Introduction
The role of operations in the day to day functioning of organizations is very important, especially in the manufacturing sector. As a result the topic of operations management has grown in importance as organizations have begun to understand the need to streamline operations. “Operations management is concerned with managing the resources that directly produce the organization’s service of product”. (Galloway, Rowbotham and Azhashemi 2000, p. 2).
Operations deals with all set of activities associated with the production of goods and services. In any organization, operations can be broadly classified into manufacturing operations and service operations. Manufacturing operations includes the conversion of input into a tangible output, whereas, manufacturing operations involve process of yielding an intangible output.
Operations management has also got a critical importance in every organization, whether it is manufacturing, production or service sector. Operation management is a diverse activity, which is concerned with the transformation of different resources that are used in the operations subsystem into value added products or services. It is really concerned with managing quality, efficiency and responsiveness of the firm. The objective of the operations management is to produce goods services of right quality and quantity at the right time and right manufacturing cost in order to satisfy the needs of the customers.
- The quality is determined based on the customers needs. The right quality may not be necessarily the top-quality. It is usually based on the cost of the products and services and also its technical characteristics as per the requirements of the customers.
- The right quantity means that organization should produce the products in right number. This is the most important objective for a manufacturing firm. If they are producing goods in excess of the demand from the customers, there will be unnecessary blocking of capital and the firm may incur a loss. Similarly if the firm is producing goods in short of demand, they could not meet the customers demand and it will affect the reputation of the firm and also there is a possibility of shifting of their customers to the competitors products.
- Timeliness is the most important parameter to be considered by the production department. For maintaining the timeliness, the production department should ensure that there are adequate inputs and raw materials required for the production process.
- Manufacturing costs must be determined before the product is actually manufactured. The manufacturing firm must take all efforts to produce the products within the targeted costs, so that they narrow the gap between targeted and actual costs.
So there are two activities that operations management has to keep in mind namely, optimum resource utilization and customer satisfaction. Frequently both the objectives could not be obtained simultaneously, so more suitable performance must be achieved. So, operations managers have to keep in mind two things which are competition in the market and also the strengths/weaknesses of the company.
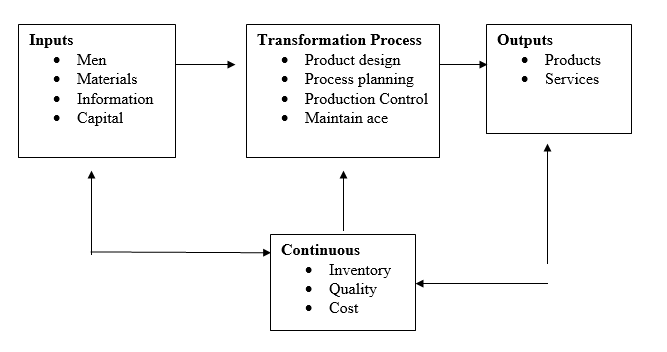
Functions of Operations Manger
Operation managers are generally concerned with planning, organizing, and controlling the activities which affect human behaviour. Planning establishes a future course of action and also provides a guideline for the future decision making. He defines the objective of the firm and also determines the policies and procedures for achieving the objectives. Overall it involves process like product planning, facility designing and also the conversion process. Organizing establishes a structure of task and authority. It determines the activities that are needed to achieve the goal and also to establish authority and responsibility for achieving them. (Young 1996, p. 82).
Controlling assures whether our actual performance is in accordance to our planned one. If there is any deviation from the planned performance, appropriate controlling measures have to be adopted timely. It mainly involves controlling costs, quality and schedules. Operation managers are also concerned with the human behaviour inside the organization and how they affect the management planning, organizing and controlling functions.
Operations strategy
Operation strategy is mainly concerned with establishing the policies and plans for using the resources of the firm so as to sustain the firm’s long term competitive strategy. Operations strategy can be defined as “major decisions about, and strategic management of: core competencies, capabilities and processes, technologies, resources, and key tactical activities necessary in the function or chain of function that create and deliver product and service combinations and the value demanded by a customer”. (Lowson 2002).
The main issues related to the operational strategy involves, the capacity requirements that is the amount and type of materials used in the production, facilities such as size location and specialization of the plant, technologies involved like the automation and other linkages, vertical integration with the suppliers and distributors, work force which includes the skill level and wage policies of the employees, quality of the product which includes defect prevention, monitoring and intervention, Another strategy include production planning and the materials control which involves sourcing policies, centralization and decision rules and the final strategy include the organizations structure control and reward system.
Toyota Motor Corporation which is a leader in automobile manufacturing can be taken as an example to explain the operational management process. Toyota started the automobile manufacturing operation in 1930s and many of the methods that it follows have been widely acclaimed and followed by many other manufacturers. The company is also a global leader in customer satisfaction. The Toyota production system (TPS) created by the company helps it to have an efficient manufacturing system which helps the company to bring down costs and at the same time maintain quality of its products. (Vokurka and Lummus 2007). TPS provides different processes in the assembly sequence.
Each process is produced only of its kind, quality and quantity, in the required sequence and only when it is needed. The end result is that there is no wastage of time between production and transportation of products. This practice was followed in every stage of the whole production process.. Kiichiro, who is the first president of the Toyota Motor Corporation, has laid the groundwork for just-in-time production, and he gets credit for coining the term “just in time.”
TPS has evolved out of a need that certain restrictions were there in the Japanese market which compelled them to produce small quantities of many varieties of products, even under the conditions of low demand. In order to overcome third problem, Toyota system was intended towards increase in production at the same time reducing wastage of raw materials and labour. TPS is not just a production system; it can show its strength even as a management system.
Many of the analysts are of the opinion that the Toyota’s strong performance is the result of its excellent operational system. It makes use of the concepts like Just-in-Time (JIT) and Kaizen or the process of continuous improvement, to achieve efficiency in production. “…kaizen, is the name that the Japanese have given to the concept of continuous incremental improvement. It is considered to be the single most important concept in Japanese management and the key to their competitive success.” (Reid and Koljonen 2000). Using the operational management system, Toyota was really able to reduce its aggressive cost, capture a huge market share, and maintain its product quality and also producing better models of cars in the market. It has made a very challenging growth in the production and also the customer satisfaction due to its efficient operations management.
We can discuss one of the issues involved in operations strategy of a manufacturing company. Manufacturers require a wide-ranging business solution which not only allows them to optimize internal processes but also to increase their relationship with their customers, suppliers, business partners and their associates. Operations Management System should be incorporated with all required section like inventory Order processing, Production Planning & Scheduling etc. to ensure faultless flow of in turn essential for real production.
Value chain management, especially supply chain management could be used to manage the suppliers of a manufacturing firm. Most activities in an organization move from one process to another in a chain and is referred to as the value chain. The end result is that the value of the finished product will be more than the sum of values of individual activities put together. But it should be remembered that costs occurring in the process and value are different.
For this purpose, identification of costs and value drivers for each activity are necessary. The concept of value chain has been universally accepted by organizations worldwide and has even become part of modern management thought. It is now considered to be one of the most useful tools for strategic planning with the ultimate aim of value maximization. This is achieved by minimizing costs incurred during each of the processes.
Four factors are considered to be part of the value chain namely the organization itself, its suppliers, its distribution channels and its customers. The term supply chain management has already become a very important concept. The important component of supply chain management analysis is identification of the supply chain driver. The manufacturing concerns should start with economies of scale upstream and should end with economies of scale down stream.
There are four Models which are used for managing the supply chain. It would cover all the quantitative techniques used in the area. The first model is statistical and other models which are used for sampling of the data and its inference. The other model is optimization which is from the point of view of a single decision maker. Next is the game theory or the equilibrium models which attempts to model multiple firms actively participate in joint outcomes. The final model is the decision support model. This would also include visualization support and various design techniques.
We can just take the example of a manufacturing firm who have a large number of globally spread suppliers. Here a mix of relationships could be applied. The company should have close relationships with a few selected suppliers along with searching in the market for newer possibilities for achieving short term goals. The feature of procurement, especially in the procurement of raw materials and other products is that they are subjected to fluctuating price in the spot market.
A particular version of procurement decision should be made while jointly procuring items. In the case of e-business, there should be automated bid collection information which should be readily available. Then there is a task of communicating with the sellers about the quantity required, timing of delivery, quality of the concerns and its services. Therefore multiple factors should be taken into consideration while purchasing and allocation decisions.
Consider a case when ‘x’ items have to be procured from ‘n’ suppliers. Then there will be large number of possibilities for a joint bid for the multiple items to be procured. This is a huge problem to be solved, since large number of bids are available. Innovative and modern methods are used to model and solve such problems. For the problem of ‘x’ items and ‘n’ suppliers, there could be x2ⁿ bids. An approach for this is given in the figure below.
Here start with small number of bids that cover all items, solve restricted winner deterministic problems for which the procedures are available. Then use an estimate of the value of these bids in a larger winner deterministic problem. If a bid is a part of winning basket, we will get the exact bid information. This adds to the pool of known bids for further estimation. Bid estimation will be available as interval estimate, which converge to accurate estimates faster as the pool of available bid information increases
Operations management system has the ability to manage the production with Kanban or Just-in-Time inventory systems. This system maintains all the required information starting from maintenance of bill, information required for maintaining and procurement of the resources, documentation, design and inspection of quality in all stages or production. Accessibility to information at the bottom level of production, status of the outsourced work, ensures that production tasks are accomplished. All these methods can be adopted appropriately to sustain the current operational effectiveness of the manufacturing firm.
A firm must take into consideration the following aspects so as to sustain its current operational efficiency and effectiveness. The management should start from selecting location of the plant. It is a very critical decision making process since a manufacturing plant is a long term investment. The plant should be located in a convenient and most appropriate place so that wastage of raw materials and other inventories could be avoided in then initial stage itself.
It should be also based upon the firm’s expansion and product diversification strategies. The physical arrangements of the firm should be also convenient for producing the required output in the desired quality. Materials handing is another important activity of a manufacturing firm that needs special attention. About 50% to 75% of the costs of production are involved in materials handling. So by efficiently managing the materials, we can reduce the cost of the product to a greatest extent. Product design and process design is another area that needs importance in operations management.
There should be appropriate product planning and control system, which includes planning, routing, scheduling and dispatching. Planning actually bridges the gap from our actual point to the target point. Routing determines the most desirable path to be followed from one department to the other and from one machine to the other till the product is into its final shape. Scheduling gives the sequence of operations to be followed so that the cost could be reduced to a maximum extent. Dispatching gives the necessary authority to start the work and release of the orders and instructions.
Then a daily follow-up should be also provided so the work in progress is known to the management and suitable control measures could be taken if there are any deviations from the planned performance. Firm that provides higher quality product than the others at the same price is more responsive to the customer, which also leads to better efficiency. Total quality management must be ensured to sustain the quality of the products, which needs to concentrate on the quality requirement of the customers.
The firm must take measures to measure quality, introduce Just in Time Inventory system, conduct Quality circles and also remove the barriers existing between the departments. As the name suggests Just in Time is a strategy whereby an organization attempts to reduce inventory and related costs thereby increasing return on investment. In short, a properly implemented Just in Time system will ensure that the organization will have ‘the right material, at the right time, at the right place and in the exact amount. (Epps 1995). The advantage of this system is that companies can forecast inventory requirements accurately. There are many merits and demerits for JIT.
The main merits of JIT include reduction of the set up time, which will allow the company improve the efficiency of their bottom level work, focus more on the areas which really needs improvement, thereby improving the overall productivity. It also improves the flow of goods from the store to shelves. The multiple skills of the employees could be effectively utilized. Scheduling of employee work hours can also be improved. Increased supplier relation ship could be achieved. The major problem with Just-In-Time operation is that it is more exposed to risk, since the consumers are opened to demand shocks and supply charges.
Quality circles are another measure which is adopted for operations management so as to achieve total quality management in the firm. The quality circle involves regular meetings of a group of employees (usually small) for the purpose of identifying, analyses and problem solving in areas related to work. This concept was started by Dr Ishikawa of Mushashi Institute of Technology, Tokyo in post war Japan. He included even the lowest level of workers as a part of this group. The effect was great and quality of production went up. It also had the effect of motivating and energizing work groups. (Talib and Ali 2003, p. 1). Through conducting quality circles in the organizations, the total quality management could be achieved.
The value of employees as an asset to the company is a recognized factor in business organizations. Quality circle is the way by which this value, consisting of human qualities like, wisdom, intelligence, experience attitude, feelings etc. will be recognized. In fact this concept is a part of human resources management and is considered to be a necessary or even key factor in improving worker productivity and product quality. The essence of quality circle is team work and participation. Through this a group effort is aimed at removal of any obstacles that may stand in the way of achieving stated objectives. (McKenna, p. 330).
There are three attributes to this concept. They are participation management, a technique for the development of human resource development and as a technique to solve problems. The objectives of Quality Circles include Change in Attitude, self development, development of team spirit and also improving the organizational culture..
Quality control is also an important factor involved in the operations management. It helps to develop the firm by providing long life, greater usefulness, and maintenance also reduces the cost through reduction of the possible losses. It also ensures satisfaction of customer’s high quality of the products and services and also brings goodwill and reputation to the manufacturer. (Hiraishi. P.4).
The materials management involved in the operations management also reduces the cost of the firm by reducing the investment in the inventories. Maintenance management also should be properly practiced so as to achieve minimum breakdown and keeping the plant in good working conditions. These all aspects of operations management should be effectively implemented in order to sustain the current operation effectiveness.
The operational environment today is highly embarrassed with mounting costs and declining prices; the customer is demanding, operating margins are getting depressed and obsolescence of products and processes is speeding up. Kaizen is another technique used to improve the operations of a manufacturing firm. Kaizen technique can be used for the process improvements. Improvements can be in the quality thereby providing quality product to the customer, cost reduction, efficiency in the delivery system and also in providing safety and morale to the employees. This method can be used for improving every aspect of the business in a step by step way, also gradually develop the employee skills by means of training and increased involvement.
The Kanban process is also an integrated approach concerned with the operation management process. It involves alteration of the production and supplier scheduling systems. The purpose in to see that inventory is kept to a minimum by close monitoring whereby on ordering it as and when needed. Kanban means card signal.
The importance of the Kanban concept is that the supplier should supply materials to the production line only as and when they are needed, so that there will be no storage problems in the production department. In this system the other work areas which are working along with the production department should produce or supply materials to the production department when they receive a card and an empty container, which indicates that more materials will be needed for the production department.
If there are any interruptions during the work process, each of the process will only produce enough materials to fill the container and then stop production. Kanban is a simple and easily understandable process which provides quick and precise information to the management and also to the production department. It gives quick responses according to the changes, avoids over production and minimizes wastes so that the costs could be reduced.
The manufacturing firm can adopt different methods for improving its operational effectiveness in the future. The first thing the firm has to focus is on the procurement of the raw materials and other goods from the suppliers. Procurement is one of the multifarious decisions of any manufacturing firm who is depending on its suppliers for the procurement of its raw materials. From the day to day transactions to more bulk transactions, complex decisions have to be taken by the management in each and every step.
The real task is to procure materials at lowest cost with out compromising on the required time. Now a days, e-business is gaining much importance, in which we can procure the goods through the web. “Studies have shown that a 5% saving in procurement costs translates into an effective increase in sales growth of 30%”. (Improving profitability through efficient sourcing and procurement).
The single largest item of expenditure in the manufacturing process is usually purchased products and services. It may come up to even 50% of the manufacturing cost. So any reduction in the procurement price therefore results into a direct increase in the profits. E-business involves e-sourcing and e-procurement.
E-sourcing is a strategy development which involves finding out ways in which the products needed may be got. It includes all the aspects of the buying process which involves knowledge, such as supply-base analysis, supplier identification, auctions and contract management. E-sourcing helps the companies to develop and implement best and successful practices, since most of the process used in the e-sourcing will become templates. These templates could be used in all another areas of the business, which is the greatest advantage of e-sourcing. This practice would probably develop a procurement strategy, which will reduce the time spent on that process.
In the case of purchase also it reduces the time of actual procurement, establishing contracts for the required products. It saves time and helps to build a strong supplier relationship. “E-sourcing can dramatically improve purchasing decisions through techniques for rapid market and price discovery.” (Gattoma, Ogulin and Mark, p. 347).
E-procurement is using internet to operate all the transactional aspects of requisition, ordering or products, receiving them and paying for them.
E-business has got many benefits. The main benefit cited are to achieve reduction in procurement costs which can be quite considerable. (Johnston, Wade and McClean 2007). Other benefits include improved supplier and market knowledge, easy availability of market, improved product quality, standardization of sourcing practices, shortened production cycles, improving skill in sourcing, and increasing the role of strategic sourcing in total spending.
The advantage that companies have when they e-source is that they are able to command better prices and have a large base of suppliers (when compared to traditional sourcing methods). So the end result is better quality raw materials at better rates. Many companies are now using e-sourcing as a base for better cost management strategy.
The role played by information technology in the felid of operations management is very important. It has come to such a stage that IT has come to be the most important and effective tool to formulate strategy and techniques in operations management. IT also plays an important role in formulating the support decision-making process of Operation Management. In fact, it is common knowledge that IT plays a major role in every business function including operations management. Decision-making process, Communication, Production Systems and Management are the main areas that are benefited from the use of information technology.
The manufacturing companies face challenges both from internally and externally. The external challenges include the pains of globalization, global competition, operational shortcomings etc. From inside, the challenge comes in dealing with the availability and price of the materials and controlling the margin by reducing the wastes and managing the resources. In order to overcome all these internal and external challenges, the companies have to optimize its value chain i.e., value chain management.
This means that the companies must efficiently manage their production and distribution value chain, which include the process of pushing the product through the manufacturing and the distribution cycle. The process starts from procurement of raw materials and ends by putting the products in the hands of the customers quickly, efficiently and cost effectively. (Schönsleben , p. 8). In any organization, particularly in a manufacturing firm, the operations management really deserves relevance.
In the era of heavy competition and globalization, gaining market share and achieving customer satisfaction is difficult. Competitive environment has also forced the firms to focus from inside the firm to outside trading and other partners. Communication facilities is also enhanced so as to redefine the work and to improve the customers expectation. Internet has made the companies to come up with highly improved and innovative solutions to accelerate the operations process. E-business in integration with the value chain management will definitely increase over competitive edge over our competitors.