Introduction
Effective operations management is critical for the success of any organisation because it determines and regulates all processes in the company, influencing the quality of products and services. Toyota Motor Corporation is an example of a company that pays close attention to organising its operations and supply chain while remaining a leader in the automotive industry.
The purpose of this report is to present an overview of Toyota’s products and strategies, describe its micro-operations and processes, discuss the application of the House of Quality technique to an analysis of the company’s products, describe Toyota’s competitive capabilities, and compare them with other companies in the automotive industry. Additionally, this report will provide a discussion of the supply chain and illustrate an application of an approach to forecasting demand for the company.
Overview of Toyota: Products, Environments, Strengths, and Weaknesses
Toyota was founded by Kiichiro Toyoda in Japan in 1937, and today this multinational manufacturer of vehicles holds sixth place among the largest companies with the highest revenues in the world. Toyota’s revenue for 2018 was $265 billion, and the current number of employees is more than 360,000 worldwide (Toyota USA, 2019). Presently, the company produces about 10 million cars per year, including hybrid cars (Toyota, 2018).
Still, Toyota’s variety of products is represented not only by vehicles (sedans, minivans, coupes, liftbacks, crossovers, and trucks) but also by automobile engines, as well as car electronics and compressors, along with textile machinery. Currently, Toyota is focused on increasing the market share of the company’s hybrid electric vehicles in order to preserve its position as a leader in this sector.
The modern environment of the automotive industry in which Toyota operates is characterised by manufacturers’ focus on technologies, innovation, diversification, and sustainability. These aspects are among the most important ones that must be taken into account when developing a company’s strategy. Companies’ opportunities in the present environment are associated with possibilities to design and implement the latest technologies in order to increase sustainability and attract more customers (Bhattacharya, 2014). The focus is also on the further growth of the market for hybrid electric vehicles.
Still, threats in this area include the intense competition between rival companies, frequent changes in oil prices and their impact on the industry, and consumers becoming more interested in economically advantageous cars, including hybrid and electric vehicles (Bhattacharya, 2014; Toyota, 2018). In addition, the rise of the Chinese automotive industry has been observed in recent years, which is also influencing the global market.
However, it is also important to mention Toyota’s specific strengths and weaknesses that affect its strategy, operations, and position in the market. Toyota is interested in applying the principles of innovation to different processes, including research and development (R&D), the manufacturing process, and even corporate culture. The focus on R&D allows the company to remain a pioneer in the industry through applying the most innovative technologies (Bhattacharya, 2014). The company spends about $9 billion on R&D each year and regularly develops new models and variants of vehicles, as well as improvements on existing models (Toyota, 2018).
In addition, the company is characterised by high customer loyalty and wide brand recognition. The company’s vehicles have a good reputation among consumers because of their safety, design, and innovative technologies. Weaknesses associated with Toyota’s operations and products are mainly related to incidents that led to the recalls of vehicles in recent years (Toyota, 2018; Toyota USA, 2019). This has affected consumers’ attitudes towards the brand and sales because of safety issues.
Toyota Operations & Processes
The process of manufacturing vehicles should be discussed as a macro-process, or a macro-level consisting of a range of micro-operations. Moreover, for Toyota, manufacturing involves the participation of many different suppliers who are responsible for producing certain parts of its vehicles. The process of completing a car also includes several important micro-levels of operations. For example, at the stage of creating a product design, micro-operations include the development of a cost-efficient but innovative draft design, the discussion of this design, its approval, and the development of test models or prototypes.
At the stage of producing car components, processes include manufacturing parts and components according to schemes and models addressing the standardised tasks and their further control and testing (Bhattacharya, 2014; Gao & Low, 2014). In addition, it is important to note that Toyota’s overall production process is guided by the company’s philosophy of lean manufacturing.
The company is focused on optimising the production process in order to address inventory and storage issues to reduce the time that manufactured parts are stored, as well as to decrease the associated man-hours. These principles are used in the context of the company’s operations strategy (Lean Production and the Toyota Production System, which regulate management practices), which directly influences micro-operations (Bhattacharya, 2014).
Thus, the company avoids utilising long assembly lines, the use of rounded-off sets of tasks is supported, and the overall assembly line is divided into several specific segments with a separate quality control for each segment (Bhattacharya, 2014; Gao & Low, 2014). From this perspective, managers are interested in developing a continuous flow of processes that are based on the Lean Systems approach to address the issues of overproduction and quality (Gao & Low, 2014). These approaches allow for increasing the quality of produced parts or components and minimising the resources used.
The House of Quality Technique
The House of Quality is a specific technique in operations management that includes taking customers’ preferences into account while developing and manufacturing a product. This approach has been actively used in Toyota since the 1970s, when this method was developed and adopted by Japanese manufacturers of automobiles, equipment, and electronics (Barnes, 2017). The focus is on determining customers’ preferences regarding the expected design and qualities of a specific product with reference to certain target values (Barnes, 2017; Bhattacharya, 2014). This approach is important for Quality Function Deployment and quality planning in order to design an effective product that will address customers’ expectations.
The following components comprise the House of Quality: customers’ requirements and expectations regarding a product, prioritised customer requirements, an importance rating provided by customers, benchmarking, target values, and technical descriptors.
Thus, the matrix includes the sides or walls, the ceiling, the roof, and the floors, which are composed of these parts. The interior parts of the house represent the relationships that are observed between customers’ specific requirements and certain technical descriptors that have been determined for a product (Bhattacharya, 2014; Barnes, 2017). In addition, the house has a roof, representing the interrelationship between the technical descriptors that have been identified.
The example of Toyota presents an opportunity to analyse the application of this technique to choosing materials and design aspects for the X components of the body of some of Toyota’s vehicles. The analysis will be conducted with reference to a comparison of Toyota’s products to the products manufactured by two of its competitors, companies A and B. Figure 1 represents the House of Quality matrix that was developed to address this task.
The major customer requirements regarding the car body are its aesthetics and performance qualities. These requirements are subdivided into look, cost, finish, resistance to corrosion, light weight, durability, and strength. In the section for technical descriptors, the materials to be used and the specifics of the manufacturing process are listed. With reference to certain aspects, customer requirements and technical descriptors seem to be highly correlated, for example, cost and steel, cost and aluminium, and strength and steel, among others. The analysis of the House of Quality makes it possible to reach a decision regarding the design and development of the X component that addresses both technical issues and customers’ preferences.
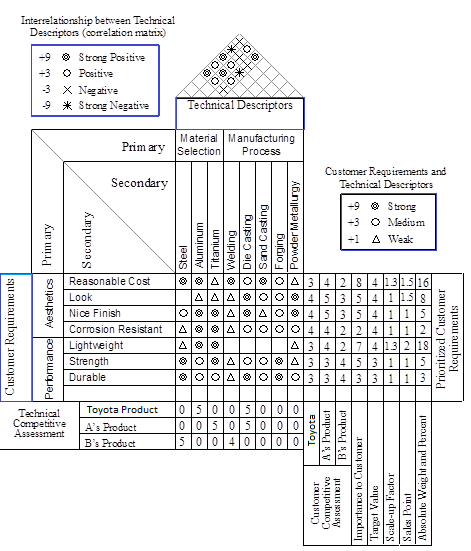
Toyota Competitive Capabilities
A company’s general competitive capabilities include its situation regarding product prices and production costs to make a manufacturing process cost-efficient, the quality issue, the speed of product delivery, dependability, its focus on innovation and flexibility, productivity, and sustainability (Barnes, 2017). Toyota’s competitive advantage is also based on these capabilities, which need to be discussed in detail.
The cost structure in Toyota is very effectively organised because of its close relationships with suppliers (Toyota USA, 2019). Furthermore, well-organised production processes and good distribution channels allow the company to control costs (Barnes, 2017; Bhattacharya, 2014). Still, these processes do not contribute to decreasing prices to attract more customers: cost-efficient production is used in the company along with a distinctive price policy to accentuate the reputation and quality of the company’s vehicles.
Toyota is able to produce high-quality cars through its specific Toyota Production System and an associated philosophy based on the principles of lean manufacturing. As a result of applying these rules, the company has improved its manufacturing process, interaction with suppliers, logistics, and quality control processes (Toyota USA, 2019). All these principles and rules are known as the Toyota Way, and they allow for manufacturing cost-efficient but high-quality products that are attractive to customers because of their design, innovation, and safety (Bhattacharya, 2014; Gao & Low, 2014).
In addition, attention is given to the organised delivery of products through official dealers and distributors in different regions of the world. Thus, capabilities related to speed and dependability are also addressed.
The company’s productivity is also based on the Toyota Production System and the Kaizen philosophy. It is important to note that, in the context of Toyota, the Kaizen philosophy means a focus on the continuous improvement of all operations and functions in the organisation in order to increase productivity through involving all employees in the process (Bhattacharya, 2014; Gao & Low, 2014). Just-in-time is one more concept utilised by Toyota in order to improve its operations through optimising all actions and processes while avoiding repetitive or unnecessary steps and activities (Bhattacharya, 2014).
Furthermore, sustainability is one of the key principles on which Toyota’s philosophy is based. The company pays close attention to balancing the use of economic, human, and environmental resources. The major action in this context is the production of hybrid and electric cars. In addition, the company is developing and improving its waste management and recycling systems (Toyota, 2018; Toyota USA, 2019). It is also focused on decreasing the use of water and energy resources in its operations.
Toyota Vs. Nissan Competitive Capabilities
A polar or radar chart can illustrate the comparison of two organisations from one sector with respect to certain performance objectives while using a scoring system to determine the importance these organisations assign to various performance indicators. By comparing the strategies followed by Toyota and Nissan in this area, it becomes clear that Toyota pays maximum attention to and spends considerable resources on achieving high-level quality and the degree of flexibility associated with innovation (Figure 2; Barnes, 2017).
For Nissan, the aspect of quality is also the key priority (Nissan, 2019). Sustainability and productivity are also critical performance objectives and competitive capabilities for Toyota that guarantee its competitive advantage.
In the case of Nissan, the other priority is cost in order to preserve its price leadership in the market. Cost and delivery issues are not viewed by Toyota’s managers as requiring additional attention because these areas are effectively regulated by the company’s policies (Toyota, 2018). When comparing the situation of Toyota with Nissan’s capabilities, it is important to note that flexibility and sustainability are lower priorities for Nissan, and speed and dependability receive almost the same scores.
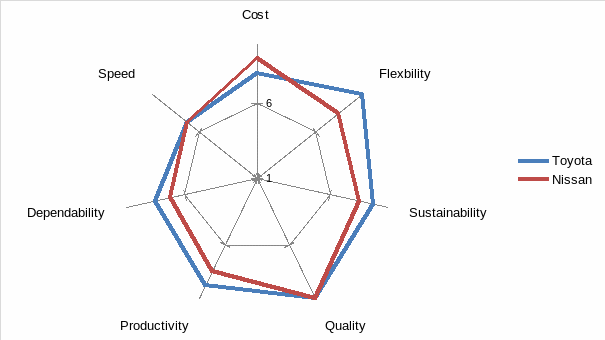
Toyota Supply Chain & Recommendations
The supply chain of Toyota involves suppliers of the first and second tiers that initially competed against each other in order to cooperate with the company. In this context, first tier suppliers provide Toyota with particular systems that are not interchangeable, and second tier suppliers produce certain parts or components of these systems (Kito, Brintrup, New, & Reed-Tsochas, 2014).
According to the Toyota Production System, the focus is on those suppliers that can decrease the costs of production but that use the most innovative and high-quality technologies (Bhattacharya, 2014). Furthermore, the supply chain system currently in use is based on the just-in-time principle, and the need for certain components and parts is addressed only when this need is observed because the connection with suppliers is well organised.
First tier suppliers actively participate in the process of product development, and they receive the order after presenting and testing the prototype or model of a certain system for Toyota. The company leaders make decisions after analysing performance and costs related to the prototype. In the context of the Toyota Production System and lean manufacturing to decrease costs and the overuse of resources, suppliers are encouraged to communicate with each other and develop the most cost-efficient solutions (Bhattacharya, 2014).
Second tier suppliers produce parts and provide components depending on the needs of first tier suppliers. As a result, specific functional units are organised. First tier suppliers are viewed as responsible for product design and engineering, while second tier suppliers are responsible for micro-operations and process engineering (Kito et al., 2014). From this perspective, relationships between suppliers are developed, employees actively communicate and cooperate, and decisions are made and problems are resolved in pursuit of key objectives and by involving first tier and second tier employees. Figure 3 illustrates the supply chain of Toyota with a focus on flows of information and production between customers, the company, and suppliers.
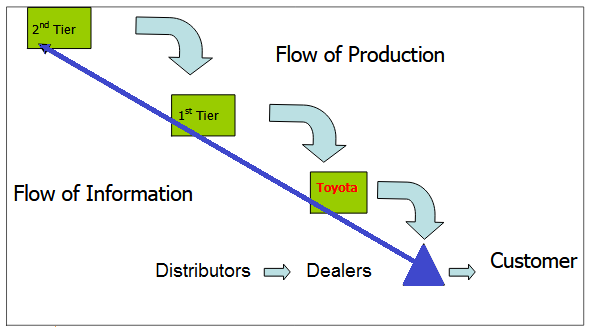
Although this supply chain is effective and characterised by highly positive outcomes, there are challenges associated with supply chain management. The problem is that all suppliers working with Toyota are expected to be actively involved in the company’s operations and share knowledge and resources while being guided by the principles of the Toyota Production System. Therefore, some improvements can be made in order to contribute to more effective supply chain management for the company.
Firstly, more attention should be paid to implementing and improving technologies for sharing secured corporate data. Secondly, more attention should be paid to organising training for new suppliers about working in the context of the Toyota Production System and the Toyota Way philosophy (Gao & Low, 2014). The active integration of suppliers into the activities and culture of Toyota requires additional training so that they can achieve better results through collaboration.
Toyota Forecasting Methods
Forecasting future demand is important for operations management in order to determine what capacity should be guaranteed from a long-term perspective. Depending on the products and services companies sell, they can choose between different forecasting methods, including focusing on the average and exponential smoothing (Bhattacharya, 2014; Barnes, 2017). Toyota makes use of various forecasting techniques depending on trends in customers’ behaviour in order to plan capacity and production processes (Ludwig, 2015). Regional dealers provide monthly reports, including data on forecasting for the next three months, as well as contacting distribution centres to discuss the demand.
Toyota uses specific demand forecasting software to control inventory management and set the objectives for operations management. The updated version of this software allows for including more factors that can influence increases and decreases in demand. Thousands of forecasts are analysed with the help of this software monthly (Ludwig, 2015). With reference to the forecasts and analysis provided in the Toyota Industries Report for 2018, it is possible to predict further increases in demand for products in Japan, the United States, Europe, and other regions (Toyota, 2018). The numbers of units forecast to be sold are presented in Figure 4.
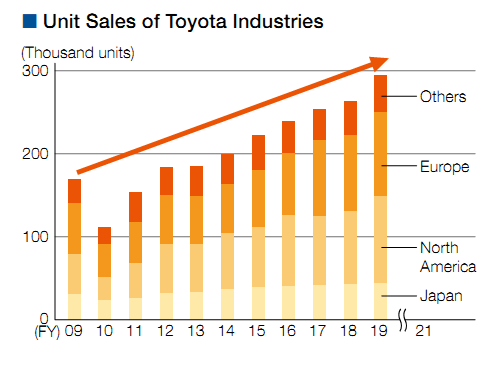
Conclusion
In the automotive industry of Japan and globally, Toyota takes a leading position while being associated with such features and characteristics as innovation, safety, durability, and flexibility in products and operations.
This report has presented an analysis of Toyota’s micro-operations, a House of Quality analysis based on customers’ expectations regarding one of the company’s products, the competitive capabilities of the company, and its prioritisation and realisation of performance objectives. In addition, the report has also provided a discussion of the company’s supply chain and the application of a forecasting technique to the case of Toyota.
It should be stated that the company’s reputation and popularity among customers depend on its high-quality and highly innovative products. Still, it is also important to note that the exceptional success of the company’s operations management depends on the Toyota Production System and the company’s specific philosophy, which allow it to increase productivity and quality, contribute to cooperation between suppliers, reduce costs, focus on innovation, and achieve sustainability. From this perspective, the operations management strategies and methods that are applied by Toyota appear to contribute to its continued strength and growth in the industry.
References
Barnes, D. (2017). Operations management: An international perspective. London, UK: Macmillan International Higher Education.
Bhattacharya, S. (2014). Operations management. Sonepat, India: PHI Learning.
Gao, S., & Low, S. P. (2014). The Toyota Way model: An alternative framework for lean construction. Total Quality Management & Business Excellence, 25(5-6), 664-682.
Kito, T., Brintrup, A., New, S., & Reed-Tsochas, F. (2014). The structure of the Toyota supply network: An empirical analysis. Web.
Ludwig, C. (2015). Toyota part 4: Looking for the ‘holy grail’ of predictability. Web.
Nissan. (2019). Our company. Web.
Toyota. (2018). Toyota industries report 2018. Web.
Toyota USA. (2019). Our story. Web.