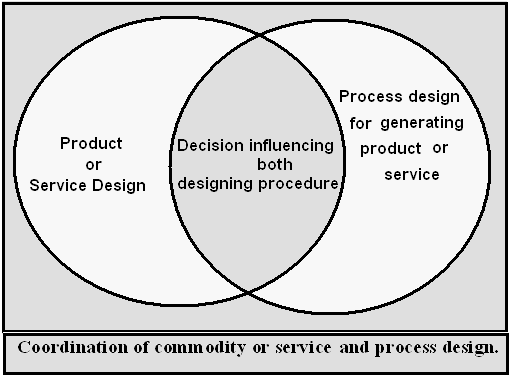
So, the contrast between those issues also exists in design activities as:
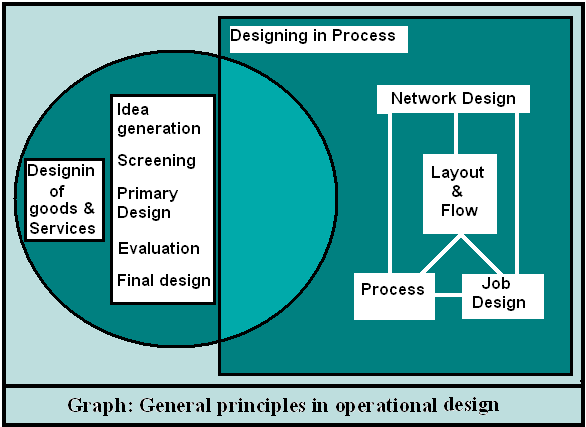
In broader term, such overlapping can be described – for goods and services. The phases of designing of goods and services started with idea generation which is based on 3 sources, such as:
- Supply- chain based
- Competitor based
- Research based
One of the strongest motivators of new products or service is competitors’ products and services by reverse engineering. Wycoff J. (2008) mentioned that the personnel valuable insight can be achieved from surveys, focus groups, dealers, distributors, workers and others. Research is another source of ideas that is generally built by R & D department to provide organizing efforts that are directed toward increasing scientific knowledge and product or process innovation. Wycoff J. (2008) pointed out that the primary idea reduction stage is idea screening which assists spot first-class ideas and drop poor ones without delay. In screening phase, irrelevant ideas are eliminated to get together better ones. After that, preliminary design is prepared for further processing of design. Then, selected idea is evaluated and necessary improvements are made for further acceptance. Finally, prototyping and final design is prepared.
Process design starts with designing networks which involves:
- Response time
- Product variety
- Product availability
- Customer experience
- Time to market
- Order visibility
- Return ability etc.
Job design is done to enhance the motivation of the employees associated with upward production in which ergonomics is an important factor. Combining process with those factors, process flow and layout is prepared and completes the process design. Thus, along with the structural proposition, variation in such designs may cause for a number of influential factors in terms of legislation, ethics, environment, life cycle analysis, mass customization, postponement, culture, standardization, reliability etc.
Companies can take a specific pattern of decision regarding the long- term capacity through its operation and thus can contribute to the major strategy of its own. Stevenson, W. J. (2005) argued that the operation strategy is mainly related to products, processes, technique, operating assets, quality, expenses, and lead times and scheduling.
Regarding the operation strategy matrix, a company’s senior management should take into account the distinctive competencies and scan to the environment. Stevenson, W. J. (2005) mentioned that they must critically examine many factors having both optimistic and negative impact by applying SWOT analysis. Thompson, A. A., and Strickland, A. J. (2003) stated that strengths and weaknesses have an internal view point and these are typically evaluated by operation individuals. Threats and opportunities have an external focus and are typically evaluated by marketing people. Thus, SWOT is often regarded as the link between organizational and operation strategy. Thompson, A. A., and Strickland, A. J. (2003) also argued to meets the quality strategy; a company must point out on maintaining or developing the quality of their products as well as services. This policy may be motivated by a variety of issues including the endeavor to overcome poor quality and preserving existing image of summit quality. Time- based strategies focus on reducing the time required to accomplish various activities by managing a number of tools like- design time, processing time, changeover time, delivery time and response time. The motive to increase productivity depends on labor, machine, capital or energy productivity that can be improved by control of the operation, critical analysis o the entire system, reexamination of work, reasonable goals, publicizing the work etc. However, the overall operation strategy can be meet up by product design, choice of location, choice of new technology, new facilities, employment, output level, inventory management purchasing etc.
A number of successful companies in the world have redefined the industry expectation through operation strategy
Dell computer
- Beginning of supply chain with the users or customers.
- They reduce existing complexity.
- Regular communication with the suppliers.
- Use of postponement approach to maintain inventory.
- They adopt lower pricing strategy than the rivals or competitors.
- They are maintaining strong administration rather than quantity.
Singapore Airlines
- Conducting surveys about passengers.
- Frequent audits, experience report on travel, providing magazines, test calls and benchmarking.
- Deep attention towards customer complaints.
- Offering newsletters to aware the air staffs about customer troubles and problems.
- Proving the “Higher ground” newsletters for the purpose of informing guards.
IBM
- Offering the most advanced information technologies;
- The operational expertise within exact industries;
- Consulting service and maintain system integration;
- Clarification department and technical support.
Along with those companies, McDonalds, Southwest Airlines, British Airways, Sony also maintains such procedure.
Postponement Strategy
Now- a- days, a number of manufacturers are moving towards postponement strategy for differentiation for keeping the best inventory amount at each of the segment of PLC. This strategy allows the manufacturer to use a “pull” or demand- oriented supply chain. Studies have shown that a systematic application of this can decrease the expense of inventory more than 40%. It is also been observed that implementation of postponement enables the manufacturers of keeping 80% to 90% of the finished stocks.
Stevenson, W. J. (2006) provides an example that furniture manufacturer can produce reading room sets such as table, chair but they do not apply stain unless customer allowing stains. Customer choice is important because once required stains, this will be applied in a comparatively short period of time. To achieve competitive benefit, they remove a long wait for customers.
Cohen, S., and Roussel, J, (2005) stated that garments workers produce shirt with pants which is unfinished, allowing the customers to alter their preference as to the exact length regarding the issue whether it should have cuffs or no cuffs. In the same way, delayed differentiation approach has been used by a number of market leaders of many sides, basically the manufacturers of semi- conductor industries as well as consumer electronics goods like- Dell, HP, Home Depot etc.
Like manufacturing, postponement can also be successfully implemented in service sector. For instance, different internet and e- mail services can deliver to the customers as standardized packages that can be customized according to the customer’s choice. The output of this differentiation of a service with customized features which can be easily produced, focusing the customer’s wish for differentiation and delivery speed on which the majority is standardized, capable the user to understand the usefulness of that service.
Modular Design Strategy
According to the viewpoint of systems engineering, modular design or ‘design in modularity’ is a process of targeting of converting a system into many parts or modules which can be individually made for utilizing in various systems as an indicator of multiple performer. Griffin, R. W. (2006) stated that computers, multi- storied based on illustrations of modular systems. Among them computer companies are the most popular which have modular parts and these can be replaced if they damaged. Chopra, S., Meindl, P. (2008) viewed that by arranging modules in distinct configurations, different computer proficiency can be achieved. Such as modular design producer quickly collect products with modules to accomplish a customized configuration for each customer.
Dell computer has effectively used this concept to become a leading power in the PC industry by providing the customers the chance to configure modules according to their own provision. Recently, other rival computer manufacturers are applying the similar approach.
Stevenson, W. J. (2006) argued that modular design can also be applied in service industry. For instance, an organization in London builds prefabricated motel complete with script, plumbing and even space decorations in its industrial unit and after that moves the entire rooms by railing to the construction site, anywhere they are integrated into the structure.
While designing a process, a number of considerations must be taken in mind as-
- Doing the task in correct order;
- Effective layout of the premise;
- Organization of task;
- Quality of the products;
- Customer services;
- Manuel or mechanical framework;
- The environmental sustainability.
A number of influential factors in designing any operation process are:
- Legislation, ethics and environment: Designers must take care about a vast range of legal and ethical concern as the environment posses a number of potential harms.
- Analysis the Life cycle of the company: Chopra, S. (2008) expressed that life cycle is one of the most significant factor of process design since wide distinction exists in amount of time a particular product or service takes to pass through a given stage of its life cycle on the basis of desire and demand and rate of technological change.
- Standardization: Standardization for both products and services affect process design through the absent of variety.
- Dependability: Chopra, S. (2008) also mentioned that reliability is used by prospective buyers in comparing other options and sellers in terms of cost, repeat transaction and normal effective conditions.
- Robust design: It is efficient since it is the design which results in goods or services that can function over a wide range of conditions20.
- Culture: Product designers of multinational companies must concern it in process design.
- Modernization: It affects by technology, module or engineering effort.
The product- process matrix introduced by Robert H. Hays and Steven C. Wheelwright indicates the relationship between PLC (Product life cycle) and TLC (Technological life cycle). This matrix can be shown as:
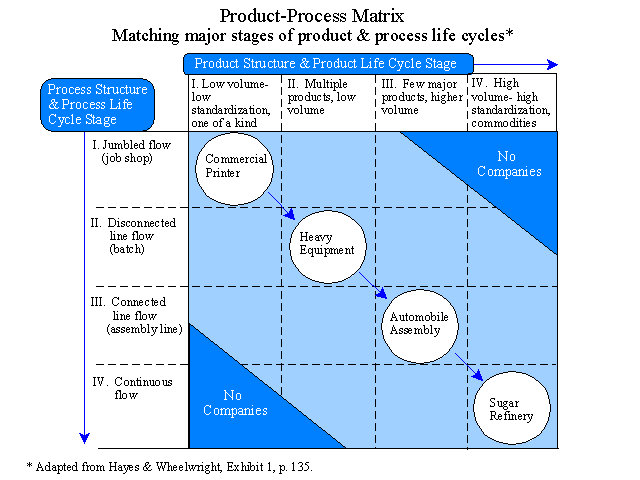
It can aid in the process design as:
- The process requires producing an item through a series in the market, which makes the process flexible, highly standardizes, automated and mechanized as a cost- effective impression.
- The matrix recognizes the available strategic options regarding manufacturing as a company can be indicated with a specific region in the matrix through PLC.
- It provides adequate predictions about the changes in market and industry that facilitates the design as more updated.
- It can help to define goods that prove a better guideline of assembly- line process.
- Product design, processing technology and other tactics like TQM and JIT are also prospective design procedure.
MRP and JIT
MRP and JIT are two most common and popular tools for investments management purpose. However, there are lots of differences can be notified among them. For instance:
- Definition: Stevenson, W. J. (2006) mentioned that Material requirements planning that is MRP is an information technology based information scheme that translates the completed manufactured goods necessities of the master schedule into time- based requirements for subassemblies. The element part and raw materials as well as working backward from the due date by using lead times. The other relevant information to verify when and how much of the order progress occurred. At the same time JIT that indicates ‘Just- in- time’ is basically a method for setting up production that consequences in low rank of work among process and inventory.
- Theme: MRP is as much a philosophy as it is a technique, and as much as an approach to scheduling as it is to inventory control while JIT represents a philosophy that encompasses every aspect of the process, from design to after the sale of a product. Here the philosophy is to practice a method that works fighting fit with nominal levels of inventories, minimal space, nominal waste as well as minimal transactions.
- Purpose: The purpose of MRP is to answer the following questions: What is needed? How much is the required? When is it would be required?
The basic purpose of JIT is to gain a balanced system along with disruption elimination, flexible production and waste elimination, especially excessive inventory:
- System view: MRP is considered as a system for batch production while JIT is sometimes viewed as a system for repetitive production operation.
- Functional view: MRP systems are fairly complex, requiring extensive and detailed shop floor controls. But JIT systems are much simpler, involving only minimal shop floor controls.
- Production and deliveries: MRP relies on a computer- based component scheduling system to trigger production and deliveries. In contrast, JIT relies on visual or audible signals to trigger production and deliveries.
- Demand basis: JIT operates on a “pull” demand basis whereby work is pulled from each step in the process to the next step when the next step has a demand for it while JIT does not maintain that rule.
There are three types of costs of inventory in supply chain. It has demonstrated as bellow:
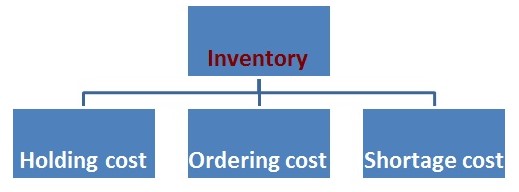
- Holding or carrying costs: Stevenson, W. J. (2006) addressed that it speaks about the physically situated items in storage. Here the costs take account of interest, insurance, depreciation, spoilage, taxes, pilferage, cracks as well as warehousing costs. The holding costs are affirmed in moreover in two ways such as a proportion of unit prices accounted in per unit of currency. The typical holding cost varieties from 2% and up to 40% of each item.
- Ordering costs: It point toward the costs of order otherwise in receipt of an inventory. The ordering costs are the costs to facilitate to vary with the authentic appointment of the order. In addition it involves shipping costs to determining how much it is required to involve to preparing invoices, moving shipping costs as well as the products hooked on transitory storage.
- Shortage costs: It comes into effect as soon as demand goes beyond the supply of inventory on hand. This set composed with the opportunity cost of not assembly any sale as well as delayed charges those are easier said than done to measure. In addition if the shortages take place within the item conceded for domestic use such as supply and assembly line up. The cost of nowhere to be found production or downtime is well thought-out as a shortage cost that can easily sprint into hundreds of standards as well.
These are the explanation of appropriate costs of inventory.
Bibliography
Bowersox, D. Closs, D., and Cooper, M. B. (2002), Supply Chain Logistics Management, 1st ed., McGraw-Hill/Irwin: London, ISBN-10: 0072351004.
Chopra, S., Meindl, P. (2008), Supply Chain Management, 3rd Edition, Pearson Prentice Hall, India, ISBN: 81-317-0401-7.
Christopher, M. G. (2005), Logistics and Supply Chain Management, 3rd Edition, Pearson Education: London, ISBN: 0273681761.
Cohen, S., and Roussel, J, (2005), Strategic Supply Chain Management, 2nd ed., McGraw-Hill: London, ISBN-10: 0071432175.
Coyle, J. J. et al (1995), The Management of Business Logistics: Instructor’s Manual, 6th edition., International Thomson Publishing: London, ISBN-10: 0314204393.
Ferrer J. and Karlberg J. (2008), Supply Chain Management: How to Build a Successful Global Operations Model, Web.
Fred, C.P. M. Sollish et al (2007), The Procurement and Supply Manager’s Desk Reference, 1st ed., Wiley, London, ISBN-10: 0471790435.
Griffin, R. W. (2006), Management, 8th Edition, Houghton Mifflin Company, Boston New York, ISBN: 0-618-35459x.
LTD Management (2008), Lean Supply Chain Management — The Essentials Part 2, Web.
Matthews P. and Syed, N. (2004), The Power of Postponement, Supply Chain Management Review, Web.
McGraw-Hill Higher Education (2008), System Design: Product and Service Design, Chapter-4, Vol. 6, Seg. 1, Web.
Ming Chuan University (2008), Inventory Management, Web.
Stoner, J. A. F., Freeman, R. E., Gilbert, D. R. (2006), Management, 6th Edition, Prentice-Hall of India Private Limited.
Stevenson, W. J. (2005), Operations Management, 8th Edition, Tata McGraw- Hill Company, New Delhi, ISBN: 0-07-060357- X.
Stevenson, W. J. (2006), Operations Management, 9th Edition, McGraw- Hill Company, ISBN: 0073041912.
Thompson, A. A., and Strickland, A. J. (2003), Strategic Management: Concepts and Cases, 13th ed., Irwin/McGraw-Hill, ISBN-10: 0072443715.
Wycoff J. (2008), Input Wanted: Principles of Innovation, Web.